A Review of the Grinding Media in Ball Mills for Mineral …
The performance of grinding media in a ball mill is measured in terms of wear rate, which is a function of the media composition, hardness, phase structure, and …
اقرأ أكثر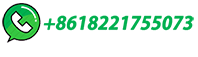
(PDF) Producing Metal Powder from Machining Chips Using Ball …
Nevertheless, parameter factors, such as the type of ball milling, ball-to-powder ratio (BPR), rotation speed, grinding period, size and shape of the milling media, and process control agent (PCA ...
اقرأ أكثر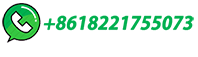
Materials | Free Full-Text | The Influence of the Grinding …
The image showing the ground product in the chamber depicts an increase in material volume during grinding, resulting from high comminution efficiency (lower bulk density of this finer-grained material). ... 2024. "The Influence of the Grinding Media Diameter on Grinding Efficiency in a Vibratory Ball Mill" Materials 17, no. 12: 2924. …
اقرأ أكثر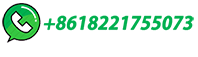
Grinding Media in Ball Mills for Mineral Processing
The ball mill is a rotating cylindrical vessel with grinding media inside, which is responsible for breaking the ore particles. ... In both types of mills, a portion of the charge is lifted along the perimeter of the shell during the mill rotation and, after exceeding the angle of repose, part of it slides down while the other part cataracts ...
اقرأ أكثر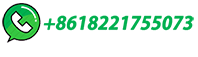
What is a ball mill and What are Its Advantages and …
Applications of ball mill. Cement industry: The ball mill is commonly used for grinding cement clinker and gypsum to produce cement. Mineral processing: The ball mill is widely used in ore processing plants to grind various ores and other materials. Ceramic industry: The ball mill grinds different ceramic materials, such as clay, quartz, …
اقرأ أكثر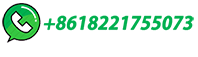
A contact-electro-catalysis process for producing reactive …
a Schematic illustration of a ball mill process using ... In virtue of frequent collisions that naturally occurred during ball milling, a triboelectric material-based grinding setup was first ...
اقرأ أكثر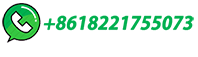
What is a Ball Mill Explained: In-Depth Guide
Critical Speed: Critical speed is the hypothetical speed at which the centrifugal force is equal to the gravitational force, and the grinding media starts sticking to the inner shell of the equipment instead of falling freely.Grinding at or close to critical speed of the mill yields a poorer grinding efficiency. The ball mills are mostly operated at 65 …
اقرأ أكثر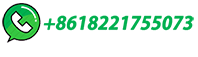
Selected Advances in Modelling of Size Reduction in Ball Mills …
In this paper, we have highlighted some selected significant developments that have taken place during the last ten years or so in our understanding the size reduction of the particulate materials in ball mills using the traditional population balance model. These developments relate to experimental technique and design of …
اقرأ أكثر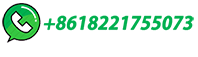
Ball mill- Principle, Construction, Working
This design prevents contamination and minimizes the risk of dust emissions during operation. Some ball mills may have transparent or removable panels for inspection and maintenance. 7. Control Systems. Many pharmaceutical ball mills have control systems that allow operators to set and monitor various parameters during the …
اقرأ أكثر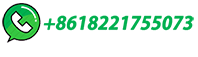
Producing Metal Powder from Machining Chips Using Ball …
A ball mill is additionally utilized to grind and combine materials, commonly with spherical or cylindrical-shaped grinding media such as balls or rods . Numerous researchers have effectively used ball milling to produce nanostructures of various materials or to investigate structural changes in materials during ball milling …
اقرأ أكثر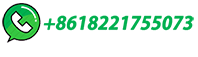
Size Reduction
For example, steel balls are denser than porcelain balls and are used to produce fine material. The ball mill is very versatile in operation and can be used for both wet and dry milling. However, it produces a lot of noise due to the movement of collision of the metal balls with the walls of the mill during grinding. Another limitation of the ...
اقرأ أكثر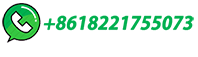
Exploring ball milling theory: A comprehensive guide
Applications of Ball Milling. 1. Materials Science and Research. Ball milling is widely used in materials science and research for the synthesis of new materials, the modification of material properties, and the preparation of nano-sized particles. It is employed in the production of metal alloys, ceramics, and composite materials. 2.
اقرأ أكثر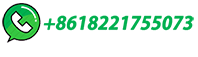
Ball Mill (Ball Mills Explained)
Ball Mill Introduction . There are three main stages to mineral processing in the mining industry.These are: Comminution (crushing and grinding).; Beneficiation (separation and concentration).; Smelting and refining.; …
اقرأ أكثر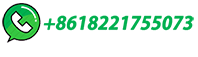
Ball-milling – Nanoscience and Nanotechnology I
In continuously operated mills, precursor material is fed from left side at an angle of 60°, and the end product is removed from right side at 30°. When the shell is rotated, the balls lift upwards on the rising side of the mill. ... During alloy formation using ball-mill, two processes simultaneously occur: (a) fracturing, and (b) cold ...
اقرأ أكثر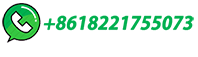
Ball Mill Adalah? Prinsip Kerja, Bagian, Komponen Dan …
Ball (bola) merupakan komponen utama yang berperan penting dalam proses penghalusan material pada mesin ball mill. Bola tersebut menempati antara 30 - 50% dari volume silinder. Ukuran diameter bola pada mesin ball mill bervariasi mulai dari 2 cm sampai 15 cm. Bola tersebut terbuat dari bahan logam, porselen, baja tahan karat dan …
اقرأ أكثر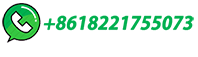
A Review of the Grinding Media in Ball Mills for Mineral …
The ball mill is a rotating cylindrical vessel with grinding media inside, which is responsible for breaking the ore particles. Grinding media play an important role in the comminution of mineral ores in these mills. This work reviews the application of balls in mineral processing as a function of the materials used to manufacture them and the …
اقرأ أكثر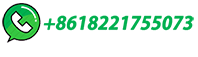
What Is a Ball Mill and How Does It Work?
While they may appear deceptively simple, a ball mill consists of a hollow cylindrical shell, grinding media such as balls, and an inner lining of abrasion-resistant …
اقرأ أكثر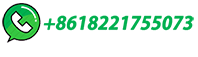
Ball Mill
Brief introduction. The ball mill is the key equipment for crushing the material after it is crushed. Ball mills are widely used in cement, silicate products, new building materials, refractory materials, fertilizers, ferrous and non-ferrous metal beneficiation and glass ceramics and other production industries, dry or wet grinding of various ores and other …
اقرأ أكثر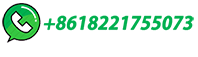
High-Energy Ball Milling Parameters in Production of
During HEBM energy is transferred from the movement of the balls to the powder. High energy transferred to the powder material causes deformation, fracture, welding, and diffusion processes; leading to alloying at the atomic level in addition to significant grain refinement [1,2,3,4].The most widely accepted mechanism to rationalize …
اقرأ أكثر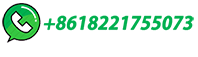
The operating principle of the ball mill
The operating principle of the ball mill consists of following steps. In a continuously operating ball mill, feed material fed through the central hole one of the caps into the drum and moves therealong, being exposed by grinding media. The material grinding occurs during impact falling grinding balls and abrasion the particles between …
اقرأ أكثر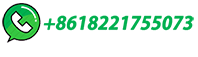
The Ultimate Guide to Ball Mills
The gravel ball mill adopts porcelain material or granite as the lining board, which is widely used in the field of colored cement, white cement and ceramics. 3. According to the discharging method of ball mill: ... but also the service life of the ball mill. During grinding operation, the grinding efficiency of the ball mill generally depends ...
اقرأ أكثر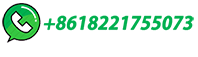
Ball Milling
Ball milling is a mechanical technique that involves grinding solid materials using hard balls like stainless steel or tungsten to prepare nanosized metal particles with desired …
اقرأ أكثر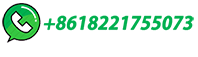
Calculate and Select Ball Mill Ball Size for Optimum Grinding
In Grinding, selecting (calculate) the correct or optimum ball size that allows for the best and optimum/ideal or target grind size to be achieved by your ball mill is an important thing for a Mineral Processing Engineer AKA Metallurgist to do. Often, the ball used in ball mills is oversize "just in case". Well, this safety factor can cost you much in …
اقرأ أكثر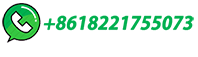
Exploring Ball Mill Diagram: A Comprehensive Guide
Generally, the length-to-diameter ratio of the mill, known as the L/D ratio, is between 0.5 and 3. Shorter mills are used for crushing coarse materials, while longer mills are utilized for grinding fine materials. The ball mill dimensions and capacity are determined based on the application, and the required throughput.
اقرأ أكثر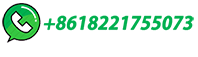
Tuning size distribution of zinc borosilicate glass additives by …
Journal of Materials Science: Materials in Electronics - The urgent need for the electronic industry is to replace the expensive silver with a cheaper copper for conductive paste. ... Surface treatment of glass powder is needed to reduce the aggregation during ball-milling process [10,11,12,13,14]. ... Ball mill modifiers specifically refer to ...
اقرأ أكثر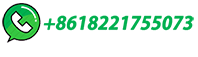
Research progress on synthesis mechanism and performance …
The formation of composite materials combining biochar and iron-based materials effectively mitigates the agglomeration phenomenon of a single material during ball milling and ensures good dispersion.
اقرأ أكثر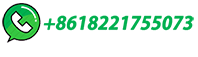
All About End Milling
A roughing end mill can efficiently remove significant amounts of material from a workpiece, especially during the initial stages of machining. It is designed with a coarse and rugged geometry that allows for aggressive material removal while withstanding high cutting forces. ... devices such as square, ball, or flat end mills. Hard materials ...
اقرأ أكثر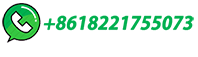
Exploring ball milling theory: A comprehensive guide
Ball milling is a fundamental and widely utilized technique in material processing. Understanding the principles behind ball milling theory is crucial for achieving optimal …
اقرأ أكثر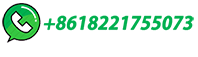