Factors Affecting Ball Mill Grinding Efficiency
a) Mill Geometry and Speed – Bond (1954) observed grinding efficiency to be a function of ball mill diameter, and established empirical relationships for …
اقرأ أكثر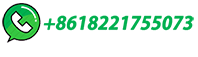
(PDF) A Review on Cryogenic Grinding
Cryogenic grinding, namely freezer grinding or cryomilling [36], is among the advanced grinding methods that allows finer particle size via grinding operation at extremely low temperature, often ...
اقرأ أكثر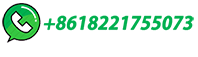
Reducing the energy footprint of grinding circuits: the …
The grinding process in ball mills is notoriously known to be highly inefficient: only 1 to 2% of the inputted electrical energy serves for creating new surfaces. There is therefore obvious room for improvement, even considering that the dominant impact mechanism in tumbling mills is a fundamental liability limiting the efficiency.
اقرأ أكثر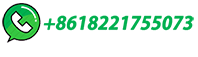
Effect of Grinding Conditions on Clinker Grinding Efficiency: …
The results obtained from the study investigating the effect of grinding conditions, such as different ball size distributions, mill speeds, and feed rates, on the …
اقرأ أكثر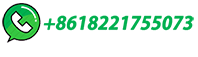
How to Calculate Grinding Mill Operating Efficiency
By definition, both work indices cover exactly the same amount of size reduction, namely from an infinite feed size to a product size of 80% passing 100 microns. In "Crushing and Grinding Calculations", Bond identified correction factors that should be applied to the calculated power (W) determined by using the Bond Equation.
اقرأ أكثر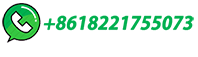
Effect of grinding media properties and stirrer tip speed …
Quartz (Lingshou County, Hebei Province, China) was used as the feed for the grinding test. The particle size distribution of the feed is illustrated in Fig. 1.The feed size was classified into three particle size classes: coarse size (class 1, +45 μm), desired size (class 2, −45 +10 μm), over-grinding size (class 3, −10 μm), and the percentage …
اقرأ أكثر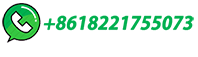
Quantifying the energy efficiency of fine grinding …
Two of the most popular methods for estimating grinding energy requirements are the Bond operating work index (OWi) and the Morrell specific comminution energy method. Both relate the …
اقرأ أكثر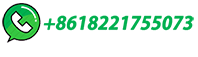
Effect of media size and mechanical properties on milling efficiency
Research Highlights The effect of mill media material properties on grinding efficiency, media wear, and power consumption was defined. High density media with optimum sizing improved milling efficiency by approximately 30%. Mill media with a low coefficient of friction resulted in reduced energy consumption of up to 2.3 times in the …
اقرأ أكثر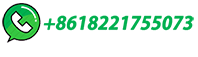
(PDF) Grinding Media in Ball Mills-A Review
media decreased the grinding efficiency due to the irregular movement of the concave-convex grinding media. Concave Concave grinding media have larger specific areas than spheres, which increases ...
اقرأ أكثر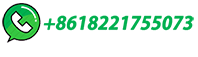
Equipment Sizing: Crusher or Grinding Mill
UNTIL THE THIRD THEORY OF COMMINUTION of "Work Index" method of determining crushing and grinding mill size was introduced, there was no way of accurately figuring the most applicable, most economical size of crushing and grinding mill. Naturally, with little or no factual operating data correlated in useful form, it was easy enough, even …
اقرأ أكثر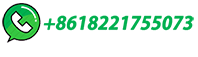
Effect of ball and feed particle size distribution on the milling
The size of grinding media is the primary factor that affects the overall milling efficiency of a ball mill (e.g. power consumption and particle size breakage). This article tackles the lack of a … Expand
اقرأ أكثر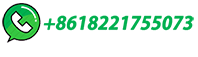
Research of grinding efficiency and main duct wear of …
The spindle speed affects the grinding force of the pendulum mill and the throwing height of the particles, thus affecting the grinding efficiency; the spade degree determines the trajectory of the particles in conjunction with the spindle speed, thus affecting the grinding efficiency; the wind introduced from the air inlet acts as an air ...
اقرأ أكثر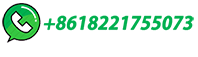
Effect of Nozzle Quantity on the Flow Field Characteristics …
A steam jet mill (SJM), which employs industrial waste heat steam as a gas source, is a widely utilized apparatus for the pulverization of fly ash. To achieve elevated single-machine grinding capacity, efficiency improvement research based on structural optimization should be conducted. In this study, numerical simulations and industrial …
اقرأ أكثر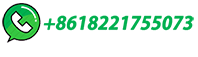
Grinding Media in Ball Mills for Mineral Processing
The grinding efficiency of a ball mill is determined by the product size distribution, energy consumption, and the grinding costs. According to Hassanzadeh [ 6 ], about 37% of the costs are used for grinding media only,13% for liners, and about 50% is used for energy in an industrial ball mill.
اقرأ أكثر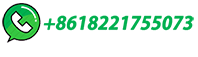
Determining optimal process parameters to increase the eco-efficiency …
Eco-efficiency originally refers to the concept of creating more value with less environmental impact, and the concept has been adapted and defined for manufacturing processes at a unit process level (Li et al., 2012).Accordingly, the grinding process can be considered as three layers (see Fig. 1): on the upper layer, the grinding …
اقرأ أكثر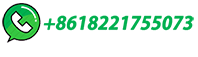
Energy and cement quality optimization of a cement grinding circuit
The size of the grinding media and its distribution is one of the major parameters influencing the grinding performance of the mill. ... Effects of separator efficiency on clinker grinding circuits. ZKG, 41–10 (1988), pp. 501-505. View in Scopus Google Scholar [33]
اقرأ أكثر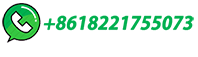
Effect of grinding, extraction time and type of coffee on the
The particle size distributions of each grinding level were determined according to NTC 2441, Colombian Technical Standard, where the average of the particle size was determined by granulometric ...
اقرأ أكثر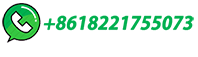
The impact of different stirrer designs and mill orientations …
Additionally, the particle size distribution and scanning. The impact of stirrer designs in vertical orientation. One of the key factors controlling media behavior and grinding efficiency in stirred mills to provide better breakage energy, collision frequency, and circulation is changing the design parameters, particularly stirrer designs.
اقرأ أكثر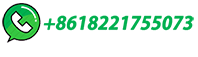
Energy-Efficient Advanced Ultrafine Grinding of Particles …
The present literature review explores the energy-efficient ultrafine grinding of particles using stirred mills. The review provides an overview of the different techniques for size reduction and the impact of energy requirements on the choice of stirred mills. It also discusses the factors, including the design, operating parameters, and feed material …
اقرأ أكثر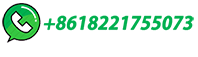
Ball Mill Success: A Step-by-Step Guide to Choosing the Right Grinding …
Size and Shape: The efficiency of the milling process and the final product's granularity are significantly influenced by the size and shape of the grinding media. Smaller media are capable of achieving finer particle sizes but may require longer milling times. Conversely, larger media offer faster size reduction but may not achieve the …
اقرأ أكثر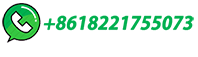
Grinding Media in Ball Mills-A Review
Table 1. Chemical composition of typical grinding media (% wt.). Adapted from [24]. 2.1.1. Cast Iron Cast iron can be grey cast iron or white cast iron, but white cast irons are commonly used in ...
اقرأ أكثر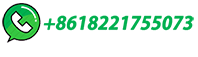
Influence of grinding on rail surface and profile
The grinding efficiency achieved by GS-ZA was the lowest compared to the highest efficiency achieved by GS-WA. The thermal imaging during grinding showed that the surface temperature was highest while grinding with GS-WA followed by GS-ZA and GS-A respectively. ... However, it can be moderated by changing the grit size of the …
اقرأ أكثر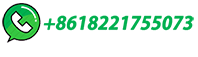
The basics of grinding circuit optimisation
Many significant grinding circuit improvements have been reported for operating plants, based on recurring themes such as the optimisation of mill feed size, mill liner design, …
اقرأ أكثر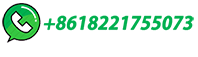
Effect of grinding media on the milling efficiency of a ball mill
The size of grinding media is the primary factor that affects the overall milling efficiency of a ball mill (e.g. power consumption and particle size breakage).
اقرأ أكثر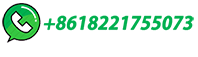
Quick Grind Check -How to Quickly Estimate Grind Size or …
Reference: Wills, B.A., 1988, "A Rapid Method for Measurement of Fineness of Grind", Minerals Engineering, Vol.1, No. 1, pp. 81-84. Here is an Excel produced Table of a 3.2 SG rock on which you check the grind size P80 -200Mesh. The password that lets you change the SG is " 911met " Marcy Grinding Analysis Chart Password 911met
اقرأ أكثر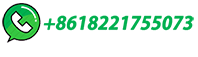
Effect of ball and feed particle size distribution on the milling
During the grinding process, coarser material (size class 1) break to finer material (size class 2) and (size class 3) which are termed the daughter products, as shown in Fig. 1.A chemical reaction on the other hand can consist of say reactant 'A' forming intermediate product 'B' then proceeding to final product 'C' or a competing reactant 'A' …
اقرأ أكثر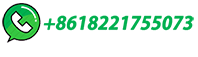
The impact of different stirrer designs and mill orientations …
The grinding process is efficient in the second zone, and as the SI GM increases, the particle size decreases until it reaches a minimum. Finally, in the third zone, the grinding efficiency declines. The inefficiency in the third zone is …
اقرأ أكثر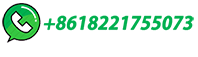
Effect of grinding media on the milling efficiency of a …
smaller particle size and lower cementite (Kano and Saito, 1998). When a larger ball size was used, crystal-lisation decreased faster, while grinding efficiency and ore specific surface area increased. On the contrary, the smaller the ball size was, the smaller the crystallinity de-crease. As a result, using a small ball size can result in
اقرأ أكثر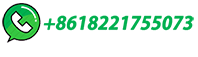
Making Milling and Grinding More Efficient | E & MJ
In his paper, 'Helping to reduce mining industry carbon emissions: A step-by-step guide to sizing and selection of energy efficient high pressure grinding rolls circuits' (2022), 4 Stephen Morell of SMC Testing Pty Ltd. provided a new power-based methodology to assess and size HPGR closed circuits in hard-rock mining applications.
اقرأ أكثر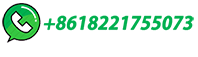
Full article: Optimizing hammer mill performance through …
In order to evaluate improvements to the size reduction process, hammer mill grinding tests were conducted using a small-scale commercial grinder with a nominal power rating of 85 hp (63.4 kW). This scale of testing is ideal to evaluate the effects of grinder configuration and process parameters on grinder capacity and efficiency.
اقرأ أكثر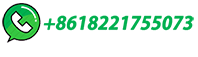