Effect of ball and feed particle size distribution on the …
Effect of ball and feed particle size distribution on the milling efficiency of a ball mill: An attainable region approach N. Hlabangana a, G. Danha b, *, E. Muzenda b a …
اقرأ أكثر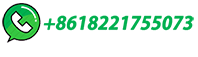
Large-scale production of ZnO nanoparticles by high energy ball milling …
We present a structural, microstructural, and optical study on ZnO nanoparticles produced in large quantities (600 kg) by high energy ball milling. Dynamic light scattering analysis indicated a decrease in the particle size from 416.60 to 33.27 nm for the sample without and with the maximum energy of milling performed, respectively.
اقرأ أكثر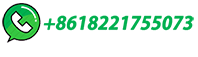
Ball Mills
Once the application requirements are clear, a suitable mill can be selected. To facilitate this process, Retsch displays the strength and efficiency of each ball mill model in a spider-net diagram, see Figure 3. A planetary ball mill, for example, offers a big jar volume compared to a mixer mill and shows a high value on this diagonal.
اقرأ أكثر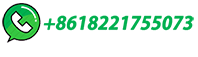
Ball Milling of Amaranth Starch-Enriched Fraction. Changes on Particle
Starch-enriched fractions of amaranth grain were obtained from planetary ball milling and subsequently studied for particle size reduction, hydration properties, and crystallinity loss. Wide-angle X-ray scattering (WAXS) was used to evaluate the crystalline of starch-enriched fractions, using an iterative smoothing algorithm to estimate …
اقرأ أكثر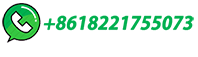
Effect of ball and feed particle size distribution on the milling
For this coarser feed the 50 + 20+10 mm ball diameter mix breaks the material at a faster rate compared to the other ball matches. The availability of a ball size for a particular feed size ensures breakage occurs at a faster rate. The 10 mm ball size …
اقرأ أكثر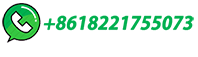
Calculate and Select Ball Mill Ball Size for Optimum Grinding
Based on his work, this formula can be derived for ball diameter sizing and selection: Dm <= 6 (log dk) * d^0.5 where D m = the diameter of the single-sized balls in …
اقرأ أكثر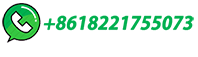
Effect of high energy ball milling on particle size and …
It was then subjected to a high-energy ball milling (HEBM) treatment under various milling speeds (600, 1200 and 1800 rpm) to produce AC nanoparticles from micro-size particles.
اقرأ أكثر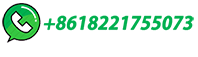
Calculate and Select Ball Mill Ball Size for Optimum Grinding
In Grinding, selecting (calculate) the correct or optimum ball size that allows for the best and optimum/ideal or target grind size to be achieved by your ball mill is an important thing for a Mineral Processing Engineer AKA Metallurgist to do. Often, the ball used in ball mills is oversize "just in case". Well, this safety factor ... title="Calculate and …
اقرأ أكثر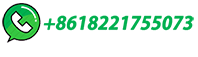
Effect of ball and feed particle size distribution on …
In another study to investigate ball size distribution on ball mill efficiency by Hlabangana et al. [50] using the attainable region technique on a silica ore by dry milling, a three-ball mix of ...
اقرأ أكثر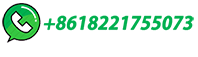
Ball Milling Guide
Larger balls are heavier and will be able to crush harder materials, but with less strikes per revolution, they will mill slower. Particle size. Ball milling has been used to grind materials to average particle sizes of 20 nanometres and finer, with extended milling time continuing to reduce particle size but with diminishing returns.
اقرأ أكثر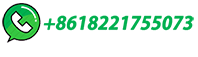
Effect of ball milling parameters on the particle size in
A model describing the mechanical comminution (ball milling) of crystals to nanocrystalline powders is proposed. It is shown that a fraction of the energy deposited in the processed material is spent for the creation of microstresses ɛ, …
اقرأ أكثر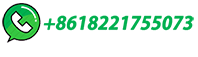
Grinding in Ball Mills: Modeling and Process Control
A ball mill is a type of grinder widely utilized in the process of mechanochemical catalytic degradation. ... The produced particle's size can be controlled by adjusting the size of grinding balls ...
اقرأ أكثر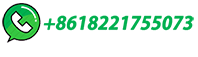
Ball Mill
The ball milling process is carried out for approximately 100–150 h to obtain uniform-sized fine powder. In high-energy ball milling, vacuum or a specific gaseous atmosphere is maintained inside the chamber. High-energy mills are classified into attrition ball mills, planetary ball mills, vibrating ball mills, and low-energy tumbling mills.
اقرأ أكثر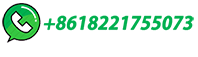
Effect of ball and feed particle size distribution on the milling …
In another study to investigate ball size distribution on ball mill efficiency by Hlabangana et al. [50] using the attainable region technique on a silica ore by dry milling, a three-ball mix of ...
اقرأ أكثر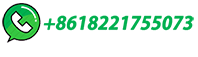
Exploring ball milling theory: A comprehensive guide
Principles of Ball Milling. Ball milling is a mechanical process that involves the rotation of a drum containing grinding media, typically steel balls, at a high speed. The materials to …
اقرأ أكثر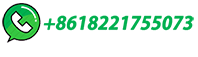
Top 5 product-specific milling technologies used in …
In a pin mill, the particle size is controlled by three parameters: Feed rate, rotor speed and airflow. ... Ball mill configuration. Ball mills use shear and impact milling techniques. Ball milling uses shear forces when particles are stressed between two surfaces that are moving in opposing directions. Particles experience impact forces as ...
اقرأ أكثر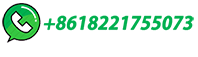
Impact of ball milling on the energy storage properties of …
Particle size reduction through ball milling presents an appealing approach to enhance the energy storage properties of lithium iron phosphate used in cathodes for lithium-ion batteries. However, the impact of ball milling conditions on electronic conduction and specific storage capacities remains poorly understood. In this …
اقرأ أكثر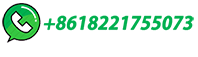
Curves Ahead: A Guide to Particle Size Distributions
One of powder's more dominate physical attributes is Particle Size Distribution (PSD) characteristics. Particle size and shape play an important role in the performance of any powder. Assurance of a powder's consistency, faithfulness of reproduction, and adherence to design are provided by any number of systems that …
اقرأ أكثر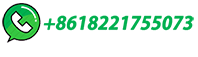
Unlocking the Potential of Corn Flour: A Study on the
Whole grain flours often exhibit suboptimal processing properties and palatability, limiting their usage in food industry. This study investigated the impact of ball milling on the physicochemical properties, thermal properties, crystalline structure and rheological properties of corn flour. Ball milling reduced the particle size of the powder …
اقرأ أكثر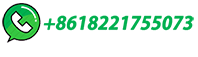
Prediction of ball milling performance by a convolutional …
1. Introduction. Ball milling is a critical process to reduce product size into a desired size range, which has been widely used in industries such as minerals processing, cement manufacturing, pharmaceutical industries and powder metallurgy [1, 2].The milling process is affected by many parameters, including ground particles, mill speed [3], …
اقرأ أكثر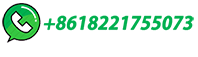
Effect of ball size and powder loading on the milling …
The effect of ball size on the particle size reduction has been investigated first for varying rotation speed of the container. Percent passing and size distributions of …
اقرأ أكثر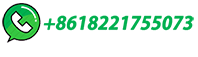
Ball milling promotes saccharification of agricultural biomass …
The ball milling results in different particle size distributions of materials powder. After that, all the feedstocks are dewaxed by 90% ethanol solution at 60 °C for 5.0 h. Importantly, in order to decrease the dosage of HPW, the dewaxed BSS powder with smallest particle diameters is milled in a teflon-lined cavity with addition of small ...
اقرأ أكثر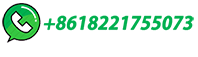
Influence of ball milling on the particle size and …
The herbal nanoparticles were prepared from shade dried Tridax procumbens plant leaves employing ball milling technique using different process parameters, like ball ratio/size and milling time. The obtained nanoparticles were comprehensively characterised using X-ray diffraction, Fourier transform infrared spectroscopy, UV-visible spectroscopy, dynamic …
اقرأ أكثر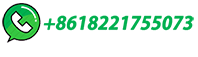
Effect of Milling Parameters on Size, Morphology, and …
In this work, the evolution of the size and morphology of Fe-Ga particles during vibration ball milling is documented and discussed. Low intensity (12 Hz) and …
اقرأ أكثر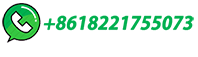
Handling the particle size and distribution of Fe3O4 …
A series of samples consisting of spinel Fe 3 O 4 nanoparticles with controlled particle sizes and increasing concentration has been obtained through 'mild' ball milling (BM) experiments by using an organic carrier liquid. We have succeeded in producing quite narrow particle size distributions with mean values 〈d〉∼7–10 nm by an appropriate …
اقرأ أكثر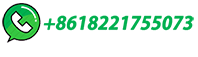
Minerals | Free Full-Text | Effects of Ball Size on the Grinding
In this study, we investigate the effect of the ball size in a high-energy ball mill on the comminution rate and particle size reduction. High-energy ball milling at 2000 rpm produces ultrafine talc particles with a surface area of 419.1 m2/g and an estimated spherical diameter of 5.1 nm. Increasing the ball size from 0.1 mm to 2 mm increases ...
اقرأ أكثر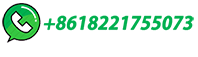
MODULE #5: FUNCTIONAL PERFOMANCE OF BALL …
particle size as the target grind size for the ball mill circuit; for ex-ample, it is convenient to select the desired 80% passing size as the target grind size. You can then use this …
اقرأ أكثر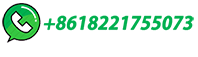
Handling the particle size and distribution of Fe3O4 nanoparticles
A series of samples consisting of spinel Fe 3 O 4 nanoparticles with controlled particle sizes and increasing concentration has been obtained through 'mild' ball milling (BM) experiments by using an organic carrier liquid. We have succeeded in producing quite narrow particle size distributions with mean values 〈d〉∼7–10 nm by an appropriate …
اقرأ أكثر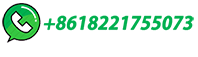
Customizing Silicon Particle Size and Shape Through Ball Milling …
Traditionally, ball milling is used to decrease particle size, however we have been able to utilize the cold-welding phenomenon with ball milling to increase the size of our Si powder particulates. Originally, the Si primary particles are between 10-100 nm in diameter as shown in figure 2a.
اقرأ أكثر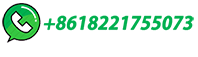
Evolution of grinding energy and particle size during dry ball-milling …
Fig. 1 a shows the oscillatory ball mill (Retsch® MM400) used in this study and a scheme (Fig. 1 b) representing one of its two 50 mL milling jars. Each jar is initially filled with a mass M of raw material and a single 25 mm-diameter steel ball. The jars vibrate horizontally at a frequency chosen between 3 and 30 Hz. The motion of the jar follows a …
اقرأ أكثر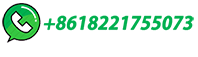