Optimization of a combined wet milling process in order to …
The article reports a wet milling process, where the planetary ball mill was combined with pearl milling technology to reach nanosize range of meloxicam (Mel; 100–500 nm). The main purpose was to increase the dissolution rate and extent of a poorly water-soluble Mel as nonsteroidal anti-inflammatory drug as well as to study its …
اقرأ أكثر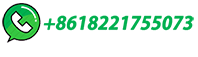
What is a Wet Milling Process?
Equipment Used in Wet Milling Process. The wet milling process requires specialized equipment that is designed to handle the unique properties of the materials being processed. Some of the common equipment used in the process include: Wet ball mills: These are used to mill materials by rotating a cylinder filled with steel balls.
اقرأ أكثر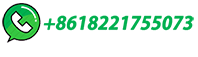
Ball Mill (Ball Mills Explained)
Crushed ore is fed to the ball mill through the inlet; a scoop (small screw conveyor) ensures the feed is constant. For both wet and dry ball mills, the ball mill is charged to approximately 33% with balls (range 30-45%). Pulp (crushed ore and water) fills another 15% of the drum's volume so that the total volume of the drum is 50% charged.
اقرأ أكثر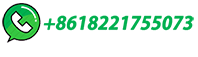
Effect of ball mill time and wet pre-milling on the …
This is as a result of the standard ball milling process mechanism. The ball milling process is a fabrication method in which the morphology and size of the particles can be controlled by exposing the particles to many mechanisms such as fragmentation, remodeling, and cold welding in a mill [40, 41]. During ball milling process cold welding ...
اقرأ أكثر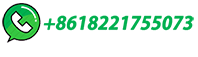
Physicochemical properties of ball milled boron particles: Dry vs. wet
Towards this direction, the grinding process of the powder, like dry/wet ball milling (BM), was employed to obtain smaller particle size and narrower size distribution [18, 19]. On the other hand ...
اقرأ أكثر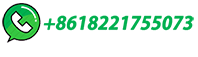
Effect of mechanochemical activation parameters on …
The particle size, surface area and other suitable characteristics shown in Fig. 1 required for industrial application as shown in Fig. 2 from a MA produced powder are notably influenced by the milling/ignition time, ball size, amount of milling energy input, BPR, rotational speed and the chemical concentration in the wet MA process as shown in Fig. 3.
اقرأ أكثر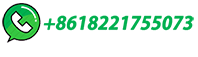
Wet Batch Laboratory Mills
Choosing the Right Laboratory Ball Mills; Conventional Ball Mill vs. Attritors; Planetary Ball Mills 101; ... (similar to those used on the Union Process DMQX Bead Mill) and run at RPMs of 1000 to 4200. The HDDM-01 features a special one-piece cover with charging port and slurry deflection device. This mill is recommended for wet grinding only ...
اقرأ أكثر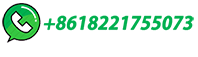
Attrition Mills and Milling
Wet Grinding Laboratory Mills Wet Batch Laboratory MillsWet Circulation Laboratory MillsChocolate Grinding Attrition MillsLimestone Slaker Ball Mill (CLS)Limestone Grinding Ball Mill (CL)Small Media Bead Mills (SDM) Wet Grinding Production Mills Wet Batch Production MillsWet Circulation Production MillsWet Continuous Production …
اقرأ أكثر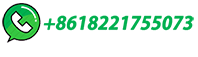
AMIT 135: Lesson 7 Ball Mills & Circuits – Mining Mill …
The process is continuously repeated as the particles move by mass and volume action through the mill. ... For wet ball mills, Bond expressed power draw as a function of the total mass of media:Pâ†"M / Mâ†"B – 15.6Φâ†"V (1 – 0.937 Jâ†"B) ...
اقرأ أكثر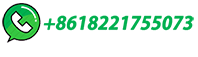
Modern Wet Milling and Material Processing
EMI Mills manufactures laboratory and production bead mills, mixers, and dispersers for wet milling, fine grinding, and dispersing of …
اقرأ أكثر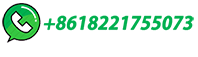
High Energy Ball Milling
The graph below compares various mills during the high energy ball milling process. Select a link to learn more about these Attritor-style stirred ball mills: Dry Grinding – Continuous or Batch Mode. Dry Grinding – …
اقرأ أكثر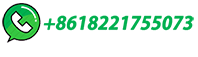
en/111/aluminium wet ball milling process.md at main
Contribute to dinglei2022/en development by creating an account on GitHub.
اقرأ أكثر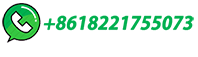
AMIT 135: Lesson 7 Ball Mills & Circuits – Mining …
Explain the role of ball mill in mineral industry and why it is extensively used. Describe different types of ball mill design. Describe the components of ball mill. Explain their understanding of ball mill operation. Explain …
اقرأ أكثر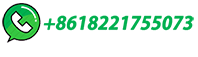
Wet ball milling of niobium by using ethanol, …
Milling was performed under the condition of a wet ball milling process. For the milling process, 40.12 g of the as-received Nb powder were loaded into two separate
اقرأ أكثر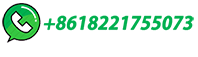
Wet Ball Mill for Metal Ores and Non-ferrous Metals Wet Milling
Wet ball mill is a kind of equipment which uses grinding medium and a certain amount of liquid (water or anhydrous ethanol) to grind materials. Unlike dry ball mill, wet ball mill adopts the wet grinding method. The characteristic of wet grinding is that the material needs to be soaked in the liquid for grinding. This method can effectively reduce the …
اقرأ أكثر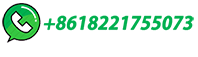
Wet ball milling of niobium by using ethanol, determination …
This study investigates the effect of using ethanol as the process control agent during the wet ball milling of niobium (Nb).
اقرأ أكثر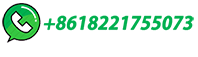
Silicon Powder Properties Produced in a Planetary Ball Mill …
Mechanical milling is a promising route for production of submicron and nano sized silicon powders, but it is challenging to predict and control the product properties. In this study a metallurgical grade silicon quality was milled in a planetary ball mill and the properties of the powder were investigated as a function of grinding time, …
اقرأ أكثر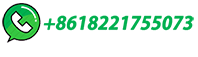
What Is a Ball Mill and How Does It Work?
Wet vs Dry Grinding. Mills can perform both wet and dry grinding, with the selection hinging on considerations like the properties of the material, desired product size, and energy consumption. ... The grinding process in a ball mill creates a smooth and homogenous mixture, essential for producing high-quality ceramics.
اقرأ أكثر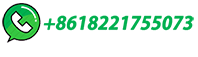
What is the Principle of Wet Ball Mill?
In the process of wet ball milling, the grinding media are typically made of steel or ceramics, and they are loaded into the mill in a specific proportion. As the cylinder rotates, the grinding media and the material being ground are subjected to centrifugal and frictional forces, which cause the grinding media to fall and impact the material ...
اقرأ أكثر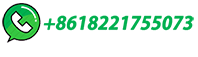
Ball Mill Loading
Talk with the Experts at Paul O. Abbe about your process requirements and Ball Mill Loading, Wet Milling, Size Reduction needs. About Section 179; 630-350-3012; sales@pauloabbe; ... loading should leave some air space above the liquid to allow for expansion of the liquid as it heats up during the milling process. So as a rule of thumb …
اقرأ أكثر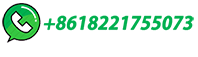
Estimation of product relating energy of wet operated …
Compared with the original two-stage ball milling process, the cost of grinding power consumption is significantly reduced by about 50.16%, which provides a reference for the subsequent research on energy saving and consumption reduction in ball milling operations. ... In the wet milling process, the ceramic slips are formed by 30 …
اقرأ أكثر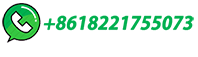
Producing Metal Powder from Machining Chips …
Two stages of the ball milling process were proposed, which involve a first stage of wet ball milling and a second stage of dry ball milling to produce a fine powder. The results showed that the ball …
اقرأ أكثر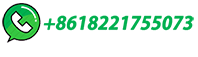
Pharmaceutical nanocrystals: production by wet milling …
Wet media milling equipment used for the production of nanosuspensions can be divided into planetary ball mills and wet stirred media mills. Planetary ball mills are high-energy ball mills and their name is derived from the kinematics of the grinding components, which are analogous to the rotation of the Earth around the sun.
اقرأ أكثر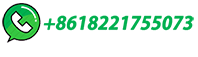
Planetary Ball Mills 101
The lack of shrouding allows the use of a water jacket on the tank in an internally agitated ball mill, providing cooling or heating to aid in the grinding process. Unlike planetary ball mills, Attritors offer the advantage of being able to sample the material during milling without having to stop the process. Formulation adjustments and grind ...
اقرأ أكثر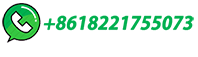
Effect of ball size and powder loading on the milling …
Wet ball mill is one of the most predominantly used method for the purpose of mixing and grinding of raw materials in laboratories and industry [1], [2], [3]. The ball mill process is very complicated process governed by many parameters, such as ball size, ball shape, ball filling, slurry loading (with respect to ball amount), powder loading ...
اقرأ أكثر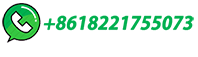
Modern Wet Milling and Material Processing
Traditional Wet Milling. The coatings industry is no different from others in its search for modern manufacturing techniques. The traditional high-speed dissolver, ball mill, vertical mill and standard …
اقرأ أكثر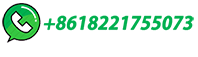
Extended Lifespan of Low-Cost Metal Silicon Anodes via a One-Step Wet
Herein, we report the fabrication of submicron Si particles coated by a polyacrylonitrile (PAN) layer with a highly polar nitrile group via a facile one-step wet ball-milling process. During the milling of Si particles in PAN solutions, PAN adheres to the Si surface and forms a nanometer coating layer.
اقرأ أكثر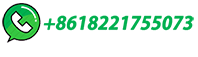
Physicochemical properties of ball milled boron particles: Dry vs. wet
In the wet milling process, the boron powder and tungsten carbide ball were put into the milling jar as in the dry milling process. Also, 15 ml of anhydrous hexane (Sigma-Aldrich, purity of 95%) as a solvent and 1 ml of oleic acid (Sigma-Aldrich, USA) as a coating material were added to the milling jar.After the grinding process, cleaning and …
اقرأ أكثر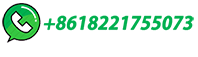
Materials Development Using High-Energy Ball …
High-energy ball milling (HEBM) of powders is a complex process involving mixing, morphology changes, generation and evolution of defects of the crystalline lattice, and formation of new phases. This …
اقرأ أكثر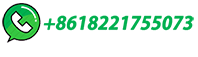
Overview of milling techniques for improving the solubility …
This technology, first developed by Liversidge and co-workers [76], [77], is a classical wet milling technique wherein a sufficiently concentrated dispersion of drug particles in an aqueous or non-aqueous liquid medium is subjected to a traditional ball milling operation [77], [78]. The liquid medium prevents adhesion and subsequent …
اقرأ أكثر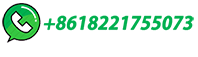