Understanding Pellets and Pellet Plant Operations
Fig 2 Typical schematic diagram of straight grate system. The grate-kiln system depicted in Fig 1 consists of a traveling grate for drying and preheating the pellets to about 1040 deg C, a rotary kiln for uniformly heating the throughput to the final induration temperature of 1315 deg C, and an annular cooler for cooling the product and heat …
اقرأ أكثر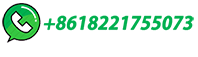
Understanding the mechanism: How does a ball mill work?
A ball mill is a versatile and efficient tool for the grinding and blending of materials. Its working principle, based on impact and friction between rotating balls and the powder materials, results in the fine grinding and refinement of the material. The components of a ball mill, including the drum, grinding media, liners, and drive system ...
اقرأ أكثر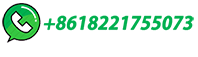
Review on vertical roller mill in cement industry & its …
In the study the advantages of vertical roller mill are discussed over ball mills. VRM construction, its process and parameters which affects the performance and productivity of vertical roller mill are discussed. ... Now a days Cement plants are producing 75–80% PPC & 20–25% OPC due to high market demand of PPC. …
اقرأ أكثر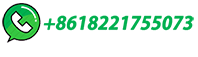
A new model-based approach for power plant Tube-ball mill …
In the reported work, mill model parameter sensitivity analysis was performed and the results were used to guide parameter optimisation. Tube-ball mill is another dominant type of coal mill apart from Vertical Spindle mill in industry. Compared with the Vertical Spindle mills, Tube-ball mills have a much higher grinding capacity.
اقرأ أكثر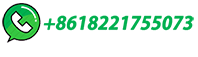
A Review of Advanced Ball Mill Modelling
Introduction. In spite of the development and increase in popularity of several other technologies, such as vertical roller mills, stirred media mills and high-pressure grinding …
اقرأ أكثر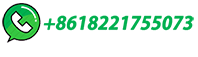
The operating principle of the ball mill
The operating principle of the ball mill consists of following steps. In a continuously operating ball mill, feed material fed through the central hole one of the caps into the drum and moves therealong, being exposed by grinding media. The material grinding occurs during impact falling grinding balls and abrasion the particles between …
اقرأ أكثر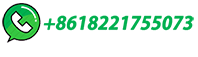
The Cement Plant Operations Handbook
4. Tromp curve – 5. Mill critical speed - 6. Charge volume loading – 7. Grace factor and other ball mill parameters – 8. Mill power – 9. Ball weight and surface area – 10. Maximum ball size required –11. Measurement of wear – 12. Effects of gypsum upon setting time B5. Kilns and burning 284 1. Cement compounds and ratios – 2 ...
اقرأ أكثر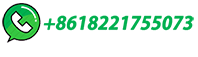
(PDF) Performance optimization of an industrial ball mill …
An increase of over 10% in mill throughput was achieved by removing the ball scats from a single -stage SAG mill. These scats are non- spherical ball fragments resulting from uneven wear of balls ...
اقرأ أكثر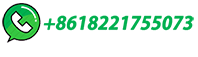
Design considerations for large diameter ball mills
Large mill (D>5.0 m (16.5 ft)) performance has been successfully predicted from small scale batch experiment for grinding kinetics and an RTD correlation for transport using population balance models.The effect of ball size must be properly taken into account in the scale-up. A design method that combined the kinetic scale-up findings and the …
اقرأ أكثر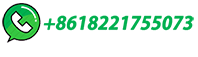
Operational parameters affecting the vertical roller mill …
In this study, pilot scale tests were performed with a mobile vertical-roller-mill grinding plant to investigate the relationships between operational parameters. The identification and quantification of the grinding parameter relationships was carried out to implement these relationships into a computational vertical-roller-mill performance model.
اقرأ أكثر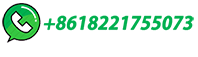
Factors Affect The Output and Quality of Ball Mills And How …
In addition to process factors, the model and parameters of the ball mill and the work of production, repair, and maintenance personnel also affect the …
اقرأ أكثر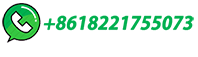
Manna and Ball to develop aluminium can facility …
US-based enterprise and investment firm Manna Capital Partners has partnered with aluminium packaging company Ball to develop and operate an advanced aluminium can sheet rolling mill in New …
اقرأ أكثر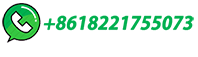
BALL MILLS Ball mill optimisation
Ball mill optimisation As grinding accounts for a sizeable share in a cement plant's power consumption, optimisation of grinding equipment such as ball mills can provide significant cost and CO 2 emission benefits to the cement producer. n by Thomas Holzinger, …
اقرأ أكثر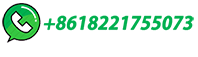
Factors Affect The Output and Quality of Ball Mills And How …
3. The ball mill is of good quality. The better the quality of the ball mill, the more stable the performance of the ball mill will be during operation. In addition, as for the lining plate of the ball mill's wearing parts, the quality of the lining plate affects the overall production efficiency of the ball mill. As we all know, the lining ...
اقرأ أكثر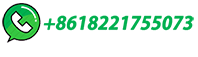
Optimization of Cement Grinding Operation in Ball Mills
Several energy efficient options for cement grinding are available today such as vertical roller mills, roller presses (typically in combination with a ball mill), and clinker pre-grinders with ball mills. Ball mills have been the traditional method of comminution in the mineral processing industries and continue to operate with old generation ...
اقرأ أكثر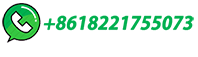
Grinding in Ball Mills: Modeling and Process …
The paper presents an overview of the current methodology and practice in modeling and control of the grinding process in industrial …
اقرأ أكثر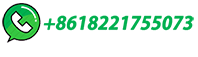
Inventory Of Common Faults And Solutions Of Mining Ball Mill
Reason: This is a common problem mining ball mills face, resulting in low productivity and low ore processing efficiency. One reason may be the improper design of the grinding chamber, which affects the flow of materials and reduces grinding efficiency. Additionally, worn or damaged liners can hinder the grinding process by reducing the …
اقرأ أكثر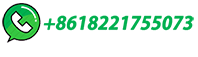
Grinding in Ball Mills: Modeling and Process Control
Grinding in ball mills is an important technological process applied to reduce the size of particles which may have different nature and a wide diversity of physical, mechanical …
اقرأ أكثر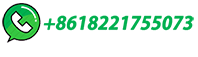
What is a Ball Mill Explained: In-Depth Guide
Critical Speed: Critical speed is the hypothetical speed at which the centrifugal force is equal to the gravitational force, and the grinding media starts sticking to the inner shell of the equipment instead of falling freely.Grinding at or close to critical speed of the mill yields a poorer grinding efficiency. The ball mills are mostly operated at 65 …
اقرأ أكثر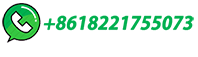
The truth about population balance modeling
While recognized as playing a key role in semi-autogenous and autogenous grinding mills, particle abrasion is ignored—or rather is absorbed—by ball mill PBM …
اقرأ أكثر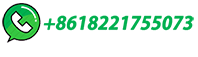
Grinding in Ball Mills: : Modeling and Process Control
Experimental Investigation on a Grinding Rate Constant of Solid Materials by a Ball Mill - Effect of Ball Diameter and Feed Size. - Powder Technology, Vol. 143/144, 2004, 196-203. Google Scholar
اقرأ أكثر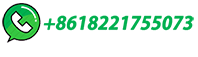
Ball Mills
Ball Mills for laboratories and pilot plants. For smaller capacities and laboratory use we manufacture grinding mills with sizes according to the table below. ... The parameter Wi, known as the work index of the ore, is obtained from batch bench tests first devised by Bond (1961). The power calculated on using equation 1, (Bond, 1961; …
اقرأ أكثر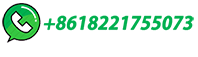
Autogenous and Semi-autogenous Grinding Circuits
the AG/SAG mill (because there is no recycle), but loads the ball mills instead. Often an existing plant that observes their SAG mill is limiting throughput, but the ball mills are …
اقرأ أكثر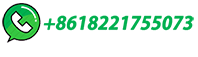
Ball Corporation
Manna Capital Partners, a minority-owned business enterprise and investment firm, and Ball Corporation (NYSE: BALL), a leading global provider of infinitely recyclable aluminum beverage packaging, today announced an alliance in which Manna will construct and operate a state-of-the-art aluminum can sheet rolling mill and recycling …
اقرأ أكثر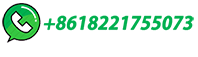
The Impact of Ball Milling Process Parameters on the Preparation …
In order to explore the impact of different ball milling technical parameters on the grain size of nano silicon powder, this paper adopted the orthogonal experimental design in combination with fitting analysis, and set the agitator shaft speed of the ball mill and the milling time as the influence factors. Then this paper studied the impact of ...
اقرأ أكثر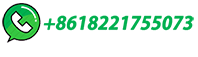
EVERY COMPONENT OF BALL MILL DETAILED & EXPLAINED
Fine Grinding and Mill Cooling. PROBLEM. Insufficient mill cooling lead to material agglomeration on balls and liners. The grinding is not any more done by balls against material but by material against material. SOLUTION. Adapted mill cooling, playing with:-Clinker temperature-Mill ventilation-Water injection
اقرأ أكثر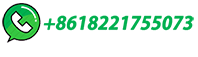
How to Improve Ball Mill Performance
In the simplest form of plant experimentation, a key performance parameter (such as the fineness of the final product) is measured with and without a specific change to the circuit.
اقرأ أكثر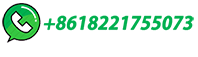
What Is a Ball Mill and How Does It Work?
The ball mill rotates around a horizontal axis, allowing the grinding process to take place as the balls reduce the material to a fine powder. A mill consists of trunnion bearings that support the shell, ensuring that the mill can accommodate the weight of the grinding charge.
اقرأ أكثر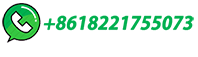
Horizontal roller mill (Horomill®) application versus hybrid HPGR/ball
They were introduced in 1993 at Buzzi Unicem's Trino plant in Italy with the purpose of reducing energy costs. Details of the operating principle of Horomill ® as compared to HPGR and vertical roller mills are given by Cordonnier (1994) and Buzzi (1997).The energy saving of this mill is claimed to be similar to that of HPGR and …
اقرأ أكثر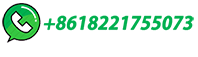
(PDF) Population balance model approach to ball mill …
The selection and breakage parameters and the specific selection functions were determined for pellet feed iron ore. ... in the pilot and plant scale mills (0.416 and 5.18 m diameter, respectively ...
اقرأ أكثر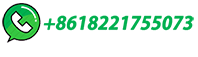