The working principle of ball mill
The ball mill consists of a metal cylinder and a ball. The working principle is that when the cylinder is rotated, the grinding body (ball) and the object to + (86) 073128420963. ... This is the critical speed of the 180 litre wet mill currently used in cemented carbide production.
اقرأ أكثر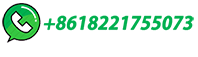
The Ultimate Guide to Understanding Ball Mill Diagrams
The ball mill diagram shows the main parts of a ball mill, including the feeding device, the cylinder, the discharge device, the hollow trunnion, the transmission device, the gear …
اقرأ أكثر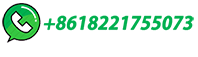
Aggregate Wet Ball Mill – Rainhart
The Rainhart Aggregate Wet Ball Mill is used to determine the resistance of aggregate in flexible base materials to disintegration in the presence of water. These results are essential in determining whether the base will resist crushing, degradation, disintegration, and premature structural failure.
اقرأ أكثر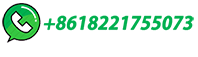
Solved (55) 3. A wet ball milling operation is used to
A wet ball milling operation is used to grind crude ore into smaller particles of a desired size classification. As shown in the diagram below a slurry of crude ore and water (Stream 1) is fed into a ball mill along with a recycle stream (Stream 2). The mill product (Stream 3) is sent to a mechanical classifier where additional ...
اقرأ أكثر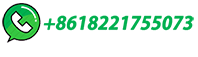
Everything You Need to Know About Wet Media Milling, …
Wet milling machines can include horizontal media mills, attritor mills, cascading type ball and/or bead mills, and basket or batch mills. Unlike dry mechanical and jet milling processes, wet milling requires multiple, specific steps that can vary based on different characteristics of the raw feed.
اقرأ أكثر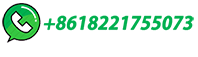
Wet Process Of Cement Manufacturing With …
As the per-flow diagram of the wet process of cement manufacturing, the rotary kiln is an essential and important component of a cement manufacturing factory. ... 13. These cooled clinkers are then taken in a …
اقرأ أكثر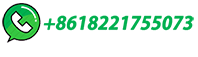
_Taurus
NETZSCH Taurus Ball Mill, the pinnacle of fine and ultra-fine grinding technology. Achieve precise particle sizes with durable, low-maintenance equipment. ... Wet Grinding Dry Grinding Mixing / De-Aerating Dispersing & Homogenizing Classifying Dedusting & Separating Laboratory Machines / Systems Grinding Media, ...
اقرأ أكثر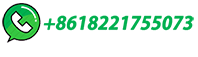
Ball Milling Method for Synthesis of …
The ball mill system consists of one turn disc (turn table) and two or four bowls. The turn disc rotates in one direction while the bowls rotate in the opposite direction. The centrifugal forces, created by the rotation of the …
اقرأ أكثر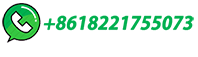
Ball Mills | Industry Grinder for Mineral Processing
A ball mill, also known as a ball grinding machine, is a well-known ore grinding machine widely used in mining, construction, and aggregate applications.JXSC started the ball mill business in 1985, supplying global services including design, manufacturing, installation, and free operation training.
اقرأ أكثر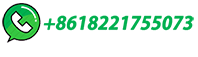
Ball Mill Working Principle, Construction, Applications, …
Ball mills produce 1 to 50 ton/h power of which about 70 to 90 percent would pass a 200 mesh screen and the energy requirement of a ball mill is about 16 kWh/t. In the case of the batch-operated mill, a measured quality of a solid to be ground is charged into the mill through an opening in the shell.
اقرأ أكثر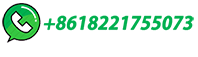
AMIT 135: Lesson 6 Grinding Circuit – Mining Mill …
Pebble mill diagram [image: (135-6-13)] Wet or dry; Always grate discharge; Secondary grinding; Grinding media : A size fraction screened out from feed; Flint pebbles; ... Special Tumbling Mill Special tumbling mills [image: (135-6-14)] Conical Ball Mill. Wet or dry (air swept) Overflow or partial grate; Conical shell for "graded" ball ...
اقرأ أكثر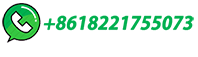
Ball Mill for Cement Grinding Process
Cement Ball Mill Structure. When Ball Mill is working, raw material enters the mill cylinder through the hollow shaft of the feed. The inside of the cylinder is filled with grinding …
اقرأ أكثر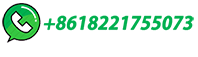
Process Training Ball Mill
Process Training Ball Mill. ... With the help of the diagram (Picture 11) the filling level of a ball mill can be determined: ... the temperature of the mill exit air constant at a suitable value by letting in fresh air or by dosing water into the mill. In the case of wet additives, on the other hand, it may be necessary to heat the system. ...
اقرأ أكثر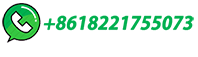
Process engineering with planetary ball mills
Planetary ball mills are well known and used for particle size reduction on laboratory and pilot scales for decades while during the last few years the application of planetary ball mills has extended to mechanochemical approaches. Processes inside planetary ball mills are complex and strongly depend on the processed material and synthesis and, thus, …
اقرأ أكثر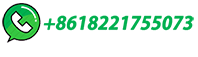
Ball Mill (Ball Mills Explained)
Crushed ore is fed to the ball mill through the inlet; a scoop (small screw conveyor) ensures the feed is constant. For both wet and dry ball mills, the ball mill is charged to approximately 33% with balls (range 30-45%). …
اقرأ أكثر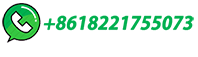
Exploring Ball Mill Diagram: A Comprehensive Guide
The rotation of the mill is driven by the motor, the power of which is determined by the mill's size and the grinding capacity. Ball mills can be as small as …
اقرأ أكثر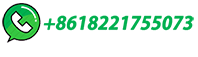
Ball mill: Principles, construction, working, uses, merits, and
1. Cylindrical Shell: The ball mill consists of a hollow cylindrical shell that rotates about its axis. The shell is usually made of steel, stainless steel, or rubber. 2. Liners: An abrasion-resistant material such as manganese steel or rubber typically lines the inner surface of the cylindrical shell to protect it from wear due to the grinding action.
اقرأ أكثر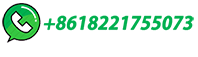
What Is a Ball Mill and How Does It Work?
Wet vs Dry Grinding. Mills can perform both wet and dry grinding, with the selection hinging on considerations like the properties of the material, desired product size, and energy consumption. In wet grinding, ... Ball mills grind materials into an extremely fine form. The ball mill contains a hollow cylindrical shell that rotates about its axis.
اقرأ أكثر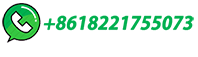
Fluid energy mill
Ball Mill Principles Ball mills, sometimes referred to as pebble mills or tumbling mills, are milling machines that take the form of cylindrical vessels containing balls mounted on a metallic frame that can revolve around its longitudinal axis. Depending on the feed and mill size, balls with varying diameters occupy 30 - 50 % of the mill volume.
اقرأ أكثر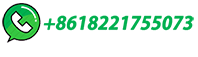
Multi-Compartment Rod/Ball Mill Evaluation on Bauxite …
Rod mills generate small amounts of fines, as fine particles typically accumulate in the space between rods without enduring comminution [2]. Effective grinding of this material occurs in the ball mill compartment, generating finer fragmentation. The Bond Rod Mill Work Index (BRMWI) test was only possible for Blend 5 (Table 2) due to excessive
اقرأ أكثر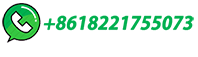
EVERY COMPONENT OF BALL MILL DETAILED
Fine Grinding and Mill Cooling. PROBLEM. Insufficient mill cooling lead to material agglomeration on balls and liners. The grinding is not any more done by balls against material but by material against material. …
اقرأ أكثر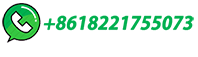
A schematic diagram of a tubular ball mill. The balls compose …
Download scientific diagram | A schematic diagram of a tubular ball mill. The balls compose the milling elements and drive rollers help to rotate the milling chamber. Adapted from Loh et al. [12] .
اقرأ أكثر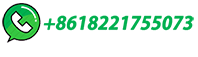
Energy-Mass-Size balance model for dynamic control of …
A dynamic model is developed for a wet overflow ball mill based on a set of mass and energy balances to simulate the mill. The energy balance relies on temperature and mass flow data. The key control parameters to be measured are mill temperature (feed and discharge streams), mill power draw and the mass flow rate in the feed stream.
اقرأ أكثر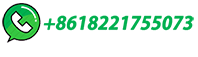
Ball mill for cement grinding
An inefficient ball mill is a major expense and could even cost you product quality. The best ball mills enable you to achieve the desired fineness quickly and efficiently, with minimum energy expenditure and low maintenance. With more than 4000 references worldwide, the FL ball mill is proven to do just that.
اقرأ أكثر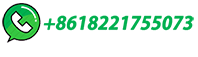
Closed Circuit Grinding VS Open Circuit Grinding …
From a theoretical point of view, the ideal method of grinding would consist of a series of ball mills, each in closed circuit with a classifier and each so short that the ore in its passage through the mill would be …
اقرأ أكثر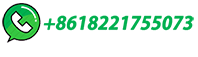
Modern Wet Milling and Material Processing
Traditional Wet Milling. The coatings industry is no different from others in its search for modern manufacturing techniques. The traditional high-speed dissolver, ball mill, vertical mill and standard horizontal mill have been the primary methods used to mill pigmented materials for more than 50 years, and are still considered to be the industry …
اقرأ أكثر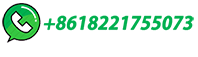
Grinding in Ball Mills: Modeling and Process Control
Keywords: Ball mills, grinding circuit, process control. I. Introduction Grinding in ball mills is an important technological process applied to reduce the size of particles which may …
اقرأ أكثر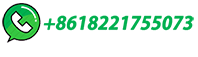
ATTRITORS AND BALL MILLS HOW THEY WORK
IV. BALL MILLS Ball mills are one of the more common mills and use a closed cylindrical container that is rotated horizontally on its axis so that the media cascades. A typical ball mill has an L/D ratio of 1.5:1. Ball mills are filled with spheres or other shapes made of steel or ceramics; or with pebbles made of flint (or of an ore being ground).
اقرأ أكثر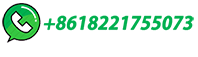
Wet Milling vs Dry Milling: The Differences, …
There are many types of mills in the market for both wet and dry milling, and the selection process can be daunting, but with the right equipment to meet your industrial milling needs, you can cost-effectively …
اقرأ أكثر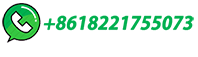
Ball Mill- Principle, Application, Uses, Critical Speed, Diagram
The cylindrical shell, grinding media, and material being ground all play important roles in the performance of a ball mill. The diagram provided gives a visual representation of the components of a typical ball mill. Critical Speed of Ball Mill Critical Speed of Ball Mill.
اقرأ أكثر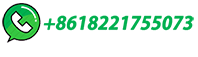