Inventory Of Common Faults And Solutions Of Mining Ball Mill
Reason: This is a common problem mining ball mills face, resulting in low productivity and low ore processing efficiency. One reason may be the improper design of the grinding chamber, which affects the flow of materials and reduces grinding efficiency. Additionally, worn or damaged liners can hinder the grinding process by reducing the …
اقرأ أكثر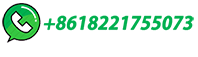
Population balance model approach to ball mill …
3 BALL MILL MODEL The population balance model may be expressed by Equation (1): > @ ¦ i-1 1 i b ij m j j i j i S Ht dt d H m t (1) where: S i (t) is the size discretized selection function for ...
اقرأ أكثر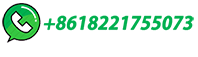
Ball Mill
You can apply our ball mill in ore beneficiation plant to grind iron ore, copper ore, gold ore, lead ore, zinc ore, kaolin, bentonite, feldspar, silica, etc. Grid Type Ball Mill The Grid Type Ball Mill has high discharge speed and high productivity (20-30% higher than overflow type and 20-30% power saving).
اقرأ أكثر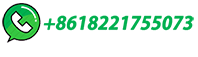
Simulation of wet ball milling of iron ore at Carajas, Brazil
Section snippets Laboratory-scale batch grinding tests. The tests were made in a steel cylindrical ball mill of 250 mm internal diameter (D T) and 250 mm length (L T) fitted with eight symmetrically located horizontal lifters (see Table 1) and smooth end walls, with one end wall removable and locked in place with a quick release locking clamp.The …
اقرأ أكثر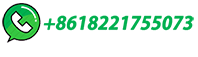
Ball Mill
Ball Mill Working Principle High energy ball milling is a type of powder grinding mill used to grind ores and other materials to 25 mesh or extremely fine powders, mainly used in the mineral processing industry, both in open or closed circuits. Ball milling is a grinding method that reduces the product into a controlled final grind and a uniform size, usually, …
اقرأ أكثر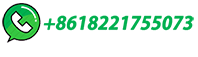
AMIT 135: Lesson 7 Ball Mills & Circuits – Mining Mill …
Mill Type Overview. Three types of mill design are common. The Overflow Discharge mill is best suited for fine grinding to 75 – 106 microns.; The Diaphram or Grate Discharge mill keeps coarse particles within the mill for additional grinding and typically used for grinds to 150 – 250 microns.; The Center-Periphery Discharge mill has feed reporting from both …
اقرأ أكثر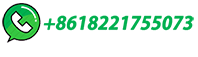
Ball Mill
The characteristic tumbling motion of these mills has given them the name 'tumbling mills', which include the ball mill, tube mill and rod mill. Ball mills are horizontal rotating cylindrical or conical steel chambers, approximately one third to half full of steel, alloy steel or iron balls, like that shown in Fig. 4.10 A–C, or flint stones.
اقرأ أكثر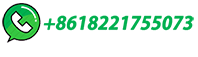
Wet Pan Mill
Wet Pan Mill also known as amalgamation grinding mill, gold grinder mill, which is a versatile ore grinding pan mill for wet materials. It's the best replacement for a medium-small capacity ball mill, owing to the excellent performance for wet crushing, small investment, and high output, widely used for separating gold, iron, molybdenum, lead, …
اقرأ أكثر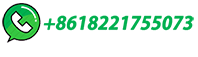
Simulation of wet ball milling of iron ore at Carajas, Brazil
A. First-order plots for batch dry grinding of feeds of 16 × 20, 35 × 45, 45 × 60 mesh iron ore. B. First-order plot for dry grinding of 4 × 6 mesh (oversized particles) iron ore: effective S ...
اقرأ أكثر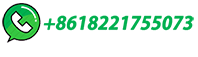
Rotary Scrubber
The trommel scrubbers are mainly applied for washing gold, diamond, and other ore (including manganese, copper, tantalum-niobium-tin, iron ore, silica sand, fluorite, etc.). It is often called gold wash trommel or …
اقرأ أكثر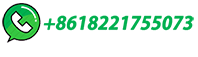
How Ball Mill Ore Feed Size Affects Tonnage & Capacity
For the purposes of this example, we will hypothesize that the the crushing index of the hard ore with the increased energy input of 1.54 kw/t reduces the ball mill feed size to 6,500 micrometers. As a result, the mill output will increase with this reduced size to approximately 77,000 tons per day.
اقرأ أكثر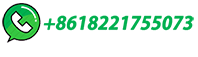
Ball Mills in the Mineral Processing Industry
The General Function of Ball Mills. A ball mill is a grinder used for grinding and blending materials for mineral dressing processes, paints, pyrotechnics, ceramics, and selective laser sintering. Appearance. Ball mills have various designs and functions, ranging from laboratory-scale versions to large industrial models.
اقرأ أكثر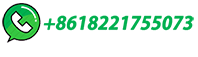
Ball Mills | Industry Grinder for Mineral Processing
JXSC is a professional ball mill, rock crusher OEM, Our ball mills are designed for long service life with minimum maintenance and grind and homogenize ores down to the nano range in a large capacity.
اقرأ أكثر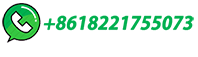
Optimization of Solids Concentration in Iron Ore …
The paper demonstrates the application of this methodology to optimize solids concentration in ball milling of an iron ore from Brazil. The wet grinding experiments were conducted in bench (0.25 m …
اقرأ أكثر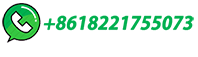
A Review of the Grinding Media in Ball Mills for Mineral …
The ball mill is a rotating cylindrical vessel with grinding media inside, which is responsible for breaking the ore particles. Grinding media play an important role in …
اقرأ أكثر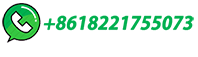
Mineral and Technological Features of …
Mineralogical studies have established that the main iron-bearing mineral is hematite, which contains 69.02 to 70.35% of iron distributed in the ore. Magnetite and hydrogoethite account for …
اقرأ أكثر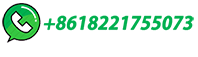
Investigation on Iron Ore Grinding based on Particle Size Distribution
The feed samples of X, Y, and Z iron ores were ground in the BBM (ball mill refers to a BBM of size 300 mm × 300 mm with smooth liners) to identify the PSD, BWI, and RT of each ore. Grinding experiments were conducted according to Bond's standard test procedure [].For each iron ore sample, the RT taken to produce 250% circulating …
اقرأ أكثر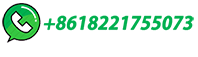
AMIT 135: Lesson 7 Ball Mills & Circuits – Mining Mill …
Explain the role of ball mill in mineral industry and why it is extensively used. Describe different types of ball mill design. Describe the components of ball mill. Explain their …
اقرأ أكثر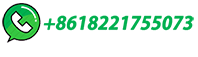
Wet Overflow Type Ball Mill and Applications
How Overflow Type Ball Mill Works. Material Feed: The raw material is fed into the mill at one end and travels through the mill by rotation. The feed enters the mill at a specific rate, ensuring a controlled grinding process.; Grinding Process: As the mill rotates, the grinding media crushes and grinds the material into a fine powder. The wet …
اقرأ أكثر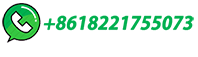
Factors Affect The Output and Quality of Ball Mills And How …
3. The ball mill is of good quality. The better the quality of the ball mill, the more stable the performance of the ball mill will be during operation. In addition, as for the lining plate of the ball mill's wearing parts, the quality of the lining plate affects the overall production efficiency of the ball mill. As we all know, the lining ...
اقرأ أكثر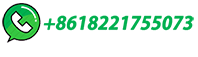
Iron ore pelletization
Iron ore mineral: The grate-kiln is best suited for magnetite and magnetite/hematite mixtures, while the straight grate is suitable for all types of feed (a) Hematite: Yes a: ... For example, a wet ball mill plus an HPGR circuit was installed in WISCO Minerals' pellet plant in China to pretreat Brazilian specularite concentrates.
اقرأ أكثر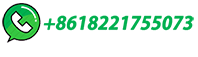
How an Overflow Ball Mill Works?
The overflow ball mill can grind iron ore, copper ore, ferrous metal, and non-ferrous metal, and is very popular in metallurgy, building materials, construction, the chemical industry, and other fields. It belongs to high-end equipment. It is generally used as the core equipment in the mineral processing production line.
اقرأ أكثر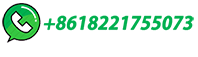
Impact of ball filling rate and stirrer tip speed on milling iron ore
DOI: 10.1016/J.POWTEC.2020.09.052 Corpus ID: 224926570; Impact of ball filling rate and stirrer tip speed on milling iron ore by wet stirred mill: Analysis and prediction of the particle size distribution
اقرأ أكثر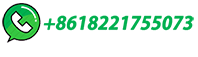
Iron Ore Pelletization Technology and its Environmental …
The details of the major plant facilities and their capacities are as follows: Table 9. Plant Facilities at Unit II Sr. No. Plant facilities Capacities (i.) Ball mills( Iron Ore grinding system) 2X 50 TPH (ii.) Vacuum Disk Filter 4X 50 TPH (iii.) Coal Grinding System 1X 5 TPH (iv.) flux and coke grinding System 1X 5 TPH (v.) Mixer 1X100 TPH (vi.)
اقرأ أكثر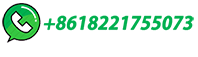
Research of iron ore grinding in a vertical-roller-mill
The application of vertical-roller-mills (VRM's) for ore grinding is part of the second strategy. The grinding parts of a Loesche mill (Fig. 1) are a rotating table (1) with a horizontal grinding track and rollers (2), which are pressed onto the table by lever arms and a hydro pneumatic spring system.
اقرأ أكثر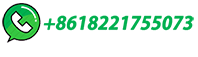
Ball Mill Design/Power Calculation
A wet grinding ball mill in closed circuit is to be fed 100 TPH of a material with a work index of 15 and a size distribution of 80% passing ¼ inch (6350 microns). …
اقرأ أكثر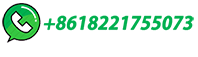
Lecture 11: Material balance in mineral processing
Key words: Material balance, ball mill, hydro cyclone, flotation. Preamble An important aspect of any mineral processing study is an analysis of how material is distributed …
اقرأ أكثر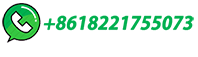
Ball Mills
Ball Mills. Ball mills have been the primary piece of machinery in traditional hard rock grinding circuits for 100+ years. They are proven workhorses, with discharge mesh sizes from ~40M to <200M. Use of a ball mill is the best choice when long term, stationary milling is justified by an operation. ... We bought a turn-key ore processing system ...
اقرأ أكثر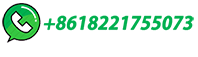
Scale-up procedure for continuous grinding mill design …
The work demonstrates the calibration of industrial-scale ball mill model parameters from laboratory milling tests on Platinum Group Metals (PGM) and Itabirite iron ores. Minor fine-tunning of a single model parameter was required to simulate the large-diameter industrial mills, demonstrating the validity of the approach for ores as distinct …
اقرأ أكثر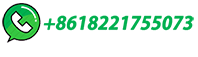