CBE Crusher buckets
CBE crusher buckets provide optimal performance when working with iron, rock, soil and deformable parts. Open an assistance ticket. Reserved area; Academy; ... Crushable materials: bricks, reinforced concrete, natural aggregates, concrete, tiles, glass and asphalt slabs. Unaffected by the presence of earth, wet or humid material, or iron rods. ...
اقرأ أكثر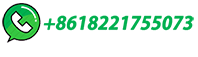
® HP350e™ cone crusher
The new ® HP350e™ cone crusher provides better performance and uptime in a more sustainable way. Menu Close About us. ... Classic HP300 liners with backing material can be used in the HP350e crushers alternatively, too. Wider application coverage. New application specific chambers: Coarse chambers EC (Extra Coarse) and C (Coarse) for ...
اقرأ أكثر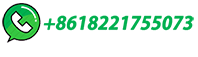
Understanding Industrial Crushers: Types And Applications
How does it work? Feed a glass crusher machine with glass containers, and its powerful mechanism, often featuring spinning metal discs or 'hammers,' grinds them …
اقرأ أكثر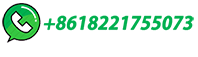
What Type of Crusher Is Best for Primary Crushing?
The material and its characteristics, e.g., its hardness, density, shape and condition, will affect the type of crusher that needs to be used. Knowing the material characteristics as well as the advantages and limitations of the different crusher types will help to determine the best primary crusher for a given application.
اقرأ أكثر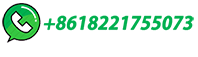
Types of Crushers Explained: Everything You Need to Know
Crushers are key equipment in mining, construction and aggregate industries. They break large rocks, ore, or other materials into smaller, more usable pieces. This equipment reduces the material by means of compressive force, impact, attrition or shear that are specific for the type of crusher being used.
اقرأ أكثر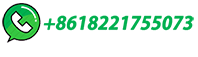
Crushing 101 – Different types of crushers for distinctive needs
Impact crushers are traditionally classified into two main types, horizontal shaft impact (HSI) crushers and vertical shaft impact (VSI) crushers. These different …
اقرأ أكثر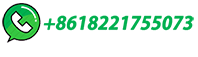
Aggregate Crushers, for Rock, Ore & Minerals
Marcy® Lab Cone Crusher is ideal for reducing aggregates and mineral ores. The Marcy® GY-Roll 6in (152mm) or 10in (254mm) Lab Cone Crushers have 300lb per hour (136kg) or 600lb per hour (272kg) throughput capacity. The throughput rate is dependent upon the material crushed; with coarser settings, the throughput capacity may be higher.
اقرأ أكثر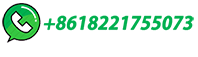
A Comprehensive Guide to Stone Crusher Machines
Stone crusher machines are essential tools in the construction industry, used to crush rocks and stones into smaller pieces for a variety of applications. This guide provides an overview of stone crusher machines, including their history, components, applications, and buying considerations. Whether you are a contractor, landscaper, or …
اقرأ أكثر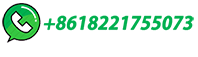
Primary Crusher vs. Secondary Crusher: …
Learn about the key differences between primary and secondary crushers and their respective functions in the mining and construction industry. Discover real-world applications and when to use …
اقرأ أكثر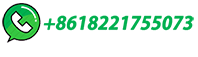
Crusher Run
Crusher Run gravel-- also known as 'Crush and Run', 'Crush N Run', 'Graded Aggregate Base ... The material is most commonly used in home projects as a compactible sub-base material. It is a combination of coarse and fine aggregates that form a solid, level base of support for the top layers of things like driveways, patios, and structural ...
اقرأ أكثر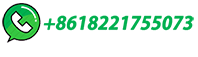
Crushers
The main purpose of a primary crusher is to reduce the material to a size that allows its transportation on a conveyor belt. In most crushing installations a jaw crusher takes care of primary crushing. Plants with very high capacities that are common in mining and less popular in aggregates production, normally use a primary gyratory crusher. ...
اقرأ أكثر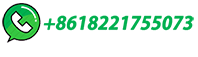
AusIMM – Leading the way for people in resources
%PDF-1.6 %âãÏÓ 4215 0 obj > endobj 4235 0 obj >/Encrypt 4216 0 R/Filter/FlateDecode/ID[87C03FABF6FB2246BC4F9AB649B4B217>]/Index[4215 26]/Info 4214 0 R/Length 101 ...
اقرأ أكثر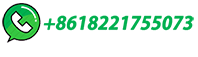
Industrial Lump Breakers & Crushers | DELUMPER
Franklin Miller's lump breakers and crushers excel at enhancing material processing efficiency. Our DELUMPER® crushers are expertly designed to reduce solids, lumps, and agglomerates to precise sizes through a once-through, non-churning action, minimizing fines and ensuring consistent product quality.
اقرأ أكثر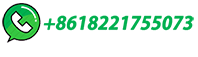
Roll Crushers
Single Roll Crushers. Single Roll Crushers are typically used as primary crushers that provide a crushing ratio of up to 6:1. They crush materials such as ROM coal, mine refuse, shale, slate, gypsum, bauxite, salt, soft shale, etc., while producing minimal fines.Designed with intermeshing roll teeth and a curved crushing plate, they are extremely effective in …
اقرأ أكثر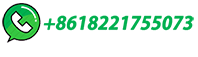
Cone Crushers – MEKA
When you need a crusher for aggregates production, our cone crushers are well known for its great performance, in terms of its high throughput capacity, high reduction and high end product quality. For mining applications they are typically used when maximum material size reduction in an open circuit is required. WHY MEKA CONE CRUSHER?
اقرأ أكثر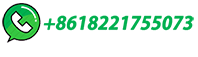
What Is 57 Stone Used For? A Comprehensive Guide
57 stone, also known as "crush and run" or "crusher run," is a mixture of stone dust and three-quarter inch crushed stone. It is commonly used as a base material for driveways, roads, and parking areas, as well as for drainage and erosion control projects. Its angular shape and high percentage of fines make it ideal for these …
اقرأ أكثر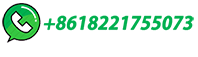
Choosing the Right Crusher
A crusher is a machine that uses mechanical energy to break blocks of stone, concrete, or other building materials into smaller blocks of a specific grain size. They are particularly used in the mining industry to reduce the size of ore blocks and facilitate their processing. Crushers are designed to receive blocks of a maximum […]
اقرأ أكثر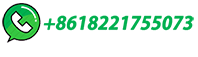
Type of crushers and their difference
Impact crusher can also be equipped with a bottom screen, which prevents material leaving the crusher until it is fine enough to pass through the screen. This type of crusher is usually used for soft and non abrasive materials. Roller Crusher. Roll crushers crush the material use two opposite rotation of the rollers.
اقرأ أكثر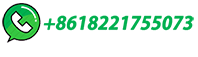
How Impact Crushers Work: A Comprehensive Guide
An impact crusher is a machine used to crush materials by impact energy. It works by feeding the material into a rotating rotor, which is equipped with a series of hammers. As the rotor spins, the hammers strike the material, causing it to break into smaller pieces. The basic working principle of an impact crusher
اقرأ أكثر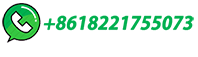
Crushers vs. Breakers: A Complete Guide for Choosing the
Method of feeding the raw material to the crusher, breaker or sizer; Desired production rate; Desired products; From this information, you will be able to narrow down whether a crusher, breaker or sizer is the best option. You may also be able to determine what type of crusher, breaker or sizer is best suited for the job.
اقرأ أكثر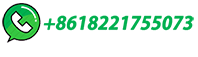
Choosing the right crusher for rock, stone, concrete and …
To choose a suitable crusher, you'll need to provide information about the material you plan to crush. The abrasiveness and hardness of the material determine the compressive strength it can withstand before breaking. The size of the feed material to determine the size of the crusher required.
اقرأ أكثر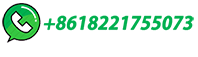
Types of Crushers: What You Need to Know
The material and its characteristics, e.g., its hardness, density, shape and condition, will affect the type of crusher that needs to be used. Knowing the material characteristics …
اقرأ أكثر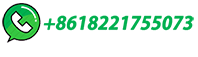
Construction, Working and Maintenance of
The first crusher in a crushing system into which material is fed. Succeeding crushers in the system are referred to as secondary (second), tertiary (third) or quaternary (fourth) crushers. Reduction Ratio The ratio of the top size of input material to the top size of crusher discharge material. Run of Mine (ROM)
اقرأ أكثر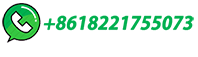
Primary Crusher vs. Secondary Crusher: Understanding Their …
The jaw crusher works by moving the material between a fixed and a moving plate. The moving plate applies force to the material, causing it to break down into smaller pieces. The gyratory crusher, on the other hand, uses a mantle and concave surfaces to compress the material. The mantle is located above the concave, and as …
اقرأ أكثر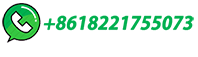
Primary Crusher Selection & Design
How you select your primary crusher will be based on factors like moisture content, maximum rock lump size, material density SG, abrasion index, degradability and it being prone to dusting or not. The crusher capacities given by manufacturers are typically in tons of 2,000 lbs. and are based on crushing limestone weighing loose about 2,700 …
اقرأ أكثر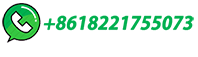
Types of Rock Crushers | Quarry Crushing Equipment | Kemper
It is common to use multiple crusher types within a project and set them up as stations in a circuit format to perform the necessary material reduction work. In many cases, primary, secondary, and tertiary, and quaternary stations are installed to reduce the rock to the desired size, shape, and consistency.
اقرأ أكثر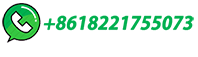
ALLU CRUSHER -CRUSHING BUCKET
1. Mainframe. 2. Upper jaw – safe and easy to replace. 3. Crushing plates – allow material to flow freely through jaws. 4. Streamline wear-resistant frame – no external parts for a long-lasting operational life. 5. Straight side and angled tip plates – provide a rigid frame, reduce the wear and provide a higher crushing filling rate. 6. Adjustable pin – for quick fragment …
اقرأ أكثر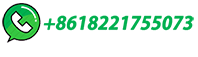
Primary and Secondary Crushing: Understanding …
Learn the differences between primary and secondary crushing and how to choose the right crusher for your mining or construction project. This guide explains the basics of crushing, the …
اقرأ أكثر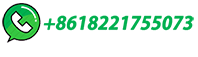
Understanding Industrial Crushers: Types And Applications
In any industrial setting, you'll encounter machinery integral to the workflow. One crucial type is industrial crushers. You might not realize it, but these machines are often the unsung heroes in mining, quarrying, recycling, construction, waste management, and the chemical industry for material handling and processing.
اقرأ أكثر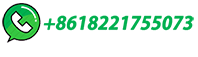
8 Tips for Crusher Safety | Stewart-Amos Equipment Company
Ending the operation of a crusher is an essential part of crusher safety. There are a few steps to follow when shutting down a crusher that every trained worker should follow: Shut down the apron feeder. Ensure equipment is free of material. Shut down the primary crusher. Shut down the secondary crusher. De-energize the …
اقرأ أكثر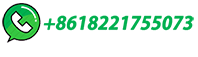