Ultra fine wet grinding in stirred ball mill: Part II. Slurry …
The aim of this review is to present main principles and some previous work with respect to the slurry rheology and stability in ultra fine wet grinding with stirred …
اقرأ أكثر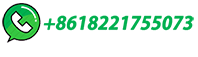
Ultra-fine grinding and mechanical activation of mine …
Slurry rheological properties, particle size distribution, specific surface area, crystallinity, and CO 2 sequestration reaction efficiency of the initial and mechanically activated mine waste rock and olivine were characterized. ... Ultra-fine grinding and mechanical activation of mine waste rock using a high-speed stirred mill for mineral ...
اقرأ أكثر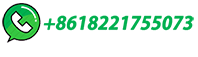
ISAMILL FINE GRINDING TECHNOLOGY AND ITS
Young et al, 2000). These are required for ultra-fine grinding to achieve liberation of fine-grained minerals, which improves separation of th e minerals in the flotation circuits. The process parameters and IsaMill designs have been continuously improved to increase the IsaMill grinding performance and the component life between maintenance ...
اقرأ أكثر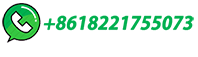
Parameter Effects on Wet Ultrafine Grinding of Limestone Through Slurry
Wet ultra-fine grinding of a limestone powder (< 100 μm) has been investigated in a stirred media mill with respect to the effect of slurry rheology.
اقرأ أكثر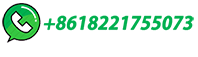
IsaMill Ultrafine Grinding for a Sulphide Leach Process
Ultrafine grinding provides an effective method of liberating physically locked gold, or for producing a feedstock that is amenable to oxidative processes. Motor Gearbox. …
اقرأ أكثر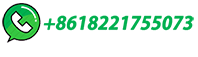
Fine Grinding of Ceramics with Attritors
A rising demand for high quality ultra-fine ceramic pow-ders makes fine grinding one of the most important operations in ceramic processing. Three types of mills are commonly used: ball, vibratory and attrition. This article addresses Attritors and their applications. The Attritor was conceived by Dr. Andrew Szegvari in the 1920s.
اقرأ أكثر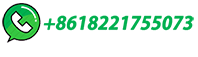
Sustainability of coal mines: Separation of clean coal from the fine …
Wet grinding experiments conclude that 30 min of grinding time, 350 rpm speed, water addition of 50% (w/w), and 2 mm grinding media results in achieving the fine-sized coal slurry with an average particle size of 45 μ and total undersize less than 75 μ. It was observed that direct centrifugal separation at 50% pulp density can result in ...
اقرأ أكثر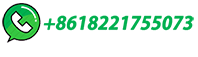
Some breakage characteristics of ultra-fine wet grinding …
DOI: 10.1016/J.MINPRO.2005.11.005 Corpus ID: 98519957; Some breakage characteristics of ultra-fine wet grinding with a centrifugal mill @article{Cho2006SomeBC, title={Some breakage characteristics of ultra-fine wet grinding with a centrifugal mill}, author={Heechan Cho and Hoon Lee and Yeongwoo Lee}, journal={International Journal …
اقرأ أكثر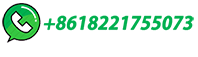
Ultrafine Grinding and the IsaMill™ Technology
Glencore Technology will provide the IsaMill™ as a packaged Grinding Plant, consisting of the mill, slurry feed and discharge systems, media handling system, all instrumentation and control and all structural steel …
اقرأ أكثر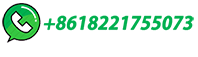
Energy Use of Fine Grinding in Mineral Processing
Fine grinding, to P80 sizes as low as 7 μm, is becoming increasingly important as mines treat ores with smaller liberation sizes. This grinding is typically done using stirred mills such as the Isamill or Stirred Media Detritor. While fine grinding consumes less energy than primary grinding, it can still account for a substantial part of …
اقرأ أكثر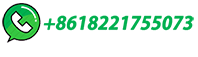
Parameter effects on wet ultrafine grinding of limestone through slurry
DOI: 10.1016/J.POWTEC.2005.08.026 Corpus ID: 96060794; Parameter effects on wet ultrafine grinding of limestone through slurry rheology in a stirred media mill @article{He2006ParameterEO, title={Parameter effects on wet ultrafine grinding of limestone through slurry rheology in a stirred media mill}, author={Mingzhao He and …
اقرأ أكثر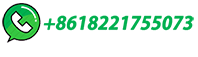
Outotec HIGmills; A Fine Grinding Technology
the mill which classifies the target size material off from the feed and defines the pulp density. The defined underflow is then mixed with water to optimal grinding density and pumped into the mill at base level. The slurry enters a grinding chamber containing grinding media (beads) and rotating discs which provide momentum to stir the charge
اقرأ أكثر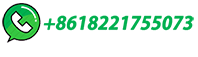
Operating experience of Mitsubishi ultra-fine mill for various slurry …
OSTI ID: 41616 Report Number(s): CONF-940320-; TRN: 95:002914-0061 Resource Relation: Conference: 19. international technical conference on coal utilization and fuel systems: the greening of coal, Clearwater, FL (United States), 21-24 Mar 1994; Other Information: PBD: [1994]; Related Information: Is Part Of Proceedings of the 19th …
اقرأ أكثر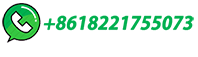
Ultra-fine grinding mechanism of inorganic powders in a stirred ball mill
It was confirmed that the grinding rate constant K, when using grinding aids improved by 1.95% and 25.6% for a 60 wt% and 70wt% slurry concentrate, respectively, when compared with the case of the ...
اقرأ أكثر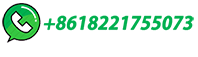
The influence of suspension properties on ultra-fine grinding …
The mills traditionally used for ultra-fine grinding are high-speed stirred ball mills. These mills are based on grinding using loose, moving grinding media which are moved by rotation of an axial stirring device. ... M. Gao, E. Forssberg, The influence of slurry rheology on ultra-fine grinding in a stirred ball mill, 18th Int. Miner. Process ...
اقرأ أكثر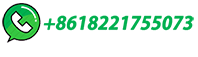
Investigation of some parameters affecting the Ultra-fine grinding …
Ultra-fine grinding involves a large number of parameters in its operation. In this paper, four important parameters of the Drais stirred ball mill, i.e., the bead density, slurry density, mill ...
اقرأ أكثر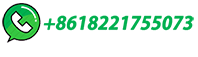
Parameters affecting wet ultra-fine grinding of talc ore
this time. The submicron ultra-fine grinding products of Egyptian talc could be used in different industrial filler applications such as paints, ceramic and paper coating. Index Terms— Ultra-Fine grinding, Stirred media mills, Attritor mill, Talc ore, Ultrafine talc properties, Ultrafine talc applications, and Functional fillers.
اقرأ أكثر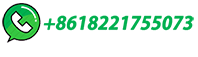
Effect of grinding parameters on the rheology of pyrite–heptane slurry
Most of the mills used in ultra-fine grinding are stirred media mills, rather than conventional tumbling ball mills. ... Also, the principles from tumbling ball mills concerning the role of slurry rheology on the grinding results are not completely applicable to the stirred media milling due to their different breakage mechanisms (Kwade, 1999 ...
اقرأ أكثر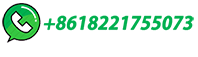
(PDF) Slurry flow in a tower mill | Paul Cleary
IsaMill TM is a high-speed stirred mill for a range of milling duties from ultra-fine to relatively coarse grinding in the mineral processing industry. This work investigated particle and slurry flow in a mill using a combined Discrete Element Method and Computational Fluid Dynamics (DEM-CFD) approach.
اقرأ أكثر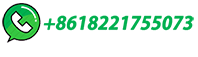
IsaMill Ultrafine Grinding for a Sulphide Leach Process
Ground slurry was discharged from the mill through a slurry discharge port and was collected in a sealed product tank. Samples of ground slurry were collected for the leaching tests, and each of the slurry samples was filtered and the filter cake stored frozen prior to the leach tests. The mill media was 0.8 – 1.2mm steel shot. The Vertically ...
اقرأ أكثر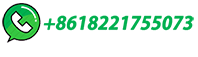
Parameter effects on wet ultrafine grinding of limestone through slurry
Wet ultra-fine grinding of a limestone powder (< 100 μm) has been investigated in a stirred media mill with respect to the effect of slurry rheology.The grinding results obtained by various parameters (i.e., molecular weight of a dispersant, solids concentration, additive dosage, addition method and beads load) are evaluated in …
اقرأ أكثر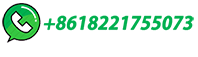
ISAMILL FINE GRINDING TECHNOLOGY AND ITS
The IsaMill is a horizontal stirred mill with sizes up to 3 m3 chamber net volume and 1120 kW installed motor. It was jointly invented by Mount Isa Mines of Australia and Netzsch …
اقرأ أكثر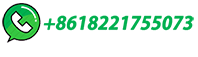
OUTOTEC HIGMILL – ENERGY-EFFICIENT HIGH …
of the grinding chamber, with rotating discs stirring the charge and grinding taking place between the beads by attrition. Depending on the application, there can be up to 30 discs or grinding stages. Feed slurry is pumped into the mill via a bottom connection, and as the flow transfers upwards it passes through each consecutive grinding stage.
اقرأ أكثر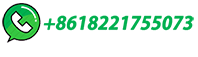
Grinding
In the case of ultra-fine grinding, along with the high energy consumption, the greatest problematic issue would be related to particle-particle interactions. ... The effect of slurry rheology on fine grinding in a laboratory ball mill. Int. J. Miner. Process. 69, 29–47 ... Bagga, P.: An analysis of fine dry grinding in ball mills. Powder ...
اقرأ أكثر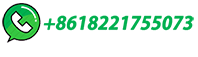
Fine grinding: How mill type affects particle shape characteristics …
The slurry density of the ball mill feed sample was low at 47%, and that of the IsaMill samples was 51%. A mass balance was not performed over the circuit, and these samples were only used for a preliminary assessment of particle shape within the circuit. ... as well as progeny from the laboratory stirred mill. Although fine and ultra-fine ...
اقرأ أكثر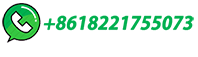
Parameter effects on wet ultrafine grinding of limestone …
Wet ultra-fine grinding of a limestone powder (< 100 μm) has been investigated in a stirred media mill with respect to the effect of slurry rheology.
اقرأ أكثر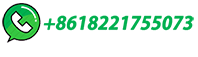
Slurry rheology in wet ultrafine grinding of industrial …
In the case of ultrafine grinding, various parameters (such as solid concentration, particle size and distribution, particle shape, temperature, rotation and …
اقرأ أكثر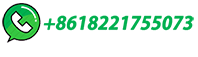
Effect of grinding parameters on the rheology of pyrite–heptane slurry
The influences of wet ultra-fine grinding parameters on the rheological behavior of pyrite–heptane slurry in a laboratory stirred media mill were investigated with solid concentration ...
اقرأ أكثر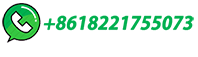
Energy-Efficient Advanced Ultrafine Grinding of Particles …
The present literature review explores the energy-efficient ultrafine grinding of particles using stirred mills. The review provides an overview of the different …
اقرأ أكثر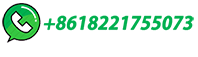