Grinding in Ball Mills: Modeling and Process Control
Keywords: Ball mills, grinding circuit, process control. I. Introduction Grinding in ball mills is an important technological process applied to reduce the size of particles which may have different nature and a wide diversity of physical, mechanical and chemical characteristics. Typical examples are the various ores, minerals, limestone, etc.
اقرأ أكثر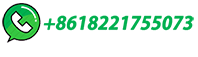
Ball Mill Success: A Step-by-Step Guide to Choosing the …
Unlock the secrets to ball mill efficiency with our comprehensive guide on choosing the right grinding media. Learn how material composition, size, shape, hardness, and cost impact your milling process and outcomes. ... pivotal for the efficacy of the ball milling process, come in various materials, each offering unique characteristics and ...
اقرأ أكثر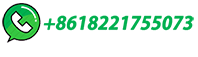
Wet ball milling of niobium by using ethanol, determination …
This study investigates the effect of using ethanol as the process control agent during the wet ball milling of niobium (Nb).
اقرأ أكثر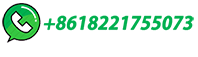
Ball Mill (Ball Mills Explained)
Crushed ore is fed to the ball mill through the inlet; a scoop (small screw conveyor) ensures the feed is constant. For both wet and dry ball mills, the ball mill is charged to approximately 33% with balls (range 30-45%). Pulp (crushed ore and water) fills another 15% of the drum's volume so that the total volume of the drum is 50% charged.
اقرأ أكثر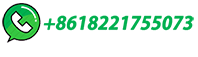
AMIT 135: Lesson 7 Ball Mills & Circuits – Mining Mill …
Mill Type Overview. Three types of mill design are common. The Overflow Discharge mill is best suited for fine grinding to 75 – 106 microns.; The Diaphram or Grate Discharge mill keeps coarse particles within the mill for additional grinding and typically used for grinds to 150 – 250 microns.; The Center-Periphery Discharge mill has feed reporting from both …
اقرأ أكثر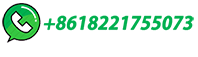
Ball Mill Loading
When charging a ball mill, ceramic lined mill, pebble mill, jar mill or laboratory jar use on a jar rolling mill it is important to have the correct amount of media and correct amount of product. Charging a Wet Mill – The general operation of a grinding mill is to have the product impacted between the balls as they tumble.
اقرأ أكثر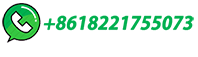
Modelling of the High-Energy Ball Milling Process
High-energy ball milling is a complicated process employed in solid reactions for obtaining nanostructured materials, in powder form, with an average particle size of less …
اقرأ أكثر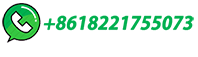
Influence of Post‐Synthesis Processing on the Structure, …
The tortuosity factor decreases with milling at 40 Hz and is the lowest after milling in the planetary ball mill where the sample milled for 10 and for 240 min exhibit …
اقرأ أكثر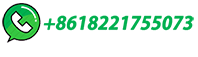
Ball milling: a green technology for the …
Abstract. Ball milling is a simple, fast, cost-effective green technology with enormous potential. One of the most interesting applications of this technology in the field of cellulose is the preparation and the chemical …
اقرأ أكثر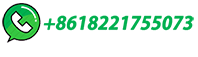
Ball Mill
The history and necessity of mechanical alloying. M. Sherif El-Eskandarany, in Mechanical Alloying (Second Edition), 2015. 2.5.1.5 Planetary ball mills. The Planetary ball mills are the most popular mills used in MM, MA, and MD scientific researches for synthesizing almost all of the materials presented in Figure 1.1. In this type of mill, the milling media …
اقرأ أكثر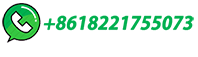
Wet Ball Milling Vs Dry Ball Milling
The power to drive a wet ball mill is said to be 30% lesser than that of a similar dry ball mill. Nature Of Materials ... In the production of ethanol, wet ball milling is the process used, because of its versatile process. It produces more products than dry ball milling, but in terms of efficiency, capital, and operating cost, most ethanol ...
اقرأ أكثر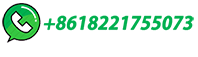
Effect of ball size and powder loading on the milling efficiency …
1. Introduction. Wet ball mill is one of the most predominantly used method for the purpose of mixing and grinding of raw materials in laboratories and industry [1], [2], [3].The ball mill process is very complicated process governed by many parameters, such as ball size, ball shape, ball filling, slurry loading (with respect to ball amount), powder …
اقرأ أكثر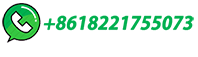
Ball Mill Loading (wet milling) : 네이버 블로그
Ball Mill Loading (wet milling) When charging a ball mill, ceramic lined mill, pebble mill, jar mill or laboratory jar use on a jar rolling mill it is important to have the correct amount of media and correct amount of product. Charging a Wet Mill – The general operation of a grinding mill is to have the product impacted between the balls as ...
اقرأ أكثر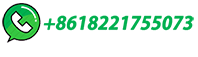
Ball Mills in the Mineral Processing Industry
The General Function of Ball Mills. A ball mill is a grinder used for grinding and blending materials for mineral dressing processes, paints, pyrotechnics, ceramics, and selective laser sintering. Appearance. Ball mills have various designs and functions, ranging from laboratory-scale versions to large industrial models.
اقرأ أكثر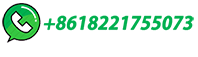
BALL CHARGING & GRINDING MEDIA HANDLING
y all process plants haing mills as part of their comminution process. The handling of heay steel alls can e a safety issue when drums of alls are hoisted and tipped often manually into chutes and mill inlets. Transmin has a range of systems available to safely store and feed balls from simple kibbles through to comple handling
اقرأ أكثر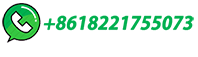
Ball Charging System — Material Handling Engineering, …
Knight Industrial Equipment, 3701 Airfield Drive West, Lakeland FL, 33811-1244, United States 863-646-2997 863-646-2997
اقرأ أكثر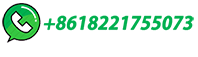
Dry Grinding Vs. Wet Ball Mill Grinding | Economy Ball Mill
Wet ball milling requires more energy than dry ball milling but also has higher throughput. Dry ball milling is more efficient for materials that don't require very fine particles or have a low tendency to group together.
اقرأ أكثر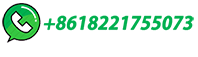
A Review of the Grinding Media in Ball Mills for Mineral …
The ball mill is a rotating cylindrical vessel with grinding media inside, which is responsible for breaking the ore particles. Grinding media play an important role in the comminution of mineral ores in these mills. This work reviews the application of balls in mineral processing as a function of the materials used to manufacture them and the …
اقرأ أكثر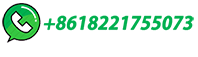
A Review of the Grinding Media in Ball Mills for Mineral …
Ball mill efficiency directly affects the cost of mineral processing. Grinding media play a vital role in enhancing the efficiency of a ball mill through their direct …
اقرأ أكثر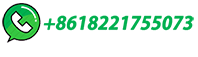
Exploring ball milling theory: A comprehensive guide
The milling process also promotes the mixing and blending of different materials, leading to the formation of new compounds or the modification of existing ones. Factors Influencing Ball Milling. 1. Grinding Media. The size, shape, and hardness of the grinding media significantly impact the ball milling process.
اقرأ أكثر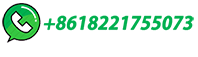
Energy-Mass-Size balance model for dynamic control of …
simulation of open circuit wet ball mills under MATLAB environment. It integrates the energy balance with the population balance model in a simple and clear representation of the physics and thermodynamics of the wet ball milling process. Easily measurable parameters such as mill temperature and product size distribution would
اقرأ أكثر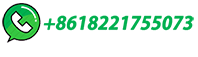
High-Energy Ball Milling
Nanotechnology-enhanced metals and alloys for orthopedic implants. Lei Yang, in Nanotechnology-Enhanced Orthopedic Materials, 2015. 2.1.2 High-energy ball milling. High-energy ball milling is a mechanical deformation process that is frequently used for producing nanocrystalline metals or alloys in powder form. This technique belongs to the …
اقرأ أكثر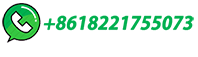
Wet Overflow Type Ball Mill and Applications
How Overflow Type Ball Mill Works. Material Feed: The raw material is fed into the mill at one end and travels through the mill by rotation. The feed enters the mill at a specific rate, ensuring a controlled grinding process.; Grinding Process: As the mill rotates, the grinding media crushes and grinds the material into a fine powder. The wet …
اقرأ أكثر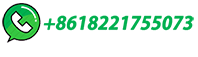
Ball Milling Method for Synthesis of Nanomaterials
It is a ball milling process where a powder mixture placed in the ball mill is subjected to high-energy collision from the balls. This process was developed by Benjamin and his coworkers at the International Nickel Company in the late of 1960. ... Hence, the planetary ball mill can be used for high-speed milling. Schematic view of motion of the ...
اقرأ أكثر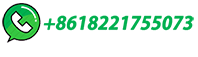
Ball Mill Loading
Ball Mill Loading (dry milling) When charging a ball mill, ceramic lined mill, pebble mill, jar mill or laboratory jar use on a jar rolling mill it is important to have the correct amount of media and correct amount of product. Charging a Dry Mill - The general operation of a grinding mill is to have the product impacted between the balls as ...
اقرأ أكثر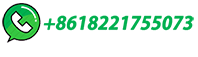
Ball Mill Application and Design
Ball mills scale up well and in fact improve in performed with increasing size. Ball mills are available in sizes from laboratory scale (also called milling jars) of 0.1 usg to large 5,000 gallon mills. Ball mills are available in various contact materials to accommodate contamination and wear requirements.
اقرأ أكثر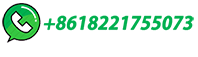
BALL MILLS Ball mill optimisation
co. optimising the process, the grinding tools will have a significant impact on lower production costs as well as maintenance costs. Ball mills and grinding tools. ler media …
اقرأ أكثر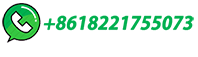
Effect of ball size and powder loading on the milling …
The ball mill process is very complicated process governed by many parameters, such as ball size, ball shape, ball filling, slurry loading (with respect to ball amount), powder loading with respect to the amount of total slurry (slurry viscosity), and rotation speed. ... Multiphase materials based on the Fe 73.9 Si 15.5 Cu 1 Nb 3 B 6.6 …
اقرأ أكثر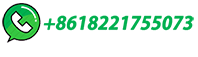
What Is a Ball Mill and How Does It Work?
The agitation process in vibratory mills involves the charge of powder and milling tools being agitated in three perpendicular directions at extremely high speeds, up to 1200 rpm. ... The grinding process in a ball mill evenly distributes and blends the ingredients, ensuring a consistent final product. ... They serve both dry and wet milling ...
اقرأ أكثر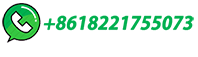
How To Optimize Wet Grinding Ball Mill Performance
Wet Ball Milling Process. Wet ball milling is a versatile method employed in mineral processing, ceramics, and various industrial applications to grind and blend materials effectively. The process unfolds within a rotating cylindrical drum filled with grinding media, such as steel balls or ceramic beads, and a liquid medium, typically water.
اقرأ أكثر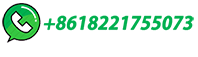