Modular Grinding Plant | AGICO Cement Machinery
Modular Mobile Cement Grinding Solution. ... Clinker and other additives for grinding are fed by fork-lift truck to respective feeding bins. The feeding bins are installed in standardized containers. ... All other equipment in the grinding station serves the purpose of grinding. The performance of the mill will directly determine the output and ...
اقرأ أكثر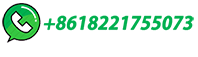
Efficient grinding unit selection impacts profitability
Technology has advanced over the period and the grinding process can help in augmenting some properties of cement. Tell us about the equipment used for grinding raw material and clinker. The main equipment used for grinding raw materials and clinker are categorised based on their size reduction concept and mechanism as, …
اقرأ أكثر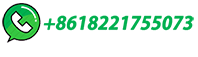
Cement Euipment Overview | Cement Making Machines
Finished cement: add some gypsum, admixture or additive into cement clinker, and using cement mill grinding cement clinker into finished cement. The finished cement can be stored in the cement silo or packed into bags. ... Cement kiln is used to make cement clinker, and it is the core equipment of cement production line; usually, …
اقرأ أكثر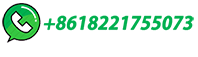
Overview of cement grinding: fundamentals, additives, technologies
Grinding is an essential operation in cement production given that it permits to obtain fine powder which reacts quickly with water, sets in few hours and hardens over a period of weeks. i ...
اقرأ أكثر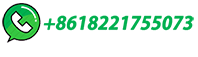
Cement Grinding Plant / Grinding Unit
We master the construction and design schemes of various cement grinding plant systems such as vertical mill system, combined system, and ball mill system. No matter what …
اقرأ أكثر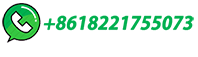
Clinkerization
The process of clinkerization signifies conversion of raw meal into clinker minerals mainly consisting of C4AF (Aluminoferite), C3A (Aluminite), C2S (Belite) and C3S (Alite) phases along with small percentage of free lime …
اقرأ أكثر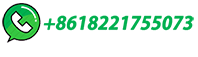
What is Cement Clinker? Composition, Types & Uses
Clinker is a nodular material produced in the kilning stage during the production of cement and is used as the binder in many cement products. The lumps or nodules of clinker are usually of diameter 3-25 mm and dark grey in color. It is produced by heating limestone and clay to the point of liquefaction at about 1400°C-1500°C in the rotary kiln. ...
اقرأ أكثر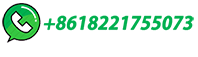
Clinker cooling
The thermal efficiency of rotary kiln clinker coolers of all types of design is within the range of 40 to more than 80%. b)Another criterion for judging the cooler efficiency is the temperature difference between the hot clinker entering the cooler and the hot secondary air leaving the Furthermore, the best cooler is the particular cooler which, because of its …
اقرأ أكثر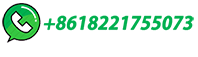
Quality & Composition of cement clinker
Quality & Composition of cement clinker ... The higher strength performance of mineralised cements provides the opportunity to reduce the fineness of grinding of cement at the finish milling stage and thereby save electrical energy consumption, and also boost the capacity of the finish milling equipment if this is a constraint on factory output.
اقرأ أكثر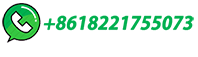
Roller Press
Simply put, the roller press is the most energy-efficient grinding machine on the market. Since its commercial introduction into the cement industry by KHD in the 1980s, hundreds of them have been installed in the cement and minerals industries, in both finish and semi-finish applications. And with the lowest specific energy consumption among comparable …
اقرأ أكثر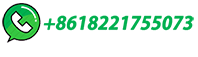
The Cement Plant Operations Handbook
6. Cement milling Finish milling is the grinding together of clinker with some 3-5 per cent gypsum, natural or synthetic, for set control, and quite often other components: …
اقرأ أكثر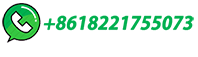
Cement Plant Machinery Manufacturers, Ball Mill …
At Supertech, our vision is to integrate our solutions according to our Customers' needs. And keeping this in mind, we manufacture and supply a varied range of Cement Plant Machinery for our Clients and have become a complete solution provider. Supertech has successfully emerged as a single stop for all kind of Cement plant machinery that are …
اقرأ أكثر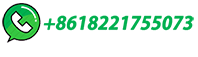
Eqiom orders equipment from Fives FCB to upgrade Héming cement grinding …
Eqiom has awarded Fives FCB a contract to upgrade its cement grinding plant at Héming. The project involves integrating an FCB TSV 4000 TSF Classifier and an FCB TGT Filter with the existing milling circuit at the unit operating by the subsidiary of Ireland-based CRH. ... The upgrade is intended to reduce the plant's clinker factor, …
اقرأ أكثر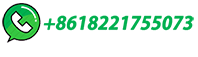
Clinker Grinding Plant
Clinker Grinding units are now a days very popular when it comes to catering the marketing needs of a particular area. A full-fledged Cement plant cannot be installed at just about any location as it requires a large initial capital investment & local limestone availability for manufacturing of cement.
اقرأ أكثر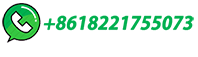
An Introduction to Clinker Grinding and Cement Storage
would be a length of 13.5 m and a diameter of 2.5 m, with a speed of approximately 20 revolutions per minute. Such a mill would normally have a load of approximately 90 tons of grinding media, graduated from 90 mm to 60 mm in the first chamber, 50 mm to 15 mm in the second chamber and 15 mm down in the final chamber.
اقرأ أكثر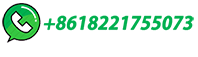
Finish grinding
Grinding with propylene glycol generates approxi mately 800 cm2/gram cement more surface than grinding without an aid, given the same energy con sumption. The cost of these grinding aids is about 0.25- 0.40 U.S. Dollars/kg. The grinding aid is added to the cement in an amount of approximately 1 kg/t.
اقرأ أكثر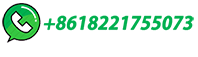
Key factors in setting up a cement plant
The cement manufacturing process starts with mining of limestone followed by grinding it with other raw materials like clay, shale, bauxite, iron ore, etc. to prepare a raw meal, which is heated at a sintering temperature of 1,400 to 1,500 degree Celsius in a kiln to manufacture clinker.
اقرأ أكثر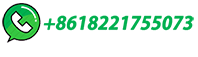
Cement Plant Equipment
Frigate Teknologies Pvt. Ltd. is a leading manufacturer and supplier of Cement Plant Equipment in India. A-1550, 2nd Floor, Green Field, Faridabad +91 987 188 8647 ... manufacture, supply & installation of a wide range of cement plant equipment. List includes the following equipment: Clinker Grinding Plants; Ball Mills; Mill Heads; Mill ...
اقرأ أكثر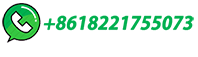
Energy-Efficient Technologies in Cement Grinding
1. Introduction. Cement is an energy-intensive industry in which the grinding circuits use more than 60 % of the total electrical energy consumed and account for most of the manufacturing cost [].The requirements for the cement industry in the future are to reduce the use of energy in grinding and the emission of CO 2 from the kilns. In …
اقرأ أكثر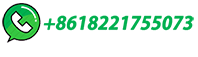
Cement Clinker Grinding Plant
The cement clinker grinding plant or cement grinding station acts as an individual production line in the last period of the cement production process. +86 +86-371-55902868 ; zkeqpt@zkcorp; Home ... Main Equipment: Cement Ball Mill / Cement Vertical Mill, Bag Filter .
اقرأ أكثر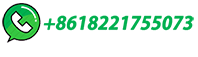
10 secrets of clinker
Previous Post Next Post Contents1 10 secrets of clinker1.1 First Rule1.2 Second rule1.3 Third rule1.4 Fourth rule1.5 Fifth rule1.6 Sixth Rule1.7 Seventh rule1.8 Eighth rule1.9 Ninth rule1.10 Tenth rule 10 secrets of clinker First Rule Reducing raw mix rejects lowers burning temperature and grinding energy. This is particularly the case with siliceous rejects. …
اقرأ أكثر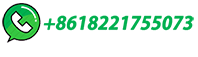
Modular & Mobile Cement Grinding Plant For …
Based on customer needs and years of experience in cement equipment manufacturing, AGICO Cement develops a low-cost and highly efficient EPC solution for cement grinding unit – modular & mobile (MMG) …
اقرأ أكثر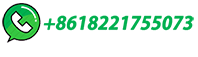
OPTIMIZATION OF CEMENT GRINDING OPERATION IN …
Condition in one of the grinding chambers of the mill . Results of Optimization . The graphical analysis presented in Figure 2 represents progress of grinding along the length of the mill after optimizing the grinding process. rogress of grinding is clearly visible in Desired p the graphs. Figure -2: Analysis of longitudinal samples.
اقرأ أكثر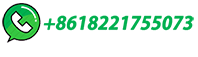
SEPARATE OR INTERGRINDING?
Separate grinding vs intergrinding. Looking specifically at the pros and cons of separate grinding compared to intergrinding, which is the focus of this article, a detailed test …
اقرأ أكثر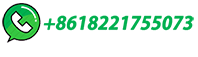
2.4x11m cement ball mill | cement tube mill | cement grinder …
The 2.4x11m Cement Grinder Mill is a specialized equipment designed for grinding clinker in cement production plants. Engineered for efficiency and high performance, this mill plays a crucial role ...
اقرأ أكثر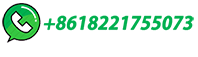
Clinker grinding technology in cement manufacturing
Clinker grinding technology is the most energy-intensive process in cement manufacturing. Traditionally, it was treated as "low on technology" and "high on energy" as grinding circuits use more than 60 per cent of total energy consumed and account for most of the manufacturing cost. Since the increasing energy cost started burning the benefits …
اقرأ أكثر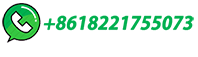
Improvements in New & Existing Cement …
o Cement manufacture consumes typically 3,100 – 3,400 MJ of fuel/t clinker & 90 -130 kWh / t cement in a modern plant, & more for older or less efficient plants; o Generally 2/3 of the electricity consumed is used …
اقرأ أكثر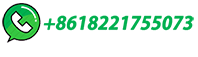
Cement Grinding
Exact proportioning is dependent upon their chemical properties before and after calcining to cement clinker. For good kiln practice the grind required is 88-92% – 200 mesh for standard cement, …
اقرأ أكثر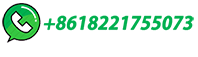
Cement Grinding Plant | Expert Cement Grinding
The main task of the cement grinding plant is to grind the cement clinker into particles with a certain fineness to make it into finished product cement. ... Cement Grinding Equipment. The core equipment in a grinding plant is the cement mill. According to different grinding systems, the often-used cement mills include ball mill, roller press ...
اقرأ أكثر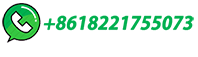
Grinding in closed circuit
The tendency to agglomeration causes difficulties when grinding cement clinker in open circuit to higher specific surfaces than 3000-3500 Blaine [143a]. For fine grinding in open circuit, the F. L. Co, developed a grinding system consisting of two tube mills.
اقرأ أكثر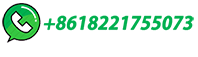