Crankshaft: Parts, Function, Types, Diagram & More [PDF]
#1 Crank Pin. The crankpin is a mechanical part of an engine. It allows the connecting rod to be attached to the crankshaft very firmly. ... In this, all the components are shrink-fitted after the fabrication process. This type of crankshaft is used in old engines. It consists of a separate crank web, crankpin, and main journals. This crankpin ...
اقرأ أكثر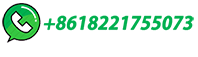
Complete Machining of Crankshafts in Small Series
A 60% saving can be achieved in the process chain thanks to complete machining, and this figure is even 80–90% for the set-up time. Cranx–The Crankshaft Profiler. Machining crankshafts is a demanding process that not only requires perfect tools but also relevant software to be successful.
اقرأ أكثر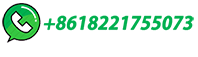
CRANKSHAFTS
Heavy Duty crankshafts of 12 & 16 Cylinder Engines length 2.5 mtr are fully machined and ready to use. From Raw forgings to turning, heat treatment, grinding, finishing, washing and packing. The facility deploys high end & specialized CNCs & SPMs. GFM make CNC Milling SPM for Crankshaft Pin Milling. EMA make Semi Automation CNC Induction …
اقرأ أكثر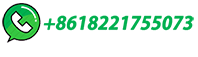
Typical crankshaft parts machining process …
To design a keyway milling fixture for milling a 12 × 40 mm keyway in Process 210, it is necessary to limit the workpiece to 6 degrees of freedom. When milling the keyway, the long journal of the …
اقرأ أكثر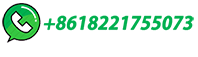
Model of Milling the Root and Connecting Rod Necks of …
Milling of the crankshaft 1 is carried out by a cutter 2, which in the middle of the root neck 3 cuts into the entire depth of cut t (Fig. 1) and moves along the axis O CrZ Cr coordinate system of the part with the supply s z. Cutting of a mill in the middle of a Fig. 1. Crankshaft milling scheme with crossed tool axes and parts. 162 V ...
اقرأ أكثر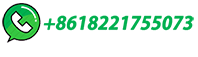
Heat Treatment: Enhancing Material Properties Through …
2. Process annealing: Process annealing is performed on cold-worked materials to restore their ductility. The material is heated to a temperature below its critical range and then cooled slowly. 3. Stress relief annealing: Stress relief annealing is carried out to minimize residual stresses in a material.
اقرأ أكثر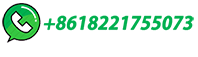
Crankshaft for Engines » Cutting Tools
Excellent solutions are available to ensure that you meet the increasing requirements and targets relating to crankshaft quality. For external milling of the pin and main bearings of the crankshaft, for example, we offer the Walter external milling cutter with Tiger·tec ® Gold indexable inserts, which is available with an outer diameter of up ...
اقرأ أكثر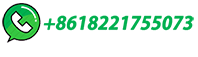
Crankshaft solutions
Internal milling M641 (tangential mounted inserts) and M642 (radial mounted inserts) crankshaft disc milling concepts. This is a stable system with good process security, which provides an unrivalled cost efficiency. The different tools range from lightweight up to large tools for ship diesel crankshafts. Concept description
اقرأ أكثر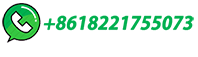
Analysis and Optimization of Milling Process for Crankshaft Pin …
Download Citation | On Sep 9, 2019, Hui-ling LI and others published Analysis and Optimization of Milling Process for Crankshaft Pin Based on Energy Consumption | Find, read and cite all the ...
اقرأ أكثر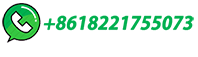
Evaluation of Crankshaft Manufacturing Methods
process makes it much easier to locate the counterweights and journals webs exactly where the designer wants them to be. This process required tooling like Lathe machine, Shaper, Precision Drills, Milling machine. Chart -4: Machining process for manufacturing crankshaft 1.2 Performance comparison of competing manufacturing techniques
اقرأ أكثر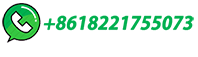
Grinding performance in crankshaft pin journal path …
in crankshaft pin journal path-controlled grinding of 40Cr using vitrified bonded cubic boron nitride (CBN) abrasive. ... theturning,milling,andturningandbroachingprocess,asthe final finishing before polishing. The traditional way to grind ... programmable wheelheads process the main and pin journal simultaneously. During the path-controlled ...
اقرأ أكثر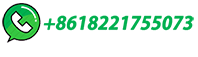
Mathematical modelling of the crankshaft pin grinding process
Novel mathematical models to predict crankshaft pin grinding forces, out-of-roundness and thermal damage were developed as part of this thesis. The models were validated at a local automotive manufacturer's plant. The outcomes of this research have resulted in reduced scrap and warranty costs, improved manufacturing process quality and reduced lead …
اقرأ أكثر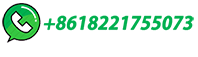
NILES-SIMMONS CM-Series Crankshaft/Camshaft Milling …
The NILES-SIMMONS CM-Series Crankshaft/Camshaft Milling Centers perform rough and finish milling of the main and pin bearing journals on automotive truck and …
اقرأ أكثر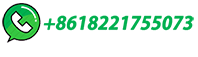
Crankshaft crank pin transition round corner milling …
A technology of excessive rounded corners and crankshafts, applied in metal processing equipment, milling machine equipment, details of milling machine equipment, etc., can solve the problems of tool overhang, severe tool vibration, limitations, etc., to improve product quality and production efficiency, easy to operate, wide range of effects
اقرأ أكثر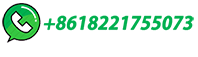
What Is Crankshaft Machining? | Crankshaft Machining
The traditional crankshaft machining process involved turning a crankshaft and bearing journal machining and final grinding. Specifically, each crankpin was turned on a large, …
اقرأ أكثر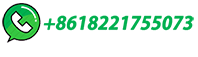
Crankshaft
As one of the most challenging engine components, a crankshaft involves multiple production processes using complex custom tooling.
اقرأ أكثر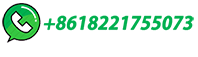
CNC crankshaft milling machine HELLER RFK 20-2-800
CNC crankshaft milling machine HELLER RFK 20-2-800 was built in 2001 by the German company Gebr. Heller Maschinenfabrik . The machine is designed for rough and finish milling of main bearings and/or lift bearings, including crankshaft sidewalls. The milling machine works in five axes with the feeds of 625 mm (W axis), 180 mm (U axis), …
اقرأ أكثر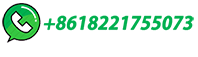
CN104339010A
The present invention discloses a crankshaft crank pin transition round corner milling processing equipment and a method, wherein the crankshaft crank pin transition round corner is R27*R10 mm, and is a smooth transition round corner formed by combining two arcs. The processing equipment comprises two milling cutter portions, wherein three …
اقرأ أكثر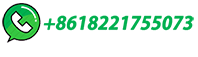
In-Place Crankshaft Machining and Grinding
Goltens has a great deal of experience repairing bent and twisted crankshafts In-Situ as well as the expert application of our in-situ crankshaft annealing process to remove hardness and salvage …
اقرأ أكثر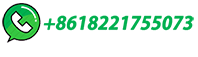
Machining Camshafts and Crankshafts
Overview. Crankshaft. Camshaft. Innovative Tooling Solutions. Machining cam profiles with profiling slot milling cutters, machining bearings and key widths as well …
اقرأ أكثر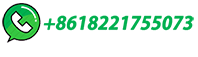
Crankshaft Machining and Polishing
If a main- or connecting rod bearing fails, then the crank pin or journal surface may get damaged and may show one or several of the following: Bearing material sticking to the crankshaft surface; Overheating, made evident by black/blue discoloration and, as a consequence, local hard sports; Dents and scoring on the pin or in the fillet; Heat ...
اقرأ أكثر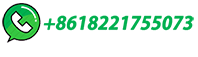
Crank shaft machining
Crankshaft machining The right milling tool for every processing step. ... Continuous process optimisation regarding cycle times, quantities and workpiece tolerances; ... Tool repair; Service and application engineers worldwide; Training events; Milling of pin bearings and main bearings of crankshafts Turn-milling tools for large crankshafts ...
اقرأ أكثر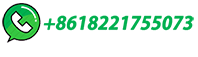
crankshaft pin milling process
Crankshaft Manufacturing Process. Manufacturing Process for crankshaft's: For Custom Billet Crankshaft Orders Click the order link below. Order. 1. The 1st process is to shape the Crankshaft on the lathe. This process shaves the journals leaving a margin of finishing. 2. The next process is to mill the pin. This process shaves the weight part ...
اقرأ أكثر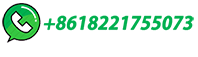
Crankshaft Fillet Rolling
The deep rolling process leaves a new compressive residual stress in the undercut area strengthening this area. The process involves applying a specific load to a rotating crankshaft utilizing small "work rolls" that have the desired shape and size of the finished undercut. This machining operation is not a metal removal process.
اقرأ أكثر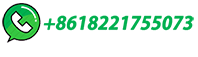
Complete Machining of Crankshafts in Small Series
A single machine carries out milling, boring, turning, deep hole drilling and measuring – from the blank to the nearly finished product. In addition to significantly …
اقرأ أكثر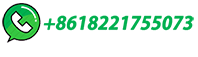
Design and optimization of multi-stage manufacturing process …
Crankshafts are among the most important parts in internal combustion engines, of which stirling engine is a useful example. Manufacturing process of a crankshaft, is considered as a three-step forging process using preform, due to the complexity in geometry. The most challenging step of the multistage forging process is …
اقرأ أكثر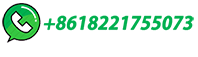
Typical crankshaft parts machining process …
The crankshaft is one of the most important parts of a diesel engine, and its processing and manufacturing quality directly affects the normal work and life of a diesel engine. The crankshaft mainly consists …
اقرأ أكثر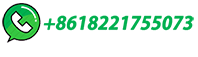
Model of Milling the Root and Connecting Rod Necks of the Crankshaft …
In, the process of milling the connecting rod necks of the crankshaft based on the machine's power consumption has been optimized. In, a series of experiments were performed to investigate the machinability in crankshaft pin journal path-controlled grinding of 40Cr using vitrified bonded cubic boron nitride (CBN) abrasive. …
اقرأ أكثر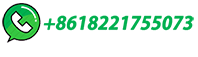
Crankshaft/camshaft production systems
steady rest travels on the guideway below the milling slides and is positioned between the two milling units on twin-spindle machines; machining using one or two milling units is possible; machining of …
اقرأ أكثر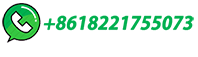