Surface roughness prediction in ball screw whirlwind milling
Whirlwind milling is a kind of intermittent cutting, which is carried out by multiple tools on the whirling ring. As shown in Fig. 1, the low-speed rotary motion of the workpiece, the high-speed rotary motion of the whirling ring, the axial feed motion of the whirling ring and the radial translation motion of the tool constitute the whirlwind milling …
اقرأ أكثر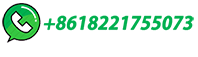
Exploring Ball Mill Diagram: A Comprehensive Guide
A ball mill consists of three main components: the shell, the grinding media (balls or pebbles), and the engine. The shell is constructed as a metal tube that is …
اقرأ أكثر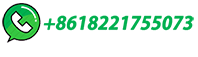
Ball Milling
Ball milling is a grinding method that grinds nanotubes into extremely fine powders. During the ball milling process, the collision between the tiny rigid balls in a concealed …
اقرأ أكثر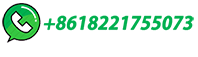
New approach to ball mill modelling as a piston flow process
This paper presents a new population balance model (PBM) of ball mills that understands the ball mill process as a hybrid of a perfectly mixed mill and piston flow mill. Usually, PBM for grinding is related to a perfectly mixed mill. In this case, the piston flow was introduced for a more realistic process.
اقرأ أكثر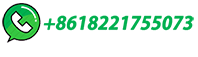
Crushing Plant Flowsheet & Design-Layout
To reduce run-of-mine to mill feed requires reduction in a series of stages. The physical size and power requirements of a crusher capable of reducing hard rock vary depending on the application. Extended experience in most crushing plants show that a minus 19MM (¾") rod mill feed can be and is being produced in three stages of crushing.
اقرأ أكثر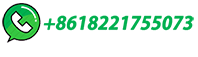
AMIT 135: Lesson 7 Ball Mills & Circuits – Mining Mill …
The process is continuously repeated as the particles move by mass and volume action through the mill. Dry and wet grinding common. Ball mill photographed by Ron Frisard and shared on Flickr, CC ... the feed trunnion is smaller than the discharge trunnion to ensure a good flow and no backflow to the feed. Diagram of ball mill and interior cut ...
اقرأ أكثر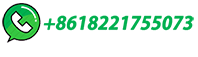
Exploring ball milling theory: A comprehensive guide
Ball milling is a fundamental and widely utilized technique in material processing. Understanding the principles behind ball milling theory is crucial for achieving optimal …
اقرأ أكثر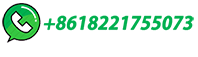
Everything You Need to Know About Wet Media Milling, …
Toll processors have a range of wet and dry milling methods at their disposal to achieve incredibly fine gauge powders.. Wet grinding — also called wet media milling — is often the preferred process for particle size reduction to a very fine scale, down to the micrometer and even nanometer range.. Fine milling, micronization, and nanonization can be …
اقرأ أكثر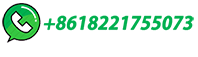
Process Training Ball Mill
Process Training Ball Mill. ... Therefore, bigger balls are moving opposite the material flow in the direction of the intermediate diaphragm or mill inlet (if only one compartment). Smaller ball have a smaller impact force and stay at their location or even being pushed towards the discharge of the ball mil.
اقرأ أكثر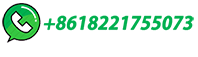
Schematic diagram of a ball mill. | Download Scientific …
Back in 1995, Liversidge and Cundy reported that ball milling could be used for preparing nanoparticulate formula- tion of a poorly water soluble drug, danazol, which showed enhanced ...
اقرأ أكثر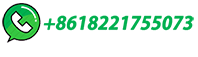
Ball Mill (Ball Mills Explained)
If a ball mill uses little or no water during grinding, it is a 'dry' mill. If a ball mill uses water during grinding, it is a 'wet' mill. A typical ball mill will have a drum length that is 1 or 1.5 times the drum diameter. Ball mills with a drum length to diameter ratio greater than 1.5 are referred to as tube mills.
اقرأ أكثر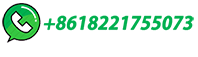
AMIT 135: Lesson 7 Ball Mills & Circuits – Mining …
Explain the role of ball mill in mineral industry and why it is extensively used. Describe different types of ball mill design. Describe the components of ball mill. Explain their understanding of ball mill operation. Explain the …
اقرأ أكثر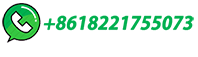
Exploring ball milling theory: A comprehensive guide
The milling process also promotes the mixing and blending of different materials, leading to the formation of new compounds or the modification of existing ones. Factors Influencing Ball Milling. 1. Grinding Media. The size, shape, and hardness of the grinding media significantly impact the ball milling process.
اقرأ أكثر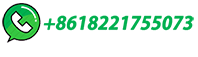
Producing Metal Powder from Machining Chips Using Ball Milling Process
The study results showed that the ball milling process was effective in breaking down the e-waste swarf and liberating valuable metals, such as silver, copper, and gold. The authors also found that the ball milling process is environmentally friendly compared to traditional methods, as it reduces the use of chemicals and produces less …
اقرأ أكثر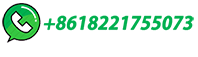
BALL MILLS Ball mill optimisation
co. optimising the process, the grinding tools will have a significant impact on lower production costs as well as maintenance costs. Ball mills and grinding tools. ler media …
اقرأ أكثر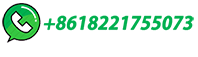
Effect of the ball milling process on surface hydration …
The grinding process performed by mechanical techniques, such as ball mill, vibration mill, and jet mill generally implies crushing raw materials to achieve a fine-dispersed state, and a possible mixing with the additives and temporary binder to homogenize powder mixtures in a dry mode or mixing with the solvents such as water, …
اقرأ أكثر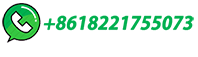
Mechanical Milling: A Superior Nanotechnological Tool for Fabrication
As with any other process, ball milling has a number of drawbacks that limit the potential to deliver a high-quality end product. Among the parameters that influence the milling process (Section 2.3.3), milling temperature is regarded as one of the most critical variables to control. When high energy ball mills are used, the temperature of the ...
اقرأ أكثر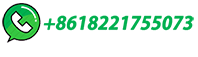
Investigation of chip formation in high speed end milling
Nakayama [2] explained the essential meaning of the direction of side curling and chip tool flow angle on the chip form and made clear the proceeding of a helical chip. ... In the chip formation process of ball-nose end milling, there also exists a "segmenting" phenomenon under certain cutting conditions. The reason is found to be self ...
اقرأ أكثر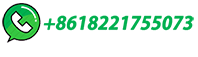
CNC Milling
The milling process usually comprises of a few different operations but this depends on the shape of the final product and the state of the raw piece. Often, milling is necessary for giving a precise finish and adding a few features like slots or threaded holes. But it is also suitable for creating a finished part from a block of material.
اقرأ أكثر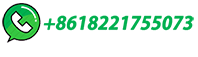
What Is a Ball Mill and How Does It Work?
Ball mills grind materials into an extremely fine form. The ball mill contains a hollow cylindrical shell that rotates about its axis. Steel or rubber balls of various sizes partially fill this shell to grind the material inside. How long does it take to mill? Ball milling usually takes 3-4 hours. It can take longer with conventional machines ...
اقرأ أكثر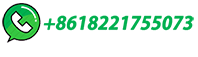
Ball Grinding Process
Ball grinding process is a grinding method of crushing ore with ball-shaped grinding medium in the grinding mill. In the ball grinding process, because the steel ball has 360° free rotation, it is suitable for falling motion and throwing motion. When the rotating speed of the cylinder is low, the medium rises to a certain height along the ...
اقرأ أكثر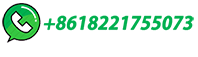
Ball milling: a green technology for the …
The use of ball milling to obtain cellulose nanocrystals was also explored by the group of Yu, who extracted CNCs from ball-milled wood via a multi-step process. 40 Douglas-Fir wood chips were firstly hammer-milled to …
اقرأ أكثر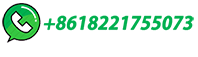
Ball mill for cement grinding
An inefficient ball mill is a major expense and could even cost you product quality. The best ball mills enable you to achieve the desired fineness quickly and efficiently, with minimum energy expenditure and low maintenance. ... Process data management and insights. ... In addition, the large through-flow areas enable the mill to operate with ...
اقرأ أكثر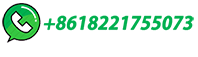
Exploring Ball Mill Diagram: A Comprehensive Guide
Explore the anatomy of a ball mill with a detailed ball mill diagram. Learn more on our blog for valuable insights into this essential industrial equipment. ... hoppers, and grates, are the most important component to have a consistent and controlled flow of the material through the mill. ... the milling process can produce particles in the ...
اقرأ أكثر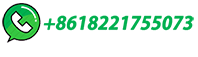
The Cement Plant Operations Handbook
6. Cement milling process summary data – 8. Typical equipment downtime 110 1. Storage of clinker and other components – 2. Cement milling – 3. Separators (classifiers) – 4. Ball mill circuit control – 5. Cement storage – 6. Cement dispatch – 7. Distribution – 8. Quality assurance and customer service 7. Quality control 134 1 ...
اقرأ أكثر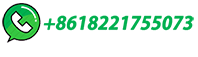
Gold CIL & CIP Gold Leaching Process Explained …
Cyanide is a lixiviant, or reagent that is used to leach, often in tanks, gold from a solid matrix and form a gold cyanide complex. The gold cyanide complex is then extracted from the pulp or slurry by adsorption …
اقرأ أكثر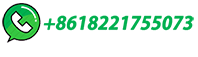
Exploring the Impact of Machining Forces on Ball End Milling …
The material's flow yield stress is denoted by the symbol σ, where B signifies the pre-exponential factor, and A represents the yield stress.T and T m represent the cutting temperature and material's melting point, respectively. C denotes strain rate factor in relation to the ambient temperature, where n and m serve as exponents for the …
اقرأ أكثر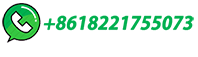
Functional Performance of Ball Milling Circuits – A Plant …
Functional performance analysis provides the tools and insights needed to measure, understand and improve the two key process eficiencies in ball milling circuits: …
اقرأ أكثر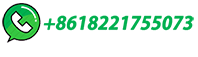
Mixing methods for solid state electrodes: Techniques, …
In wet ball-milling, all the variables that influence the process must be understood to achieve the transfer of high-energy inputs from the milling media to the material under study. In this way, the targeted particle size, the production of defects or structural changes and the generation of new surfaces in the material can be achieved …
اقرأ أكثر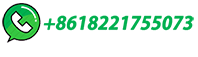
Impact of fat content during grinding on particle size …
Consumer acceptance depends on taste and mouth feeling. Processing can generate varying particle size distributions (PSD), which again influence flow parameters. Chocolate can be produced by roller refining and conching or alternatively by ball milling. Fat content during milling is an important parameter of both processes. The aim of this …
اقرأ أكثر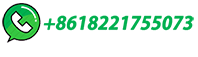