What is the Principle of Wet Ball Mill?
The wet ball mill is composed of a cylinder and a supporting device, which is used to hold the cylinder in place. The cylinder is filled with the grinding medium (usually water or …
اقرأ أكثر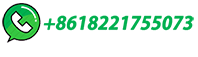
Effect of chemical additives on the dynamics of grinding media in wet
Recent papers on the role of grinding aids in wet ball mills indicate that certain polymeric aids favorably act by altering pulp rheology, leading to improved production rates at high pulp densities. Analysis of recent data indicates that there can be an improvement in terms of the production of fine particles per unit time, but on the other ...
اقرأ أكثر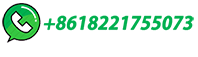
Wet Ball Milling Method and Technology
Wet grinding, a subset of the wet milling process, involves the reduction of particles in a liquid medium. Unlike dry grinding, where contact with air can lead to undesirable …
اقرأ أكثر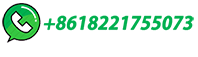
Ball Mill; Principle, Working, and Construction » Pharmaguddu
Produced strong vibration and sound and less in case of rubber ball usage. Can not reduce soft, tacky, and fibers materials; Wear occurs inside the cylinders hence chances of possible contamination are high; Less capacity, do not handle the large quantity. Ball Mill Price. Ball Mill Price in India ranges from 53,000 to 1.20 Lac depends on the size.
اقرأ أكثر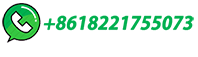
Ball milling: a green technology for the …
The use of ball milling as a defibrillation method after a series of pre-treatments of raw materials was also described by the group of Elkoun, who reported the extraction of CNFs and CNCs from carrot pulp by ball …
اقرأ أكثر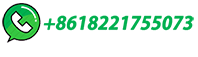
Overview of milling techniques for improving the solubility …
In wet milling, the addition of surfactants (e.g. sodium lauryl sulfate and polysorbate 80) and polymers (e.g. hydroxypropylmethyl cellulose, hydroxypropyl …
اقرأ أكثر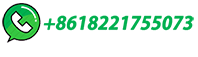
Wet Ball Mill for Metal Ores and Non-ferrous …
Capacity: 0.65-615t/h. Motor power: 18.5-4500kW. Applications: It can deal with metal and non-metal ores, including gold, silver, copper, phosphate, iron, etc. The ore that needs to be separated and the material that will …
اقرأ أكثر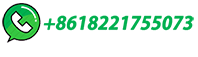
Overview of milling techniques for improving the solubility …
Milling is a unit operation where mechanical energy is applied to physically break down coarse particles to finer ones and hence, is regarded as a "top–down" approach in the production of fine particles ... In wet milling, the addition of surfactants (e.g. sodium lauryl sulfate and polysorbate 80) and polymers (e.g. hydroxypropylmethyl ...
اقرأ أكثر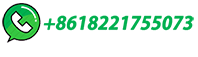
AMIT 135: Lesson 7 Ball Mills & Circuits – Mining Mill …
Explain the role of ball mill in mineral industry and why it is extensively used. Describe different types of ball mill design. Describe the components of ball mill. Explain their …
اقرأ أكثر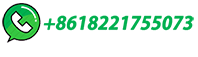
Intelligent optimal control system for ball mill grinding …
J Control Theory Appl 2013 11 (3) 454–462 DOI 10.1007/s11768-013-1210-3 Intelligent optimal control system for ball mill grinding process Dayong ZHAO 1†, Tianyou CHAI,2 1.State Key Laboratory of Synthetical Automation for Process Industries, Northeastern University, Shenyang Liaoning 110819, China;
اقرأ أكثر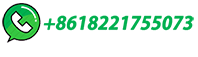
Ball Mill
The characteristic tumbling motion of these mills has given them the name 'tumbling mills', which include the ball mill, tube mill and rod mill. Ball mills are horizontal rotating cylindrical or conical steel chambers, approximately one third to half full of steel, alloy steel or iron balls, like that shown in Fig. 4.10 A–C, or flint stones.
اقرأ أكثر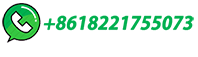
Wet Ball Milling Method and Technology
The Wet Milling Method: A Deep Dive. Wet milling, a core aspect of the wet grinding process, involves breaking down materials in a liquid medium. The wet ball milling process, a popular choice in many sectors, employs a ball mill to achieve a fine grind. This method is particularly effective for materials that are too hard for standard milling ...
اقرأ أكثر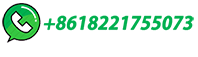
Preparation of copper phthalocyanine/SiO2 composite …
sometimes time consuming. In addition, the presence of organicdispersantsmayin uencethedownstreamapplications of the organic pigments. Preparation of pigment/inorganic CPs through a simple physical milling process may be straightforward and efficient. Lan et al. prepared pigment/clay CPs by simple wet-pulverizing
اقرأ أكثر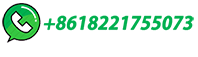
Promise of combined hydrothermal/chemical and mechanical refining …
Ball mills, extruders, and disk (disk) mills are the major scalable methods used for pretreatment. These unit operations are scalable and adapted for dry and wet samples (Fig. 4). Ball mills grind using shear and compressive forces. Ball milling reduces cellulose crystallinity as well as particle size [37, 38]. Since the ball milling can be ...
اقرأ أكثر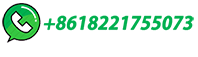
Aggregate Wet Ball Mill – Rainhart
The Rainhart Aggregate Wet Ball Mill is used to determine the resistance of aggregate in flexible base materials to disintegration in the presence of water. These results are essential in determining whether the base will resist crushing, degradation, disintegration, and premature structural failure.
اقرأ أكثر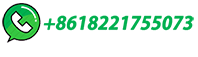
Ball milling as a mechanochemical technology for …
The mass ratio of milling media to biochar during wet ball milling was demonstrated as the most crucial parameter and the best performance was obtained at 100:1 (Peterson et al., 2012). Despite being comparatively less effective, salt-assisted dry ball milling could also increase the total surface area and the proportion of micropores …
اقرأ أكثر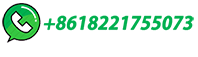
Grinding kinetics of quartz and chlorite in wet ball milling
For each grinding test, the mill was first loaded with a 1.86 kg mass of ball mix and a 150 g mass of feed sample material.A volume of 64.0 ml tap water was then added to the mill charge in order to make a 70 wt.% pulp density.Four mono-sized fractions of quartz and chlorite(− 2 + 1.19 mm, − 1.19 + 0.5 mm, − 0.5 + 0.25 mm, − 0.25 + 0.15 …
اقرأ أكثر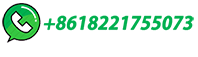
Foods | Free Full-Text | Emulsification Characteristics of …
To improve the application potential of pomelo peel insoluble dietary fiber (PIDF) in emulsion systems, acetylation (PIDF-A), cellulase hydrolysis (PIDF-E), and wet ball milling (PIDF-M) were investigated in this paper as methods to change the emulsification properties of PIDF. The impact of the methods on PIDF composition, …
اقرأ أكثر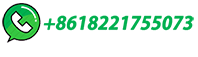
Pharmaceutical nanocrystals: production by wet milling …
Wet media milling equipment used for the production of nanosuspensions can be divided into planetary ball mills and wet stirred media mills. Planetary ball mills are high-energy ball mills and their name is derived from the kinematics of the grinding components, which are analogous to the rotation of the Earth around the sun.
اقرأ أكثر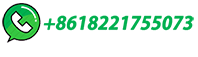
Emulsification Characteristics of Insoluble Dietary Fibers …
Wet ball milling was reported to improve the water- and oil ... followed by rapid cooling to 60 °C and addition of 1 mL papain solution. ... Specifically, a 2% (w/v) PIDF aqueous solution was prepared and added to the dispersion unit connected to the laser particle size analyzer until the degree of masking was approximately 10%. The particle ...
اقرأ أكثر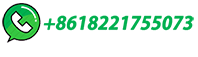
Wet Overflow Type Ball Mill and Applications
How Overflow Type Ball Mill Works. Material Feed: The raw material is fed into the mill at one end and travels through the mill by rotation. The feed enters the mill at a specific rate, ensuring a controlled grinding process.; Grinding Process: As the mill rotates, the grinding media crushes and grinds the material into a fine powder. The wet …
اقرأ أكثر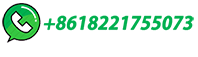
Modeling of Bauxite Ore Wet Milling for the Improvement …
In addition, based on experimental ball mill studies, the fractal particle distribution was found to describe the PSDs of comminution products [40,41,42], although the results of other studies differ . In the present study, the two-parameter functions, namely GGS, RR, and logistic models, were used to characterize the PSDs of the grinding mill ...
اقرأ أكثر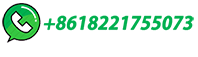
The best addition of graphene to LiMn0.7Fe0.3PO4/C …
LiMn x Fe 1-x PO 4 with high electronic conductivity is synthesized by a combination of wet ball milling, spray drying, carbon thermal reduction technology and using graphene oxide (denoted as GO) as the carbon additive. The effect of graphene content on morphology and structure of LiMn 0.7 Fe 0.3 PO 4 /C cathode material is …
اقرأ أكثر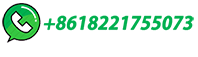
Closed Circuit Grinding VS Open Circuit Grinding …
The simplest grinding circuit consists of a ball or rod mill in closed circuit with a classifier; the flow sheet is shown in Fig. 25 and the actual layout in Fig. 9. ... It takes nearly half an hour to clear the circuit …
اقرأ أكثر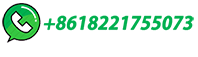
Modern Wet Milling and Material Processing
Grinding media for ball mills ranges in size from 6 - 10 mm for most traditional applications and 1.5 - 2.0 mm for vertical mills. …
اقرأ أكثر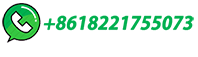
_Taurus
NETZSCH Taurus has the most advanced technology in Mills using Grinding Media for micronizing.. A rotating robust steel drum with liners is supplying kinetic energy to grinding media inside the mill. These grinding media are crushing and grinding fresh product due to impact and friction.
اقرأ أكثر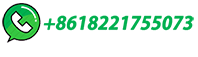
Ball Mill (Ball Mills Explained)
Crushed ore is fed to the ball mill through the inlet; a scoop (small screw conveyor) ensures the feed is constant. For both wet and dry ball mills, the ball mill is charged to approximately 33% with balls (range 30-45%). Pulp (crushed ore and water) fills another 15% of the drum's volume so that the total volume of the drum is 50% charged.
اقرأ أكثر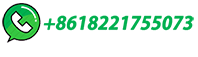
Ball Mill Design/Power Calculation
Ball Mill Power Calculation Example #1. A wet grinding ball mill in closed circuit is to be fed 100 TPH of a material with a work index of 15 and a size distribution …
اقرأ أكثر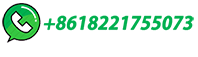
Ball milling as an important pretreatment technique in …
In terms of final particle size, wet ball milling is more suitable to reduce the particle size below 1 µm compared to dry ball milling . In addition, wet ball milling suppresses the role of surface forces and prevents the agglomeration tendency of fine particles to get narrow particle size distribution . Dry ball milling produces particles ...
اقرأ أكثر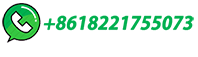
Grinding
Comparing dry and wet grinding curves in a ball mill in the same condition (an equal amount of materials and grinding media has been used on each pair of wet-dry experiments) (Fig. 1.7) indicated two significant differences at higher power values of wet grinding, specifically when speed exceeded 0.6 critical speed and for higher ω Pmax in …
اقرأ أكثر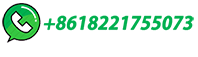