Casing Cementing Design Program Guidelines
The cement slurry gradient design can be adjusted within limits imposed by the type of cement and additives that can be used. Neat Portland cement can be made up into a stable slurry with a gradient in the range of 17 to 20 kPa/m (0.75-0.88 psi/ft).
اقرأ أكثر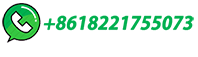
Ball charge optimization
§ Lafarge Mill grinding reference, 2nd edition, Volume 3: Process Methods and Theories, Section C: Ball Charge Design § Post-Sevilla Ball Mill Optimization § Blue Circle, Cement Optimization, November 2000 § BP Selecting Shell Liners in ball mills § VADE-MECUM, CTS 2000 § Ball mill audit BP : Contacts: Process groups in Technical Centers
اقرأ أكثر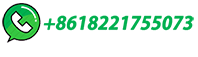
Cement Finish Milling (Part 1: Introduction & History)
The finish mill system in cement manufacturing is the second to last major stage in the process, where the feed material is reduced in size from as large as several centimeters in diameter, down ...
اقرأ أكثر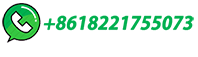
Conveying and Storing in the Cement Industry
the Cement Industry 6 Clinker Transport 10 Conveying of Raw Meal, Cement and Additives 12 Transport of Raw Material, Clinker, ... • Shock-pressure proof design as an option For coal mill feeding applications, all Chain Conveyors come in a design which is shock-pressure proof up to 3.5 bar on a standard basis. Additionally, such Chain ...
اقرأ أكثر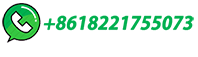
8 Tips For Cement Plant Design
The design of the raw material grinding system should focus on the energy-saving, vertical mill grinding system because of its power-saving, simple process to become a large cement plant, the use of a ball mill grinding system is no more than two reasons: first, the raw material is difficult to grind, such as high quartz sandstone content, the ...
اقرأ أكثر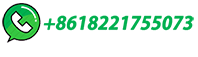
What Is Cement Milling? Difference Between Raw Mill And Cement Mill
In a cement mill, the clinker, gypsum, and other additives are ground into a fine powder which is then mixed into a slurry surrounded by rotating rollers. ... Exploring the Essentials of Modern Kitchen Design: Understanding Stainless Steel Sinks; Difference Between Gable And Eave; All About Concrete, Building, Construction and Interior …
اقرأ أكثر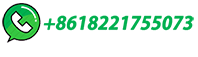
Clinker grinding technology in cement manufacturing
Clinker grinding technology is the most energy-intensive process in cement manufacturing. Traditionally, it was treated as "low on technology" and "high on energy" as grinding circuits use more than 60 per cent of total energy consumed and account for most of the manufacturing cost. Since the increasing energy cost started burning the benefits …
اقرأ أكثر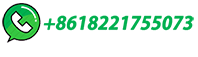
MEXICO PROJECTs Modern milling in Mexico
Modern milling in Mexico Encouraged by healthy construction demand and promising growth potential, two regional cement manufacturers have decided to invest in cement grinding facilities in Yucatán, Mexico. Both Cementos Fortaleza and Holcim México have …
اقرأ أكثر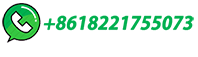
Ball mill for cement grinding
The horizontal slide shoe bearing design enables much simpler foundations and reduced installation height, making installation quicker and less expensive. Our shell linings are designed to suit the task at hand. In our two-compartment cement mills, the first compartment (for coarse grinding) has a step lining suitable for large grinding media ...
اقرأ أكثر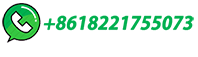
Building a House in Mexico: Costs and Considerations
Design and Architecture. Once you have chosen a location, the next step is to design your house. Hiring an architect who is familiar with local building regulations and environmental conditions is crucial. ... While traditional materials such as brick and concrete are widely used in Mexico, there is also a growing trend towards sustainable …
اقرأ أكثر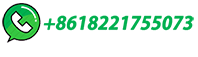
OK™ Raw and Cement Mill
Our best-in-class OK™ Mill is a globally successful vertical roller mill solution for grinding raw material, cement and slag. Its cutting-edge design features consistently deliver the highest quality products with the greatest efficiency. It is affordable to install and cost effective to operate over your cement plant's lifetime.
اقرأ أكثر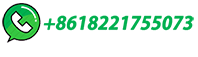
Heat Integration in a Cement Production | IntechOpen
1. Introduction. Nowadays, cement manufacturing is an energy-intensive industry. The energy costs of cement industry are about 40% of the product cost that indicates that this sector is one of the biggest CO 2 emitter. The global anthropogenic CO 2 emission of cement industry is approximately 5% [].The International Energy Agency …
اقرأ أكثر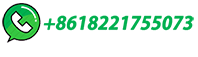
Grinding in Ball Mills: Modeling and Process Control
The design of a ball mill can vary significantly depending on the size, the . ... Mill. – Cement and Concrete Research, V ol. 33, 2003, 439-445. 16. D i n g, B. C. Modern Predictive Control ...
اقرأ أكثر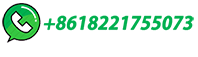
Model-Free Adaptive Controller Design Based on Data-Driven ILC Cement
Abstract: Based on the analysis of the process of cement raw meal vertical milling system, this paper points out the key control output in the process, the mill vibration, and designs a controller to control it by iterative learning and model-free adaptive control methods. Firstly, the PPD state observer is designed for dynamic linearization, and the controller design …
اقرأ أكثر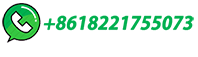
Improving cement production through Artificial Intelligence
The second-to-last stage of cement production happens in mills, where clinker is ground from a size of several centimeters into pieces less than 100 microns in size. That is smaller than a grain of beach sand! This process consumes approximately 40 kWh per ton of cement, accounting for the most electrical power consumption in the …
اقرأ أكثر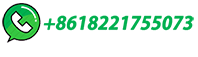
Design of Ball Mill Feeding System
Cite this article: GU Deming,SHI Zhenming,JIANG Zhiyong. Design of Ball Mill Feeding System[J]. Cement Technology, 2019, 1(5): 70-73.
اقرأ أكثر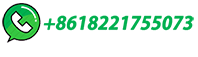
BNamericas
BNamericas talked to the president of cement chamber Canacem, Yanina Navarro, about this year's challenges, why the pandemic didn't hurt the sector, the …
اقرأ أكثر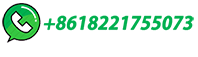
quadropol® | thyssenkrupp Polysius Grinding Technologies
The cement mills are equipped with high efficiency separators to achieve cement qualities with a fineness up to 5 000 cm2/g acc. to Blaine. Cemento Progreso, Guatemala, 4500 tons per day plant incl. QMR² and QMC² ... The vertical roller mill design calculation considers efficient comminution, longevity and highest reliability. The reduction ...
اقرأ أكثر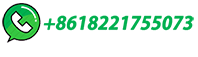
The cement mill
Cement manufacturing - brief description of a cement mill. Cement clinker is usually ground using a ball mill. This is essentially a large rotating drum containing grinding media - normally steel balls. As the drum rotates, the …
اقرأ أكثر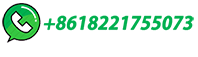
Predictive Controller Design for a Cement Ball Mill Grinding …
The annual cement consumption in the world is around 1.7 billion tonnes and is increasing by 1% every year [].Cement industries consume 5% of the total industrial energy utilised in the world [].A total of 40% of the total energy consumption of a cement plant is used in clinker grinding in a ball mill to produce the final cement product []. ...
اقرأ أكثر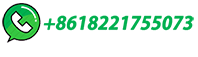
Cement Plants located in Mexico
International Cement Review; Cement Plant Operations Handbook 7th Edition; The Global Cement Report 15th Edition; Cement Plant Environmental Handbook 3rd Edition; Conferences. Cemtech Live Webinar: Approaches to cement sector decarbonisation, 04 September 2024; Cemtech Europe 2024, Warsaw, Poland, 29 September - 02 October …
اقرأ أكثر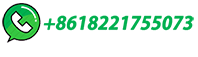
Cement Grinding Plant | Expert Cement Grinding
We master the construction and design schemes of various cement grinding plant systems such as vertical mill system, combined system, and ball mill system. No matter what type and strength of cement you want to produce, and what production capacity you need, we can customize the appropriate grinding unit for you.
اقرأ أكثر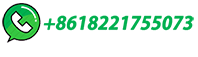
Estanda improves productivity at Mexico mill
Estanda has successfully completed the improvement of a raw cement mill for a cement plant in Mexico. The aim of the project commissioned to Estanda was to …
اقرأ أكثر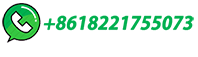
Country Report: Cement Production in Mexico is Stable
But the concrete segment, according to a study by the Asociación Mexicana de Concreteros Independientes (AMCI), which covers 550 companies in the country and has around 1,250 plants that represent 60% of the national market, the situation remains difficult due to the high price of cement as the margins of their companies have decreased.
اقرأ أكثر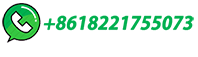
Concrete Architecture: 20 Outstanding Projects in …
Inspired by unconventional works like these, we now present a compilation of projects that explore concrete's many possibilities throughout different scales and latitudes of Mexico.
اقرأ أكثر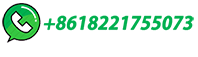
Cement Mill for Sale | Buy Cement Ball Mill
Cement mills are the milling machines used in cement plants to grind hard clinker into fine cement powders. Cement ball mill and vertical roller mill are two most widely used cement mills in today's cement grinding plants and are also the main types of cement mill we produce.. As a professional cement equipment manufacturer, AGICO has rich …
اقرأ أكثر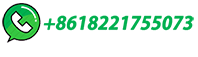
Decarbonization of Cement Industry in Mexico
In this study, we look at the current status of cement production in Mexico and we analyze different technologies pathways under major decarbonization pillars that can help to reduce CO2 emissions of …
اقرأ أكثر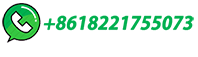
The Cement Plant Operations Handbook
Burner design – 5. Cement kiln burners – 6. Heat transfer – 7. Pollutant formation – 8. Modelling – 9. Fuel storage and firing systems in practice – 10. ... Cement mill specific power consumption – 4. Other systems – 5. De-bottlenecking – 6. Project audit – 7. Risk assessment. 14. Plant assessment list 234 1. General – 2.
اقرأ أكثر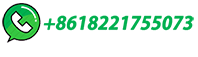