IMPROVING THERMAL AND ELECTRIC ENERGY …
use and now account for over 90 percent of cement consumption worldwide (4.1 billion tons in 2016). Cement accounts for at least 5 percent of anthropogenic emissions of greenhouse gases, and, according to some estimates, this share may be even higher. At the same time, energy-related expenses in the cement sector, mostly
اقرأ أكثر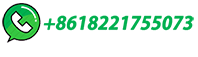
IMPROVING THERMAL AND ELECTRIC ENERGY …
Emerging markets have been rapidly increasing their cement use and now account for over 90 percent of cement consumption worldwide (4.1 billion tons in 2016). Cement …
اقرأ أكثر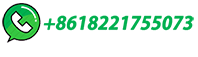
Everything you need to know about Thermal Energy Efficiency in Cement
as energy for gate to gate energy consumption. Renewable energy is a cleaner and greener way to generate power. A modern 1 million capacity plant today requires a total energy consumption of 10 MW. It can be very attractive to go for renewable power generation by design. Few of the renewable energy technology, their estimated …
اقرأ أكثر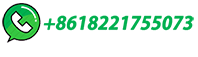
BALL MILLS Ball mill optimisation
Ball mill optimisation As grinding accounts for a sizeable share in a cement plant's power consumption, optimisation of grinding equipment such as ball mills can provide significant cost and CO 2 emission benefits to the cement producer. n by Thomas Holzinger, Holzinger Consulting, Switzerland BALL MILLS 1 FEBRUARY 2021 INTERNATIONAL …
اقرأ أكثر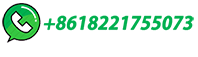
Reducing energy consumption of a raw mill in cement …
In the whole process of cement production, the electricity consumption of a raw material mill accounts for about 24% of the total. Based on the statistics of the electricity consumption of the raw…
اقرأ أكثر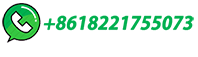
Country Report: Cement Production in Mexico is Stable
In January of this year, according to data from the national statistics institute (INEGI), the industry produced 4.2 million tonnes, 533,000 t higher than in 2020 and …
اقرأ أكثر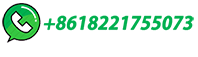
IMPROVING THERMAL AND ELECTRIC ENERGY EFFICIENCY AT CEMENT …
use and now account for over 90 percent of cement consumption worldwide (4.1 billion tons in 2016). ... mills saves energy without compromising quality. Modern,
اقرأ أكثر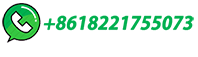
Heat Integration in a Cement Production | IntechOpen
1. Introduction. Nowadays, cement manufacturing is an energy-intensive industry. The energy costs of cement industry are about 40% of the product cost that indicates that this sector is one of the biggest CO 2 emitter. The global anthropogenic CO 2 emission of cement industry is approximately 5% [].The International Energy Agency …
اقرأ أكثر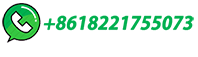
Evaluation of Carbon Emission Factors in the Cement …
The cement industry is a major contributor to carbon emissions, responsible for 5–8% of global emissions. This industry is expanding, particularly in emerging economies, and it is expected that CO2 emissions will rise by 4% by 2050. To address this critical concern, this paper identifies ten factors that contribute to carbon emissions in …
اقرأ أكثر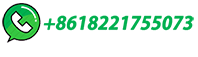
Modeling of energy consumption factors for an industrial cement …
Understanding relationships among operational variables can effectively help to improve control systems and reduce energy consumption in the cement plant as one of the most intensive energy consumer industries. Digitalization and constructing a conscious lab for exploring correlations between operational variables of a vertical roller mill and ...
اقرأ أكثر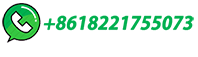
Cement grinding Vertical roller mills VS ball mills
However, with proper adjustments to the operational parameters of the vertical roller mill almost identical cement properties can be achieved by the two mills that satisfy the cement user's demands.Nevertheless, the two types of mills have their distinctive merits. ... It appears from the table that the specific energy consumption of the OK ...
اقرأ أكثر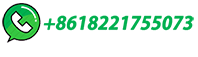
Energy consumption assessment in a cement production …
The process of manufacturing cement is known to be an energy-intensive process; it involves the consumption of coal (fossil fuel), electrical energy, as well as other resources of energy, and this ...
اقرأ أكثر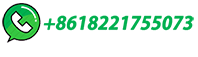
Review on vertical roller mill in cement industry & its …
Cement is an energy-intensive industry in which more than 60% of the total electricity is used in grinding circuits and also bears most of the construction cost. The need of the cement industry in the future is to reduce the specific energy consumption in grinding process [7] (Fig. 2). Download: Download high-res image (52KB)
اقرأ أكثر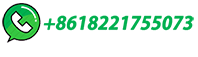
Improving cement production through Artificial Intelligence
That is smaller than a grain of beach sand! This process consumes approximately 40 kWh per ton of cement, accounting for the most electrical power consumption in the production of cement. Cemex is using "Model-Based Optimization", which consists of using machine learning to generate models that predict the …
اقرأ أكثر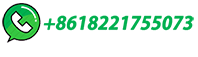
Country Report: The Cement Industry in Mexico
The fall in GDP was generated by the decrease in the production of secondary activities, which include manufacturing, construction, mining and energy activities, which fell 1.8% compared to …
اقرأ أكثر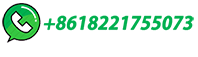
Reduce Your Energy Costs in the Cement Industry with …
Deploying a digital solution in your cement plant can help you reduce your energy consumption and your carbon impact while ensuring the sustainability of your know-how and ... In this highly digitalized Brazilian cement plant, three mills are used to produce three types of ... Mexico. Av. Oaxaca n°96 – int. 202-A, Col. Roma Norte ...
اقرأ أكثر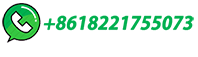
Improvements in New & Existing Cement Grinding Mills by …
o For ball mills, only 3 – 6% of absorbed energy is utilized in surface production, the heat generated can increase mill temperature to > 120⁰ C & causes excessive gypsum dehydration & media coating if mill ventilation is poor. Types of cement mills. There are basically 4 types of cement mills in use today: Ball Mill (BM)
اقرأ أكثر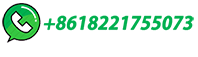
Optimising Specific Energy Consumption in the Cement …
The energy efficiency within the Cement Industry is measured as a combination of two factors – thermal specific energy consumption and electrical specific energy consumption. Currently about 99 per cent of the Indian cement companies has transitioned to a water efficient dry process technology thereby conserving a significant …
اقرأ أكثر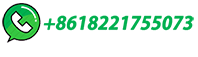
A Survey and Analysis on Electricity Consumption of …
Material Mill System in China Cement Industry between 2014 and 2019 Ruonan Meng 1,2, Qinglin Zhao 1,2,*, ... In cement production, the energy consumption of the grinding process is mainly
اقرأ أكثر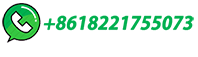
Cement plant performance optimization Benchmarking, …
Reducing energy consumption, associated costs and environmental impact Energy efficiency and energy cost reduction are the top priori-ties for the cement and minerals industry. ABB has extensive experience in developing and supplying energy management solutions that meet their needs. ABB's energy management solutions reduction energy …
اقرأ أكثر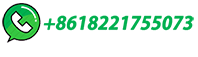
A step towards sustainable development: Cement …
Incorporating the latest technology to minimize electrical and thermal energy consumption, the plant shows outstanding operational efficiency and economic performance.
اقرأ أكثر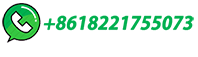
Carbon emissions mitigation methods for cement industry
The cement production process emits approximately 0.9 tons of CO 2 per ton of cement (Hasanbeigi et al. 2010), accounting for about 5–8% of global CO 2 emissions and ranking as the second-largest CO 2 emissions source (Mikulčić et al. 2016; Kajaste and Hurme 2016).According to the Intergovernmental Panel on Climate Change (IPCC) …
اقرأ أكثر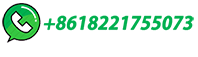
(PDF) Grinding Media in Ball Mills-A Review
the grinding media reduces energy and material consumption in a ball mill. Different performances are achieved when different sizes and shapes of grinding media are used [ 12 ].
اقرأ أكثر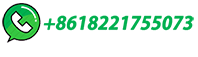
Towards Leveraging Artificial Intelligence for Sustainable Cement …
Cement manufacturing is known for its significant energy consumption and environmental footprint. As the world strives for sustainability, optimizing electrical energy consumption (EEC) in cement manufacturing is essential for reducing operational costs and minimizing the industry's environmental impact. This systematic review aims to …
اقرأ أكثر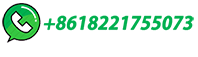
Energy use and CO2 emissions for Mexico's cement industry
In this paper, we analyze the factors that influenced energy use and CO 2 emissions in the Mexican cement industry from 1982 to 1994. During this period, energy …
اقرأ أكثر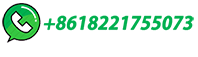
Electricity use per tonne of cement in selected countries and …
n.e.c = not elsewhere counted. CIS = Commonwealth of Independent States. BAT = energy intensity covers the process up to the liquid steel stage, i.e. it does not include energy used in casting and rolling, or energy used by captive thermal utilities (which are included in reported energy intensity).
اقرأ أكثر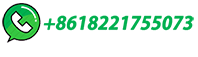
The cement industry is the most energy intensive of all …
The industrial sector, which encompasses manufacturing, mining, agriculture, and construction, accounted for almost a third of total U.S. energy use in 2012.Energy-intensive manufacturing accounted for a little more than half of total industrial energy use. Although the cement industry used only one-quarter of one percent of total U.S. energy, …
اقرأ أكثر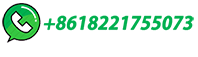
Energy-Efficient Technologies in Cement …
1. Introduction. Cement is an energy-intensive industry in which the grinding circuits use more than 60 % of the total electrical energy consumed and account for most of the manufacturing cost [].The …
اقرأ أكثر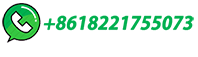
Best energy consumption
A typical comparison of three competing technologies is given in Table 1, demonstrating that an efficient ball mill/third-generation separator, CKP/ball mill/third-generation separator and vertical mill on a typical 4000Blaine limestone cement show little overall difference in energy consumption.
اقرأ أكثر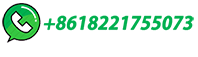
Energy efficiency in clinker production
Figure 1 shows the areas of high energy consumption in a cement plant. The numbers clearly indicate that grinding of both raw meal and cement needs highest attention. ... The main energy issue was the high power consumption of mill fans, with pressure drops of 100 mbar is not uncommon with high nozzle ring velocities (>70m/s) …
اقرأ أكثر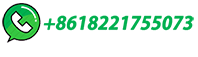