"Blueprint" Your Pulverizer for Improved Performance
areas of the burner coal pipes and coal nozzles (Figure 8). Step 4. Properly maintain the classifier. Once the grinding zone is blueprinted and put in first-class condition, the next com-ponent to examine is the classifier. The best furnace combustion performance is governed by uniform coal combustion by the burn-ers and satisfactory coal fineness.
اقرأ أكثر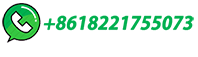
A Comparison of Three Types of Coal Pulverizers
As shown in Figure 2, coal and preheated primary air first enter the crusher section. Here the coal is im- pacted on a grid section by swing hammers, reducing the coal to a nominal 1/4" size. Drying of the coal also occurs in this section. After the coal passes through the grid section, it enters the two-stage pulverizing sec- tion.
اقرأ أكثر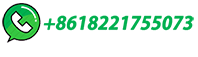
Standard Test Method for Sampling and Fineness Test …
6.1 In the direct-fired system, the coal is pulverized and delivered directly to the furnace in an air stream. It is difficult to obtain representative samples, as it is necessary to sample the coal from a moving stream of coal-air mixture inside the pipe between the pulverizer and furnace. It is preferable to
اقرأ أكثر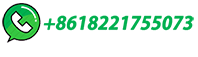
RILEY POWER'S ATRITA COAL PULVERIZERS RELIABLE …
Integral fan purges the pulverizer of coal dust after the coal feed is stopped As raw coal and primary air enter the crusher section during start-up, air temperature is lowered as coal moisture is evaporated and only relatively cool air comes in contact with the pulverized coal Easy Access for Maintenance
اقرأ أكثر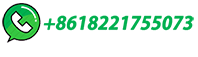
Pulverizers 101: Part III
A well-performing system will have coal fineness of 75% or more passing a 200 mesh screen; 50-mesh particles should be less than 0.1% in each of the coal pipes. Courtesy: Storm Technologies Inc.
اقرأ أكثر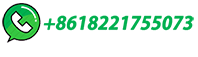
"Blueprint" Your Pulverizer for Improved Performance
Pulverizer throughput is determined by the coal fineness desired for a given coal. However, compromising on coal fineness when your pulverizer isn't up to snuff can …
اقرأ أكثر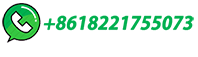
Pulverizer Performance & Capacity Improvements
ASME/ASTM Method Coal Sampling; Obtain representative fuel samples for coal fineness analysis. Dirty Air/Iso-kinetic Fuel Sampling. Ascertain relative pipe-to-pipe fuel balance. Quantify individual fuel line air-to-fuel ratios. Quantify pulverizer air-to-fuel ratios. Quantify individual fuel line velocity and air flow.
اقرأ أكثر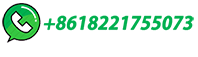
CFD based investigations into optimization of coal pulveriser
In coal-fired power plant, pulveriser is the first major component, whose performance dictates the total power plant efficiency. Uniform flow rate and desired size fraction at outlet pipes along ...
اقرأ أكثر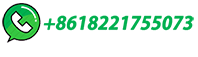
Boiler Mill and Coal Pulverizer Performance | GE Steam Power
Up to 20% improved coal fineness. GE's PV-PRO mill upgrade system uses a patented process for better control of coal fineness and reduced pulverizer wear for extended operations. Up to 6x life extension. HCX2* ceramic inserted grinding elements significantly extend operating time between overhauls.
اقرأ أكثر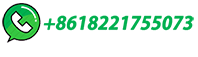
On-line measurement of pulverized coal fineness on a 300 …
DOI: 10.1016/J.POWTEC.2021.02.076 Corpus ID: 233828005; On-line measurement of pulverized coal fineness on a 300 MWe power plant with pulsed digital inline holography @article{Qiwen2021OnlineMO, title={On-line measurement of pulverized coal fineness on a 300 MWe power plant with pulsed digital inline holography}, …
اقرأ أكثر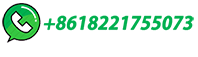
Dynamic classifiers improve pulverizer performance and …
The fineness of coal is measured using a U.S. standard sieve with a sleeve opening of 0.0030 inches. Particles smaller than 74 microns will pass through a 200-mesh screen, and those larger will ...
اقرأ أكثر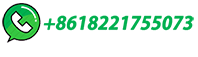
Reliable Coal Pulverizers and Mills » Babcock & Wilcox
Reliable coal pulverizer performance is essential for sustained full-load operation of today's power plants. An effective pulverizer must be capable of handling a wide variety of coals and accommodating load swings in utility boilers as large as 1,300 MW.. B&W's pulverizers, found at power stations throughout the world.
اقرأ أكثر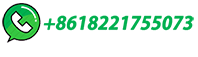
IMPROVE YOUR PULVERIZER PERFORMANCE
The 100 KPPH rating means that operating at those stated conditions the pulverizer product will have a fineness of 70% through a 200 mesh at a throughput of 100 KPPH. Figures …
اقرأ أكثر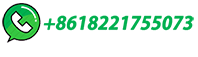
IMPROVE YOUR PULVERIZER PERFORMANCE
4. Lower air flow results in better fineness & less erosion. 5. Lower air flow can result in more pyrites, but fewer burner eyebrows. 6. Lower air flow means and a greater tendency to plug with wet coal. 7. Lower air flow leaves more reserve fines in the pulverizer. 8. Also note that lower air flow leaves a deeper bed depth of coal, and thus a ...
اقرأ أكثر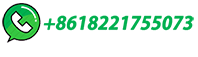
Experimental study effect of classifier pulverizer opening setting
Download Citation | Experimental study effect of classifier pulverizer opening setting variation on fineness production passed 200 mesh | In coal-fired power plants, the performance of the ...
اقرأ أكثر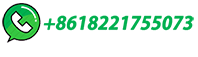
Coal mill pulverizer in thermal power plants | PPT
20. 13.1.Fineness Fineness is an indicator of the quality of the pulverizer action. Specifically, fineness is a measurement of the percentage of a coal sample that passes through a set of test sieves usually designated at 50, 100, and 200 mesh A 70% coal sample passing through a 200 mesh screen indicates optimum mill performance. …
اقرأ أكثر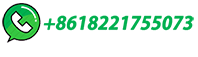
Pulverized Coal Pipe Testing and Balancing
The isokinetic coal sampling method, although more difficult, is the best option for determining the true mill coal fineness produced and to calculate pulverizer performance.
اقرأ أكثر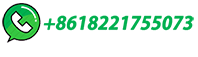
CFD based investigations into optimization of coal pulveriser
The raw coal from the coal feed chute (8) mixes with returned oversize material (7) to form a mixed stream that passes between the grinding balls and bottom grinding ring in grinder section. The top grinding ring is loaded to provide the grinding pressure. The coal size is reduced with each passage between the grinding balls . …
اقرأ أكثر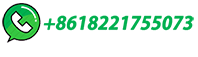
Pulverizer Performance and NOx Emissions
More even distribution of coal results in more precise control of burner stoichiometry that is critical to reducing NOx and achieving the best possible burner performance. Some units are more or less forgiving to …
اقرأ أكثر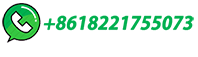
CPRI
ONLINE COAL FLOW MEASURING AND BALANCING (CONTROL) AND ONLINE COAL FINENESS MEASURING SYSTEM FOR COMBUSTION OPTIMISATION IN A THERMAL BOILER Suresh G. Chandwani1, Dr. Franc Turoni2, Reinhardt Kock2, Dr. Michael Haug2, Dr. Michael Schreiber2 1N.S.Guzder & Company Pty. Ltd, Neville House, …
اقرأ أكثر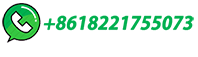
Improved Coal Fineness Improves Performance, Reduces …
Utilizing engineering ingenuity and today's developing computational fluid dynamics tools, a new classifier design is now available that significantly improves fineness from pulverizers without...
اقرأ أكثر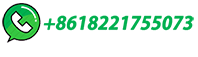
Pulveriser in Thermal Power Plant | Bowl Mill | Ball Mill
Operation Of Bowl Mill Pulveriser . In bowl mill pulveriser raw coal coming from feeder gets ground between the grinding rolls and bull ring segments installed on the revolving Bowl. ... coarser product will be obtained and if the speed of rotation is increased the fineness for given capacity increases. During grinding, balls themselves wear ...
اقرأ أكثر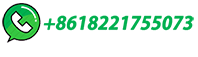
Vertical Grinding Mill (Coal Pulverizer) Explained
Introduction. This article concerns itself with vertical grinding mills used for coal pulverization only (coal pulverizers), although vertical grinding mills can -and are- used for other purposes.. The 3D model in the saVRee …
اقرأ أكثر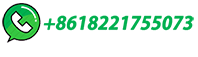
Pulverized Coal Pipe Testing and Balancing
Collecting coal samples using an isokinetic probe provides the best data describing actual operating conditions inside the coal pipe. Source: Storm Technologies Inc. The isokinetic coal sampling method, although more difficult, is the best option for determining the true mill coal fineness produced and to calculate pulverizer performance.
اقرأ أكثر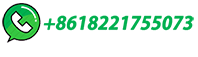
Pulverizer Capacity is not simply "tons throughput per …
the fineness is reduced from about 75% passing 200 mesh to 45% passing 200 mesh, as much as 30% more coal throughput can be pushed through the pulverizers. The previous example is often inadvertently done by increasing primary airflows or opening classifier blades up to increase the coal flow to the furnace by sacing coal fineness.
اقرأ أكثر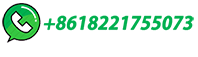
A Study on 500 MW Coal Fired Boiler Unit's Bowl Mill …
lumped coal and to the desired fineness and drying of coal. Transportation of the coal powder is carried out by the primary air to the furnace chamber for effective combustion. There are four major mechanisms that happen during the coal crushing in the mills viz., size reduction in the coal, drying of the coal, transport of the crushed coal and ...
اقرأ أكثر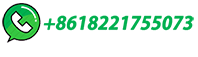
Dynamic classifiers improve pulverizer …
By adding a dynamic classifier to the pulverizers, you can better control coal particle sizing and fineness—and increase pulverizer capacity to boot.
اقرأ أكثر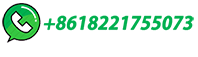
online coal pulveriser fineness
online coal pulveriser fineness. Webonline coal pulveriser fineness. T1108330000. Pulverizer Wikipedia. With adequate mill grinding capacity, a vertical mill equipped with a static classifier is capable of producing a coal fineness up to 995% or higher . 50 mesh and 80% or higher 200 mesh, while one equipped with a dynamic …
اقرأ أكثر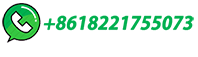
On-line measurement of pulverized coal fineness on a 300 …
Pulverized coal fineness (PCF) is a key parameter in coal-fired power plants, demanding accurate and on-line monitoring. This study presents on-line measurement of PCF on a 300 MWe coal-fired power plant with pulsed digital inline holography (DIH). A prototypal instrumentation system, comprised of sampling, measurement, collection, and …
اقرأ أكثر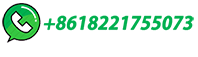