How Cement is Made
Stage of Cement Manufacture. There are six main stages of the cement manufacturing process. Stage 1: Raw Material Extraction/Quarry The raw cement ingredients needed for cement production are limestone (calcium), sand and clay (silicon, aluminum, iron), shale, fly ash, mill scale, and bauxite. The ore rocks are quarried and crushed into smaller …
اقرأ أكثر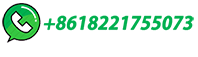
Technical Notebook CEMENT ADDITIVES FOR VERTICAL …
cement works; they allow a reduction of clinker while offering the same mechanical performance of cement, thus guaranteeing a reduction of 5-10% in CO ... 3.2 HOW DOES A VERTICAL MILL WORK? The raw materials are fed directly to the centre of the grinding plate, which, thanks to centrifugal forces and the pushing effect of the incoming ...
اقرأ أكثر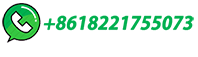
Manufacturer of Ball Mill & Lime Plants by Chanderpur Works …
Chanderpur Works Private Limited - Manufacturer of Ball Mill, Lime Plants & Biomass Gasifier from Yamuna Nagar, Haryana, India. ... Clinker Grinding Ball Mill. Interested Contact Us for more details of your requirement. Girth Gear & Pinion Drive Ball Mill; Quick Lime Calcination Plant;
اقرأ أكثر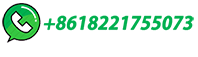
Everything you need to know about Fluxes and …
The following is a review of the role of fluxes and mineralizers in clinker burning and clinker formation with respect to practical experience and reaction kinetics, with emphasis on the reaction CaO + C2S → C3S in …
اقرأ أكثر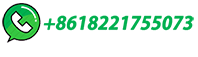
EVERYTHING YOU NEED TO KNOW ABOUT OPERATION AND CONTROL OF CLINKER
EVERYTHING YOU NEED TO KNOW ABOUT OPERATION AND CONTROL OF CLINKER COOLER . ... This means, tl1e majority of the cooling work should be accom plished in the first and second compartments because it is here that the most efficient heat transfer will take place due to the large temperature difference between the air and the …
اقرأ أكثر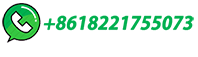
Cement grinding Vertical roller mills VS ball mills
If the temperature of the clinker fed to the mill is very high, the mill exit temperature controls a cold air damper at the air inlet to the mill or – in extreme cases – water injection into the mill. ... • a vertical roller mill installed with a minimum of civil works, i.e. as shown in Figure 9. Installed mill power: 3750 kW. System ...
اقرأ أكثر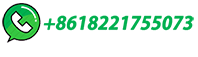
Mercury emission characteristics and mechanism in the raw mill …
The cement clinker manufacturing process can be divided into mill-on and mill-off modes according to the raw mill operating conditions (Li et al., 2019, Zheng et al., 2012). When the raw mill is running during the mill-on mode, the flue gas from the precalciner passes through the raw mill into the dust collector before being emitted.
اقرأ أكثر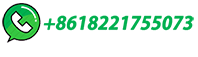
EVERYTHING YOU NEED TO KNOW ABOUT THE CHEMISTRY OF KILN FEED AND CLINKER
This compound composition is calculated with the help of the Bogue formulas, from the potential clinker analysis above (loss-free basis). BOGUE FORMULAS FOR CLINKER AND CEMENT CONSTITUENTS. For a cement chemist, these formulas are the most important and frequently used indicators of the chemical properties of a cement or clinker.
اقرأ أكثر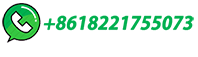
Bond Work Index Formula-Equation
The work index Wi can be determined from plant operations and from laboratory ball mill grindability, rod mill grindability, and impact crushing tests. The laboratory test results are used to check the efficiency of commercial operations and to compute the proper machine sizes for new installations.
اقرأ أكثر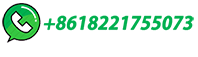
Cracking the Code: The Mystery Behind Why Clinker is Hard …
Pre-grinding involves crushing the clinker before it enters the mill, while inter-grinding additives are blended with the clinker during the grinding process to reduce particle agglomeration and improve overall grindability. ... They work by modifying the properties of clinker, such as its grindability and flow characteristics, resulting in a ...
اقرأ أكثر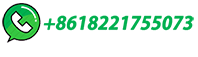
Cement
The clinker and the required amount of gypsum are ground to a fine powder in horizontal mills similar to those used for grinding the raw materials. The material may pass straight through the mill (open-circuit grinding), or coarser material may be separated from the ground product and returned to the mill for further grinding (closed-circuit ...
اقرأ أكثر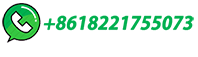
Solving Cement's Massive Carbon Problem
4. Convert Lime into Clinker. How it works: Lime is burned at up to 1,450 degrees C in a kiln rotating three to five times per minute. This process sinters (fuses) the lime into Portland cement ...
اقرأ أكثر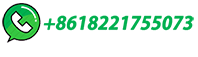
Cement Manufacturing Process
In DMC, these are mainly used for crushing of correctives, pumice, coal and clinker. They are used for size reduction of hard to medium grain size and sometimes for wet and sticky material. Hammer mills work with reduction ratios as high as 1:40 to 1:60 as primary and 15:1 as secondary crushers.
اقرأ أكثر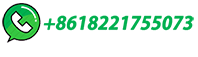
An Introduction to Clinker Grinding and Cement Storage
The typical finishing grinding ball mill is a rotating cylinder divided into two or three chambers containing steel grinding balls of classified size that reduce the clinker to the …
اقرأ أكثر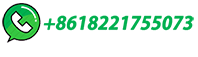
Whitaker Mill Works
Whitaker Mill Works is a creative collective in Raleigh, NC designing furniture and cabinetry. We design and build for both residential and commercial clients with focus on spatial integration. Whitaker Mill Works is a creative collective in Raleigh, NC designing furniture and cabinetry.
اقرأ أكثر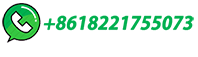
Experimental study of clinker grinding in a ball mill and …
ulometric distribution of the clinker in a ball mill operating in dierent rotation speeds, varying the lling degrees of grinding media and clinker. Then, through DEM simula- ... mental work. Materials and methods Experimental device The mill consisted in a rotating cylinder with diameter of 24.5 cm and internal length of 47 cm, and four lifters ...
اقرأ أكثر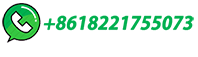
Clinker size and cement grinding | GCP Applied Technologies
Fine clinker is more of an issue in vertical roller mills, since it can quickly slip under the rollers, leading to vibration and instability. As a general rule, there should be …
اقرأ أكثر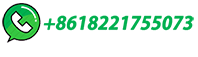
The cement mill
Cement manufacturing - brief description of a cement mill. Cement clinker is usually ground using a ball mill. This is essentially a large rotating drum containing grinding media - normally steel balls. As the drum rotates, the motion of the balls crushes the clinker. The drum rotates approximately once every couple of seconds.
اقرأ أكثر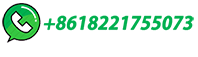
What is Clinker? (Meaning, History, Manufacturing
Ordinary Portland Cement Clinker is the essential component in producing Cement, which is made of sintering limestone.In the manufacture of Cement, clinker formed by sintering or fusing without melting to the point of liquefaction, alumina-silicate materials such as clay and limestone during the cement kiln stage and happens as 3 millimeters (0.12 inches) …
اقرأ أكثر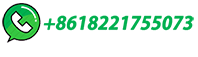
Review on vertical roller mill in cement industry & its …
The cooled clinker is fed to deep metal pan conveyor and it is sent to the clinker storage pile (CSP). The clinker cools further naturally in CSP and extracted and sent through deep pan conveyors to Cement mill for final finished grinding [1], [2], [9], [14]. 2.5. Cement grinding and storage
اقرأ أكثر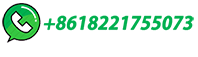
Determination of work index in a common laboratory …
work index in a more common lab mill, such as the Denver lab mill (Fig. 2), is investigated. Experimental Equipment and ore samples. A jaw crusher, a roll crusher, a series of DIN sieves and sample dividers were used to prepare the ore samples. A 305- by 305-mm (12- by 12-in.) standard Bond mill, a 305- by I 27-mm (12- by 5-in.) Denver
اقرأ أكثر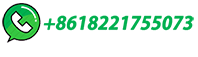
Clinker Grinding Techniques in Cement Manufacturing
Explore the significance of clinker grinding in cement manufacturing, from particle size reduction to improved reactivity and quality control. Learn how this integral …
اقرأ أكثر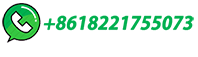
shibang/sbm how to ball mill works for clinker grinding …
shibang / sbm how to ball mill works for clinker grinding model.md. dushusbm c4a532c29b code. 19:24:26 +08:00. 30 KiB Raw ...
اقرأ أكثر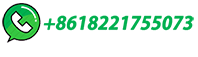
How Cement is Made
The clinker keeps cooling and a ball mill grinds it with gypsum or other ingredients into fine cement—about 150 billion grains per pound. Blending in higher ratios of limestone or SCMs can reduce a plant's carbon footprint by up to 10%.
اقرأ أكثر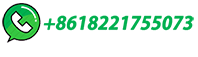
The Cement Manufacturing Process
The clinker is ground to a fine powder in a cement mill and mixed with gypsum to create cement. The powdered cement is then mixed with water and aggregates to form concrete that is used in construction. Clinker quality depends on raw material composition, which has to be closely monitored to ensure the quality of the cement. …
اقرأ أكثر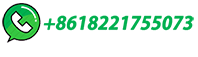
Rotary kiln process: An overview of physical mechanisms, …
The rotary kiln is used in many solid processes, including drying, incineration, heating, cooling, humidification, calcination and reduction. This widespread application can be attributed to factors such as the ability to handle varied loads, with large variations in particle size [1].The rotary kiln is a slightly inclined steel cylinder that rests …
اقرأ أكثر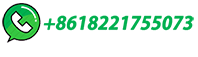
Grinding work index according to Bond
The Tovarov grindability index is used to determine the influence of materials on the cement clinker grinding capacity of a mill; the basis is rotary kiln clinker with a defined grindability index of a = 1.According to this, a mill grinding 30 t/h clinker, will grind 30 x 1.40 = 42 t/h of marl or 30 x 0.6 = 18 t/h of silica sand. The grindability index of rotary kiln clinker itself …
اقرأ أكثر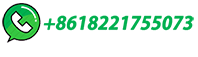
Clinker Production
Clinker production can be divided into preheating and pre-calcining, clinker sintering, and clinker cooling three stages. Cyclone preheater, cement kiln, and clinker cooler are three main cement manufacturing machines in …
اقرأ أكثر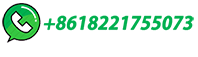
An overview of alternative raw materials used in cement and clinker
The raw materials are then ground in suitable ball mills/vertical roller mills (VRMs), both of which are common grinding mills, in order to achieve the targeted fine powder, which is stored in pre-homogenisation silos (Aïtcin and Flatt Citation 2015; Hewlett Citation 2003). In stage three, the raw mix is fed into a preheating chamber.
اقرأ أكثر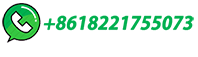