Sponge Iron Production Process
Market share: about 60% of the total production of sponge iron; 2) HYL process (4th generation) or Energiron ... The use of magnetite rock is not recommended as it requires high-grade hematite iron ore. Reducing agent: The advantage of this method is the possibility of using relatively low-quality thermal coal as the reducing agent. Coal in the ...
اقرأ أكثر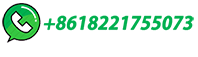
Direct Reduction Ironmaking
It is the process in which high-temperature reducing gas and solid reductant are used to reduce iron ore in order to produce sponge iron.
اقرأ أكثر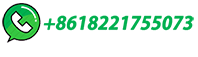
Sponge iron: Uses, process formula, iron plant, and more
Further, it is melted at 1100° C which produces sponge iron. Let's understand in-depth the uses and applications of sponge iron, the production process, and more. Sponge iron plants in India. Since the year 2002, India has become the largest producer of sponge iron worldwide and 20% of the sponge iron is produced by India …
اقرأ أكثر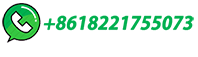
Which Is Better: A Sponge Iron or a Pig Iron?
Whether you're a seasoned professional or a newcomer to the industry, this post is for you. So, grab a cup of coffee, and let's explore the world of Sponge Iron vs Pig Iron together! An Overview of Sponge Iron vs Pig Iron. Sponge Iron vs Pig Iron are two popular raw materials used in manufacturing. Sponge Iron, also known as Direct …
اقرأ أكثر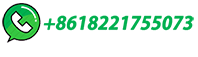
Sponge Iron
Direct reduction iron or sponge iron is an old method for producing hydrogen (Milne et al., 2006; Peña et al., 2010; Biljetina and Tarman, 1981) that was replaced by more efficient and economic processes.Recently, the interest in sponge iron as a hydrogen production process has grown again, although the technology still has some major technical and …
اقرأ أكثر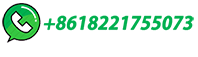
Sponge Iron
Sponge iron is produced by low-temperature reduction of iron ore in a rotary furnace, shaft furnace, or reactor. Since the reduction temperature is lower than the melting temperature of the ore, the iron ore still maintains the shape of the ore after solid-state reduction, and has a porous and low-density sponge-like structure, hence the …
اقرأ أكثر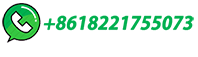
Direct Reduction Iron
It is the iron metal product that is produced from the direct reduction process that uses lump iron ore or concentrate powder pellet as raw material and gas (CO or H 2) or solid charcoal (coal or coke) as reductant and that operates in a temperature less than the melting point of furnace burden.
اقرأ أكثر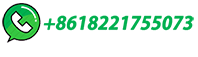
Direct Reduced Iron
Fig 1 Types of DRI. As compared with DRI, the most important specific characteristics of HBI are (i) no change in the chemical analysis by the briquetting process, (ii) only minimal loss of metallization even after long time storage, (iii) open air storage both at the producer and user sites does not cause problems (no need for inertized silos as …
اقرأ أكثر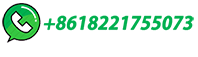
Sponge Iron
Advantages of SIPL Sponge Iron / DRI: High Fe Content and high degree of metallization. Uniform and Consistent quality. Lower Sulphur & Phosphorus content. ... This process increases the tensile strength of the material while keeping high ductility and weldability. This whole process is a patented technology from HSE, Germany under the brand ...
اقرأ أكثر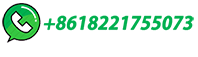
Sponge Iron
Sponge Iron: An Essential Ingredient in Steel Production. Delve into the production process, applications, and market dynamics of sponge iron, a crucial raw material in steelmaking. Explore its role in providing a cost-effective and sustainable alternative to traditional iron ore-based production methods.
اقرأ أكثر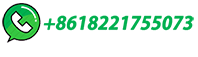
A Step-By-Step Guide To Powder Metallurgy Process
Sponge Iron Process; During this process, the mixture of magnetite ore, coke, and lime is placed in a silicon carbide retort. Heating this retort in kiln results in an iron cake and a slag. ... Powder Metallurgy Process Advantages and Disadvantages Advantages of Powder Metallurgy. The following are some remarkable benefits of …
اقرأ أكثر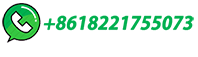
Sponge Iron | Manufacturer of Sponge Iron
Sponge iron is formed through the reduction of iron ore to metallic iron through reaction with carbon in the form of coal, etc. at approx. 1100 degree Celsius. ... Advantage. JSWAION possesses considerable expertise in the manufacture of sponge iron. ... The production process also ensures that the sponge is free from dust caused during ...
اقرأ أكثر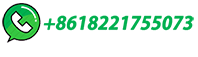
Sponge Iron
The process of sponge iron manufacturing involves removal of oxygen from iron ore. When that happens, the departing oxygen causes micro pores in the ore body, turning it porous. ... Some of the inherent advantages of using Sponge Iron in comparison to Scrap are as under : More Volumetric Weight : Considerably higher (10-) than other types ...
اقرأ أكثر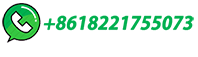
DRI (Sponge Iron) | Metallics | IBMD | Tata Steel
DRI (Direct Reduced iron), commonly known as Sponge Iron, is a metallic product produced through the direct reduction of iron ore (in the form of lumps, pellets, or fines) in the solid state. It is a substitute for scrap and therefore is mostly applicable in making steel through the secondary route.
اقرأ أكثر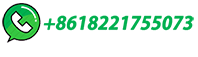
Iron Sponge Process
The advantages of the iron sponge process include: (1) providing complete removal of small to medium concentrations of hydrogen sulfide without removing carbon dioxide, (2) …
اقرأ أكثر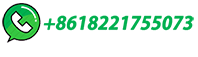
From Ore to Iron with Smelting and Direct Iron …
Smelting Reduction. Figure 2: The smelt reduction vessel (SRV) is the core technology component of the Hismelt process. Source: RioTinto While years of ironmaking technology innovations have …
اقرأ أكثر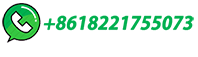
Powder production technologies
The sponge iron process. The longest established of these processes is the sponge iron process, the leading example of a family of processes involving solid state reduction of an oxide. In the process, selected magnetite (Fe3O4) ore is mixed with coke and lime and placed in a silicon carbide retort.
اقرأ أكثر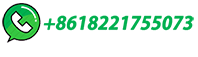
Low-Carbon Production of Iron & Steel: Technology …
These processes operate with different feedstocks. The BF-BOF pathway converts raw iron ore to pig iron and then to steel HM – while EAF converts both steel scrap and sponge iron to steel HM. DRI converts raw iron ore to sponge iron, a porous, permeable, and highly reactive product that requires treatment with EAF before selling to …
اقرأ أكثر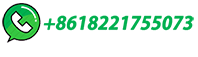
LECTURE NOTES ON Sponge Iron & Ferro Alloys
The main reasons for rapid growth of DR process are –. Worldwide shortage of metallurgical coal to operate B.F. Huge financial resources required for B.F route of iron …
اقرأ أكثر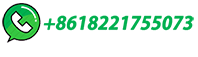
The Application and Benefits of Sponge Iron
Applications Of Sponge Iron. Sponge iron has a wide number of applications. Here are some of the significant ones: Sponge iron is a standout amongst the most imperative and the fundamental raw materials required for the generation of different steel/iron based items like TMT bars, D.I Pipes and so forth. Sponge Iron is a part– …
اقرأ أكثر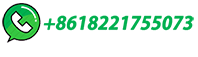
Mathematical Modelling of Sponge Iron Production in a …
VOL. 5 NO. 1 OCTOBER, 2010 STEEL TECH 11 from an industrial coal-based sponge iron rotary kiln process. We have developed a fairly comprehensive mathematical model for the direct reduction of iron ore
اقرأ أكثر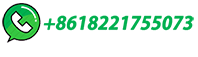
Sponge Iron
Sponge iron adopts direct reduction ironmaking method to obtain iron with sponge-like pores inside. Sponge iron is produced by low-temperature reduction of iron …
اقرأ أكثر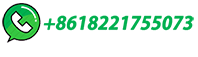
All About The Production Of Sponge Iron
Let's delve more into understanding one of the crucial by-products of Iron – Sponge Iron. Sponge Iron gets its name from its unique physical characteristics. It has hole marks on its surface. These hole marks emerge during the 'natural reduction' process where iron ore is warmed with carbon.
اقرأ أكثر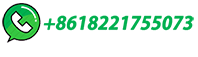
Sponge Iron
Sponge iron offers several benefits as a raw material in steel production. ... Ultimately, the decision hinges on factors like purity, production process, and intended use, with sponge iron excelling in certain modern steelmaking processes, while pig iron remains crucial for traditional 3. What are the benefits of using in-house sponge iron in ...
اقرأ أكثر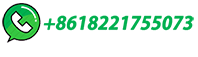
(PDF) i) Direct Reduced Iron: Production
During the last four decades, a new route of ironmaking has rapidly developed for direct reduction (DR) of iron ore to metallic iron by using noncoking coal/natural gas.
اقرأ أكثر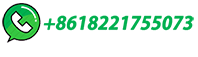
Sponge Iron
Sponge iron means porous iron produced by direct reduction process.Direct reduction (DR) process is a solid-state reaction process (i.e. solid–solid or solid–gas reaction) by which removable oxygen is removed from the iron ore, using coal or reformed natural gas as reductants, below the melting and fusion point of the lump ore or …
اقرأ أكثر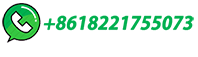
WHAT IS SPONGE IRON AND HOW IS IT MADE?
Sponge iron, also called direct reduced iron (DRI), is made from directly changing iron ore (in any form whatsoever) to iron by a cutback gas or carbon, produced from natural gas or coal. ... The process includes …
اقرأ أكثر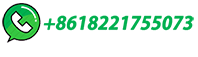
Direct Reduced Iron Industry in India — Problems and …
`the quality requirements for the rotary kiln sponge iron process. The sponge iron fines generation is high and ranges from 15 — 30% depending upon the ore used due to high reduction degradation. This will not only reduce the sales realization of the product but also will lead to accretion formation in the kiln shortening the campaign life.
اقرأ أكثر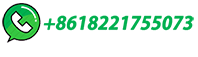
Direct reduced iron process
In the electric steel process, the sponge iron obtained from the direct reduced iron process is used for crude steel making. In general, scrap is also added to this process as well as pig iron from the …
اقرأ أكثر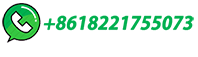
(PDF) i) Direct Reduced Iron: Production
In book: Encyclopedia of Iron, Steel, and Their Alloys (pp.pp 1082-1108) Chapter: i) Direct Reduced Iron: Production; Publisher: CRC Press, Taylor and Francis Group, New York.
اقرأ أكثر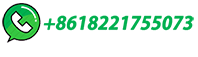