A comparative analysis of steel and alumina balls in fine …
This study explored the breakage kinetics of cement clinker in a lab-scale ball mill loaded with steel or alumina balls of 20, 30, and 40 mm sizes and their mixtures. ... Unfortunately, only the electric current data of the mills were reported; detailed operation conditions such as ball size, BSD, feed size, and most importantly, the …
اقرأ أكثر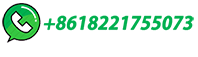
Ball Mill Grinding Machines: Working Principle, Types, Parts
Cement Industry: Ball mills are extensively used in the cement industry for grinding raw materials, clinker, and additives to produce cement. ... The integration of digitalization and automation technologies has revolutionized ball mill operations. Real-time monitoring, data analysis, and remote control capabilities allow for optimized ...
اقرأ أكثر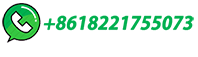
Process Training Ball Mill
BALL MILL OPERATION. Ball mills for finish grinding cement usually consist of two compartments. An intermediate diaphragm separates both compartments from each other. ... As high or varying temperature of the new feed material (generally the clinker) has a negative effect on the grinding process (poor cement setting, decrease of performance ...
اقرأ أكثر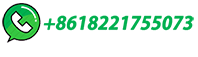
Process Training Ball Mill
The better mills on the market have an efficiency of about 8-9 % which means that only 8-9 % of the energy results in grinding and the majority is converted mainly into heat. The ball mill has the worst efficiency of all …
اقرأ أكثر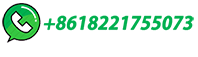
Cement Clinker Grinding Plant | Roller Press & Ball Mill
Ball mill & roller press combined cement grinding solution. Capacity: 700 ~ 5,000 TPD Main Grinding Equipment: roller press, ball mill Material: limestone, calcite, talc and dolomite Working Process: cement combined grinding system Solution: EPC service providing including design, procurement, construction, and trial operation
اقرأ أكثر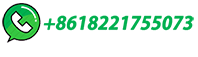
Everything you need to know about clinker/cement Grinding
OPTIMIZATION OF CEMENT GRINDING OPERATION IN …
WEBncrease.Optimization of the Cement Ball Mill OperationOptimization addresse. the grinding process, maintenance and product quality. The objective is to achieve a more efficient …
اقرأ أكثر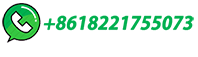
The effects of grinding media shapes on the grinding kinetics …
To investigate the effects of grinding media shapes on the grinding kinetics of ball mill cement clinker, the grinding effects with ϕ20 mm balls and ϕ20 × 20 mm cylinders on six different size ...
اقرأ أكثر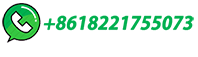
a) Cement ball mill view, b) Cement mill sketch.
Nowadays, ball mills are widely used in cement plants to grind clinker and gypsum to produce cement. The research focuses on the mill speed as well as air classifier speed effect on the two ...
اقرأ أكثر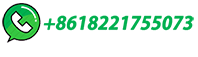
sbm ball mill operation clinker customer case.md
Write better code with AI Code review. Manage code changes
اقرأ أكثر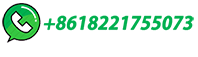
BALL MILLS Ball mill optimisation
in combination with a ball mill for cement grinding applications and as finished product grinding units, as well as raw ingredient grinding equipment in mineral applications. This paper will focus on the ball mill grinding process, its tools and optimisation possibilities (see Figure 1). The ball mill comminution process has a high electrical
اقرأ أكثر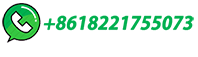
Calculation of the Parameters of the Grinding Load in a Ball-Tube Mill
To calculate the parameters of grinding load operation in mills with cross-longitudinal motion of grinding bodies it is not possible to use the classical theory of Davis assuming that the ball in the crushing cylinder first moves in its cross section along a circular path together with the crushing cylinder, and then at the breakaway point it …
اقرأ أكثر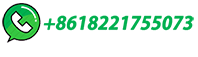
Easy Operation New Products Clinker Ball Mill for Sale
Type: Ball Mill Motor Type: AC Motor Motor Power: 18.5KW Rotationl Speed: 23-25r/min Application: Mine Materials: Stone and Ore
اقرأ أكثر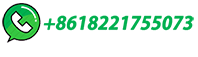
Experimental study of clinker grinding in a ball mill and …
this paper, the method was used to study the collisions between grinding media and grinding media and walls in ball mills, which is the most used unit operation in clinker …
اقرأ أكثر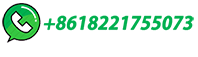
BALL MILLS Ball mill optimisation
to optimise the grinding process.Clinker grain sizes depend on pre-crusher settings but are in some cases still up to 50mm when fed to the ball mill and therefore, it is necessary to …
اقرأ أكثر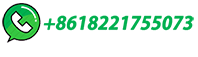
Clinker grinding technology in cement manufacturing
Clinker grinding technology is the most energy-intensive process in cement manufacturing. Traditionally, it was treated as "low on technology" and "high on energy" as grinding circuits use more than 60 per cent of total energy consumed and account for most of the manufacturing cost. ... + Lower SEEC in compare with ball mill + Stable …
اقرأ أكثر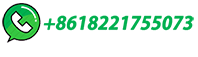
Cement Ball Mill
What is the cement ball mill? The cement ball mill is mainly used for grinding the finished products and raw materials of cement plants, and is also suitable for grinding various ore and other grindable materials in industrial and mining enterprises such as metallurgy, chemical industry, and electric power. Cement grinding is the last process …
اقرأ أكثر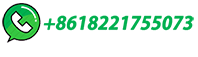
Computation of charging media for a double compartment cement ball mill
The air blown through the mill system helps to sustain material flow while drawing heat produced during the grinding operation. In a ball mill, the internal volume of the grinding compartment is typically 25–45 % of ... The effects of grinding media shapes on the grinding kinetics of cement clinker in ball mill. Powder Technol., 235 (2013 ...
اقرأ أكثر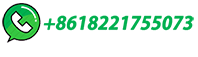
Energy and exergy analyses for a cement ball mill of a new …
Nowadays, ball mills are used widely in cement plants to grind clinker and gypsum to produce cement. In this work, the energy and exergy analyses of a cement ball mill (CBM) were performed and ...
اقرأ أكثر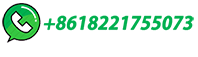
The Cement Plant Operations Handbook
The Cement Plant Operations Handbook is a concise, ... Clinker – 11. Finish mill – 12. Cement – 13. Quality control – 14. Packing and distribution – 15. Emission abatement (dust, NO x, SO 2, etc) – 16. Maintenance – 17. ... ball mills, vertical roller mills, roll presses, Horomill – in combination with separators and other ...
اقرأ أكثر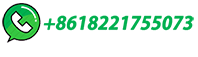
Use Cement Ball Mill Grinding Cement Clinker
Cement ball mill is a kind of cement grinding equipment commonly used in cement plants. It is mainly used for grinding materials in cement clinker section. Cement ball mill is widely used in cement production, silicate …
اقرأ أكثر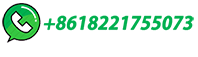
Optimization of Cement Grinding Operation in Ball Mills
The consumption of energy by the cement grinding operation amounts to one third of the total electrical energy used for the production of cement. The optimization of this …
اقرأ أكثر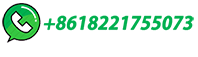
Design and Optimization of Ball Mill for Clinker …
schemes to reduce power consumption in ball mill operation. Experiment: The laboratory ball mill has length 50 cm and diameter 30 cm. Grinding media are ceramic and steel balls of 10 mm, 15 mm, 20 mm and 25 mm diameter and density from 4.5 to 7.8 g/cm3. The mill rotates at different speeds for grinding clinker, gypsum, fly ash and additives.
اقرأ أكثر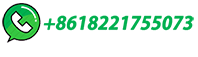
Analysis of the efficiency of the grinding process in closed …
Ball mills for fine grinding cement clinker and additives are widely used around the world. To improve the efficiency of a ball grinding the ball mills are transferred in closed circuit with air ...
اقرأ أكثر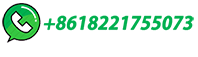
Design and Optimization of Ball Mill for Clinker Grinding …
schemes to reduce power consumption in ball mill operation. Experiment: The laboratory ball mill has length 50 cm and diameter 30 cm. Grinding media are ceramic and steel …
اقرأ أكثر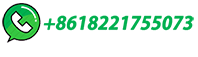
Breakthrough in Clinker Grinding
Finish grinding of clinker and other cement ingredients reduces 25 mm clinker balls to particle sizes optimally ranging from 3 to 30 microns. The European …
اقرأ أكثر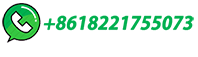
Modeling of closed-circuit ball milling of cement clinker via …
Fig. 1 shows the process flow of a closed-circuit, two-compartment cement ball mill. The closed-circuit operation helped to reduce overmilling of particles [10], resulting in lower specific power consumption [11] in comparison with open-circuit operation, where the ball mill is operated without the external air classifier.
اقرأ أكثر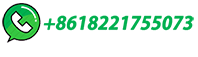
Simulation of clinker grinding circuits of cement plant based …
It increased nearly 10.5% and 15.8% in fresh feed capacity input to each tube ball mill. In addition, circulating load ratios of circuits are modified to 118% and 127% from low level of 57% and 22%, respectively, and also cut points of air separators are adjusted at 30 and 40 μm from high range of 53 and 97 μm, respectively. ...
اقرأ أكثر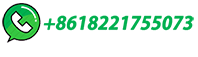
An Introduction to Clinker Grinding and Cement Storage
There is no doubt that vertical roller mills offer significant advantages over ball mills in terms of their energy efficiency. The specific energy consumption of a ball mill is greater than that of a vertical mill (VRM) that performs the same operations by a factor of between 1.5 and 2, depending on the degree of optimization of the ball mill.
اقرأ أكثر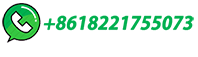
Clinker Grinding Techniques in Cement Manufacturing
Tube Mills: Tube mills are similar to ball mills but have a longer horizontal cylinder for grinding clinker. They are used less frequently than other grinding equipment in the cement industry. Air-Swept Mills: Air-swept mills use air to transport the clinker and grind it within a closed circuit. These mills are energy-efficient and can produce ...
اقرأ أكثر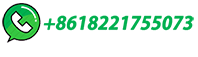
Grinding
Milling and crushing operations pose a number of headaches to cement plant operations. They consume large amounts of electrical energy. They are subject to severe abrasion. And their performance effects things well beyond the grinding plant, impacting the efficiency of the entire process, not to mention final product quality. A poorly designed or functioning …
اقرأ أكثر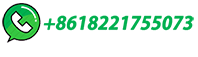