Iron ore crushing equipment and process flow
Iron ore crusher is a kind of mechanical equipment that crushes iron ore raw ore step by step, from large pieces of raw iron ore (about 500mm) to millimeter …
اقرأ أكثر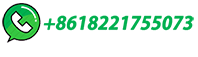
Calculate and Select Ball Mill Ball Size for Optimum Grinding
In Grinding, selecting (calculate) the correct or optimum ball size that allows for the best and optimum/ideal or target grind size to be achieved by your ball mill is an important thing for a Mineral Processing Engineer AKA Metallurgist to do. Often, the ball used in ball mills is oversize "just in case". Well, this safety factor ... title="Calculate …
اقرأ أكثر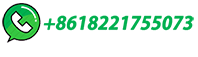
Energy conservation and consumption reduction in grinding …
1. Introduction. Grinding operation is the last preparation stage before beneficiation. In this stage, the material undergoes the combined action of impact and grinding, so that the ore particle size is diminished and the qualified materials is provided for succeeding beneficiation operations [1, 2].Generally, the quality of the grinding …
اقرأ أكثر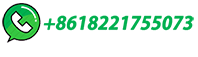
What is Powder Grinding Mill?
The powder grinding mill is the equipment used to grind and process materials such as ore. It can crush the materials into smaller particles, and then supply them to the production of other equipment or the use of various industries. ... Examples of processing materials include quartz, feldspar, barite, calcite carbonate, limestone, talc ...
اقرأ أكثر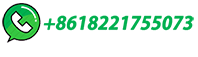
Friction and wear of liner and grinding ball in iron ore ball mill
To understand the friction and wear of working mediums in iron ore ball mills, experiments were conducted using the ball cratering method under dry and wet milling conditions, which mimic the ...
اقرأ أكثر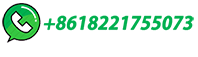
Development of a Novel Grinding Process to Iron Ore …
Based on batch grinding method and normalization idea, a conical ball mill is used and a quantitative separation method of grinding characteristics of multi-component complex ore is proposed.
اقرأ أكثر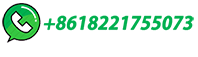
An innovative approach for determining the grinding …
The installed powder of ball mill ... and material ball ratio had a significant influence on the grinding kinetics of the iron ore sample. (2) The average grinding rate increased with a decrease in media size. Therefore, the optimal media size for −2 + 0.45 mm raw material was 40 mm, and the optimal media size for −0.45 + 0.15 mm and − 0. ...
اقرأ أكثر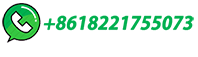
Iron Ore Processing: From Extraction to Manufacturing
Grinding Mills: Grinding mills, such as ball mills and rod mills, are commonly used for grinding iron ore. These mills contain grinding media (steel balls or rods) that tumble and impact the ore, causing it to break into smaller particles. The choice of grinding mill depends on factors such as the desired product size, capacity …
اقرأ أكثر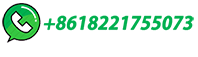
Iron Ore Pelletization
This process varies depending on the ore source, but typically involves various stages of crushing and grinding to reduce the size of the iron ore. Separation techniques such as magnetic separation or froth flotation are then used to separate the gangue materials from the iron content.
اقرأ أكثر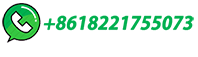
Investigation on Iron Ore Grinding based on Particle Size Distribution
The feed samples of X, Y, and Z iron ores were ground in the BBM (ball mill refers to a BBM of size 300 mm × 300 mm with smooth liners) to identify the PSD, BWI, and RT of each ore. Grinding experiments were conducted according to Bond's standard test procedure [].For each iron ore sample, the RT taken to produce 250% circulating …
اقرأ أكثر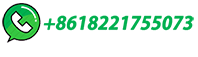
Experimental investigation of the impact breakage …
The effect of particle size, impact energy, and impact number on the iron ore particle impact breakage characteristics were analyzed to reveal the particle breakage behavior in the ball mill. This work provides the methods to quantify the breakage characteristics and provides the theoretical basis to improve the milling efficiency.
اقرأ أكثر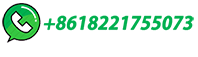
Friction and wear of liner and grinding ball in iron ore ball mill …
To understand the friction and wear of working mediums in iron ore ball mills, experiments were conducted using the ball cratering method under dry and wet milling conditions, which mimic the operating conditions in ball mills. The liner sample is made of Mn16 steel, the ball had a diameter of 25 mm and was made of GCr15 steel, …
اقرأ أكثر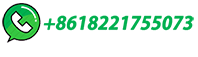
Iron Ore Processing: From Extraction to Manufacturing
Grinding Mills: Grinding mills, such as ball mills and rod mills, are commonly used for grinding iron ore. These mills contain grinding media (steel balls or …
اقرأ أكثر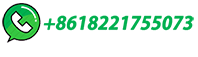
Raymond mill in iron ore for ultrafine powder making
Crushing: Raymond mill can be used as primary crusher to reduce the size of raw iron ore chunks into smaller pieces. Grinding: After crushing, the iron ore is further ground into ultrafine powder using a Raymond mill. The fineness of the powder can be adjusted by controlling the mill's speed and grinding media. Classification: The ultrafine ...
اقرأ أكثر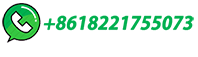
The six main steps of iron ore processing
The primary grinding mill grinds the material before it undergoes spiral gravity separation. Efficient grinding means that there will be minimal recirculation material from a cyclone …
اقرأ أكثر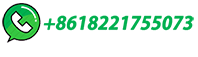
Impact of ball filling rate and stirrer tip speed on milling iron ore
The wet grinding of iron ore powder was investigated using a stirred media mill. In this study, the fitting degree of four cumulative undersize distribution functions was compared and the parameters of the four functions were discussed. ... In this study, the grinding system of the stirred mill was designed and manufactured by Shenyang Wu …
اقرأ أكثر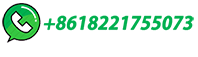
SBM Ore Ultrafine Grinding Mill
CLUM vertical mills are suitable for large-scale and high-volume non-metallic ore grinding production lines. The equipment is controlled intelligently, the work efficiency is high, and the ground powder has high whiteness and good shape.
اقرأ أكثر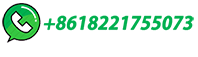
Iron ore grinding mill & Grinding plants for Iron Ore
Get Price And Support. Iron ore is an important industrial source, is an iron oxide ore, a mineral aggregate containing iron elements or iron compounds that can be economically …
اقرأ أكثر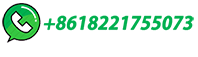
Mechanistic modeling and simulation of grinding iron ore …
The present work analyzes the application of the UFRJ mechanistic ball mill model to grinding of iron ore pellet feed in an industrial grinding circuit. ... and diameters (25–40 mm), besides powder fillings (0–). The parameter set chosen was such that allowed optimal correspondence between DEM simulations and experiments considering ...
اقرأ أكثر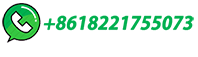
Mechanism of magnetite iron ore concentrate morphology …
The grinding method and its associated parameters strongly affect the physical properties of the iron ore concentrate. Ball milling (BM) and High-pressure grinding rolls (HPGR) are commonly employed for grinding iron ore concentrate [18], [19], [20]. In BM, the particle size was decreased by impact and attrition breakage, …
اقرأ أكثر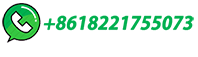
The six main steps of iron ore processing
This step involves breaking up the iron ore to obtain an F 80 grind size before it can be ground. Once the ore has been crushed, it is diverted to a stockpile. The aim of this step is to ensure a smooth crushing process and minimise downtime in the event of a breakdown or to allow planned maintenance in the crushing system, without stopping the ...
اقرأ أكثر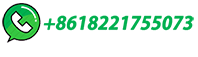
Energy conservation and consumption reduction in grinding …
Impact of ball filling rate and stirrer tip speed on milling iron ore by wet stirred mill: analysis and prediction of the particle size distribution ... Powder Technology, Volume 433, 2024, Article 119177. Jilai Ning, …, Wenbo Li. Experimental investigation of the impact breakage characteristics between grinding media and iron ore particle in ...
اقرأ أكثر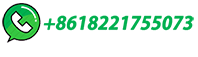
Investigation on Iron Ore Grinding based on …
The feed samples of X, Y, and Z iron ores were ground in the BBM (ball mill refers to a BBM of size 300 mm × 300 mm with smooth liners) to identify the PSD, BWI, and RT of each ore. Grinding …
اقرأ أكثر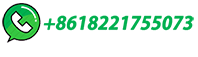
How to Dry, Grind and Granulate Your Bentonite Clay?
Grinding process is to produce grade wise powder form from activated bentonite or natural bentonite. Raymond mill is a popular bentonite grinding equipment. Learn more about bentonite Raymond mill. The particle size of bentonite powder can be adjusted within 80-425 mesh to ensure that the finished bentonite powder can serve …
اقرأ أكثر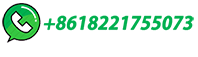
Mechanistic modeling and simulation of grinding iron ore …
DOI: 10.1016/J.POWTEC.2021.07.030 Corpus ID: 237666917; Mechanistic modeling and simulation of grinding iron ore pellet feed in pilot and industrial-scale ball mills @article{Carvalho2021MechanisticMA, title={Mechanistic modeling and simulation of grinding iron ore pellet feed in pilot and industrial-scale ball mills}, author={Rodrigo M …
اقرأ أكثر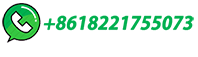
Iron ore crushing and screening process
Iron ore is gradually selected through the procedures of crushing, screening, grinding, classification, magnetic separation, flotation, gravity separation, roasting …
اقرأ أكثر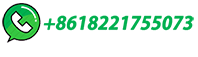
High Pressure Grinding Roll and Magnetic Separation for …
This paper presents an industrial verification test, adding a high pressure grinding roll and magnetic separation operation after the third-stage fine crushing operation to reduce the particle size of ball mill feed and improve the processing capacity of grinding operation. The optimal process parameters of high pressure grinding roll and magnetic …
اقرأ أكثر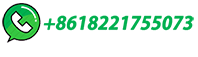
Impact of ball filling rate and stirrer tip speed on milling iron ore
The wet grinding of iron ore powder was investigated using a stirred media mill. In this study, the fitting degree of four cumulative undersize distribution functions was compared and the parameters of the four functions were discussed. ... In this study, three laboratory-type grinding mills, including a ball mill, a vertical stirred mill and a ...
اقرأ أكثر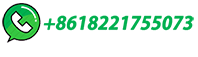
Estimation of Grinding Time for Desired Particle Size …
The grinding process for all the three iron ores is carried out individually in Bond's ball mill and the total retention time taken by each iron ore sample is calculated. The present investigation focuses on utilizing the calculated retention time of the iron ore as a standard grinding reference time to the laboratory ball mill for optimizing ...
اقرأ أكثر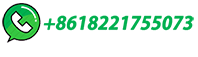
A critical review on the mechanisms of chemical additives …
1. Introduction. The term chemical additives or grinding aids (GAs) refers to any substance which results in increased grinding efficiency and reduction in power consumption when added to the mill charge (amounts not exceeding 0.25 wt.% of the feed) during grinding [1], [2], [3].The use of grinding aids to increase mill throughput is quite …
اقرأ أكثر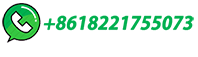