Primary and Secondary Crushing: Understanding the Basics
The primary crusher receives the materials directly from the mine or quarry, and its size reduction ratio ranges from 3:1 to 7:1. The primary crusher can be a jaw crusher, gyratory crusher, or impact crusher, depending on the hardness, abrasiveness, and size of the materials. The jaw crusher is the most common type of …
اقرأ أكثر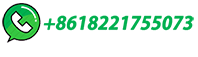
How does a stone crusher work?
Working Principle: Uses both compressive and shear forces. Stones are crushed between a rotating spindle and a concave hopper. Use Cases: Ideal for secondary and tertiary crushing stages. Impact Crusher: …
اقرأ أكثر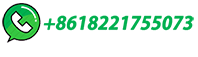
AMIT 135: Lesson 5 Crushing – Mining Mill Operator Training
The ratio of reduction through a primary crusher can be up to about 8:1. Feed: ROM up to 1.5 m; Product: -300mm (for transport) to -200mm (for SAG mill) Feed Rate: 160 to 13,000 tph; The family of primary crushers include: Gyratory Crushers Jaw Crushers Impact Crushers; Typical rules for primary crusher selection:
اقرأ أكثر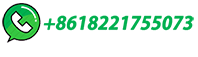
A Guide to Types of Jaw Crushers for Crushing Rocks and Minerals …
A gyratory crusher is a type of crusher that uses a mantle to guide the crushing process. The mantle is suspended on an eccentrically rotating shaft, which causes the mantle to gyrate. The gyratory crusher has a higher capacity than a jaw crusher. It is often used for primary crushing in the stone crushing industry.
اقرأ أكثر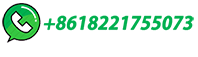
Large Capacity Gyratory Crushers for Primary Crushing
Gyratory crushers are large primary crushers designed for high capacity and large feed sizes. Gyratory crushers are large primary crushers designed for high capacity and large feed sizes. ... Applicable Materials: Most rocks, metal ores, granite, marble, basalt, and other minerals. Model: HCG4265. Max. Feed Size: 900 mm. Capacity: 2,018–2,878 ...
اقرأ أكثر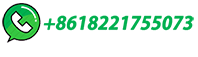
Primary Crushers
Primary crushers are suitable for the primary crushing or grinding of clay and minerals coming directly from quarries and for reducing its original irregular size to uniform sizes below 80mm so that the material may be properly batched and stored. Verdés crushers are specially designed to accept non-ferrous minerals that contain moisture ...
اقرأ أكثر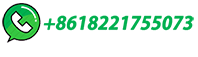
Gyratory Crusher
The majority of gyratory crushers are used as primaries, i.e. they receive the initial feed from the mine or quarry. The same type of crusher with chamber modifications is used as a secondary crusher, particularly when following a large primary crusher. The fine-reduction gyratory crusher can also be used for tertiary crushing.
اقرأ أكثر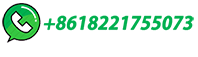
How Does a Jaw Crusher Work? A Simple Guide
To refine the size of the materials from the primary crushing stage. Cone Crusher, Impact Crusher: Usually between 125 mm and 150 mm: Further reduced to 20 mm to 40 mm. The material from the primary crusher is fed into secondary crushers for a more uniform and finer size. Tertiary Crushing: To obtain even finer material suitable for …
اقرأ أكثر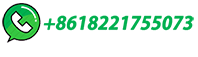
Choosing the right primary crusher for your aggregate …
All components at a crushing site depend on the primary crusher functioning properly, which is why choosing the right crusher for the job is critical. Defining the intended purpose of your primary crusher. The first step in choosing a primary crusher takes place at a high level. It's necessary to identify the purpose the crusher will be used for.
اقرأ أكثر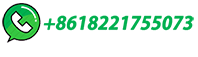
Willpactor® Primary Impact Crusher | Williams …
The Williams Willpactor® primary impact crusher can be utilized for a variety of applications such as concrete or cement crushing, or for reducing run-of-mine quarry rock, limestone, asphalt, anode butts, and various …
اقرأ أكثر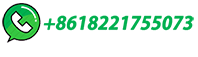
Primary Crushing
Primary crushing brings run-of-mine ore down to a maximum size of the order 4″ to 6″ in average diameter; secondary crushing receives feed at −6″ and reduces it to below "Dry" …
اقرأ أكثر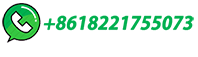
Primary and Secondary Crushing: Understanding …
Primary crushing is the first stage of crushing that takes place at the mine or quarry. The primary crusher is the equipment that reduces the size of the materials to the size that can be processed by …
اقرأ أكثر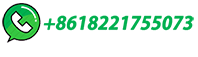
Primary Crusher Selection & Design
How you select your primary crusher will be based on factors like moisture content, maximum rock lump size, material density SG, abrasion index, degradability and it being prone to dusting or not. The crusher capacities given by manufacturers are typically in tons of 2,000 lbs. and are based on crushing limestone weighing loose about 2,700 …
اقرأ أكثر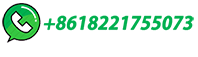
Jaw Crusher
Jaw crusher is one of the most commonly used primary crushers in the ore processing plant, with a capacity range of 1-1000tph. There are two types of feeding opening designs, rectangular and square shape. JXSC …
اقرأ أكثر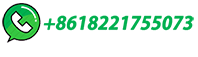
AMIT 135: Lesson 5 Crushing – Mining Mill …
The purpose of the primary crusher is to reduce the ROM ore to a size amenable for feeding the secondary crusher or the SAG mill grinding circuit. The ratio of reduction through a primary crusher can be up to …
اقرأ أكثر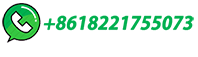
Primary Crusher
The primary crusher is located in the quarry and consists of a McLanahan 48″x72′ Shale King Crusher rated at 1,000 TPH (Tons Per Hour). The driving flywheel has a diameter of 2.5 meters and is motor driven through six v-belts. ... Gyratory and Cone Crusher. In Mineral Processing Design and Operations (Second Edition), 2016. 5.1 Introduction.
اقرأ أكثر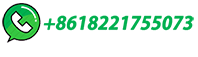
What Is Primary, Secondary, and Tertiary Crushing
Primary crushing is the first stage of material reduction and can sometimes be the only stage needed to generate the desired product for a job. Depending on the setup, primary crushing will take the larger material that has been blasted, excavated, or reclaimed and process it through an impactor, jaw, or gyratory crusher to generate a …
اقرأ أكثر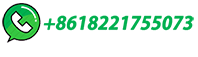
Primary Crusher vs. Secondary Crusher: …
The primary crusher is used to reduce the size of large rocks and stones, while the secondary crusher further breaks them down into smaller pieces. In this article, we will discuss the primary crusher …
اقرأ أكثر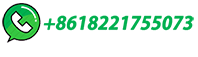
Primary Cone Crusher Construction Waste Crusher is important mineral
Primary Cone Crusher Construction Waste Crusher is important mineral crushing equipment, and plays a huge role in fine strong crushers machine crushin
اقرأ أكثر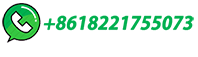
Mining crushers SuperiorTM MKIII Primary Gyratory
Minerals processing is changing. With diminishing ore grades and rising energy costs, ensuring that a plant has the lowest total cost of ownership is vital. More sustainable technologies & practices are ... Primary gyratory crushers are the initial driving force for the entire mineral processing circuit. Outotec's
اقرأ أكثر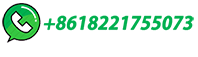
Aggregate Crushers, for Rock, Ore & Minerals
Jaw Crushers are for primary size reduction of hard rock, ores, and minerals and are available in several different Bico and Heavy-Duty Morse models. Bico Chipmunk crushers are equipped with reversible plates that extend plate life, and the Badger model has a higher crushing capacity. Morse crushers are heavy-duty and designed for high ...
اقرأ أكثر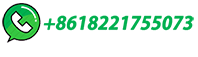
Compare Gyratory Crusher vs Jaw Crusher
To accomplish this reduction in size takes several steps or stages of crushing and grinding. Primary crushing is the first of these stages. Generally speaking there are two types of primary crushers, lets compare them: GYRATORY CRUSHER or a JAW CRUSHER. Although they don't look anything like they do have similarities that put them …
اقرأ أكثر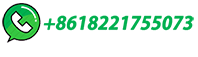
Trends in the crusher market and operational challenges
The workhorse for primary crushing here are jaw crushers (Fig. 9). If the material hardness of the materials is below 5 Mohs, horizontal-shaft impact crushers (Fig. 10) and hammer crushers can be used directly as primary crushers in these applications as these machines achieve high size reduction ratios in the range from 8 to 40.
اقرأ أكثر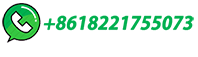
how a stone crusher operates
1. Types of Stone Crushers. Before diving into operational details, it's essential to differentiate the types of stone crushers: Jaw Crushers: Utilized primarily as primary crushers, these machines feature a pair of vertical jaws; one is stationary, and the other moves to create a V-shaped cavity.
اقرأ أكثر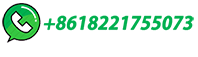
Crushing in Mineral Processing
Crushing in Mineral Processing. / crusher plant. The modern industrial use of aggregates began in the early 19th century, and the aggregate can be defined as particles of rock that, …
اقرأ أكثر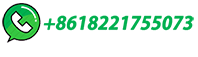
(PDF) Influence of jaw crusher parameters on the quality of primary …
Minerals, Lokomonkatu 3, 33100 Tampere, Finland. ARTICLE INFO. Keywords: Construction aggregates. Jaw crusher. ... with jaw crushers in the primary crushing stage, to gain knowledge.
اقرأ أكثر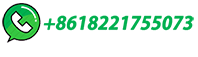
Primary Crushing: A Comprehensive Guide
Before we start primary crushing, the first stage of material reduction, we often need to get them from mines or rock quarries. This is typically accomplished by blowing objects up or digging. This raw material can be big and oddly shaped. It is then moved to the primary crusher. This is usually done by large trucks or a conveyor belt.
اقرأ أكثر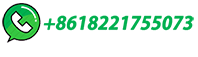
® CT Series Jaw Crushers |
The ® CT Series jaw crusher is frequently used in mining to process precious metals and a wide spectrum of other minerals. It is also used to process hard rock, sand, concrete, asphalt and slag within the aggregates industry. ... The ® CT Series jaw crusher is designed for tough primary crushing applications where large feed materials ...
اقرأ أكثر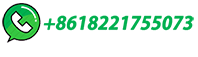
Jaw Crusher
Crushers. Barry A. Wills, James A. Finch FRSC, FCIM, P.Eng., in Wills' Mineral Processing Technology (Eighth Edition), 2016 Jaw-crusher Construction. Jaw crushers are heavy-duty machines and hence must be robustly constructed. The main frame is often made from cast iron or steel, connected with tie-bolts. It is commonly made in sections …
اقرأ أكثر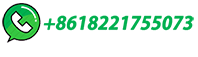
what is a primary and secondary crusher?
Primary crushers and secondary crushers are used in the mining and quarrying industry to crush rocks and aggregate, respectively. A primary crusher is a heavy-duty machinery used to reduce the ...
اقرأ أكثر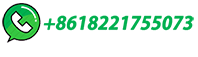