Crusher Operating Costs: How to Optimize and Reduce
Spending a little extra on drilling and blasting to increase fragmentation will same you multiples ore loading and hauling, then finally crushing. The Experts: Mining + and Quarry Academy = all agree. The approximate running costs for crushing plants of different capacities up to 4,000 tons per day on the basis of an eight …
اقرأ أكثر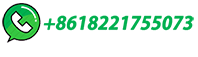
NGT earmarks 200 metre as minimum distance between stone quarries
NEW DELHI: The National Green Tribunal Wednesday earmarked 200 metre as the minimum distance to be maintained between stone quarries and residential or public structures across the country. A bench headed by NGT Chairperson Justice Adarsh Kumar Goel held that the stone quarries should maintain a minimum distance of 100 …
اقرأ أكثر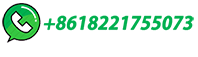
Rock Boulder Crushers
The crusher employed for the initial size reduction will have a maximum size rock capacity, and when any oversized rock is delivered, it lodges in the crusher and the materials flow in the mine or quarry is halted. ... are a set of parallel bars set apart from each other a distance which permits passage of only the maximum size rock that can be ...
اقرأ أكثر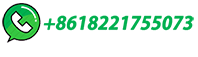
What is a Crusher?
A primary crusher breaks up large pieces of rock or concrete from the blasting or excavation process and turns them into smaller, more manageable chunks. Primary crushing produces materials ranging from 50" to 20" on average. The two main types of primary crushers are the jaw and gyratory crushers. Jaw crushers
اقرأ أكثر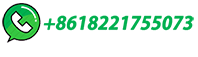
Varistem
The Varistem stemming plug for blasting is used in mining, quarrying and civil applications. ... 80% Reduction in flyrock distance Varistem helped a coal mine minimise fyrock, noise and airblast, leading to improved retention of blast energy. ... showing Varistem's effectiveness. 14%+ Crusher throughput Varistem plugs improved fragmentation ...
اقرأ أكثر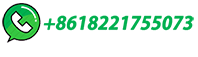
SAND, GRAVEL, AND CRUSHED STONE ON-THE-JOB …
and blasting duties. POTENTIAL ACCIDENTS OR HAZARDS 2. A) Personnel entering unsafe area. B) Struck by falling material. Ground failure under weight of equipment or persons. C) Fall over highwall or bank. 3. A) Overturning drilling equipment. B) Ground failure under weight of drilling equipment. RECOMMENDED SAFE JOB PROCEDURES 2.
اقرأ أكثر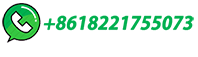
Mine-to-crusher policy: Planning of mine blasting patterns …
Mine-to-crusher policy: Planning of mine blasting patterns for environmentally friendly and optimum fragmentation using Monte Carlo simulation-based multi-objective grey wolf optimization approach. ... Application of artificial intelligence techniques for predicting the flyrock distance caused by blasting operation. Arabian J. …
اقرأ أكثر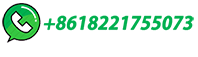
Crushing Plant Design and Layout Considerations
There are three main steps in designing a good crushing plant: process design, equipment selection, and layout. The first two are dictated by production requirements and design …
اقرأ أكثر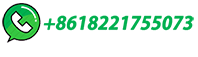
Crusher Distance Sonic Knit sneakers | EMPORIO ARMANI …
Shop EMPORIO ARMANI Crusher Distance Sonic Knit sneakers for Unisex at the official store and browse the Sneakers collection.
اقرأ أكثر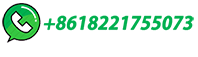
What is a Primary Crusher?
Primary jaw crusher and secondary impact crusher working together in a plant set-up. The most common primary crusher is a jaw crusher, but, there are many other types including gyratory and cone crushers. We will talk about them all in more detail later! A jaw crusher is made up of two big plates that are held in a V-shape.
اقرأ أكثر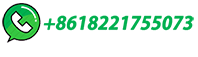
Enhancing rock fragmentation assessment in mine blasting …
The optimization of blasting operations greatly benefits from the prediction of rock fragmentation. The main factors that affect fragmentation are rock mass characteristics, blast geometry, and explosive properties. This paper is a step towards the implementation of machine learning and deep learning algorithms for predicting the …
اقرأ أكثر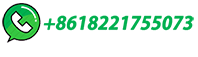
Types of Crushers: What You Need to Know
A roller crusher reduces material by compressing it between two turning cylinders, parallel to each other. The cylinders are mounted horizontally with one resting on strong springs and the other framed permanently. Material is then fed between the two. Changing the distance between the rollers allows you to control the desired material output size.
اقرأ أكثر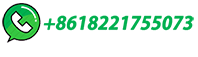
P&Q University Lesson 7: Crushing & Secondary Breaking
On these mobile impact crushers, the zero point is the distance between the ledges of the rotor and the impact plates of the lower impact toggle, plus a defined safety distance. The desired crushing gap is approached from this zero point.
اقرأ أكثر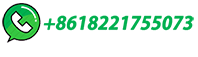
2020g
crusher. Due to the absence of the ROM stockpile, it is necessary to fragment the ore by drilling and blasting to maximise crusher throughput and minimise crusher blockages. To enable the annual material movement target of 150 million tonne (165 million ton), large rotary drills drill large diameter holes.
اقرأ أكثر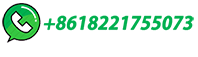
The Effects of Blasting on Crushing and Grinding …
The size of fragments is the "seen" part of blasting results. It is very important in crushing as it effects production and downtime. Overly coarse fragmentation will reduce primary crusher throughput. Coarse material will lead to more downtime for clearing crusher bridging and plugging.
اقرأ أكثر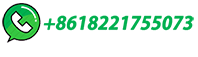
Evaluation of blast efficiency in aggregate quarries: facts and
Evaluation of blast efficiency in quarrying of aggregate stones is one of the most important decisions that should be made by quarry operators for productivity …
اقرأ أكثر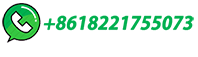
(PDF) PM10 Concentration Emitted from Blasting and
During crushing at mine A, the PM10 concentration with the range of 1.153-3.716 and 0.085-1.724 mg/m³ at crusher and piles in respectively were observed whereas the PM10 concentration measured at ...
اقرأ أكثر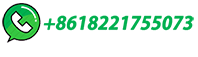
Optimization of Blasting-Associated Costs in Surface Mines …
Blasting outcomes have significant impacts on downstream mining operations such as loading, hauling, crushing, milling, and mineral processing. An ideal blasting plan can result in decrease in undesirable blast-induced impacts and in supplementary costs of downstream operations. This study developed a new …
اقرأ أكثر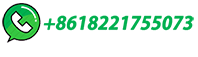
Blasting Near a Crusher
Blasting Near a Crusher, Blasting within 250 ft of a crusher was successfully executed through the application of electronic detonators, 3-D imagery, signature hole analysis, custom loading of blast holes. The blast was well contained, the vibrations were minimal, and there was no flyrock., Surface Blasting Problems and Solutions
اقرأ أكثر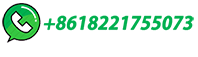
In Kerala, residents hit by quarrying demand safe distance …
The hearings will be followed by a scientific assessment of the issue based on which the committee will form conclusions. The NGT, through an order dated July 21, 2020 had approved the CPCB report ...
اقرأ أكثر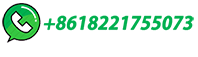
Primary and Secondary Crushing: Understanding the Basics
The secondary crusher has a size reduction ratio ranging from 3:1 to 5:1. The secondary crusher can be a cone crusher, impact crusher, or gyratory crusher, depending on the hardness, abrasiveness, and size of the materials. The cone crusher is the most common type of secondary crusher used in mining and quarrying operations.
اقرأ أكثر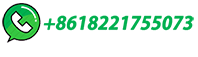
Dust emission from crushing of hard rock aggregates
The relationship between distance and emission load revealed that PM 10 concentrations below 100 μg/m 3 were achieved at approximately 750 m away from emission sources in the present study. Crusher's operations with existing emissions of 23.43 g/day/m 2 were detrimental for the region's AC and needed to be stepped down to …
اقرأ أكثر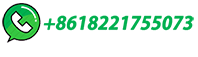
MPCB Home Page | Maharashtra Pollution Control Board
When Blasting is involved Minimum Distance 100 m 200 B Railwa Lines/Area, Page 1 of 4 . Ropeway or Ropeway trestle or station, Bridges, Dams, Reservoirs, River, Canals or Lakes or Tanks, or any other locations to be considered by States.
اقرأ أكثر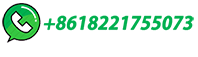
Blasting Impact on Environment and their Control Measure …
Both the magnitude of ground vibration and air pressure were well within the safe limit, however the level of sound generated(120.599 Lp(dB) ) from Blast No. 5 near the Old crusher, located at a ...
اقرأ أكثر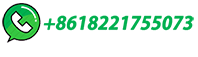
Evaluation of blast efficiency in aggregate quarries: facts and
The goal of quarry operators is to produce a run-of-mine (ROM) that does not choke the crusher and cause delays in production. In order to achieve this goal, proportions of the fines and coarse fragments must be optimized through effective planning of blasting for the overall success of quarrying and mining operations. ... Azizi A, …
اقرأ أكثر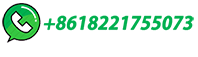
202 The Chemical Crusher: Drilling and Blasting
Chemical Crusher Fully portable and built at the rock bench. Disposable and fully consumed on use. Except for the diesel and/or electricity to build it, it is internally powered. Has design flexibility to meet variable production volumes, changing rock conditions and to produce different rock size gradations. Could be assembled daily if necessary.
اقرأ أكثر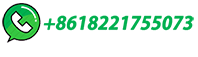
Advanced Certificate In Drilling And Blasting
Advanced Certificate in Drilling And Blasting COURSE DESCRIPTIONThis program is run by the mining department and is designed to help students develop an understanding, of various drilling methods, understand their relationship to geology, and their application in the field. It aims to equip drilling and blasting practitioners, engineers, supervisors, …
اقرأ أكثر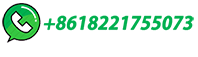
Rock-breaking mechanism and experimental analysis of confined blasting
Results of confined blasting experiment showed that the damage of surrounding rock in confined blasting condition exhibits similar damage process and regional characteristics with conventional empty-borehole blasting [4].In other words, when the explosive in the borehole is detonated, the detonation wave first acts on the …
اقرأ أكثر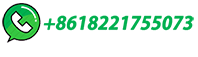
Crusher Layout
Planning your crusher layout is very critical to the entire planning process. While crusher layout in series reduces the capital costs, it severely reduces the overall availability of …
اقرأ أكثر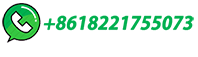