Ball Mill Grinding Machines: Working Principle, Types, Parts
Planetary ball mills are ideal for nano-scale grinding and mixing. Vibratory Ball Mills: Utilizing vibrations, these mills are suitable for ultra-fine grinding and mixing of materials. Vibratory ball mills provide high-energy input to the grinding media, resulting in faster and more efficient grinding.
اقرأ أكثر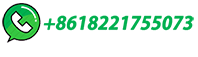
Metallurgy, mechanistic models and machine learning in …
The interrelation between machine learning, mechanistic models and metallurgy is shown by bidirectional black arrows. Some variables needed in machine learning, such as temperature, are difficult ...
اقرأ أكثر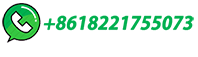
Ball Mill Critical Speed
A Ball Mill Critical Speed (actually ball, rod, AG or SAG) is the speed at which the centrifugal forces equal gravitational forces at the mill shell's inside surface and no balls will fall from its position onto the shell. The imagery below helps explain what goes on inside a mill as speed varies. Use our online formula. The mill speed is typically …
اقرأ أكثر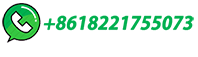
The operating principle of the ball mill
Energy consumption for ball mills is a function of many factors: the physical properties of the ground material – its specific gravity and hardness; the degree of drum filling by grinding balls; the number of …
اقرأ أكثر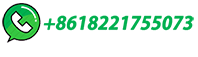
Effect of High-Energy Ball Milling on Structure and
The reported studies perfectly illustrated the effectiveness of high-energy ball milling process in obtaining nanostructured intermetallic alloys. High-energy ball …
اقرأ أكثر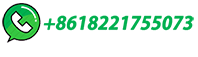
Effect of High-Energy Ball Milling on Structure and
Currently, lightweight materials and structures are potentially required for economical aspects. A major preoccupation of engineers and materials scientists is to create and to develop existing materials to satisfy the rising needs of industries and population. It is well known that intermetallic compounds, such as aluminides, are used …
اقرأ أكثر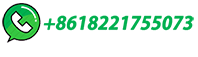
Closed Circuit Grinding VS Open Circuit Grinding
From a theoretical point of view, the ideal method of grinding would consist of a series of ball mills, each in closed circuit with a classifier and each so short that the ore in its passage through the mill would be struck only two or three times by the balls, any undersize produced being removed at once by the classifier ; in this way the ...
اقرأ أكثر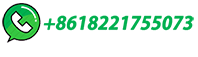
Contamination in wet-ball milling: Powder Metallurgy: Vol …
Ball milling [1], is the most widely appreciated and applied top–down solid state process for alloy designing. ... Powder Metallurgy Volume 60, 2017 - Issue 4. Journal homepage. 531 Views ... (particularly from process control agents (PCAs)), remains less studied and often ignored. In this article, a theory that explains the cause of PCA ...
اقرأ أكثر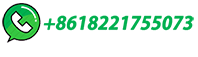
SAG milling & grinding pilot plants
Rod mills: Although rarely used in industrial practice, ALS has 2 x 2.3 kW rod mills for small (<50 kg/h) throughputs where preferential coarse grinding is advantageous for the downstream processing. Ball mills: Ball mills are the stalwart unit of the majority of pilot grinding circuits. ALS has a range of rubber lined overflow ball mills ...
اقرأ أكثر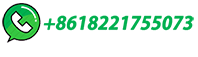
Studies on Scale-Up of Ball Mills | Mining, Metallurgy
Data from ball mills with a wide range of diameters are analyzed using detailed mathematical/numerical models. Analysis shows the relative power inefficiency of large ball mills is due to their inefficient breakage of coarse particles. The models developed can be used to scale-up mill behavior. The behavior of large mills at Bougainville and Pinto …
اقرأ أكثر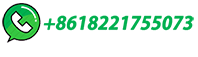
(PDF) Design and Performance of Ball Milling for Powder …
Flat products of carbon nanotubes (CNTs) reinforced Al matrix composites were fabricated using flake powder metallurgy via shift-speed ball milling and hot-rolling.
اقرأ أكثر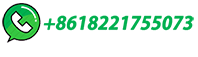
Energies | Free Full-Text | Energy-Efficient Advanced Ultrafine
The present literature review explores the energy-efficient ultrafine grinding of particles using stirred mills. The review provides an overview of the different techniques for size reduction and the impact of energy requirements on the choice of stirred mills. It also discusses the factors, including the design, operating parameters, and feed material …
اقرأ أكثر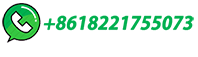
(PDF) Effects of Ball Size Distribution and Mill Speed and …
In this research, the effect of ball size distribution on the mill power draw, charge motion regime and breakage mechanism in a laboratory ball mill was studied …
اقرأ أكثر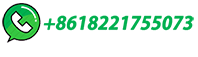
Ball Mill
The characteristic tumbling motion of these mills has given them the name 'tumbling mills', which include the ball mill, tube mill and rod mill. Ball mills are horizontal rotating cylindrical or conical steel chambers, approximately one third to half full of steel, alloy steel or iron balls, like that shown in Fig. 4.10 A–C, or flint stones.
اقرأ أكثر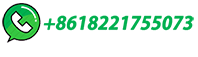
Lecture 11: Material balance in mineral processing
Key words: Material balance, ball mill, hydro cyclone, flotation. Preamble An important aspect of any mineral processing study is an analysis of how material is distributed whenever streams split and combine. This knowledge is necessary when a …
اقرأ أكثر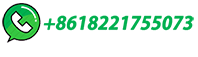
The Beginning of Copper Metallurgy in Oman
The paper examines the early evidence of metallurgy in Oman. It presents the results of some analyzes performed on prehistoric metal objects, reconstructing the operational …
اقرأ أكثر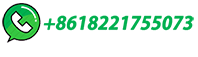
Why is the Bond Ball Mill Grindability Test done the …
the rotating charge inside most industrial ball mills. Most industrial ball mills have lifters. Data from 40 ball mills show that the average critical speed is 0.73 (Morrell, 1996). Research in mill charge motion (eg. Mishra and Rajamani, 1992; Inoue and Okaya, 1994) reveals how the charge motion vary with mill speed and liner/lifter profile.
اقرأ أكثر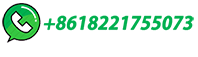
Keys to best practice comminution
Similarly, the ball mill L/D ratio should not exceed 1.65. Each of the SAG/ball mill pairs shown in the various cases in the Table 1 example, will do the required grinding job and produce the specified tonnage of 471 t/h at a finished grind of 80% passing 75 µm. As in any trade-off study, there are also reasons to favour one configuration over ...
اقرأ أكثر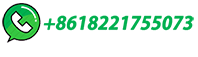
Functional Performance of Ball Milling Circuits – A Plant …
if the ball mill circuit is receiving 500 t/h of ore containing 20 per cent fines and produces 500 t/h of circuit product (eg cyclone overflow) containing 80 per cent fines, the circuit production rate of new fines is: 500 × (80 per cent – 20 per cent), or 300 t/h. Mill power draw (MP) Ball mill power draw is measured during a circuit survey
اقرأ أكثر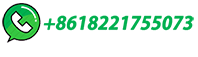
Froth Flotation Process
"The single most important method used for the recovery and upgrading of sulfide ores", that's how G. J. Jameson described the froth flotation process in 1992. And it's true: this process, used in several processing industries, is able to selectively separate hydrophobic from hydrophilic materials, by taking advantage of the different categories …
اقرأ أكثر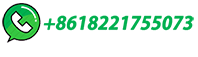
Grinding in Ball Mills: Modeling and Process Control
55 known as the distribution function [45, 46]) describes the distribution of fragment sizes obtained after a breakage of particles of size xj.Thus, b1j, b2j, …, bnj are the mass fractions of particles in size classes 1, 2, …, n after a breakage of particles in size class j. The mechanism of breakage is illustrated in [23] by a diagram shown in Fig. 3.
اقرأ أكثر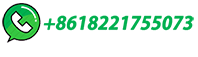
Stirred Mill
The vertical stirred mill is vertically installed, and gravity works in the grinding process. With the advantages of high grinding efficiency and less area occupation, it is widely used in the regrinding, fine grinding, and ultrafine grinding process of such metal mines as iron ore, copper ore, lead-zinc, and such nonmetallic mineral industries as …
اقرأ أكثر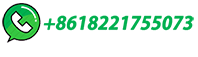
Heat generation model in the ball-milling process of a
Abstract. This work focuses on the characterization of heat generation during dry fracture by direct impact of a tantalum ore. Moreover, an attempt was made to quantify the heat …
اقرأ أكثر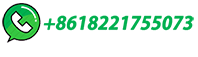
Understanding Basic Welding Metallurgy
The science of metallurgy focuses on the chemical, physical, and mechanical composition of a metal and its alloys. And it carries special importance for welders because a metal's attributes may be altered during the fusion process thermal cycles. Basic knowledge of welding metallurgy is, consequently, a great benefit for …
اقرأ أكثر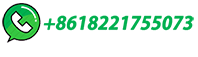
Grinding in Ball Mills: Modeling and Process Control
Grinding in ball mills is an important technological process applied to reduce the size of particles which may have different nature and a wide diversity of physical, mechanical …
اقرأ أكثر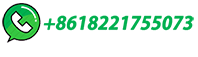
How it Works: Crushers, Grinding Mills and …
The feed enters one end of the ball mill, and discharges out the other end. Ball mills vary greatly in size, from large industrial ball mills measuring more than 25 ft. in diameter to small mills used for sample …
اقرأ أكثر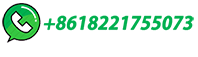
Effect of ball mill size on media wear | Mining, Metallurgy …
Correlation of scale-up from small-scale batch laboratory mills to large-diameter industrial mills was established by performing two series of laboratory and pilot plant grinding tests using a magnetic taconite ore and a siliceous sulfide ore. In one series, controlled batch grinding tests in 203-, 508-, and 914-mm (8-, 20-, and 36-in.) diameter mills were …
اقرأ أكثر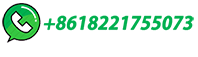
Ball Mills vs Rod Mills
The voids (or interstitial space) within a rod load are approximately half those in a ball mill grinding load. Rods in place weigh approximately 400 pounds per cu. ft. and balls in place approximately 300 pounds per cu. ft.. Thus, quantitatively, less material can progress through the voids in the rod mill grinding media than in the ball mill ...
اقرأ أكثر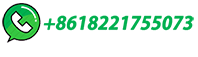
Crushing in Mineral Processing
In mineral processing or metallurgy, the first stage of comminution is crushing. Depending of the type of rock (geometallurgy) to be crushed, there are 2 largely different techniques at your disposition for crushing rocks. In principle, compression crushing is used on hard and abrasive rocks by placing them between a high wear …
اقرأ أكثر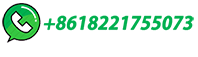
A Review of the Grinding Media in Ball Mills for Mineral …
Ball mill efficiency directly affects the cost of mineral processing. Grinding media play a vital role in enhancing the efficiency of a ball mill through their direct effect …
اقرأ أكثر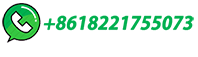