A Review of the Grinding Media in Ball Mills for Mineral …
Ball mill efficiency directly affects the cost of mineral processing. Grinding media play a vital role in enhancing the efficiency of a ball mill through their direct effect …
اقرأ أكثر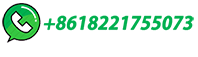
BALL MILLS Ball mill optimisation
efficient grinding systems available for the cement and mineral industry, including vertical roller mills (VRM), high-pressure grinding units (HPGR) or simple roller presses, as well …
اقرأ أكثر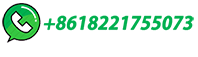
Ball Charge and Grinding Efficiency
Additionally, in ball mills grinding is primarily through cascading not cataracting (compared to an AG.SAG) so the slurry pool is not a factor unless density is high, which leads to viscosity issues. ... Ball mill liner efficiency based on liner geometry and its influence on kW-hours/ton, total tons/life cycle, and P80 transfer to cyclones. ...
اقرأ أكثر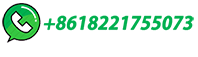
Rethinking Grinding Efficiency in Ball Mills
Kolev et al (2021) –In press. Improving the energy efficiency in tumbling mills with the use of Relo grinding media (MDPI) • Lab trials conducted using a standard Bond ball mill (@ Wardell Armstrong) • Standard Bond ball mill procedures were followed –only the RELO media PSD and mass of charge adjusted to match spherical media
اقرأ أكثر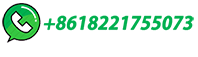
Effect of grinding media properties and stirrer tip speed …
Owing to their high energy efficiency, stirred mills are commonly used in the fine or ultrafine grinding of low-grade and fine disseminated ores to enhance liberation. In this study, batch wet grinding studies were conducted in a stirred mill to evaluate the effect of the grinding media density, grinding media diameter, and stirrer tip speed on ...
اقرأ أكثر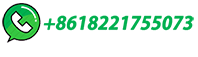
Analysis of process of grinding efficiency in ball and rod mills …
The article presents the results of laboratory-scale research on the determination of the impact of ball mill parameters and the feed directed to grinding on its effectiveness and comparing it with the efficiency of grinding in a rod mill. The research was carried out for grinding copper ore processed in O/ZWR KGHM PM S.A.
اقرأ أكثر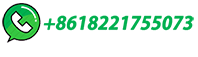
Grinding Media in Ball Mills-A Review
Table 1. Chemical composition of typical grinding media (% wt.). Adapted from [24]. 2.1.1. Cast Iron Cast iron can be grey cast iron or white cast iron, but white cast irons are commonly used in ...
اقرأ أكثر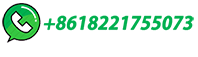
Effect of grinding media on the milling efficiency of a ball mill
The size of grinding media is the primary factor that affects the overall milling efficiency of a ball mill (e.g. power consumption and particle size breakage). This article tackles the lack of a design tool that could help choose the ball loading composition in mills. Such a tool enables the maximization of the exposed surface area per unit …
اقرأ أكثر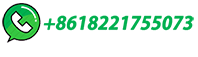
How to Measure Grinding Efficiency
In determining grinding efficiency, each stage is considered as a single stage. The power per tonne for rod milling is determined from the rod mill feed rate and …
اقرأ أكثر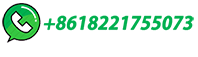
INVESTIGATION OF EFFECTS OF GRINDING MEDIA SHAPES TO THE GRINDING
Worn balls Worn balls perform more poorly than spheres, reduce the grinding chamber in the mill, and increase power consumption. [9] Spherical balls are mostly used for ball mill processes but are ...
اقرأ أكثر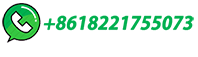
Enhancing the Grinding Efficiency of a Magnetite Second-Stage Mill
Ceramic ball milling has demonstrated remarkable energy-saving efficiency in industrial applications. However, there is a pressing need to enhance the grinding efficiency for coarse particles. This paper introduces a novel method of combining media primarily using ceramic balls supplemented with an appropriate proportion of steel …
اقرأ أكثر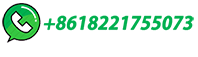
WHAT IS GRINDING EFFICIENCY? WHAT ARE GRINDERS …
Grinding Machine Technical Efficiency. The technical efficiency of the ore mill refers to the ratio between the content (%) of the qualified particle size in the product obtained after grinding and the content (%) of the original ore that is greater than the qualified particle size. The calculation formula 1 is as follows: Remark: E efficiency ...
اقرأ أكثر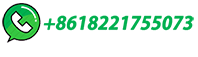
Factors Affecting Ball Mill Grinding Efficiency
The following are factors that have been investigated and applied in conventional ball milling in order to maximize grinding …
اقرأ أكثر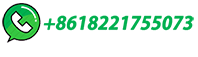
Addition of pebbles to a ball-mill to improve grinding efficiency
Ball-mills are used widely for secondary grinding. Loveday (2010) reported on laboratory tests in which small pebbles (7-25 mm) were used in various proportions with balls. The optimum proportion of pebbles, by volume, was found to be about 25%.
اقرأ أكثر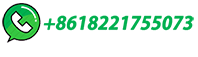
How Many Factors Affect Grinding Efficiency of Ball Mill?
01 Grinding concentration on ball mill grinding. Grinding concentration is one of the important factors affecting the working efficiency of ball mill.The influence of grinding concentration is mainly reflected in three aspects: the specific gravity of the slurry, the degree of adhesion of the ore particles around the steel ball and the fluidity of the …
اقرأ أكثر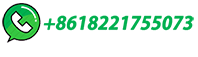
Rethinking Grinding Efficiency in Ball Mills
Lameck's work indicated that: Higher torque (power draw) can be achieved with increased packing efficiency – particularly for worn ball media. At lower mill speeds, the cylpebs …
اقرأ أكثر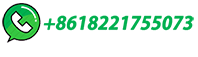
Comparison of energy efficiency between ball mills and stirred mills …
The work using a vertical shaft stirred mill compared with Bond ball mill, both operated in closed circuit with a classifier, demonstrated a clear trend that on average 30% energy saving can be expected by using the stirred mill to replace ball mill for coarse grinding from a top particle size 3.35 mm to P 80 less than 100 μm.
اقرأ أكثر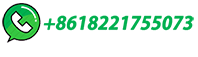
Comparison of energy efficiency between ball mills and stirred mills …
At product sizes finer than 80% passing 75 μm, the efficiency of ball mill grinding rapidly decreases. The practical limit to ball mill product fineness is considered to be 40–45 μm (Gao and Weller, 1994). Although ball mills can still be found in the regrind circuits in a number of mineral processing plants, their energy consumption is ...
اقرأ أكثر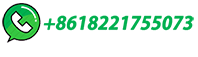
Assessing load in ball mill using instrumented grinding media
An instrumented grinding media was designed to mimic the motion state of ordinary grinding balls. • Grinding efficiency index was proposed to evaluate the grinding effect. • Time-domain features were combined with sample entropy in feature extraction. • Recognition accuracy of ball mill load based on PSO-SVM classification …
اقرأ أكثر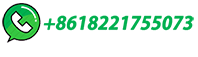
The energy efficiency of ball milling in comminution
To illustrate how grinding conditions can affect ball mill efficiency, the batch grinding model will be used to model closed-circuit ball milling of the soda-lime glass. For this model, the size range of a particulate assembly in a batch mill is divided into size intervals with a maximum size X 1 above and a minimum size X n+1.
اقرأ أكثر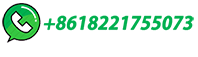
Seven Tips Increasing Ball Mill Grinding Efficiency
Through the long period operation, ball mill meets the problem of grinding efficiency descending. It impacts the normal operation of processing plant, and also causes economic losses.
اقرأ أكثر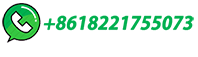
A critical review on the mechanisms of chemical additives …
1. Introduction. The term chemical additives or grinding aids (GAs) refers to any substance which results in increased grinding efficiency and reduction in power consumption when added to the mill charge (amounts not exceeding 0.25 wt.% of the feed) during grinding [1], [2], [3].The use of grinding aids to increase mill throughput is quite …
اقرأ أكثر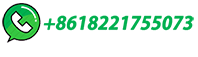
Effect of ball and feed particle size distribution on the milling
During the grinding process, coarser material (size class 1) break to finer material (size class 2) and (size class 3) which are termed the daughter products, as shown in Fig. 1.A chemical reaction on the other hand can consist of say reactant 'A' forming intermediate product 'B' then proceeding to final product 'C' or a competing reactant 'A' …
اقرأ أكثر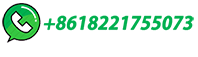
Three Major Factors Affecting the Grinding Efficiency of Ball Mill
The influence of materials on the grinding efficiency of ball mill is mainly reflected in three aspects: ore nature, feed size and product size. 01 Ore properties.
اقرأ أكثر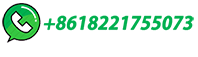
High efficiency ball mill grinding
Some of the factors that need to be considered to increase the efficiency of ball milling grinding, are discussed. Grinding efficiency can be increased by making some changes in operating practice ...
اقرأ أكثر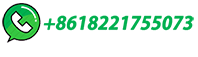
(PDF) Effects of Ball Size Distribution and Mill Speed and …
The use of high-pressure grinding rolls (HPGR) prior to ball mills has become a common practice in cement clinker grinding due to significant energy savings in comparison to ball milling alone.
اقرأ أكثر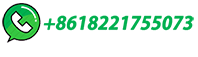
Ceramic vs. Steel Grinding Balls: A Comprehensive …
Introduction. In industrial processes, grinding balls are indispensable components in milling and grinding operations, where they play a pivotal role in reducing particle sizes and refining material textures. These balls, varying in material composition, size, and density, are at the heart of numerous industries, from mining to …
اقرأ أكثر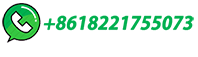
MODULE #5: FUNCTIONAL PERFOMANCE OF BALL …
Ball mill = coarse particles (in the plant ball mill) grinding efficiency Ore grindability (in the lab ball mill) The units of "ball mill grinding efficiency" will be covered in detail in the first part of the module. Alternatively, we can say that: Specific grinding rate = Ball mill x Ore grindability of coarse particles grinding (in the lab mill)
اقرأ أكثر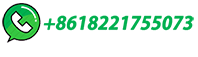
Ball Mill Grinding Theory – Crushing Motion/Action Inside
Large VS Small Grinding Balls. Two tests with closed-circuit crushing are reported to show the efficiency of the ball-mill when charged with large and with small balls. Test No. 12 shows a production of 6.3 T. of minus 200-mesh material per hour, which is 17.15 kw.-hr. per ton of this material actually produced.
اقرأ أكثر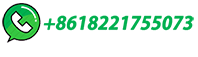
(PDF) Analysis of the efficiency of the grinding …
Ball mills for fine grinding cement clinker and additives are widely used around the world. To improve the efficiency of a ball grinding the ball mills are transferred in closed circuit with air ...
اقرأ أكثر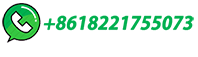