Everything you need to know about …
There is no direct to filter gas loop for cement and coal mills. ... For closed circuit mills grinding OPC as well as CEM II type products, the FL default CII media charge is 40% 25 mm, 40% 20 mm and 20% 15mm …
اقرأ أكثر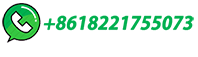
Laboratory Ultra Centrifugal Mill ZM 300
The maximum speed of classic centrifugal mills, like the widely used ZM 200, is usually limited to 18,000 rpm (rotor peripheral speed 98 m/s). The ZM 300 achieves a maximum speed of 23,000 rpm (rotor peripheral speed 118 m/s) and produces particles which are 15 to 20 % finer in comparison, depending on the material.
اقرأ أكثر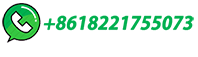
Raymond Bowl Mill designed and built for flexibility
The Raymond Bowl Mill is considered the finest vertical roller mill available for pulverizing coal. The typical Raymond bowl mill system is designed to simultaneously dry, pulverize, and classify solid fuels to 95% passing 200 mesh (<5%R75μ) with a wide range of capacities from 24 to 150 stph.
اقرأ أكثر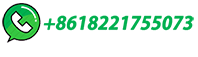
Thorwesten-Vent
In a wide variety of industries, e.g. in the cement and steel industry, an explosive dust atmosphere is created during the grinding of coal and similar products. This can lead to explosions and therefore requires the …
اقرأ أكثر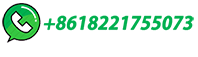
Bowl Mill Grinding Roller Tires & Table Liners
IMCO makes Grinding roller tires of mill XRP 1003 modified with Zuper replaceable segments fused with Zuper metal matrix ceramic Composites as per 3D drawing attached with complete machining and finishing. ... metal matrix ceramic composites duly fused and impregnated in a sintered chromium carbides having 60-62 Hrc hardness on surface …
اقرأ أكثر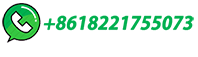
Grinding analysis of Indian coal using response surface methodology
The present work discusses a systematic approach to model grinding parameters of coal in a ball mill. A three level Box–Behnken design combined with response surface methodology using second order model was applied to the experiments done according to the model requirement. Three parameters ball charge (numbers …
اقرأ أكثر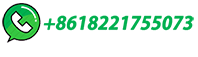
Grinding Mill Liners
Ball mills working as the secondary portion of a grinding circuit will utilize the lower profile liners. The reason is as lift decreases, friction increases. To function effectively they need this type of grinding action to obtain the …
اقرأ أكثر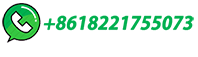
How to Process Coal into Pulverized Coal in 5 Steps?
1 To pulverize crushed coals in a ball mill, you start by feeding the mill with crushed coal. Then the grinding media crushes and grinds the coal in the rotating chamber. 2 Airflow carries the pulverized coal out of the ball mill. 3 Next, you'll need to use the mill classifier to separate the fine coal particles from the airflow.
اقرأ أكثر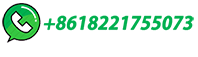
Tuning the Morphology and Surface Property of Mineral …
Grinding of minerals for particle size reduction and liberation is a prerequisite for successful mineral flotation separation and powder modification. Different grinding media produce mineral particles with different physical morphology and surface chemistry properties. Different mill particles expose different proportions of cleavage …
اقرأ أكثر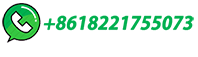
A Review of the Grinding Media in Ball Mills for Mineral …
The ball mill is a rotating cylindrical vessel with grinding media inside, which is responsible for breaking the ore particles. Grinding media play an important role in the comminution of mineral ores in these mills. This work reviews the application of balls in mineral processing as a function of the materials used to manufacture them and the …
اقرأ أكثر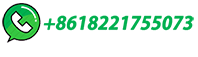
United Grinding North America Expands Distribution …
UNITED GRINDING North America announced today the expansion of their distribution net-work with the addition of Intermaq, a leader in the machine tool industry …
اقرأ أكثر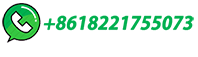
Fire and explosion protection of coal grinding systems.
You will be surprised about what has gone wrong with fire and explosion protection of your system(s). Be sure about that! Evaluation of a coal grinding system's fire and explosion protection, including the raw coal storage and the fine coal silo storage normally can be done in one day, mostly without having to stop coal grinding.
اقرأ أكثر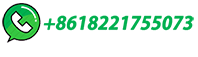
Fine grinding of wood – Overview from wood breakage to …
Fine grinding mills can be categorized into five groups [48]: impact mills, ball media mills, air jet mills, roller mills, and those of some other type, including disc mills. Impact mills and air jet mills are based on single impacts, as presented in Fig. 4 a, while ball media mills utilize double impacts between metal surfaces ( Fig. 4 b).
اقرأ أكثر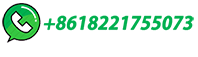
Surface Grinding: A Guide to the Process and Precision
This blog post will delve deep into surface grinding, highlighting its importance, techniques, and applications in modern manufacturing. +1(213) 398 9420 +86 ; sales@okdor; Mon - Sat: 9:00 - 18:30; Sheet Metal Fabrication. CNC Machining . Metal Stamping. Get Instant Quote. Get Instant Quote.
اقرأ أكثر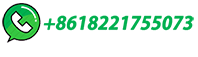
Grinding Mills — Types, Working Principle & …
Semi-Autogenous Mills/ SAG Mills (primary grinding mill) — these mills use grinding balls with forces of attrition, impact, and abrasion between grinding balls and ore particles that result in ...
اقرأ أكثر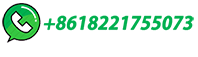
Two coal/petcoke grinding plants for Mexico
Loesche has now sold two of its biggest coal/petcoke grinding mills for the cement industry in Mexico. These are to be used in the cement plants of the group Cooperativa …
اقرأ أكثر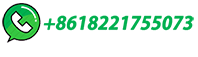
grinding process in coal
iron ore dry grinding process - Mineral Processing EPC. Jun 17, 2018· Working Principle Of Ball Mill For Lab In Grinding Iron Ore With . Working Principle Of Ball Mill For Lab In Grinding Iron Ore With Reasonable Price With . the ball mill can grind various ores and other materials with dry type and wet type. . through the discharging board thus the …
اقرأ أكثر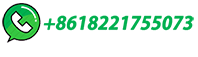
"Blueprint" Your Pulverizer for Improved Performance
that the grinding surface profiles are optimum. That means using the original design grinding profiles for your mill. The majority of coal pulverizers sized around 120,000 pph use three grinding elements, referred to as journals, rolls, or tires. For best results, all three grind-ing elements should be replaced in matched sets.
اقرأ أكثر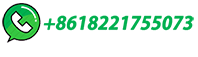
Grinding Mill
In addition to surface grinding, cylindrical, internal and centerless grinding methods are also available. For disc-shaped sputtering targets (e.g., tungsten), surface grinding is …
اقرأ أكثر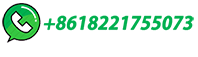
Grinding
Comparing dry and wet grinding curves in a ball mill in the same condition (an equal amount of materials and grinding media has been used on each pair of wet-dry experiments) (Fig. 1.7) indicated two significant differences at higher power values of wet grinding, specifically when speed exceeded 0.6 critical speed and for higher ω Pmax in …
اقرأ أكثر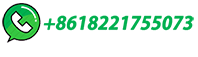
Seller of 200TPH- 300 TPH coal mining Raymond mill Mexico
Usually coal mining process includes primary crushing process and secondary crushing process. According to the coal mineral size your demand, we will choose different grinding mill machines which including Raymond mill hammer mill, ball mill, vertical mill are usually used. Features of Raymond mill applied 200-300TPH coal mining industry:
اقرأ أكثر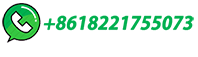
Optimization of grinding pretreatment for effective flotation of
The coal surface is easy to be oxidized, resulting in a decrease in surface hydrophobicity. ... and feed amount on the flotation behavior of oxidized coal. The optimum grinding conditions are as follows: the feed amount is 70 g, the pulp density is 40%, and the grinding time is 15 min. Under the optimum grinding conditions, 62.53% …
اقرأ أكثر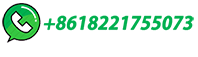
Raymond Bowl Mill designed and built for flexibility
The Raymond Bowl Mill is considered the finest vertical roller mill available for pulverizing coal. The typical Raymond bowl mill system is designed to simultaneously dry, …
اقرأ أكثر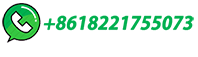
LOESCHE to Deliver Two Powerful Coal / Pet Coke Gringing …
LOESCHE has now sold two of its biggest coal / pet coke grinding mills for the cement industry in Mexico. These are to be used in the cement plants of the group Cooperativa La Cruz Azul, S.C.L. – on the one hand in the plant in the province of Hidalgo, 80km north …
اقرأ أكثر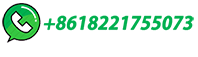
Grinding analysis of Indian coal using response surface methodology
The Box–Behnken experimental design was used to provide data for modeling and the variables of model were Bond work index, grinding time and ball diameter of mill. Coal grinding tests were ...
اقرأ أكثر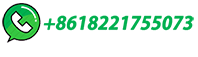
Flexible grinding mills solutions that last | FL
The OKTM mill can skilfully grind raw or cement feed material and offers parts commonality, simplifying spare parts inventory and facilitating easy switching of parts between vertical roller mills. Our ATOX® coal mill has large rollers with great grinding capability of all types of coal, tolerating moisture levels up to 20 percent.
اقرأ أكثر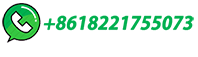
Energy-Efficient Advanced Ultrafine Grinding of Particles …
The present literature review explores the energy-efficient ultrafine grinding of particles using stirred mills. The review provides an overview of the different techniques for size reduction and the impact of energy requirements on the choice of stirred mills. It also discusses the factors, including the design, operating parameters, and feed material …
اقرأ أكثر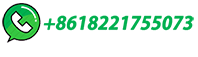
How Does a Vertical Coal Mill Work
A vertical coal mill functions by introducing coal into a rotating table, where it undergoes pulverization through a combination of compression and grinding forces. As the table rotates, coal fed through a central chute is crushed between the rollers and the grinding table surface.
اقرأ أكثر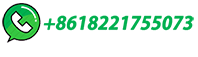
ATOX® Coal Mill
A compact coal mill solution for grinding virtually any type of raw coal. ... making use of the entire segment surface. The coal mill's liner segments can also be repeatedly hardfaced for maximal longevity. 01. Handles all types of coal. The durable grinding mill can handle virtually any type of raw coal and has been designed to grind feed ...
اقرأ أكثر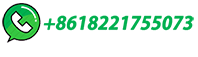