Ball Mill | Ball Mills | Wet & Dry Grinding | DOVE
DOVE offers a wide range of high quality ball mills, for wet or dry grinding operations, as well as regrinding application, for capacities up to 240 Tons/Hour. ... DOVE laboratory will assay your ore samples rapidly and analyze your raw materials and recommend the ... WE HIGHLY RECOMMEND FORWARDING SOIL SAMPLES OF YOUR MINE TO US FOR …
اقرأ أكثر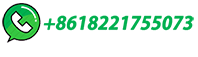
What is a Ball Mill Explained: In-Depth Guide
Critical Speed: Critical speed is the hypothetical speed at which the centrifugal force is equal to the gravitational force, and the grinding media starts sticking to the inner shell of the equipment instead of falling freely.Grinding at or close to critical speed of the mill yields a poorer grinding efficiency. The ball mills are mostly operated at 65 …
اقرأ أكثر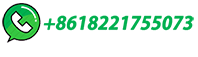
MODULE #5: FUNCTIONAL PERFOMANCE OF BALL …
INTRODUCTION. In the prerequisite module entitled "Work Index Efficiency", you have learned about work index analysis* to define overall grinding circuit efficiency. In rod …
اقرأ أكثر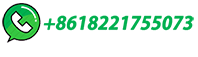
Specifications of the Ball Mill | Download Scientific Diagram
Download scientific diagram | Specifications of the Ball Mill from publication: Energy Optimization of a Grinding Circuit at a Copper Mine | This study aimed to reveal the …
اقرأ أكثر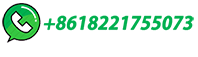
Ball Mill Is Indispensable For Lithium Ore Processing
The advantage of the grid type ball mill is that the ore discharge speed is fast, it can reduce the over-crushing of ore, and at the same time it can increase the output per unit volume. 1. Large row of ore mouth design, stronger processing capacity for lithium ore, up to 160t/h; 2. Equipped with an automatic control system PLC, reducing labor costs, …
اقرأ أكثر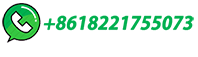
Basic Ball Mill Grinding Circuit
In some plants a ball-mill or rod-mill will reduce the ore to, say, 100 mesh and a tube-mill will finish the grinding to 200 mesh or finer. In other plants a ball- mill or a tube-mill will do all the grinding, but it must be fed with fine ore—say, 1/8 to …
اقرأ أكثر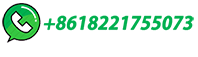
Analysis and validation of a run-of-mine ore grinding mill circuit
Two types of mills commonly found in the minerals processing industry are ball and semi-autogenous (SAG) mills, which use both ore and steel balls as grinding media (Wei and Craig, 2009b).In the case of a ball mill the ore is crushed before it enters the mill, whereas a SAG mill receives run-of-mine (ROM) ore directly (Stanley, 1987).A …
اقرأ أكثر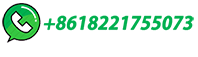
Mechanistic modeling and simulation of grinding iron ore …
DOI: 10.1016/J.POWTEC.2021.07.030 Corpus ID: 237666917; Mechanistic modeling and simulation of grinding iron ore pellet feed in pilot and industrial-scale ball mills @article{Carvalho2021MechanisticMA, title={Mechanistic modeling and simulation of grinding iron ore pellet feed in pilot and industrial-scale ball mills}, author={Rodrigo M …
اقرأ أكثر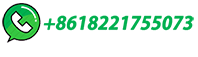
Calibrating the Digital Twin of a Laboratory Ball Mill for Copper Ore
This article presents a novel approach to calibrating the digital twin of a laboratory mill used for copper ore milling. By integrating computer vision techniques for real-time data extraction and employing DualSPHysics simulations for various milling scenarios, including balls only, balls with ore, and balls with slurry, we achieve a high …
اقرأ أكثر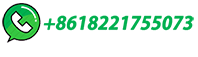
Population balance model approach to ball mill optimization in iron ore
An analysis of the kinetics of dolomite grinding in a dry ball mill reveals that the following approximations apply for the parameters of the batch grinding model: the size discretized selection ...
اقرأ أكثر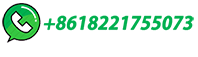
MODULE #5: FUNCTIONAL PERFOMANCE OF BALL …
Relating design and operating variables to grinding, classification, and circuit efficiencies 53 Relative accuracy of functional performance parameters 62 ... During Survey #1 at the Camco Mine, the ore feed rate to the ball mill circuit was 67 t/h. The circuit feed contained 29.33% of -106 micron (150 mesh) material (fines) and the circuit ...
اقرأ أكثر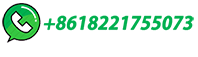
How to Size & Design a Regrind Ball Mill
Referring to Table VI the L/D can be between 1.75 and 2.0 or even greater. Referring to Table VII a 3.05 meter (10 foot) by 3.05 meter (10 foot) overflow ball mill with a 40 percent by mill volume ball charge, new liners and 50 mm (2″) balls draws 491 HP. Using equation 5 there will be a loss of 0.55 Kw (0.74 Hp) per metric tonnes of balls.
اقرأ أكثر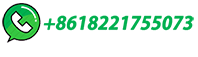
Ball Mill & Rod Mill Design
In all ore dressing and milling processes, including flotation, cyanidation, gravity concentration, and amalgamation, it is necessary to crush and grind, often with rob mill & ball mills, the ore in order to liberate the minerals. In the chemical and process industries, grinding is an important step in preparing raw materials for subsequent …
اقرأ أكثر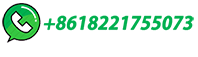
AMIT 135: Lesson 7 Ball Mills & Circuits – Mining …
Explain the role of ball mill in mineral industry and why it is extensively used. Describe different types of ball mill design. Describe the components of ball mill. Explain their understanding of ball mill …
اقرأ أكثر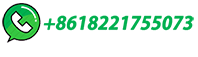
Iron Ore Grinding Energy Conservation Research Based
This article briefly introduces the iron ore grinding classification process and analyzes the distribution of mining energy consumption. To realize the energy conservation of the mill by using genetic BP neural network, we make MATLAB simulation test. It shows feasibility and superiority of the control scheme, which has some meaning for energy conservation and …
اقرأ أكثر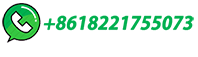
Simulation and optimization of a two-stage ball mill grinding …
The grinding circuit investigated in the current study is a two-stage grinding circuit (Fig. 2) in which two overflow type mills are arranged in series and operated under wet condition.The run-of-mine ore was crushed to 10 mm, and it was then fed to the first ball mill, which was closed by a rake classifier.The second mill operated in a combined …
اقرأ أكثر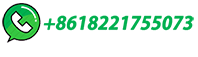
Ball Mills
In all ore dressing and milling Operations, including flotation, cyanidation, gravity concentration, and amalgamation, the Working Principle is to crush and grind, often with rod mill or ball mill, the ore in order to liberate the minerals. In the chemical and process industries, grinding is an important step in preparing raw materials for …
اقرأ أكثر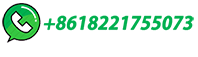
Understanding the SAG Mill in Copper Ore Mining Process
The rod mill is another type of grinding mill used in the copper ore mining process. This machine uses steel rods as the grinding media instead of balls, which are commonly used in ball mills. The rods grind the ore by tumbling …
اقرأ أكثر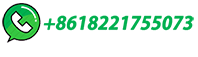
A Review of the Grinding Media in Ball Mills for Mineral …
The ball mill is a rotating cylindrical vessel with grinding media inside, which is responsible for breaking the ore particles. Grinding media play an important role …
اقرأ أكثر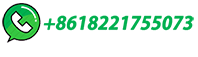
Investigation of some parameters affecting the Ultra-fine grinding …
ABSTRACT In this study, ultra-fine grinding of a refractory silver ore tailings was studied. A laboratory scale pin-type vertical stirred mill and ceramic beads were employed for the grinding tests.
اقرأ أكثر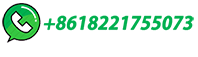
Grinding Media in Ball Mills-A Review
Table 1. Chemical composition of typical grinding media (% wt.). Adapted from [24]. 2.1.1. Cast Iron Cast iron can be grey cast iron or white cast iron, but white cast irons are commonly used in ...
اقرأ أكثر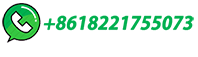
Ball Mill (Ball Mills Explained)
If a ball mill uses little or no water during grinding, it is a 'dry' mill. If a ball mill uses water during grinding, it is a 'wet' mill. A typical ball mill will have a drum length that is 1 or 1.5 times the drum diameter. Ball mills with a drum length to diameter ratio greater than 1.5 are referred to as tube mills. Ball mills may be ...
اقرأ أكثر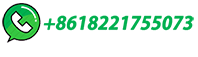
Fine Grinding as Enabling Technology – The IsaMill
Figure 1 : Grinding Power to produce various product sizes in a Ball Mill (9mm balls) and an Isa Mill (2 mm sand) (for KCGM pyrite concentrate) Chemistry Impacts The use of inert grinding media gives a crucial advantage to stirred milling in fine flotation and leaching applications. Even if it were economic to grind to 10 microns in a steel ...
اقرأ أكثر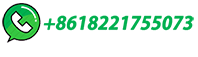
Design and Optimization of Ball Mill for Clinker …
equations showed top side steel ball size M = 127 mm; mill speed actual n = 16.6 rpm; grindability G = 1.69 g/rev, for throughput 80 T/hr clinker grinding from ~ 40 mm size down to average 5–6 microns, employing retention time in the ball mill 20 minutes, feed linear velocity 36 m/hr; hold up 70 Tons, specific energy requirement for clinker ...
اقرأ أكثر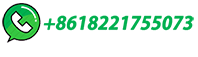
BGM grinding circuit flowsheet with ball mills in series …
Furthermore, the SAG mill circuit indicated varying feed sizes (i.e. xF,80 =102 to 185 mm) which could be rectified by closer monitoring and control of ratios for the SAG mill feeders drawing the ...
اقرأ أكثر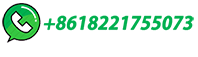
Ball Mill Grinder | Wet & Dry Grinding Ball Mill
Ball Mill Grinder. Our ball mill grinder is a versatile tool designed for grinding and blending materials into fine particles. Its cylindrical chamber houses the grinding medium—be it metallic or ceramic balls—allowing for smooth, efficient milling.
اقرأ أكثر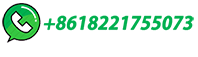
Ball Mill Design/Power Calculation
The basic parameters used in ball mill design (power calculations), rod mill or any tumbling mill sizing are; material to be ground, characteristics, Bond Work Index, bulk density, specific density, desired mill tonnage capacity DTPH, operating % solids or pulp density, feed size as F80 and maximum 'chunk size', product size as P80 and …
اقرأ أكثر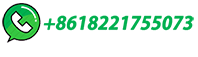
Welcome to Starkey & Associates Inc.
The latter is now acknowledged by our clients to be a world-class method for grinding circuit design, and is accepted by our peers as a standard for ore hardness testing. SAGDesign testing provides SAG pinion energy grindability in kWh/t to within +/- 5% from 152 to 1.7 mm, and Bond Ball Mill Work Index on SAG ground ore, from the SAG test …
اقرأ أكثر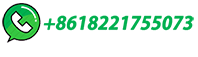
Effect of grinding media on the milling efficiency of a …
The size of grinding media is the primary factor that affects the overall milling efficiency of a ball mill (e.g. power con-sumption and particle size breakage). This article tackles the lack of a design tool that could help choose the ball loading composition in mills.
اقرأ أكثر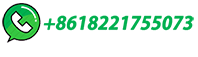
A CRITICAL REVIEW OF GRINDING DESIGN …
• Transfer size (T80) is the term used to describe the SAG mill product that is sent to the ball mill. For peak performance and balancing the power available in the SAG mill and ball mill, the transfer size must be measured and controlled. • The transfer size will be 500 microns using a 12mm opening trommel. This can be true under special
اقرأ أكثر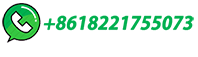