From Ore to Iron with Smelting and Direct Iron Reduction
Figure 1: Steelmaking byproducts for blast furnace (BF), basic oxygen furnace (BOF) and electric arc furnace (EAF) processes. Source: World Steel Association (worldsteel) The first step in the production of steel or cast iron alloys is the reduction of iron ore—which contains iron oxide and gangue or mineral impurities—to unrefined, reduced …
اقرأ أكثر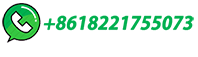
CIE IGCSE Chemistry Revision Notes 2023
The raw materials: iron ore (hematite), coke (an impure form of carbon), and limestone are added into the top of the blast furnace; Hot air is blown into the bottom; Zone 1. Coke burns in the hot air forming carbon dioxide The reaction is exothermic so it gives off heat, heating the furnace; carbon + oxygen → carbon dioxide. Zone 2
اقرأ أكثر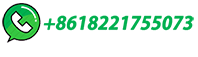
Cement Manufacturing Process- Wet and Dry Processes
Steps of Cement Manufacturing. The steps involved in cement manufacturing are as follows: Quarrying: Raw materials such as limestone and clay are extracted from quarries or mines.; Crushing and Grinding: The extracted raw materials are crushed and ground into a fine powder.; Blending: The crushed and ground raw …
اقرأ أكثر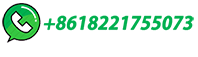
Mineral processing | Metallurgy, Crushing & Grinding
Mineral processing, art of treating crude ores and mineral products in order to separate the valuable minerals from the waste rock, or gangue. It is the first process that most ores undergo after mining in order to provide a more concentrated material for the procedures of extractive metallurgy.
اقرأ أكثر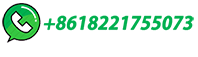
Lime Production Process and Required Equipment
Please enter the materials to be processed, expected productivity, feed size (mm), output size (mm), or other requirements. From lime production from limestonequick, you can get quick lime and …
اقرأ أكثر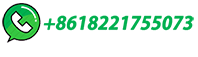
11.23 Taconite Ore Processing
Concentration is the second step in taconite ore processing. As the iron ore minerals are liberated by the crushing steps, the iron-bearing particles must be concentrated. Because only about 33 percent of ... adding between 1 and 10 percent limestone to the ore and binder before pelletization. Pelletization
اقرأ أكثر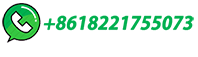
Blast furnace process
The direct reduction can again be divided into intermediate steps in which the iron content in the ores increases in each case: begin{align} ... This makes the ore processing described above necessary. The reduced admixtures in the blast furnace then react with the added flux in the charge and are bound in the resulting slag.
اقرأ أكثر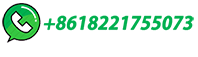
A Life-Cycle Inventory of Limestone Dimension Stone …
The first step of the process is a primary cutting or shaping of the material. This is typically accomplished for limestone using a circular blade saw, diamond wire saw, or a …
اقرأ أكثر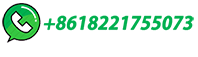
Iron Production
The production of iron from its ore involves an oxidation-reduction reaction carried out in a blast furnace. Iron ore is usually a mixture of iron and vast quantities of impurities such as sand and clay referred to as gangue. ... The high temperatures are needed for the reduction of iron and the oxidation of the limestone which will be seen ...
اقرأ أكثر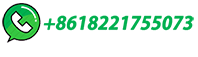
What are the steps in manufacturing Portland cement?
what are the steps limestone ore processed? What are the different steps of chromite ore beneficiation ? what are the equipment in iron ore crusher? What are the parts of a mill in a cement plant?
اقرأ أكثر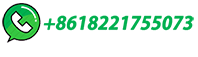
Limestone Quarrying and Processing: A Life-Cycle …
The first step of the process is a primary cutting or shaping of the material. This is typically accomplished for limestone using a circular blade saw, diamond wire saw, or a splitter.
اقرأ أكثر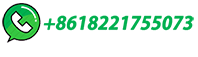
Metallurgy
Steps in Metallurgical Process. The various processes involved in extracting metals from their ores and refining them for use are referred to as metallurgy. The following are the various steps in the metal extraction or …
اقرأ أكثر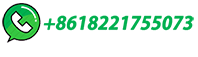
From Ore to Alloy: Navigating Ironmaking in Modern Steel …
In this process, iron ore, coke (a form of carbon), and limestone are fed into the furnace, where intense heat and chemical reactions extract molten iron. Innovations in blast furnace technology, including hot blast systems, oxygen enrichment, and refractory materials, have significantly improved productivity and environmental performance.
اقرأ أكثر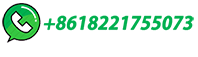
How Cement is Made
An English bricklayer made the first portland cement early in the 19th century by burning powdered limestone and clay on his kitchen stove. ... and appearance, the general process of manufacturing portland cement is the same: crushed limestone and sand are mixed with ground clay, shale, iron ore, fly ash and alternative raw materials ...
اقرأ أكثر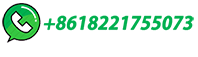
Steps in the Modern Steelmaking Process
The Modern Steel Manufacturing Process Removing Carbon From Iron Creates Steel. Print sdlgzps / Getty Images ... such as iron ore, coal, and limestone. Two processes, basic oxygen steelmaking (BOS) and electric arc furnaces (EAF), account for virtually all steel production. Ironmaking, the first step in making steel, involves the …
اقرأ أكثر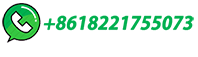
How is iron extracted from ore in an industrial process?
Smelting: The final step in the extraction process is smelting, where the iron ore is heated in a blast furnace along with coke (a carbonaceous fuel) and limestone (which acts as a flux).
اقرأ أكثر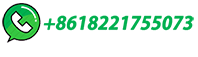
Redox, extraction of iron and transition metals Extracting iron
Raw material: Contains: Function: Iron ore (haematite) Iron(III) oxide (Fe 2 O 3): A compound that the iron is extracted from: Coke: Carbon (C) Used as a fuel and reacts to form carbon monoxide ...
اقرأ أكثر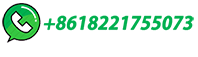
What is the raw ore crushing process?
The raw ore crushing process is the initial stage of mineral processing, which involves breaking the raw ore into smaller pieces in order to extract valuable minerals. This process may vary ...
اقرأ أكثر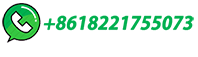
Ironmaking 101 – From Ore to Iron with Blast …
Iron ores with lower iron content such as taconite are first processed to concentrate the iron level and drive off volatile impurities. The iron ore is dressed or crushed into 0.5-1 in. chunks, which increases …
اقرأ أكثر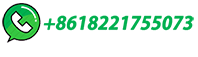
Iron Ore Processing: From Extraction to Manufacturing
Iron ore processing is a crucial step in the production of steel, one of the most essential materials in modern society. Iron ore, a naturally occurring mineral composed primarily of iron oxides, is mined and processed to extract iron for various industrial applications. ... In a blast furnace, iron ore, coke (carbon), and fluxes …
اقرأ أكثر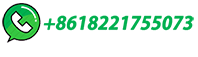
Limestone extraction – underground mining techniques, …
Limestone is a sedimentary rock comprising about 15% of the earth's sedimentary crust. Limestones are generally mined using the methods of open-pit mining and underground mining based on economic and environmental conditions. WHERE DO THEY FORM LIMESTONE : Limestone forms in a variety of marine, freshwater, and terrestrial …
اقرأ أكثر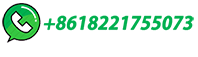
Silver (Ag) Ore | Minerals, Formation, Occurrence, Deposits
Silver ore refers to natural deposits of silver-containing minerals that are mined and processed to extract silver metal. Silver is a precious metal known for its lustrous appearance, high thermal and electrical conductivity, and various industrial, technological, and ornamental uses. Silver has a long history of human use, dating back …
اقرأ أكثر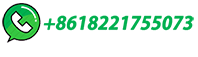
HOW A BLAST FURNACE WORKS
lined with refractory brick, where iron ore, coke and limestone are dumped into the top, and preheated air is blown into the bottom. The raw materials require 6 to 8 ... a blast furnace without any further processing. Iron ore that contains a lower iron content must be processed or beneficiated to increase its iron content. Pellets are
اقرأ أكثر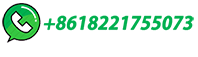
What is Smelting
Thus, smelting is the process before melting, serving as the initial step in transforming raw ore for further processing. Which Metal Is Used In Smelting? 1. Iron. Primary Metal for Smelting: Iron is the primary and most commonly used metal in the process of smelting. Its versatility and abundance make it important for metallurgy.
اقرأ أكثر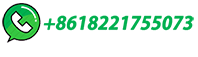
23.3: Metallurgy of Iron and Steel
The first step in the metallurgy of iron is usually roasting the ore (heating the ore in air) to remove water, decomposing carbonates into oxides, and converting sulfides into oxides. The oxides are then reduced in a blast furnace that is 80–100 feet high and about 25 feet in diameter (Figure (PageIndex{2})) in which the roasted ore, coke ...
اقرأ أكثر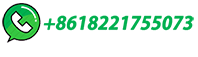
Sintering: A Step Between Mining Iron Ore and Steelmaking
World resources are estimated to be greater than 800 billion tons of crude ore containing more than 230 billion tons of iron. The only source of primary iron is iron ore, but before all that iron ore can be turned into steel, it must go through the sintering process. Sinter is the primary feed material for making iron and steel in a blast furnace.
اقرأ أكثر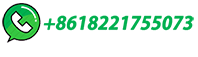
2 Major Roles of Limestone in Cement Manufacturing
Step 1. Limestone mining Cement manufacturing starts from the mining of raw materials, mainly, limestone and clay. ... Fe 2 O 3: from clay, iron ore, scrap iron and fly ash; Gypsum, CaSO 4.2H 2 0: found together with limestone. ... If you own limestone rocks and want to process them into limestone chips or limestone powder for cement …
اقرأ أكثر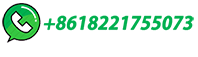
How limestone ore is processed?
The processing of limestone ore typically involves extraction, crushing, grinding, and calcination. Extraction refers to the process of removing the limestone from the earth's surface or...
اقرأ أكثر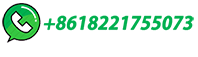
How is the limestone process?
Here are the steps involved in the process of extracting and processing limestone: 1.Mining: Limestone is mined from quarries or mines, usually by blasting or …
اقرأ أكثر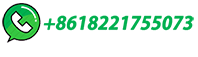
Lithium Production Processes
The gypsum–limestone process was later utilized by Büyükburç and Köksal 69 to extract lithium from a ... No technical information has been released on the processing steps employed. ... Quebec using its proprietary process. 152 After mining from Whabouchi, the raw ore is processed into a concentrate using both dense media …
اقرأ أكثر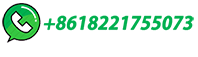