Primary Crusher Optimisation for Improved …
the primary crusher. DEFINITION The primary crusher selection is the key to the success of any mining operation that involves the reduction in size of the ore. The crushing plant can be provided with almost any type of primary rock crusher. The rock/ore determines the type of crusher. The plant capacity determines the size of the crusher.
اقرأ أكثر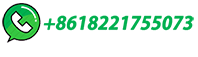
Selecting the right crusher for your operations
These crushers offer an ideal solution for primary crusher applications involving hard, abrasive materials such as granite or recycled concrete. Efficient and less costly to operate because of their minimal …
اقرأ أكثر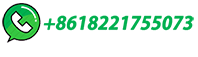
Primary Crusher Selection & Design
How you select your primary crusher will be based on factors like moisture content, maximum rock lump size, material density SG, abrasion index, degradability and it being prone to dusting or not. The …
اقرأ أكثر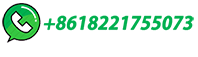
Jaw Crusher Working Principle
The primary rock breaker that is most commonly used in small plants is a jaw crusher of the Blake type, a typical section of which is shown in Fig. 4. ... Bulldog Jaw Crusher. Some jaw crushers are on-floor, some aboveground, and others underground. This in many countries, and crushing many kinds of ore. ...
اقرأ أكثر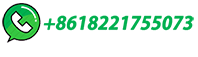
Primary and Secondary Crushing: Understanding the Basics
The primary crusher receives the materials directly from the mine or quarry, and its size reduction ratio ranges from 3:1 to 7:1. The primary crusher can be a jaw crusher, gyratory crusher, or impact crusher, depending on the hardness, abrasiveness, and size of the materials. The jaw crusher is the most common type of …
اقرأ أكثر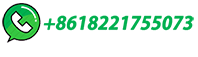
AMIT 135: Lesson 5 Crushing – Mining Mill Operator Training
The ratio of reduction through a primary crusher can be up to about 8:1. Feed: ROM up to 1.5 m; Product: -300mm (for transport) to -200mm (for SAG mill) Feed Rate: 160 to 13,000 tph; The family of primary crushers include: Gyratory Crushers Jaw Crushers Impact Crushers; Typical rules for primary crusher selection:
اقرأ أكثر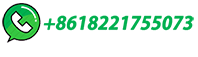
Crushers and Their Types
These are (i) primary crusher, (ii) secondary crusher, and (iii) tertiary crusher. The primary crusher receives material directly from run of mine (ROM) after blasting and produces the first reduction in size. The output of the primary crusher is fed to a secondary crusher, which further reduces the size of the material.
اقرأ أكثر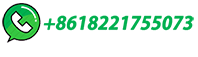
Primary Crusher vs. Secondary Crusher: …
In the aggregate industry, primary crushers are used to break down larger rocks and stones into smaller particles, while secondary crushers are used to further refine these particles into the …
اقرأ أكثر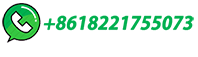
Mining crushers SuperiorTM MKIII Primary Gyratory
metallurgy and thousands of crusher installations around the world combine to create a Primary Gyratory crusher with the best performance, highest capacity and highest reliability. Outotec's line of Superior™ Primary Gyratory crushers are designed to meet the demand for high efficiency and high capacity mining installations.
اقرأ أكثر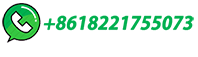
Superior™ MKIII 60-110 primary gyratory crusher
Superior™ MKIII 60-110 primary gyratory crusher is the highest capacity primary gyratory crusher that is available from 's product family. The Superior™ MKIII 60-110 primary gyratory crusher provides great benefit to the entire mineral processing circuit with high throughput and reduced downtime.
اقرأ أكثر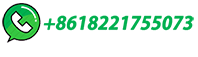
What Crusher Should You Choose for Primary Crushing?
How to choose the right primary crusher? A suitable primary crusher can optimize your production line, increase TPH, handle all heavy-duty tasks, and reduce …
اقرأ أكثر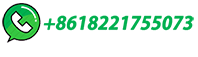
Superior™ MKIII 60-89 primary gyratory crusher
's product family of primary gyratory crushers is called Superior™ MKIII primary gyratory crushers. The "MKIII" stands for the third generation of the Superior™ primary gyratory crushers has developed during over 100 years in designing and manufacturing crushers. ... Superior™ MKIII 60-89 primary gyratory crusher fits a wide ...
اقرأ أكثر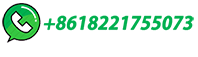
What Type of Crusher Is Best for Primary Crushing?
Primary crushers reduce large run-of-mine material, such as rocks and ore lumps, into smaller sizes for further processing downstream, whether that be …
اقرأ أكثر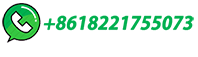
Primary Jaw Crusher – Everything You Need to Know
What is the capacity of a typical primary jaw crusher? The capacity of a primary jaw crusher depends on the machine's size and the material being crushed. Typical capacities range from a few hundred tons per hour to more than 10,000 tons per hour. Types of Primary Jaw Crushers. There are two main types of primary jaw …
اقرأ أكثر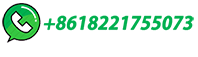
CG820 Primary Gyratory Crusher For Safe Crushing …
CG820i crusher offer excellent reliability and safer & faster maintenance – up to 30% faster than competing crushers. A robustly designed one-piece main shaft and reinforced shells are made for tough use. The one-piece spherical spider bearing offers 5 times longer wear life than competing spider bushing design.
اقرأ أكثر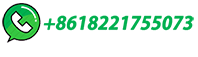
Crushing Technologies
Travel distances and the number of trucks can thus be optimized to the greatest possible extent, thus also reducing CO2 emissions. At the new Yamama Cement Co. site, not only two of our mobile crushers are used, but also three stationary impact crushers for additives, two jaw crushers for iron ore and one roller crusher for clinker.
اقرأ أكثر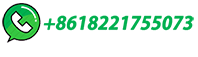
Primary Crusher Selection & Design
Primary crushers with crush run-of-mine rock from blast product size to what can be carried by the discharge conveyor or fit/math the downstream process. A typical example of primary crushing is …
اقرأ أكثر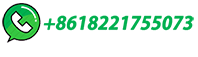
Crusher
Crusher. Crushers are machines that use a rigid surface to compress and break large rocks into smaller rocks. From: Iron Ore, 2015. About this page. Add to Mendeley. Set alert. ... There are two main types of primary crushers in metalliferous operations: jaw and gyratory crushers, although impact crushers have limited use as primaries and will ...
اقرأ أكثر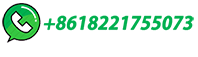
Used Crushers for Sale | Mining | | Surplus Record
USA and Canada's #1 source for used and surplus crushers for the mining and minerals. All types available and in stock from mining equipment dealers near you. go to top. Skip to main content ... 42" x 86" #XHD Primary Gyratory Crusher With 600 HP (450 KW), 60 Hz. A M King Industries | Oroville, CA. 530-53... (Show) 530-534-7965 ...
اقرأ أكثر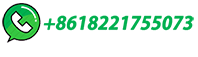
Understanding the Difference Between Primary …
A primary crusher is the initial stage of the crushing process that reduces large rocks or stones into manageable sizes. Secondary crushers, on the other hand, take smaller rocks or stones …
اقرأ أكثر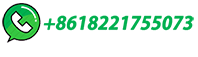
What Are the Differences Between The 7 Types of Crushers?
The ultimate mission of primary crusher is done. Horizontal shaft impact crusher (HSI) VS cone crusher ... The final product prices of the two crushers are also different. The VSI crusher making sand is much higher than the latter. VSI crushers make limestone into Manufactured sand in India
اقرأ أكثر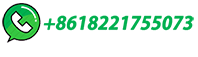
Impact Crushers
Impact Crushers - Primary. Impact Crushers create material reduction by providing a sudden impact force that causes the material to shatter along all the weakest fissures in the stone. Controlling the flow of the material through the Impact Crusher requires features that vary from one style of impactor to another, and this is what separates ...
اقرأ أكثر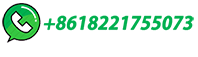
Gyratory Crushers
Gyratory Crushers. The primary rock breaker most commonly used in large plants is the gyratory crusher, of which a typical section is shown in Fig. 5. It consists essentially of a gyrating crushing head (521) working inside a crushing bowl (522) which is fixed to the frame (501).
اقرأ أكثر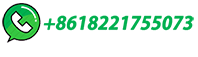
Large Capacity Gyratory Crushers for Primary Crushing
2. Gyratory Crusher Vs. Cone Crusher Gyratory crushers and cone crushers are important crushing equipment in the mining and aggregates industries. They are both used to break down large rocks into smaller ones. However, there are 4 differences between them: a. Gyratory crushers are primary crushers that break the largest rocks into …
اقرأ أكثر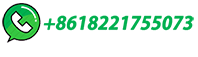
Primary Crusher
4.2.2 Jaw Crusher Circuits. Primary jaw crushers typically operate in open circuit under dry conditions. Depending on the size reduction required, the primary jaw crushers are followed by secondary and tertiary crushing. The last crusher in the line of operation operates in a closed circuit. That is, the crushed product is screened and the ...
اقرأ أكثر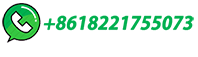
Types of Crushers: What You Need to Know | Machinery …
The three main stages of crushing are primary, secondary, and tertiary - all of which have their own unique benefits. Primary crushing involves using a large object as the initial …
اقرأ أكثر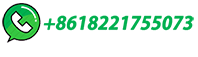
What Crusher Should You Choose for Primary Crushing?
An ideal primary crusher can not only handle the toughest materials with ease, but also ensure a stable high output. In this article, FTM Machinery introduces different types of primary crushers, their working principles, and advantages to help you choose the best one for your needs, transforming your operations and staying ahead of …
اقرأ أكثر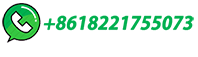
The Ultimate Guide to Rock Crushers
• Jaw crushers are used for primary crushing. • Cone crushers are used for secondary crushing and fine crushing. • Impact crushers are used for primary and secondary crushing. • Gyratory crushers are used for heavy-duty crushing. Let's delve deeper into each type. Jaw Crushers Jaw crushers are perhaps the most common type …
اقرأ أكثر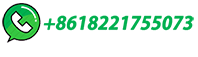
Roll Crushers
Single Roll Crushers. Single Roll Crushers are typically used as primary crushers that provide a crushing ratio of up to 6:1. They crush materials such as ROM coal, mine refuse, shale, slate, gypsum, bauxite, salt, soft shale, etc., while producing minimal fines.Designed with intermeshing roll teeth and a curved crushing plate, they are extremely effective in …
اقرأ أكثر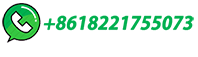
Primary Impact Crushers – MEKA
Primary Impact crushers have proven their effectiveness in a host of missions like crushing low abrasive materials for quarrying, cement industry, concrete and asphalt recycling, and slag recycling. ...
اقرأ أكثر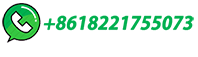