Vertical Roller Mill (VRM)
2018 Target Operating Hours in Cement industry S.No. Department Operating hrs/Day 1. Mines* 10 2. Crusher* 10 3. Raw Mill (Ball mill, VRM) 21 Raw mill (Roller press) 20 4. Coal mill (Ball mill, VRM) 21 5. Kiln 24 6. Cement Mill (Ball mill, VRM + …
اقرأ أكثر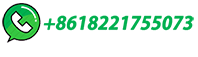
Everything you need to know about cement Materials Preparation and Raw
The effect of this trend on the manufacture of vertical roller mills is shown in Figure 2.3.23 (Jung, 1999), which indicates that mills having capacities in the range of 400 to 600 tph with drive ratings between 4000 to 5000 kW have already been produced; the operating experience of running vertical roller mills with output ranges of 630 to 650 ...
اقرأ أكثر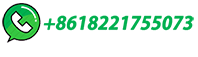
(PDF) The latest innovative technology for vertical roller mills
For decades vertical roller mills have been in use in the cement industry for the grinding of cement raw material and coal. Since the 1980's this mill type has also been used for combined or ...
اقرأ أكثر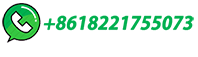
Operational parameters affecting the vertical roller mill …
Vertical roller mills (VRM) have found applications mostly in cement grinding operations where they were used in raw meal and finish grinding stages and in power plants for coal grinding. The mill combines crushing, grinding, classification and if necessary drying operations in one unit and enables to decrease number of equipment …
اقرأ أكثر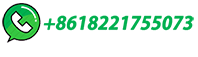
Roller Press
Simply put, the roller press is the most energy-efficient grinding machine on the market. Since its commercial introduction into the cement industry by KHD in the 1980s, hundreds of them have been installed in the cement and minerals industries, in both finish and semi-finish applications. And with the lowest specific energy consumption among comparable …
اقرأ أكثر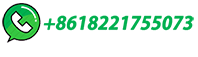
Raw milling and blending
The main difference to cement mill operation is the need to dry raw·feed and assure transport of stightly moist materialwithin a mill. Also, many raw materials are softer than clinker, and operations must avoid coarse residues in kiln feed that are difficult to combine in the kiln and would result in high clinkerfree-lime, and/or excessive ...
اقرأ أكثر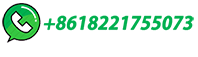
VRM – AMCL Machinery Limited
Individual large air swept Vertical Mills are preferred over ball mills for better grinding efficiency and to get an advantage in power consumption. Cement raw material is the mixture of mainly Limestone & other constituent such Iron oxide, Shale etc. having different moisture contain depending on composition & deposit.
اقرأ أكثر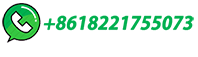
Technical Notebook CEMENT ADDITIVES FOR VERTICAL …
operation costs, vertical mills have made their way into the cement industry. At first, these new systems were employed for the grinding of solid combustibles and kiln-feeding raw meal. In the past decade, however, the new generation of vertical mills has demonstrated to be a competitive solution for final cement grinding as well.
اقرأ أكثر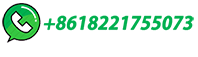
Raw Mill in Cement Plant | Cement Manufacturing Raw …
Pre-Blending and Raw mill Stage Limestone from mines are brought to plant site and stored in the yard then fed to dump hopper of primary crusher by mixing high-grade and low-grade limestone in defined proportion to meet the quality norms.
اقرأ أكثر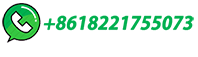
Important operation parameters in Vertical mill
Important operation parameters in Vertical mill TO DOWNLOAD THE EXCEL SHEET AND ALL THE OTHER USEFUL BOOKS AND RESOURCES KINDLY CLICK HERE Feed rate to mill, production rate [t/h]. Mill differential pressure [mbar] Grinding bed thickness with span [mm]. Amount of external material recirculation [t/h, or BE current A] Gas flow …
اقرأ أكثر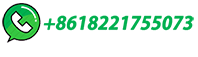
Vertical Roller Mill for Cement Raw Material – SBCCO-CEMENT
Vertical Roller Mill. Vertical Roller Mill for Cement Raw Material; Cement Mill, Clinker Mill; Slag Mill; Coal Grinding Mill; Ball Mill; Rotary Kiln; Grate Cooler; Hydraulic Roller Press(HRP) Spare Parts; ... stable operation and can feed continuously. The wear-resistant liner of the housing is machined metal, featuring high precision; the gap ...
اقرأ أكثر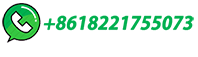
Gebr. Pfeiffer vertical mills with MultiDrive®
The MultiDrive?, which has proven successful in industrial operation since 2008, was developed by Gebr. Pfeiffer in cooperation with Siemens/Flender especially for the MVR mill. In cement industry, while considering large and extra-large capacity solutions, the most important point for grinding raw material, cement and granulated …
اقرأ أكثر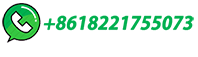
Arabian Cement Company
•One raw materials vertical grinding mill (520 tph) •Five stage pre-heater, kiln and cooler system (capable of producing between 6,600-7,000 tpd each) •One clinker silo (35,000 tons) •Two horizontal cement mills (190 tph) •Two cement silos (16,000 tons each) •Packing unit comprising of 3x120 tph packers and four bulk loading outlets ...
اقرأ أكثر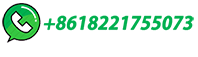
Cement Raw Vertical Mill Area Maintenance
Cement Raw Vertical Mill Area Maintenance Dam Ring. There is high wear and deformation in the dam ring segments. new dam ring segments . worn out and deformed dam rings segments . Recommendation: Replace the dam ring segments with a new one. Action has been taken: The defected dam ring has been replaced. Thermo cable for …
اقرأ أكثر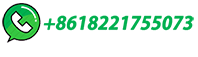
Parts of Vertical Roller Mill
Vertical Roller mills. Vertical Roller mills Main parts of a vertical roller mill Mill body feed Hydraulic system Nozzle and retention ring mill body seperator Vertical roller mill: frame type Polysius: Polroll Gbr. Pfeiffer: MPS Vertical roller mill: rocker arm type Loesche: LM : OK Processes inside a vertical roller mill Grinding…
اقرأ أكثر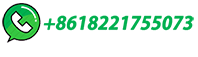
EVALUASI KINERJA VERTICAL ROLLER MILL (Cement Mill)
Pada Vertical Cement Mill terjadi empat proses yang berlangsung secara simultan. Keempat proses tersebut yaitu penggilingan, pengeringan, transport, dan separasi. Proses penggilingan, pengeringan ...
اقرأ أكثر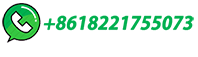
PROCESS TRAINING for operators of Vertical RAW …
PROCESS TRAINING for operators of Vertical RAW Mills. Heating of mill and grinding plant. In fact there are three processes going on in the MPS mill namely grinding, drying and clas sifying, and only when all three …
اقرأ أكثر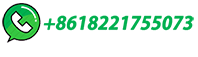
Assessment of the thermodynamics efficiency of a cement vertical raw
Table 10 shows both the inlet and outlet streams of the vertical raw mill process and their mass and energy balances. According to Table 3, the cement vertical raw mill system has an energy efficiency of 67.3 percent. Energy efficiency percentages in this study followed a similar pattern, with estimated values between 60 and 70%.
اقرأ أكثر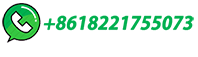
OK™ mill The most reliable and efficient mill for raw …
FL has supplied the global cement industry with leading Vertical Roller Mill (VRM) designs for raw, fuel and cement grinding for several decades. The OK™ mill has been FL's standard cement VRM since 1993.
اقرأ أكثر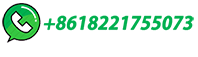
National Cement Company inaugurates upgraded Ragland …
The National Cement Company of Alabama unveiled its new US$300 million ultra-modern production line on July 21st 2022. ... During 2021, crews simultaneously erected a vertical raw mill, a preheater tower with an advanced kiln line and cooler, an automated clay storage system, an alternative fuel storage facility and finally, a fully …
اقرأ أكثر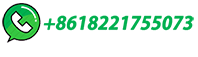
(PDF) Thermodynamic Analysis of Raw Mill in Cement
The simulator was used for the thermodynamic performance of a raw mill (RM) and raw materials preparation unit in a cement plant in Nigeria using actual operating data. The raw mill has a capacity ...
اقرأ أكثر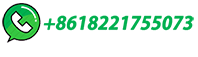
(PDF) CEMENT RAW MATERIAL GRINDING ; …
Grinding aids are materials that are added to cement mixtures to improve the characteristics of the cement or increase the efficiency of the milling systems or both in the clinker grinding (finish grinding) stage.
اقرأ أكثر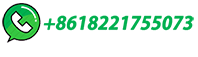
PROCESS OPTIMISATION FOR LOESCHE GRINDING …
Loesche – Innovative Engineering. The core elements of these plants are the Loesche vertical mills for dry-grinding the above-mentioned grinding stock. Loesche has …
اقرأ أكثر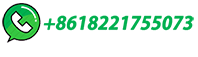
Vertical Roller Mill Operation in Cement Plant
The vertical roller mill or vrm cement mill is a popular equipment for raw material processing and cement grinding. Here are some factors we should pay attention to during the operation of vertical roller mill in cement plant.
اقرأ أكثر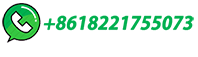
Vertical roller mill for raw Application p rocess materials
At the beginning stage when vertical roller mill was adopted to cement manufacturing, mill gas circulation fan and dust collection fan are required and their ... Vertical Raw Mill EP Raw Mill EP fan 69 - 4 - Item Pre-grinding equipment for raw ... it is expected that operation in the daytime can be shortened and then power cost can be reduced. Cost
اقرأ أكثر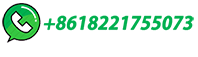
PROCESS CONTROL FOR CEMENT GRINDING IN VERTICAL ROLLER MILL …
The power ingesting of a grinding process is 50-60% in the cement production power consumption. The Vertical Roller Mill (VRM) reduces the power consumption for cement grinding approximately 30-40% associated with other grinding mills. The process variables in cement grinding process using VRM are strongly nonlinear and having large time …
اقرأ أكثر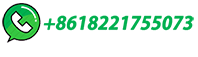
Vertical roller mill for raw Application p rocess materials
In the cement grinding process, the vertical roller mill having high grinding performance is applied especially cement grinding instead of the conventional tube mill. For further …
اقرأ أكثر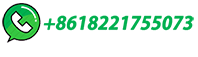
Important Operation Tips For Cement Vertical Mill
Mill System Operate Safety. When the raw material is running in the vertical mill, the drying heat source of the material comes from the hot gas at the kiln tail. Therefore, when the vertical mill is operated, the control of the inlet …
اقرأ أكثر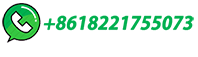
Cement Application Page
The Vertical Raw Mill (VRM) is a pivotal component in the grinding process within a cement plant. Efficient control and optimization of this process are critical for the quality of the …
اقرأ أكثر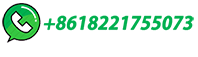
Energy and exergy analyses for a cement ball mill of a new …
Nowadays, ball mills are used widely in cement plants to grind clinker and gypsum to produce cement. In this work, the energy and exergy analyses of a cement ball mill (CBM) were performed and ...
اقرأ أكثر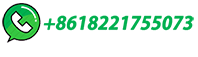