AMIT 135: Lesson 7 Ball Mills & Circuits – Mining Mill …
Mill Type Overview. Three types of mill design are common. The Overflow Discharge mill is best suited for fine grinding to 75 – 106 microns.; The Diaphram or Grate Discharge mill keeps coarse particles within the mill for additional grinding and typically used for grinds to 150 – 250 microns.; The Center-Periphery Discharge mill has feed reporting from both …
اقرأ أكثر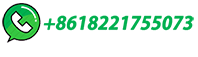
Ball Mill Success: A Step-by-Step Guide to Choosing the Right Grinding …
Additionally, evaluate the milling conditions, including the type of mill, speed, duration, and whether the process is wet or dry. These factors will influence the selection of the most suitable grinding media. Step 2. Comparing Media Types: With a clear understanding of the milling requirements, compare the different types of grinding …
اقرأ أكثر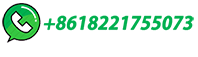
A Review of the Grinding Media in Ball Mills for Mineral …
Although there are several types of grinding media, which include inert grinding media such as ceramic, zirconia, agate, and glass, this section is going to focus on cast iron and steel grinding media, together with their applicability in ball mills.
اقرأ أكثر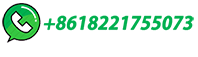
Mechanistic modeling and simulation of grinding iron ore …
DOI: 10.1016/J.POWTEC.2021.07.030 Corpus ID: 237666917; Mechanistic modeling and simulation of grinding iron ore pellet feed in pilot and industrial-scale ball mills @article{Carvalho2021MechanisticMA, title={Mechanistic modeling and simulation of grinding iron ore pellet feed in pilot and industrial-scale ball mills}, author={Rodrigo M …
اقرأ أكثر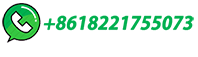
Research of iron ore grinding in a vertical-roller-mill
Pilot scale mill LM4.5. For the grinding tests, a Loesche mill LM4.5 (table diameter 0.45 m) is used (Fig. 2a). This pilot scale mill is a special development for ore grinding, which is reflected by several features. The mill has four rollers, which are able to stress the particle bed with grinding pressures of up to 5000 kN/m 2. Various ...
اقرأ أكثر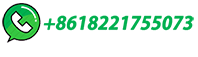
Grinding Media in Ball Mills for Mineral Processing
In both types of mills, a portion of the charge is lifted along the perimeter of the shell during the mill rotation and, after exceeding the angle of repose, part of it slides down while the other part cataracts and drops to the toe of the shell, imparting the grinding action in the process. ... together with their applicability in ball mills ...
اقرأ أكثر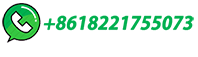
Ball Mill Grinding Media Options | Ceramic Balls …
There are different types of steel ball mills, they are, cast nickel alloys, stainless steel. They are usually applied in the grinding process of copper, gold, iron ore and polymetallic. Steel ball grinding media are used in …
اقرأ أكثر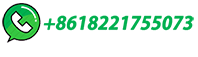
Investigation on Iron Ore Grinding based on Particle Size Distribution
The feed samples of X, Y, and Z iron ores were ground in the BBM (ball mill refers to a BBM of size 300 mm × 300 mm with smooth liners) to identify the PSD, BWI, and RT of each ore. Grinding experiments were conducted according to Bond's standard test procedure [].For each iron ore sample, the RT taken to produce 250% circulating …
اقرأ أكثر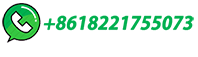
Wet Overflow Type Ball Mill and Applications
How Overflow Type Ball Mill Works. Material Feed: The raw material is fed into the mill at one end and travels through the mill by rotation. The feed enters the mill at a specific rate, ensuring a controlled grinding process.; Grinding Process: As the mill rotates, the grinding media crushes and grinds the material into a fine powder. The wet …
اقرأ أكثر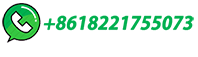
Ball Mill Grinding Theory – Crushing Motion/Action Inside
The object of this test was to determine the capacity of the ball-mill crushing in closed circuit and producing 200-mesh material. The conditions were as follows: Feed rate, 7.37 T. per hr. Ball-mill power, 108 kw. Classifier, Dorr duplex bowl-type. Feed, minus ¼-in. ore. Ball load, 28,000 lb. of 2- and 2 3/8-in. balls.
اقرأ أكثر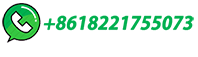
Mining Balls: The Backbone of Material Processing
Grinding Balls: Grinding balls are spherical components used in grinding mills to crush and grind raw materials, turning them into fine powders. These balls are essential in the mining industry to extract valuable minerals from ore. Steel Grinding Balls: Steel grinding balls are a subset of grinding balls, specifically made from high-quality …
اقرأ أكثر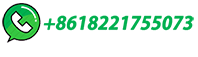
Grinding Mills — Types, Working Principle & Applications
Semi-Autogenous Mills/ SAG Mills (primary grinding mill) — these mills use grinding balls with forces of attrition, impact, and abrasion between grinding balls and ore particles that result in ...
اقرأ أكثر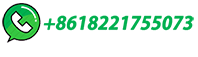
Friction and wear of liner and grinding ball in iron ore ball mill
An iron ore mill relies on the grinding and impact of grinding balls to complete iron ore crushing. The operating process of an iron ore mill is as follows: first, the ores are poured into the mill, and both the ores and the grinding balls are lifted by the lifting bar arranged on the wall of the cylinder body to a certain height, after which they …
اقرأ أكثر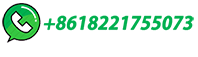
What Is a Ball Mill and How Does It Work?
A ball mill and a tumbling mill are both types of grinding mills used to reduce material size. We mainly use a ball mill for mixing and grinding processes. In contrast, we generally use a tumbling mill for finer material reduction. What are the balls? Ball mills grind materials into an extremely fine form.
اقرأ أكثر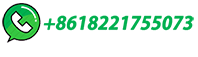
Ball Mills
Ball mills have been the primary piece of machinery in traditional hard rock grinding circuits for 100+ years. They are proven workhorses, with discharge mesh sizes from ~40M to <200M. Use of a ball mill is the …
اقرأ أكثر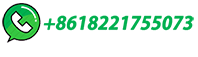
The Effect of Grinding Media on Mineral Breakage Properties …
2.2. Grinding Test. In this paper, the wet ball milling process was used in the laboratory ball milling test. Before grinding, the ball mill was kept idle for 10 minutes and then washed together with the grinding media. Three types of ores were crushed and separated by a jaw crusher, and the ground particle size of -2 mm was selected.
اقرأ أكثر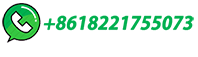
Metallurgical Testing for Iron Ore
• Train critical mill staff experience SGS Minerals Services has run over 20 semiautogenous grinding (SAG) and metallurgical pilot plants on iron ores, including extremely large plants treating up to 1,000 tonnes of ore and lasting for 6 months. Many complex circuits using autogenous grinding, de-sliming, magnetic separation, gravity separation,
اقرأ أكثر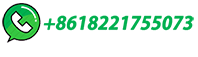
Closed and Open Circuits Ball Mill for Cement, …
We bring forth a highly advanced Ball Mill, specifically engineered for both wet as well as dry cement grinding applications. Classified depending on the circuit design, bearing, grinding type and drive, the selection is …
اقرأ أكثر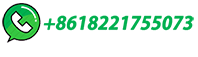
The effects of iron ore concentrate grinding methods (HPGR and Ball
An iron ore concentrate sample was ground separately in a pilot-scale HPGR mill in multiple passes and a dry open-circuit ball mill to increase the specific surface area of particles.
اقرأ أكثر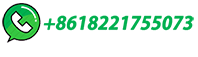
Buy Ore Ball Mill for Mineral Processing | Iron & Gold Ore Ball Mill
Ore ball mill sometimes called ore grinding mill, is generally used in mineral processing concentrator, processing materials include iron ore, copper ore, gold ore, molybdenum ore and all kinds of nonferrous metal ore.The core function of the ore ball mill is to grind the materials, and also to separate and screen different mineral materials, and to separate …
اقرأ أكثر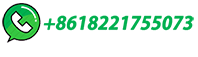
Experimental investigation of the impact breakage …
DOI: 10.1016/j.apt.2023.103982 Corpus ID: 257196294; Experimental investigation of the impact breakage characteristics between grinding media and iron ore particle in ball mills
اقرأ أكثر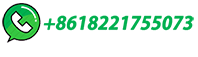
Consumption of steel grinding media in mills – A review
Albertin and Sinatora (2001) have considered the effect of carbide volume fractions from 13% to 41% and matrix microstructure on the wear of 50 mm diameter cast iron balls tested in a laboratory ball mill during wet grinding of hematite, phosphate rock and quartz sand. Martensitic, pearlitic and austenitic matrices were evaluated.
اقرأ أكثر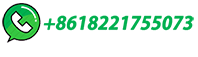
Grinding Mills
In Fig. 1.3 is shown a large ball mill, designed for the dry grinding of limestone, dolomite, quartz, refractory and similar materials; this type of mill being made in a series of sizes having diameters ranging from about 26 in. to 108 in., with the corresponding lengths of drum ranging from about 15 in. to 55 in.
اقرأ أكثر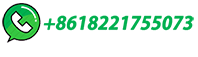
Autogenous Grinding & Semi Autogenous …
ABC closed circuit, Autogenous-Ball-Mill-Crusher. Another similar technique is the ABC open circuit where the crusher product feeds the ball mill rather than the autogenous mill. Crusher product is typical …
اقرأ أكثر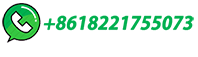
Experimental investigation of the impact breakage …
The drop-ball apparatus can simulate the impact contact behavior between steel ball and particle in the ball mill. The effect of particle size, impact energy, and impact number on the iron ore particle impact breakage characteristics were analyzed to reveal the particle breakage behavior in the ball mill.
اقرأ أكثر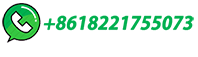
Friction and wear of liner and grinding ball in iron ore ball mill
Introduction. An iron ore mill relies on the grinding and impact of grinding balls to complete iron ore crushing. The operating process of an iron ore mill is as follows: first, the ores are poured into the mill, and both the ores and the grinding balls are lifted by the lifting bar arranged on the wall of the cylinder body to a certain height, after which …
اقرأ أكثر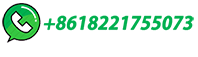
Friction and wear of liner and grinding ball in iron ore ball …
To understand the friction and wear of working mediums in iron ore ball mills, experiments were conducted using the ball cratering method under dry and wet milling …
اقرأ أكثر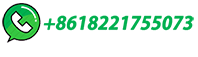
Grinding Ball Design
In ball mills, balls take up most of charge volume and are the major ore grinding components. The balls do most of the ore size reductions, unlike SAG mills …
اقرأ أكثر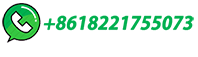