sbm/sbm modern maitenance of mining equipment in cement …
You've already forked sbm 0 Code Issues Pull Requests Packages Projects Releases Wiki Activity
اقرأ أكثر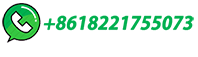
Clinker grinding technology in cement manufacturing
Clinker grinding technology is the most energy-intensive process in cement manufacturing. Traditionally, it was treated as "low on technology" and "high on energy" as grinding circuits use more than 60 per cent of total energy consumed and account for most of the manufacturing cost. Since the increasing energy cost started burning the benefits …
اقرأ أكثر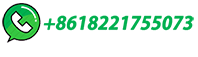
Industrial Fan solutions for Cement industry …
Raw Mill Exhaust Fans. Raw mill exhaust fans/ stack fans also known as de-dusting fans handle 2.2 tons of exhaust gases for the production of 1 ton of clinker. Raw mill exhaust fans are operated in a …
اقرأ أكثر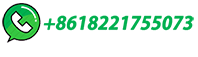
Raw mill
Raw mill is generally called cement raw mill, raw mill in cement plant, it refers to a common type of cement equipment in the cement plant.In the cement manufacturing process, raw mill in cement plant grind cement raw materials into the raw mix, and the raw mix is sent to the cement kiln to make cement clinker, next, clinker and other …
اقرأ أكثر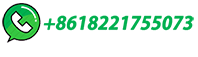
Baghouse in Cement Plants: Understanding How They Work …
Baghouses are designed based on the size of the cement baghouse building and the volume of the dust emissions. Large plants tend to have more numerous and larger baghouses than small plants. For example, a cement plant that has a production capacity of 1 million metric tons per year will have around six to eight baghouses.
اقرأ أكثر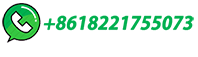
Key factors in setting up a cement plant
Setting up a cement plant is both time and capital intensive; it could take anywhere between five to seven years from concept to commissioning and an investment of around to Rs 1,800-2,000 crore for a typical integrated plant of 3 million tpa cement capacity. Size of a cement plant could vary from 0.2 million tpa to 5.0 million tpa.
اقرأ أكثر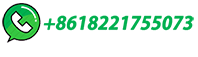
Main Fans in Cement plant
Previous Post Next Post Contents1 Main Fans in Cement plant1.1 Things that I want to talk about…1.2 Learning Objectives1.3 Enormous power consumption by main fans1.4 The lower the dust load the better the fan can be1.5 power consumption Equation for Main Fans1.5.1 Saving money with high efficiency fans1.6 Fan performance curves to be …
اقرأ أكثر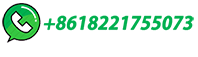
Coal Mill in Cement Plant
The ball mill is a traditional coal pulverizer machine, which has been widely used since it was invented. In the cement plant, the new dry process cement manufacturing requires the moisture content of coal powder to be 0.5% ~ …
اقرأ أكثر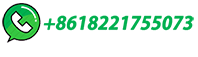
Ball Mill Maintenance In Cement Factory
Ball Mill Maitenance In Cement Factory. Most of the cement ball mills are used in the circulating grinding system which is characterized by high grinding efficiency large mill output and low power consumption Especially when 1 fine maintenance for 1 month; 2 minor maintenance 1 3 months; 3 medium maintenance 12 – 24 months; 4 large ...
اقرأ أكثر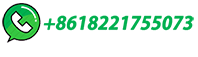
Dust Emission Monitoring in Cement Plant Mills: A Case …
This paper is a case study of a Portland cement plant in Romania, the experimental determinations presented mainly focusing on dust emissions in an important sector of the plant (cement mill and related facilities), with dust extraction from two chimneys in working areas (cement mill filtration system and grinder component …
اقرأ أكثر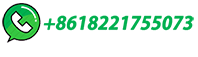
Dalmia Bharat boosts capacity with new cement mill of 1
New Delhi, May 17, 2024: Dalmia Bharat Limited (DBL), a leading Indian cement major announced the installation of a new cement mill at its existing cement manufacturing unit in Ariyalur, Tamil Nadu. This new unit adds 1.0 million tons of cement capacity to the company's overall installed capacity, bringing it to a total of 45.6 million tons ...
اقرأ أكثر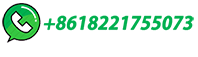
BALL MILL MAINTENANCE
Imagine an online classroom that takes you to learn at your own pace, allowing more choices with your learning opportunities. The Cement Institute is dedicated to providing the most dynamic and engaging programs available, as our enhanced online experience demonstrates an interactive and hands-on knowledge applicable directly to your plant.
اقرأ أكثر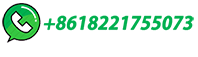
Applications and Maintenance Practices
Furthermore, the integration of hydraulic hose systems with Industry 4.0 initiatives is set to revolutionize steel plant operations. This entails a comprehensive interconnection of machines, processes, and systems, creating a smart …
اقرأ أكثر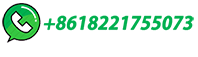
How to Start a Cement Factory
A cement ball mill is ready for transportation. There are many kinds of industrial equipment used in a cement plant, including thermal equipment, grinding equipment, dust removal system, transportation system, storage system, and so on.When placing an order, we may need to order different equipment from multiple manufacturers at the same time.
اقرأ أكثر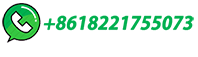
Auxiliary Equipment
AGICO CEMENT is a cement plant manufacturer supplies cement equipment with high quality and competitive price, including cement mill, cement kiln, cement crusher, and other cement plant equipment. any …
اقرأ أكثر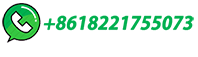
How Is Cement Produced in Cement Plants | Cement …
The cyclone preheating system Phase IV: Calcination. The calcination is the core phase of the cement making dry process. The calcination of the preheated raw meal takes place in the rotary kiln of the cement plant. The rotary kiln is a huge rotating furnace in which the raw meal is heated up to 1450 ⁰C and turned to clinker.
اقرأ أكثر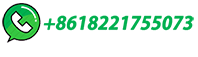
Digitization and the future of the cement plant | McKinsey
There's never been a more important time to build resilience into the core of the cement value chain: the cement plant. The cement industry is being hit hard by the COVID-19 pandemic, with global demand for cement expected to decline by 7 to 8 percent in 2020—though these declines have been unevenly distributed across regions. 1 Paul …
اقرأ أكثر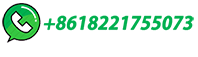
The Cement Plant Operations Handbook
The Cement Plant Operations Handbook is a concise, practical guide to cement manufacturing and is the standard reference used by plant operations personnel …
اقرأ أكثر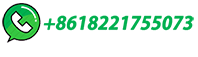
12630 ball mill maitenance in cement factory pdf
Crusher Plant. ball mill maitenance in cement factory pdf.Mixer Mill – High-energy ball mills for pulverizing brittle materials, mixing of cement, ores, ceramics and other materials for analysis by XRF, AA, ICP and wet. Read More …
اقرأ أكثر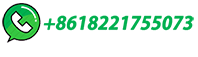
Predictive Maintenance for Cement Industry
Predictive Maintenance as a Service uses IIoT and sensor data to predict machinery failures before they occur, enabling proactive maintenance strategies in …
اقرأ أكثر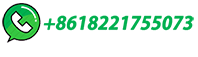
The Cement Plant Operations Handbook
The Cement Plant Operations Handbook is a concise, practical guide to cement manufacturing ... Finish mill – 12. Cement – 13. Quality control – 14. Packing and distribution – 15. Emission abatement (dust, NO x, SO 2, etc) – 16. Maintenance – 17. Process – 18. Materials analysis –19. Plant capacity summary – 20.
اقرأ أكثر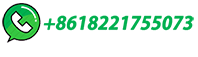
The cement mill
Cement manufacturing - brief description of a cement mill. Cement clinker is usually ground using a ball mill. This is essentially a large rotating drum containing grinding media - normally steel balls. As the drum rotates, the motion of the balls crushes the clinker. The drum rotates approximately once every couple of seconds.
اقرأ أكثر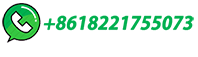
How Cement is Made
Stage of Cement Manufacture. There are six main stages of the cement manufacturing process. Stage 1: Raw Material Extraction/Quarry The raw cement ingredients needed for cement production are limestone (calcium), sand and clay (silicon, aluminum, iron), shale, fly ash, mill scale, and bauxite. The ore rocks are quarried and crushed into smaller …
اقرأ أكثر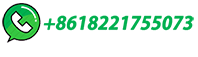
Cement
Cement - Extraction, Processing, Manufacturing: Raw materials employed in the manufacture of cement are extracted by quarrying in the case of hard rocks such as limestones, slates, and some shales, with the aid of blasting when necessary. Some deposits are mined by underground methods. Softer rocks such as chalk and clay can …
اقرأ أكثر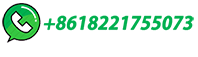
Evaluation of Carbon Emission Factors in the Cement …
The cement industry is a major contributor to carbon emissions, responsible for 5–8% of global emissions. This industry is expanding, particularly in emerging economies, and it is expected that CO2 emissions will rise by 4% by 2050. To address this critical concern, this paper identifies ten factors that contribute to carbon emissions in …
اقرأ أكثر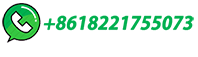
Cement mill maintenance best practices :a guide on best …
Effective maintenance of cement mills is crucial for ensuring high levels of productivity, reliability, and operational efficiency. By following best practices, cement plant operators can minimize downtime, reduce costs, and extend the lifespan of their equipment.
اقرأ أكثر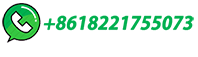
Raw Mill Feeding
This is very important, particularly in the situation when the moisture content of raw material is on higher side and the deficiency of hot gas in mill can effect on mill throughput or reduce mill outlet material temperature below 80 o C. Rotary feeders (gravel gate), double flap valve are used to stop/minimize cold air leakage into mill system ...
اقرأ أكثر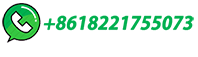
Predictive Maintenance in Cement Industry: Driving Plant …
Bearing and coupling faults in the gearbox of a cement mill can halt the cement plant production for up to 3 days. At the same time, structural looseness and …
اقرأ أكثر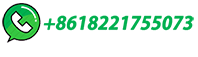
Cement Plant Machinery Manufacturers, Ball Mill …
At Supertech, our vision is to integrate our solutions according to our Customers' needs. And keeping this in mind, we manufacture and supply a varied range of Cement Plant Machinery for our Clients and have become a complete solution provider. Supertech has successfully emerged as a single stop for all kind of Cement plant machinery that are …
اقرأ أكثر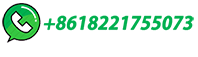
BALL MILL MAINTENANCE
This course offers an in-depth understanding of the maintenance activities, providing the precise tools to achieve optimal levels of personal performance and accomplishment, …
اقرأ أكثر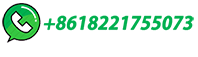