Ball Charge and Grinding Efficiency
Most SAG mill are not optimized for the combined SAG & Ball mill throughput such as: SAG & Ball mill % ball content SAG % ore content SAG grate size and end mill design including grate geometry, location, shape, pan cavity, recycle % in pan cavity, et. al. SAG lifter and end cone geometry - can change SAG mill performance more than 20%-50% ...
اقرأ أكثر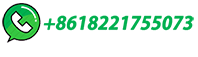
A Comprehensive Guide to SAG Mill Operation
SAG Mill Operation. SAG mills operate differently from ball mills, which rely on the impact of balls to break down the material. SAG mills use a combination of impact and attrition to grind the material. The grinding media in a SAG mill are larger than in a ball mill, and there are fewer of them per ton of ore.
اقرأ أكثر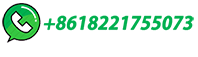
TECHNICAL AND COMMERCIAL BENEFITS OF GEARLESS …
general, the bigger the mill diameter, the lower are the mill operating and critical speeds. Thus, for larger mills the number of poles will increase. As a result, the number of poles can vary from 48 to 72 poles (Fig. 3.) with typical mill speed requirements of about 10 rpm for larger SAG mills and about 15 rpm for smaller ball mills. Figure 3.
اقرأ أكثر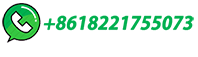
Understanding the SAG Mill in Copper Ore Mining Process
Tower Mills were developed to overcome some of the limitations of both ball mills and SAG mills. They can handle finer feeds than ball mills and have higher energy efficiency thanks to their vertical design. However, Tower Mills are not without their drawbacks. The high cost of manufacturing and maintaining these mills makes them less common ...
اقرأ أكثر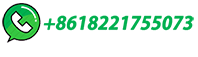
SAG Mill Design and Benchmarking Using Trends in the …
Figure 3(a)—Pilot SAG mill Ecs vs. Ball Load, Reproduced from Morrell (2006a); (b) SAG Mill Ecs vs. Ball Load for 'Open-Circuit' SAG Mills in JKTech Database 0 2 4 6 8 10 12 14 16 18 20 0 2 4 6 8 10 12 14 SAG mill Ecs (kWh/t) Ball load (%) 0 5 10 15 20 SAG mill Ecs (kWh/t) Ball load (%) Coarse feed, uncrushed pebbles Very soft ores, Axb >80
اقرأ أكثر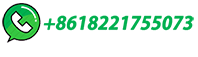
Semi-autogenous grinding (SAG) mill liner design and development
SAG mill liner development draws primarily on practical experience from SAG milling operations supported by computer-based modeling of charge motion in SAG mills and on established good design practice. Liner design needs to respond to the process aspects of mill liner action that are critical to good SAG mill performance, i.e., …
اقرأ أكثر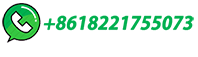
What is the Difference Between Attritor Mill and Ball Mill?
Key differences between attritor mills and ball mills. We explore their unique features, applications, and advantages to help you determine which is the best option for your specific milling needs. ... rod mill and AG/SAG mill for grinding in a variety of industries and materials. Contact. Email: info@ballmillssupplier; Tel: +86 ...
اقرأ أكثر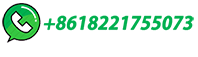
Semi-autogenous grinding (SAG) mill liner design and …
operation of SAG mills. SAG mills are currently the technology of choice in hard rock milling operations for reducing primary-crushed ore to ball mill feed. In recent years, the trend has been towards larger-sized SAG mills with diameters of 10.4 m (34 ft) and above, with the largest being 12.2 m (40 ft) in
اقرأ أكثر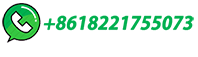
Ball, Pebble and SAG Mills: A Buyers Guide
The Ball Mill, the Pebble Mill and the SAG Mill are 3 of the most popular types of mills on the industrial market. They are primarily used for the Mining industry, but they can also be used in the Chemical & Processing industry which has it's own category page for those listings here: Ball, Pebble, SAG Mills for Chemical Use .
اقرأ أكثر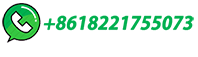
SAG mill compared to crusher and ball mill product size …
Batch experiments in a 0.6 m diameter mill have shown that improvements of about 13 per cent in the efficiency of energy utilisation can be realised in ball mills by replacing 25 per cent of the ...
اقرأ أكثر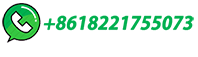
Ball Mill vs SAG Mill: What's the Difference?
SAG mills deal with larger rocks with a blend of rock particles and steel balls suitable for primary grinding though they consume more power. Ball mills employ steel …
اقرأ أكثر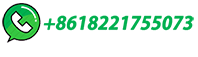
Improving SAG and Ball Mill Control in 4 hours
There are good and bad control techniques for SAG and Ball mill operation used in the industry. It is difficult to get an online measurement of ore hardness that can be used for process control.
اقرأ أكثر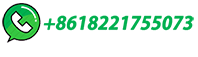
SAGDesignTM – Using Open Technology for Mill Design …
1.68 m diameter SAG mill test in Hibbing, Minnesota, one is not included in Table 2, and the other fivewere industrial plants, of which were single stage SAG mills and three were two various configurations of SAG and ball mills as indicated in Table 2 below.
اقرأ أكثر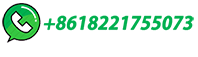
SAG Mill Grinding Circuit Design
By combining with SAG discharge and screening on the SAG discharge screens, top size control to the ball-mill circuit feed is maintained while still unloading the SAG circuit (Mosher et al, 2006). A variant of …
اقرأ أكثر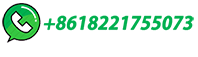
SAG Mill Testing
mill. As such, primary ball mills should be designed with the rod mill work index, and single-stage ball mills should be with both the rod mill and ball mill indices. This is because it is common to observe a difference (sometimes significant) between the rod mill and ball mill index values for a given ore type (McKen, Verret, & Williams, 2006). On
اقرأ أكثر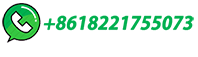
SAG Mill | Autogenous and Semi-Autogenous Mills
Rely on our proven track record of AG and SAG Mill superiority. Since the early 1980s, we have been designing and manufacturing Semi Autogenous Mill (SAG Mill) and Autogenous Mill (AG Mill) under the Fuller-Traylor brand. Semi-autogenous grinding uses a minimal ball charge in the range of 6-15% while autogenous grinding uses ore only.
اقرأ أكثر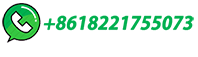
ball and sag mills
Most mills used in mining rely on impact to breakdown rock to a suitable size for downstream processing. The impact can be rock on rock such as in an Autogenous Grinding (AG) mill, rock and a small ball charge (~10%), used in Semi Autogenous Grinding (SAG) mills, balls of various sizes in Ball Mills and less commonly these days, …
اقرأ أكثر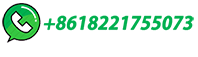
Charge segregation and slurry transport in long SAG …
The charge was emptied out from a SAG mill treating open cast UG2 ore. The mill is a single-stage RoM overflow SAG mill closed with a cyclone and a flash float cell with a re-circulating load of ...
اقرأ أكثر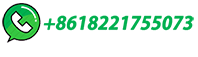
#139 – Semi-Autogenous Grinding (SAG) Mills | RPMGlobal
Perspective #139 – Some thoughts on Semi-Autogenous Grinding (SAG) Mills. Written by Richard Addison | Principal Process Engineer. This paper explores why SAG mills are an enigma when compared to ball mills, providing an in-depth analysis of how the advantages of SAG milling outweigh the shortcomings.
اقرأ أكثر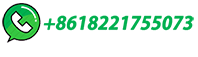
Understanding the SAG Mill in Copper Ore Mining Process
A SAG mill, or semi-autogenous grinding mill, is a type of machine used in mining and mineral processing operations. It uses the crushing and grinding action of rocks to …
اقرأ أكثر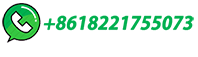
Design SAG mill production when you need it most: In …
INTRODUCTION. The purpose of this paper is to highlight and encourage the use of a recently developed and recommended approach to designing SAG mill grinding circuits …
اقرأ أكثر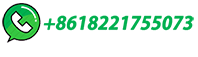
What's the Difference Between SAG Mill and Ball Mill
SAG mill: The SAG mill adopts a self-return device to realize the discharge of the mill. Ball mill: There are many types of ball mills, mainly including overflow ball …
اقرأ أكثر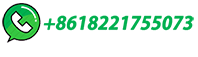
RoM BALL MILLS
RoM Ball mills, like SAG mills, utilise coarse rocks in the RoM feed as grinding media but with 25 – 40% steel balls added, which is advantageous when the coarse fraction in the RoM feed is ...
اقرأ أكثر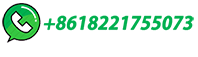
Ball Mill (Ball Mills Explained)
The following process description is based upon a ball mill used in the hard rock mining industry for liberating minerals from ore, but the operating principle for ball mills used in other industries is the same.
اقرأ أكثر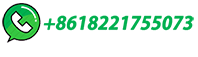
Closed Circuit Grinding VS Open Circuit Grinding
The simplest grinding circuit consists of a ball or rod mill in closed circuit with a classifier; the flow sheet is shown in Fig. 25 and the actual layout in Fig. 9. ... Difference between open circuit and closed circuit grinding. Single-stage grinding is generally to be recommended for small plants on account of its simplicity. Variations in ...
اقرأ أكثر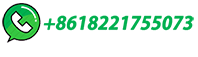
Key considerations when selecting a mill lining system | …
A comparison of SAG and ball mill charge actions is shown below. Figure 1 shows the sliding abrasion action of a ball mill while figure 2 depicts the cascading impact action of a SAG mill. The geometrical differences in the liner system lifters can also be seen. Figure 1: Sliding-abrasion action in a Ball Mill.
اقرأ أكثر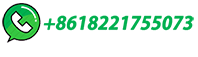
Difference Between Sag Mill Vs Ball Mill | PDF | Mill …
Difference Between Sag Mill vs Ball Mill - Free download as Word Doc (.doc / .docx), PDF File (.pdf), Text File (.txt) or read online for free. SAG mills and ball mills are both used for grinding materials into smaller pieces in mining and processing applications. SAG mills use steel balls and large rocks to grind large fragments into smaller pieces inside a rotating …
اقرأ أكثر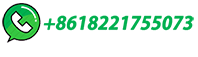
SAG Mill Liner Design
To a more significant degree than in other comminution devices, SAG Mill Liner Design and Configuration can have a substantial effect mill performance. In general terms, lifter spacing and angle, grate open area and aperture size, and pulp lifter design and capacity must be considered. Each of these topics has had a considerable amount of …
اقرأ أكثر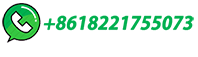
Impact on Grinding Mill Design of Recent New Discoveries
SAG and ball mill design energy measurements on many samples. These were compared with the ... at the data this way shows the extreme differences between ores at the same ball mill hardness. Fig. 4 - SAG Pinion Energy Vs Ratio of SAG / Bond BM Wi, with NICO, Aurora 0 4 8 12 16 20 24 28 32 36
اقرأ أكثر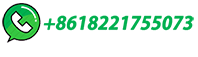
Design SAG mill production when you need it most: In …
Transfer Size, T80: Is the 80% passing size of ore as it passes from the SAG mill to the ball mill. It is typically about 1/3 the size of the screen opening but can be coarser than 1/3, especially when a pebble crusher is used. Screening at 5 mm ensures that the T80 will be about 10 mesh (1.7 mm) ensuring that the ball mill will work efficiently.
اقرأ أكثر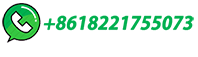