Delta Beryllium Plant | The Center for Land Use …
This large industrial plant in the remote Sevier Desert of western Utah is one of the only sources of concentrated beryllium in the world. The plant is a mill and finishing facility for beryllium, a high-strength, lightweight metal used in military, aerospace, and medical industries. The ore for the plant comes from Brush Wellman's mine, located in the …
اقرأ أكثر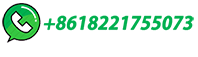
Ball Mills
Ball Mills. In all ore dressing and milling Operations, including flotation, cyanidation, gravity concentration, and amalgamation, the Working Principle is to crush …
اقرأ أكثر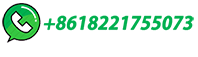
Gold Ore Roasting Plant
The blended ore is crushed in an open circuit – two-stage crushing plant (primary and secondary crushing) to produce coarse ore (80% passing ¾ inches and 97% passing 2 inches) to feed the dry grinding plant.
اقرأ أكثر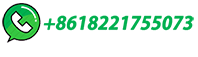
Gold Fields South Deep Gold Mine
When ore enters the plant from underground it first needs to be milled to reduce its size so that the gold is liberated from the host rock. South Deep's milling circuit consists of a single-stage semi-autogenous grinding mill (SAG) and a pebble crusher for primary milling, followed by secondary milling using two overflow ball mills.
اقرأ أكثر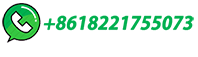
Iron Ore Supply Chain: From Mining to Steel Production
Iron ore is a crucial raw material for the global steel industry, and its supply chain is a complex network that involves multiple stakeholders and activities. The iron ore supply chain begins with the mining of iron ore, which is then transported to processing plants for beneficiation and further refinement. The refined iron ore is then transported …
اقرأ أكثر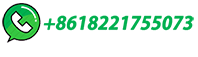
Gold Ore CIP CIL Processing Plant & Equipment Solution
In practice, maintaining the pulp pH value between 10.0 and 11.0 is crucial. The cyanide leaching rate of gold ore decreases if the pH value exceeds 12 due to excessive alkalinity or falls below 9 due to insufficient alkalinity.
اقرأ أكثر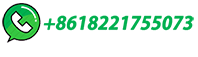
Winning the Metal: Ore Mills of the West
This article will focus on the most common type of ore processing facility – the stamp mill. An ore is any naturally occurring solid from which a metal or other commodity can be extracted for a profit. "For a profit" is the key …
اقرأ أكثر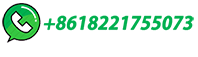
Iron Ore Facilities :: Cleveland-Cliffs Inc. (CLF)
At the plant, two additional stages of crushing occur before the ore is sent to the concentrator. The concentrator utilizes rod mills and magnetic separation to produce a magnetite concentrate, which is delivered to the pellet plant located on-site. The plant has a ship loading port located on Lake Superior.
اقرأ أكثر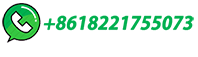
About Us
The facility was indefinitely idled in late 2019. Tin production has been shifted to Midwest Plant and Gary Works. United States Steel Corporation ... with an annual production capacity of 400,000 net tons. Mill No. 2 can produce pipe ranging from 1.088" to 7.15" OD with an annual capacity of 390,000 net tons. ... U. S. Steel's Minnesota ...
اقرأ أكثر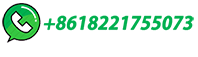
Understanding the SAG Mill in Copper Ore Mining Process
A SAG mill, also known as a semi-autogenous grinding mill, is one of the essential equipment used in copper ore mining. It plays a vital role in reducing large chunks of …
اقرأ أكثر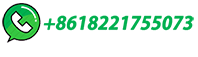
Copper Mining and Processing: Processing Copper …
This process uses a series of physical steps and high temperatures to extract and purify copper from copper sulfide ores, in four basic steps: 1) froth flotation, 2) thickening, 3) smelting, and 4) electrolysis.
اقرأ أكثر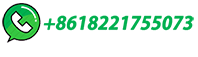
Ball Mill | Ball Mills | Wet & Dry Grinding | DOVE
DOVE ball mill is integrated and used in DOVE Portable and Semi-Stationary Hard Rock plants (Hard Rock processing plants) to efficiently grind the ore from primary deposit until the liberation size of valuable minerals is reached. DOVE ball mill is the key grinding equipment after material is crushed.
اقرأ أكثر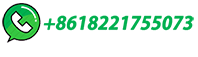
Ball Mill | Ball Mills | Wet & Dry Grinding | DOVE
DOVE ball mill is integrated and used in DOVE Portable and Semi-Stationary Hard Rock plants (Hard Rock processing plants) to efficiently grind the ore from primary deposit until the liberation size of valuable …
اقرأ أكثر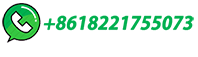
Recycling of steel plant mill scale via iron ore pelletisation process
Abstract. Mill scale is an iron oxide waste generated during steelmaking, casting and rolling. Total generation of mill scale at JSWSL is around 150 t/day and contains 60–70%FeO and 30–35%Fe 2 O 3.To recover the iron, the mill scale must be smelted in a blast furnace or other reduction furnace; however, it is usually too fine to …
اقرأ أكثر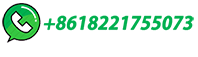
Crushing Plant Flowsheet & Design-Layout
The advantages of producing a fine mill feed have been recognized for many years. The extent to which fine crushing can be carried out will vary and depends on the ore characteristics, plant and crusher design. Unfortunately, the ore characteristics are generally beyond our control, so the concentration of effort lies primarily on the plant ...
اقرأ أكثر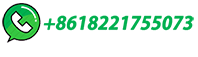
Ball Mill Is Indispensable For Lithium Ore Processing
The advantage of the grid type ball mill is that the ore discharge speed is fast, it can reduce the over-crushing of ore, and at the same time it can increase the output per unit volume. 1. Large row of …
اقرأ أكثر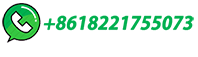
Crushing Plant Design and Layout Considerations
This paper addresses the critical design parameters as well as the consideration of ore characteristics, geographical location, climatic conditions, expected operational life, expansion ... on both greenfield and retrofit projects, to increase feed rate to the SAG mill. In other words, crushing plants, from primary to quaternary circuits, are ...
اقرأ أكثر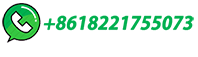
Recycling of steel plant mill scale via iron ore sintering plant
In similar conditions Rounak Sneh Anand et al., [42] prepared the green pellets using (90%) mill scale and (10%) slime fines and reduced it with coal fines and developed high-grade DRI which was ...
اقرأ أكثر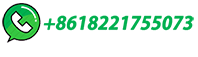
The six main steps of iron ore processing
When the material exits the mill, the iron ore is classified using cyclones or vibrating screens that separate fine and large particles. The large particles are diverted back into the crusher and the fine particles will undergo a spiral gravity separation process. 5. Spiral gravity separation
اقرأ أكثر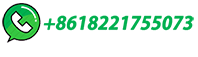
Feldspar Processing Plant
Raw feldspar ore information: contains iron, calcium, mica, and other impurities, so the feldspar ore dressing process including magnetic separation, flotation or gravity separation, so as to remove iron, mica and other impurities to obtain high-grade feldspar. 1. Crushing section: Utilize coarse jaw crusher, fine jaw crusher and vibrating screen to form a …
اقرأ أكثر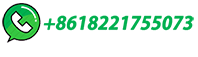
Lecture 11: Material balance in mineral processing
Roughly 7⁄ of water is required for a plant treating 10000 tons of ore. Two product is of great use in assessing water balances. In two product. divided in two products, namely concentrate and tailing. Consider a hydrocyclone fed with a slurry containing f q %
اقرأ أكثر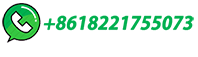
Ball Mill | Mining Grinding Mill
The ball mill is a tumbling mill that uses steel balls as grinding media. Ball mills can be used in wet or dry systems for bulk and continuous milling, and are most widely used in small or large-scale ore beneficiation plant.
اقرأ أكثر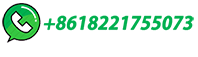
Understanding the SAG Mill in Copper Ore Mining Process
The rod mill is another type of grinding mill used in the copper ore mining process. This machine uses steel rods as the grinding media instead of balls, which are commonly used in ball mills. The rods grind the ore by tumbling within …
اقرأ أكثر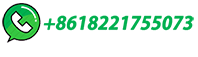
The Basics of How Ore Processing and Recovery …
The term processing and recovery plant is broad to say the least so we are going to give some basic examples of the types of ore processing plants. It is important to understand that each full ...
اقرأ أكثر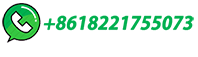
Iron Ore Processing: From Extraction to Manufacturing
b. Autogenous and Semi-Autogenous Mills: In some cases, autogenous (AG) and semi-autogenous (SAG) mills are used for grinding. These mills utilize the ore itself as the grinding media, reducing the need for additional grinding media. AG/SAG mills are typically used for coarse grinding, where large pieces of ore are efficiently broken …
اقرأ أكثر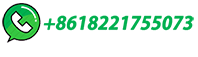
Bellary Steels & Alloys Limited
Bellary Steels & Alloys Limited is a leading player in the steel and alloys industry, known for its commitment to quality, innovation, and customer satisfaction.Late Sri. Singanamala Nagappa has started Blacksmith works, manufacturing Agriculture implementation in 1956. He went into backward integration by setting up first Re Rolling Mill in 1970 later added …
اقرأ أكثر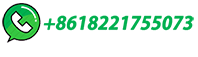
Winning the Metal: Ore Mills of the West
Some mills were as famous as the mines that supplied them. I will leave it to the interested reader or researcher to investigate this list of some of the more famous mills: The Consolidated ia Mill, Standard Mill at Bodie, Anaconda and Dexter mills in Montana, Mercur (perhaps first to use …
اقرأ أكثر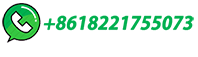
Ore Milling
Mt. Baker Mining and Metals is focused on providing a cost-effective and durable ore processing plant that includes a jaw crusher, hammer mill, size classification …
اقرأ أكثر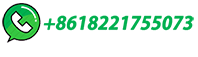
No. 7 concentrating mill in Mineville
Caption on photo reads: No.7 plant concentrating mill. The mining facilities at this location were owned and operated by Witherbees, Sherman, & Company until 1939; then, leased to and operated by Republic Steel until 1971.
اقرأ أكثر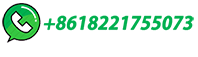
AMIT 135: Lesson 6 Grinding Circuit – Mining Mill …
Basic Mill Linings. Use rubber linings wherever possible due to lifetime, low weight, easy to install and noise dampening.; When application is getting tougher use steel-capped rubber, still easier to handle than steel.; When these both options are overruled (by temperature, feed size or chemicals) use steel.; Ore-bed is a lining with rubber covered permanent …
اقرأ أكثر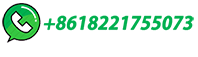