Clinker size and cement grinding | GCP Applied Technologies
Clinker size and cement grinding. Clinker size is important for the optimization of cement grinding, and is also an indicator of cement quality. Having a high percentage of coarse clinker can be difficult to grind. However, having a high percentage of fine clinker can also be hard to grind and have a negative impact on cement …
اقرأ أكثر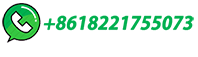
AN INTRODUCTION TO THE CEMENT MANUFACTURING
Module 4: Cement Grinding Systems and Dispatch. Cement clinker is grinding in roller mills and ball mills, such as granulated blast furnace slag, fly ash, limestone, and approximately 5% sulfate agents (e.g., gypsum). During production and before leaving the plant, the cement is internally inspected and tested in the plant's laboratories.
اقرأ أكثر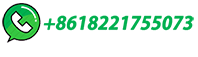
Comparing ball mills and VRMS for cement grinding
This is an abridgedversion of the full article, which appeared in the March 2013 issue of World Cement. Subscribers can view the full article by logging in. Introduction. Vertical roller mills (VRM) have become the standard for grinding raw materials in the cement manufacturing process.
اقرأ أكثر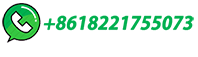
Cement grinding Vertical roller mills VS ball mills
However, a vertical roller mill for cement grinding generally requires the use of grinding aid to achieve the most efficient operation with a stable grinding bed and a low level of vibrations. Vertical roller mills grinding an OPC of low fineness, say around 3000 cm2/g (Blaine) can operate without grinding aid, but even when grinding to that ...
اقرأ أكثر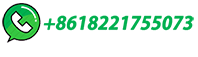
Effect of Feed Amount and Composition on Blaine and …
Grinding Mill: The obtained data were generated using a ball mill shown in Figure 1. The mill was mounted on a milling rig and allows a wide range of mill speeds to be used. Two chamber mills are used for grinding clinker and additive materials (pozzolana and gypsum). They are typically
اقرأ أكثر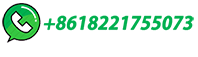
Update on Mexico
Interesting news from Holcim Mexico this week with the announcement that it is planning to invest US$40m towards building a 0.7Mt/yr grinding plant in the state of …
اقرأ أكثر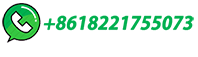
A New Cement Plant In Yucatan – Cement Products
With the Umán plant, Holcim Mexico operates nationwide through its seven cement plants and a grinding plant with a production capacity of 13.3 million tpy, 37 cement distribution centers, more than 50 …
اقرأ أكثر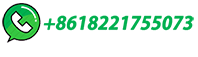
Horizontal roller mill (Horomill (R)) application versus hybrid …
This paper is concerned with a comparative analysis of modern cement grinding systems, namely, combined grinding (Comflex®), high-pressure roll mill (HPRM) grinding, and horizontal roller mill ...
اقرأ أكثر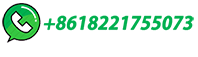
Holcim Mexico to Strengthen Tabasco Operations with $55 …
Holcim Mexico, a leader in innovative and sustainable building solutions, has announced a strategic investment of USD 55 million to construct a new grinding …
اقرأ أكثر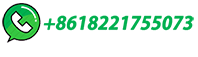
Cement Ball Mill | Cost Effective Cement Grinding Mill from …
The installation of liners. Length Diameter Ratio. The length-diameter ratio of the cement ball mill is relatively large. For mills of open-circuit grinding system, the length-diameter ratio is usually between 3.5 and 6 to ensure that the product fineness is qualified through single grinding; For ball mills in closed-circuit grind system, in order to increase the …
اقرأ أكثر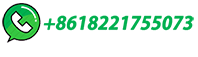
Ciment Québec Inc. has selected Fives FCB to upgrade its cement …
Ciment Québec Inc. has selected Fives FCB to upgrade its cement grinding in Saint Basile Plant, Quebec ... after having visited installations in the USA and Mexico, and also thanks to the excellent quality results during the pilot tests performed by the FCB Horomill® 500 compared to industrial ones in ball mill. ... quality results during …
اقرأ أكثر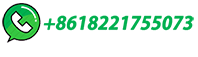
Cement Mill
Coal mill is the main equipment in the pulverized coal preparation process.Because calcining top-grade cement clinker requires a stable supply of coal powder as the fuel of cement kiln, and more than 85% of …
اقرأ أكثر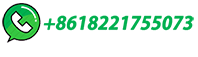
Let's talk: polysius® booster mill – the next level in cement grinding?
Reducing the clinker factor without compromising quality and the rising demand for high-performance cements are great challenges for the fine grinding technology used in cement plants. As part of its green cement plant project, thyssenkrupp has expanded its product range with the polysius® booster mill. While one cement manufacturer has already …
اقرأ أكثر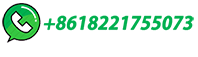
Cemento Cruz Azul to build new grinding mill at Lagunas …
Mexico: Cemento Cruz Azul will invest nearly US$40m to build a new grinding mill at its Lagunas cement plant in Oaxaca to increase cement production …
اقرأ أكثر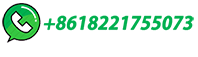
GRINDING TECHNOLOGY COURSE
A 6-week modular course is designed to give the course attendee a solid understanding of the grinding system and its auxiliary equipment. The purpose of the training is to Identify and understands necessary known and unknown information towards the completed cycle of the grinding system, whether it is a ball mill, vertical mill, or crushing process.
اقرأ أكثر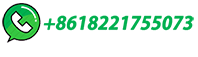
Clinker Grinding Techniques in Cement Manufacturing
Ball mills are often used for grinding cement clinker into a fine powder before it is mixed with other materials to produce cement. Vertical Roller Mill (VRM): Vertical roller mills are increasingly popular in modern cement plants. They use rollers and a table to grind clinker, offering greater energy efficiency and finer particle size control ...
اقرأ أكثر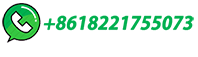
Country Report: The Cement Industry in Mexico
In Mexico, the cement industry is still concentrated in a group of six companies that dominate the national market today: Cemex, Grupo Cementos Chihuahua, Cemento Moctezuma, Holcim-Apasco, …
اقرأ أكثر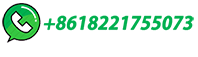
FCB Horomill® grinding plants in The Philippines
and cement grinding plants installed Tepetzingo plant - Cementos Moctezuma (Mexico) Operation time (hours) Availability (%) 1 Raw mill 1 6576 95,2 Raw mill 2 6352 94,4 Cement mill 1 7828 95,1 Cement mill 3 7831 95,4 Ball mill + Roller press 7038 93,3 r s) Raw mill 1 5429 94,7 Raw mill 2 5809 96,2 Cement mill 1 6042 92,9 Cement mill 3 …
اقرأ أكثر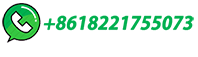
CEMENT GRINDING SYSTEMS
The final manufacturing stage at a cement plant is the grinding of cement clinker from the kiln, mixed with 4-5% gypsum and possible additives, into the final product, cement . In a modern cement plant the total consumption of electrical energy is about 100 kWh/t . The cement grinding process accounts for approx. 40% if this energy consumption.
اقرأ أكثر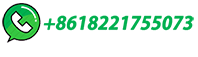
Cement Grinding
6 Cement Production Technology –Cement Grinding –Mechanical Design and Function of Separator Separators –General Classification of Separating Principles •according to flow direction relative to particle track •according to kind of separating field separation by gravitational force separation by centrifugal force
اقرأ أكثر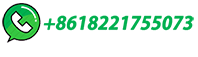
Finish grinding
The following increase in mill throughput was reported: 10-30 % when grinding Portland cement N° 375 (equal to compressive strength of 5321 psi after 28 days), and 25- 50 Ofo when grinding Portland cement No 475 (equal to 6740 psi).
اقرأ أكثر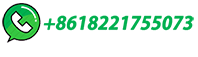
Ball mills | FL Cement
Ball mill for cement grinding. An inefficient ball mill is a major expense and could even cost you product quality. The best ball mills enable you to achieve the desired fineness quickly and efficiently, with minimum energy expenditure and low maintenance. With more than 4000 references worldwide, the FL ball mill is proven to do just that.
اقرأ أكثر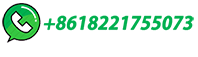
Holcim Mexico strengthens its presence in Tabasco with a new grinding
This expansion, which will increase cement production capacity to 1.5 million tpy, is aligned with Holcim's commitment to promoting economic and sustainable development in the southeastern region of Mexico. The new grinding unit will generate 800 jobs during its construction and will increase the plant's workforce to more than 300 jobs …
اقرأ أكثر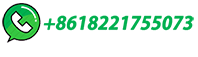
Grinding
Milling and crushing operations pose a number of headaches to cement plant operations. They consume large amounts of electrical energy. They are subject to severe abrasion. And their performance effects things well beyond the grinding plant, impacting the efficiency of the entire process, not to mention final product quality. A poorly designed or functioning …
اقرأ أكثر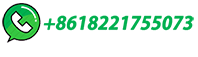
Overview of cement grinding: fundamentals, additives, technologies
Grinding is an essential operation in cement production given that it permits to obtain fine powder which reacts quickly with water, sets in few hours and hardens over a period of weeks. i ...
اقرأ أكثر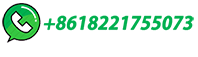
Ciment Québec Inc. has selected Fives FCB to upgrade cement grinding …
Ciment Québec Inc. has selected Fives FCB to upgrade cement grinding in the Saint Basile Plant; ... after having visited installations in the USA and Mexico, and also thanks to the excellent quality results during the pilot tests performed by the FCB Horomill 500 compared to industrial ones in ball mill.
اقرأ أكثر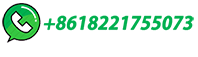
Modern milling in Mexico
Encouraged by healthy construction demand and promising growth potential, two regional cement manufacturers have decided to invest in cement grinding facilities in Yucatán, Mexico. Both Cementos …
اقرأ أكثر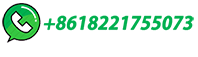
Grinding Mills
In Fig. 1.3 is shown a large ball mill, designed for the dry grinding of limestone, dolomite, quartz, refractory and similar materials; this type of mill being made in a series of sizes having diameters …
اقرأ أكثر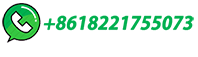
Holcim Mexico Invests $55 Million in New Grinding Facility
Holcim Mexico announced a strategic investment of $55 million to construct a new grinding facility at its cement plant in Macuspana, Tabasco. The expansion will …
اقرأ أكثر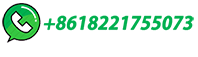
Cement Mill Optimization: Practical Strategies for Enhanced …
The grinding process in cement mills consumes a significant amount of energy and has a direct impact on the overall efficiency of the mill. By optimizing the grinding process, cement manufacturers can achieve higher productivity and lower energy consumption. Let's explore some practical strategies with real-world figures and numbers ...
اقرأ أكثر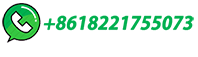