Coal Mill Safety: A Critical Aspect of Power Plant Operations | Coal …
Coal mills, also known as pulverizers, play a critical role in power plants by grinding coal into fine powder, which is then used in various pyroprocesses. ... Prolonged exposure to coal dust can cause respiratory issues and other health problems for workers. Proper ventilation and dust suppression are essential to mitigate these risks.
اقرأ أكثر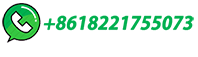
Coal Grinding Systems
A potentially serious problem exists if coal dust is allowed to accumulate inside a building or enclosure, for example around an unloading facility or because of a leaking coal conveying line. ... Coal mill hot air inlet temperatures should never be more than 600 F and the outlet temperature should not exceed 200°F on Raymond coal mills. If ...
اقرأ أكثر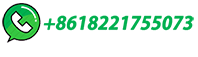
COAL PREPARATION AND FIRING
For the latter, impact mills may be more suitable than slower types; for the former, if the problem is severe, it may be necessary to reduce the mineral content of the coal, or choose another source. In any case a slow or medium speed mill will be necessary, in some cases for particularly abrasive coals a ball mill may have to be considered in
اقرأ أكثر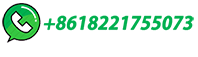
Child Labour in the British Industrial Revolution
An example is the Quarry Bank Mill in Styal in the county of Cheshire. Here the owner provided schooling after the long working day was over for 100 of its child workers in a dedicated building, the Apprentice House. ... Children very often suffered health problems from the physical hard work and long, 12-hour shifts. Breathing in coal …
اقرأ أكثر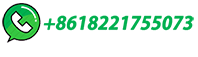
Review of control and fault diagnosis methods applied to coal mills
The operating window [161], [162] specifies the safe operational limits for an individual mill in terms of the coal flow and air flow, such that if these constraints are obeyed during the operation, mill problems such as coal choking, erosion, fire or explosion in pulverized coal-air pipes or inside the mills can be avoided. The diagnostic ...
اقرأ أكثر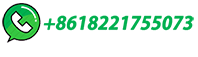
(PDF) Modeling and Control of Coal Mill
The main control problem associated with the coal mill is the lack of sensors for measuring the outlet pulverized coal flow. The input raw coal flow into the mill is also difficult to be measured. Generally, the speed of the conveyor belt will be used for this purpose. Additionally, estimation of varying coal quality, type of coal, moisture ...
اقرأ أكثر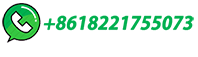
World Coal "Sticky When Wet"
by fines building up. One plant str uggled for days with wet coal problems in the plant, while the coal yard processed the coal through hammer mills as usual. When these crushers were by -passed the plants situation improved considerably. The purpose for crushing the coal in the first place was to assist the pulverizers in their job.
اقرأ أكثر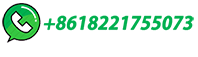
A Innovative Solution to the Problem of Mill Rejects in Thermal Power
The present paper discusses an innovative means for solving the problem of accumulation of waste coal in some pulverized coal fired plants. A major waste in a pulverized coal fired power plant is the reject produced from pulverizing mills. When coal is ground in a bowl mill heavy mineral matters are separated, but they still contain a small …
اقرأ أكثر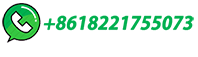
Large-scale wind power has its down side — Harvard Gazette
"If your perspective is the next 10 years, wind power actually has — in some respects — more climate impact than coal or gas. If your perspective is the next thousand years, then wind power has enormously less climatic impact than coal or gas. "The work should not be seen as a fundamental critique of wind power," he said.
اقرأ أكثر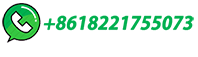
An investigation of performance characteristics and …
This study shows the performance of a currently running vertical roller coal mill (VRM) in an existing coal-fired power plant. In a power plant, the coal mill is the …
اقرأ أكثر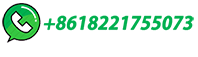
Coal Grinding
Mill Feeders: Feeders for coal mill are generally installed directly under hoppers with rod gate in between. The feeders are generally 2 to 3 m long and discharge on to conveyor or feeding chute to mill. For coal mill feeding, table feeders, belt feeders, chain feeders and weigh feeders have been used.
اقرأ أكثر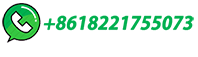
OPEN LETTER: How to fix the boiler and mill problems at …
The source of the problem is the coal pulveriser mills not being able to produce the more stringent fineness required. This results in coal/char particles burning higher up in the furnace, causing excessive reheater temperatures, etc. One could attempt to increase the rotational speed of the vertical spindle mills by at least 15%.
اقرأ أكثر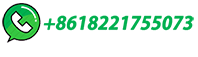
Detection of Malfunctions and Abnormal Working …
Coal mill malfunctions are some of the most common causes of failing to keep the power plant crucial operating parameters or even unplanned power plant …
اقرأ أكثر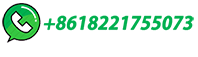
Pulverizer failure cause analysis. Final report
This report contains the results of a 16 month study to examine the problem of pulverizer outages and to identify root cause failure modes for the major mill types currently in service. A data base of 469 pulverizers, the majority larger than 40 tons/hr coal capacity, was compiled by surveying the utilities with coal fired boilers in this country.
اقرأ أكثر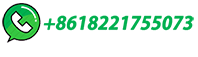
Measurement and Control of Coal Pipe Temperature of …
additional field tests, but require suitable modelling techniques which are to be identified properly. A novel coal mill modelling technique for E-type coal mill and dynamic behaviour are developed using genetic algorithms [3]. Genetic Algorithms (GAs) have been successfully applied to problems in business, engineering, and science.
اقرأ أكثر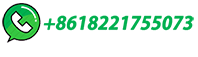
Design Scheme of Fault Diagnosis System for Rollers of Coal Mills
In order to solve the problem to directly measure the wear of roller of HP coal mill in thermal power plant, this paper proposes a new design scheme of wear monitoring and diagnosis system for the rollers, based on the theory of mechanical vibration fault monitoring and diagnosis, combined with CAE simulation analysis technology. The …
اقرأ أكثر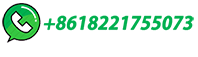
Review of control and fault diagnosis methods applied to …
Power plant performance and reliability is highly influenced by coal mills that grind, dry, and transport coal to the furnace. This paper presents a review of the current …
اقرأ أكثر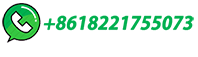
(PDF) Modeling and Control of Coal Mill
The main control problem associated with the coal mill is the lack of sensors for measuring the outlet pulverized coal flow. The input raw coal flow into the mill is also …
اقرأ أكثر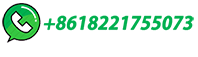
Mill Inerting and Pulverizer/Mill Explosion Mitigation
• Rehydration is exothermic and dried coal that is stagnate anywhere in the coal mill can begin to smolder and burn. • Smoldering coal inside an idle mill can evolve into a big problem when the mill is started, agitating these accumulation combined with a high air to fuel ratio environment •
اقرأ أكثر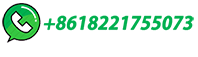
Safety considerations when purchasing a stand-alone …
However, when new coal grinding systems are purchased for existing lines, the situation is similarly complex. Vincent Grosskopf of Coal Mill Safety asks some pertinent questions... Vincent Grosskopf, Coal Mill Safety I n cases when a complete clinker line is purchased, the attention paid to the details of the coal grinding
اقرأ أكثر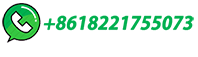
The Inferential predictive control method of coal mill | IEEE
Finally, we take the estimation of coal outlet mass flow as the new controlled variable and use inferential predictive control method to solve the coal mill control problems. The simulation results show that the new control method can shorten the delay time of the coal preparation system, and speed up the response of the boiler to AGC …
اقرأ أكثر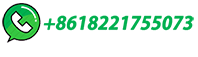
Hidden hazard: Boulder's million-ton coal ash problem
Coal ash was thrust into the national conversation in 2008, after a disastrous spill in Kingston, Tennessee, released one billion gallons of ash into the Emory River, causing hundreds of cleanup workers to be exposed to hazardous heavy metals and radioactive particles they say resulted in illnesses, some fatal.Seven years later, the …
اقرأ أكثر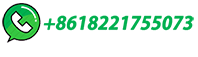
COAL GRINDING SYSTEMS SAFETY CONSIDERATIONS
Belt magnets and metal detectors on coal belts must always be operating properly. Pieces of metal can cause sparks or become overheated which can ignite a fire or initiate an …
اقرأ أكثر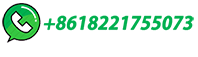
Fire and explosion protection of coal grinding systems.
With 'everybody' in the cement industry focussing decarbonisation, but with coal grinding systems still being used in the foreseeable future, the topic dealt with here must not be shoved into the background. There is a serious need for change here too.
اقرأ أكثر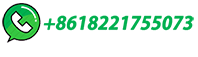
LOESCHE-MILLS
1927 First Loesche coal mill delivered for the Klingenberg power station in Berlin. 1953 500th coal mill plant sold worldwide. 1961 Introduction of hydraulic spring assembly system. 1965 Construction of first pressure mill (LM 12.2 D). 1980 Delivery of first modular coal mill (LM 26.3 D). 1985 Delivery of first self-inerting coal grinding plant (LM 21.2 D) …
اقرأ أكثر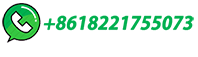
Dual fault warning method for coal mill based on
Problem description. The coal mill is a machine that breaks and grinds coal into pulverized coal. It is the core equipment of pulverizing system. Coal mills are categorized according to speed as low, medium and high speed mills. The low and medium-speed coal mills are the most popular due to their economy [25]. The modeling …
اقرأ أكثر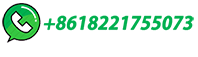
A Wear Condition Monitoring Model of Coal Mill Grinding
Download Citation | On Oct 14, 2020, Yanping Li and others published A Wear Condition Monitoring Model of Coal Mill Grinding Roller Based on LSTM | Find, read and cite all the research you need on ...
اقرأ أكثر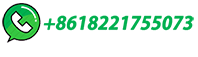
Comprehensive explosion protection of technological equipment in a coal
Problem: explosion hazard of a coal dust/air mixture upon contact with an ignition source (e.g. hot surface, mechanical and electrostatic sparks, open fire source) in apparatus involved in the storage, dust extraction, grinding and pneumatic transport of coal on the premises of a coal mill
اقرأ أكثر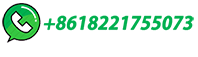
Derivation and validation of a coal mill model for control
The paper presents development and validation of a coal mill model to be used for improved mill control, which may lead to a better load following capability of …
اقرأ أكثر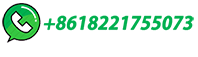