Potential of High-Pressure Grinding Roll (HPGR) for Size Reduction …
Abstract HPGR has been found to be efficient size reduction equipment compared to conventional size reduction equipments due to its potential processing benefits in terms of energy savings, improved exposure or liberation and particle weakening. The objective of the current work is to study the optimization of different …
اقرأ أكثر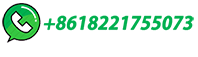
Size reduction performance evaluation of HPGR/ball mill and …
It was found that the ball mill consumed 54.67 kWh/t energy to reduce the F 80 feed size of 722.2 µm to P 80 product size of 275.4 µm while stirred mill consumed …
اقرأ أكثر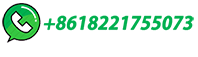
Performance optimization of an industrial ball mill for
The particle size (D 80) of the ball mill discharge increased from 312 μm to 455 μm after circuit optimization. The recirculating load of the grinding circuit was not improved due to the rejection of >3 mm particles during feeding of hard ore (high-grade middle band ore).
اقرأ أكثر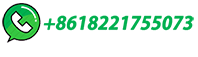
Complete Optimisation from Mine-to-Mill to Maximise …
the Cerro Corona project and the predicted impact on throughput and final grind size (P 80) for the ore type investigated are shown in Figure 1. ... and Bond Ball Mill Work Index ... fragmentation ...
اقرأ أكثر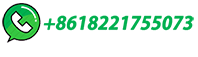
Population balance model approach to ball mill …
The process of particle size reduction by grinding is inherently inefficient and involves high capital and operating costs. In particular, ball milling is one of the important unit operations in ...
اقرأ أكثر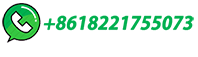
(PDF) Grinding Media in Ball Mills-A Review
ments, the author also observed that the br eakage kinetics of ore depend on ball size and shape. ... [87] also found that when the mill loading is reduced, there is a reduction in mill power . draw.
اقرأ أكثر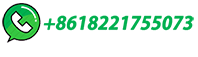
Effect of ball and feed particle size distribution on the …
It was found that the ball mill consumed 54.67 kWh/t energy to reduce the F 80 feed size of 722.2 lm to P 80 product size of 275.4 lm while stirred mill consumed 32.45 kWh/t of energy to produce ...
اقرأ أكثر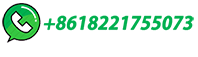
Optimization of in-mill ball loading and slurry solids …
Highlights Combined effects of slurry % solids and ball load on milling of UG-2 ore are studied. Central composite design and response surface methodology (RSM) are applied. Response variables are specific energy consumption and size reduction index. Optimized input factors levels combination are ∼29% ball load and ∼75% slurry solids. …
اقرأ أكثر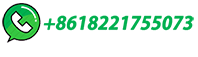
Intelligent optimal control system for ball mill grinding …
The ball mill grinding process is mainly composed of a ball mill, a hydrocyclone cluster, a sump, a slurry pump and an ore bin. The schematic diagram of this process is shown in Fig. 1. Fig. 1 Schematic diagram of ball mill grinding process. The variables of this process shown in Fig. 1 are ex-plained as follows: W
اقرأ أكثر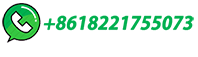
Simulating large-diameter industrial ball mills from batch …
An Itabirite iron ore sample with a top particle size of 19 mm was tested in another batch ball mill with a diameter of 580 mm and a length of 240 mm. Analysis of …
اقرأ أكثر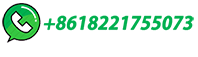
v117n1a11 Performance optimization of an industrial …
17 r/min. The energy consumption in the ball mill was found to be 6.5 kWh/t of ore with a targeted product size below. 1 mm. The BWI of the ores varied from 5.8 to 7.8 kWh/t to …
اقرأ أكثر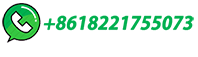
Optimization of Solids Concentration in Iron Ore Ball …
PDF | Important advances have been made in the last 60 years or so in the modeling of ball mills using mathematical formulas and models. One approach... | Find, read and cite all the research you ...
اقرأ أكثر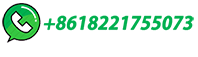
Population balance model approach to ball mill …
3 BALL MILL MODEL The population balance model may be expressed by Equation (1): > @ ¦ i-1 1 i b ij m j j i j i S Ht dt d H m t (1) where: S i (t) is the size discretized selection function for ...
اقرأ أكثر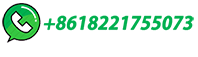
Optimisation of the size distribution of ball mill product by …
Proposed approaches for optimisation of size distribution of ball mill product are to minimise the product 80% passing size or to reach the desired product …
اقرأ أكثر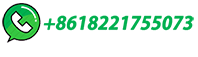
Potential of High-Pressure Grinding Roll (HPGR) for Size …
lowed by rod and ball mills. To reduce operating cost by accepting coarser feed, the rod mills were replaced by larger-diameter ball mills during the 1960s. During the 1970s, autogenous grinding mills (AG) and semiautoge-nous grinding mills (SAG) were largely used, and soon the comminution circuits with AG/SAG mills and ball mills
اقرأ أكثر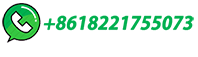
Optimization of Solids Concentration in Iron Ore Ball …
minerals Article Optimization of Solids Concentration in Iron Ore Ball Milling through Modeling and Simulation Patricia M. C. Faria 1,2, Raj K. Rajamani 3 and Luís M. Tavares 2,* 1 Department of Development Engineering, Vale S.A., Porto de Tubarão, Vitória-ES CEP 29090-900, Brazil; [email protected]
اقرأ أكثر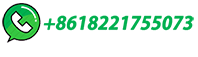
Selected Advances in Modelling of Size Reduction in …
chemical industries are subjected to grinding in ball mills [1–3]. The specic energy consumption for these materials typically ranges from 5 to 50 kWh/ton. Thus, the ball mills consume an enormous amount of energy. The energy e-ciency of the ball mill being as low as 1% or less [2], there is considerable incentive to improve the energy …
اقرأ أكثر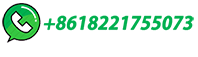
Population balance model approach to ball mill …
Population balance model approach to ball mill optimization in iron ore grinding. January 2014; Authors: Patrícia Mundim Campos Faria ... P. T. (1984) Process engineering of size reduction: ball ...
اقرأ أكثر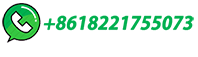
Intelligent optimal control system for ball mill grinding …
The ball mill grinding process is mainly composed of a ball mill, a hydrocyclone cluster, a sump, a slurry pump and an ore bin. The schematic diagram of this process is shown in …
اقرأ أكثر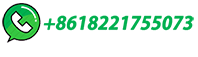
OneMine | Fragmentation Optimisation – Adopting Mine to Mill …
The Anglo American phosphate mine is located in the Brazilian state of Goiás and possesses one of Brazil's most important phosphate rock deposits, with the site being the country's second largest producer of phosphate rock concentrate. Despite the site having been in operation since 1979, the mining team only started using explosives …
اقرأ أكثر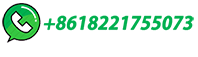
A specific energy-based size reduction model for batch grinding ball mill
A specific energy-based size reduction model has been developed for ball mill. • Ore-specific and size-dependent breakage function is incorporated in the model. ... and its applications in engineering design and production optimisation. Many of the tumbling mill models are derivable from population balance considerations (Kelsall and …
اقرأ أكثر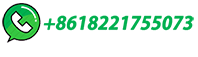
Estimation of the Specific Energy Requirement for Size Reduction …
Table 1 shows a comparison of the specific energy values calculated from Eqs. () and for the 100 mesh test sieve (S = 150 µm) and seven values of G in the range of 0.33–3 g/rev.It can be seen that at a G value of 1.5 both the equations give the same estimate of the specific energy. For G values greater than 1.5 the Bond equation gives …
اقرأ أكثر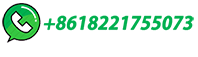
Ball Mill
Ball mills are horizontal rotating cylindrical or conical steel chambers, approximately one third to half full of steel, alloy steel or iron balls, like that shown in Fig. 4.10 A–C, or flint stones. The size reduction is accomplished by the impact of these balls on the material as they fall back after being lifted by the rotating chamber.
اقرأ أكثر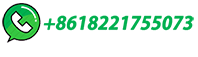
OPTIMIZATION OF LATERITE ORE GRINDING PROCESS USING BALL MILL …
Under a fixed rotating speed of agitating shaft and within the considered particle size reduction range, the ash content of coal has the greatest in-fluence on the specific flux and energy ...
اقرأ أكثر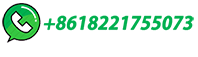
Simulation and optimization of a two-stage ball mill …
In an example of application of this approach, Faria et al. [9] recently demonstrated the ability of the population balance model to predict size reduction in an industrial ball mill grinding iron ...
اقرأ أكثر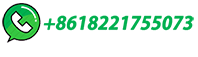
BALL MILLS Ball mill optimisation
in combination with a ball mill for cement grinding applications and as finished product grinding units, as well as raw ingredient grinding equipment in mineral applications. This paper will focus on the ball mill grinding process, its tools and optimisation possibilities (see Figure 1). The ball mill comminution process has a high electrical
اقرأ أكثر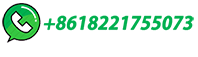
Simulation and optimization of a two-stage ball mill …
Using the obtained particle size distributions, the reduction ratio based on the 80% passing size was calculated to be 80.5 for the first ball mill, while it was only 1.19 for the second ball mill. To solve the process imbalance problem, a layout rearrangement that involves the switching of the first and second ball mills in the process was ...
اقرأ أكثر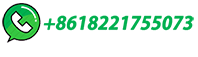
v117n1a11 Performance optimization of an industrial …
The run-of-mine ore is reduced to a particle size of less than 1 mm in the comminution circuit and concentrated using ... ball mill, process optimization, chromite benefi-ciation, ultrafine reduction. * Research and Development Department, Tata Steel
اقرأ أكثر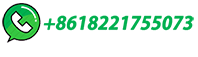
The design and optimization process of ball mill to reduce …
Small particle size in the order of micrometer of event nanometer size is preferred. The raw materials were ground from the big particle size to the smallest possible by using multistep grinding. In the laboratory, the common method to be used as the ball mill. This work aims to design a simple horizontal ball mill.
اقرأ أكثر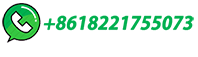
Effect of ball and feed particle size distribution on the …
tively milled in a ball mill because each media size can effectively break a particular particle size during the size reduction process ensuring that the product fineness is optimized. The same policy is employed for the make-up chargewhereadding different ball sizes is done in order to optimize the mill performance. Chimwani et al.
اقرأ أكثر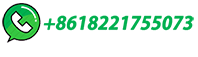