Iron Min- ing and Manufacturing in Utah: A History.
York Jones, former mine manager of an iron-ore mine in Utah (deceased), and his son Evan have compiled the history of iron mining and manufacturing in Utah from its …
اقرأ أكثر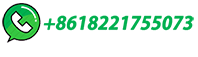
Making Iron Directly From Concentrate by Gaseous Reduction
Considering the two most important issues the ironmaking industry faces today, i.e., energy consumption and greenhouse gas emissions, it would be advantageous to utilize the concentrate-size raw materials directly without pelletizing or sintering, especially without the use of coke. This plenary lecture describes two such processes …
اقرأ أكثر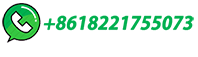
Nonferrous Metals Milling Plants in Utah
Table 2 lists some of the processes that were used in utah milling plants. The history of process development, and its application to specific utah ore bodies, are documented mainly by references in the text. Ritcey (1989) Somasundaran (1989) and others provide detail on current processes with respect to tail ings management.
اقرأ أكثر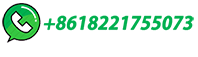
Sintering: A Step Between Mining Iron Ore and Steelmaking
The remaining 2% of domestic iron ore was produced for non-steel end uses. Seven open-pit iron ore mines (each with associated concentration and pelletizing plants), and three iron metallic plants—one direct-reduced iron (DRI) plant and two hot-briquetted iron (HBI) plants— operated during the year to supply steelmaking raw …
اقرأ أكثر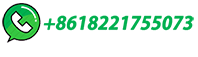
Introduction: Overview of the global iron ore industry
Turning to iron ore exports and imports, the tonnages are summarized in Table 1.1 for 2012 and 2018 (Australian Department of Industry, Science, Energy and Resources, 2021; US Geological Survey, 2020; United National Conference on Trade and Development (UNCTAD), 2021).As shown in Fig. 1.3, China is the largest iron ore …
اقرأ أكثر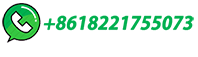
Leamington Cement Plant
Mr. Aspdin thought that his cement resembled a well-known limestone building stone quarried on the British Isle of Portland. Portland cement is typically made from (1) limestone, (2) a source of silica like sandstone or quartzite, (3) a source of alumina like shale, clay, or bauxite, (4) iron ore or industrial by-product iron, and (5) gypsum.
اقرأ أكثر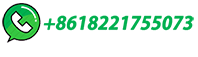
Your iron ore beneficiation solutions
Wright iron ore mine in Canada. In 2011, we delivered 5,760 spiral starts and in 2014 we delivered an additional 2,688 iron ore spiral starts to the mine. These represented the largest delivery of iron ore spirals to any one mine site. To meet Mont Wright's specific beneficiation requirements, we embarked on an extensive research
اقرأ أكثر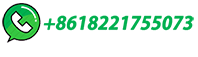
Iron processing
Iron processing - Ores, Smelting, Refining: Iron ores occur in igneous, metamorphic (transformed), or sedimentary rocks in a variety of geologic environments. Most are sedimentary, but many have been changed by weathering, and so their precise origin is difficult to determine. The most widely distributed iron-bearing minerals are oxides, and …
اقرأ أكثر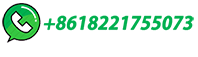
Development of Ironmaking Technology by the Direct …
This plenary lecture describes two such processes developed at the University of Utah. One is the Flash Ironmaking Tech-nology (FIT), and the other is a …
اقرأ أكثر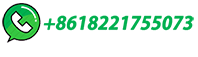
16 Energy and Mineral Resources – An Introduction to Geology
16.1.2. Ore Banded-iron formations are an important ore of iron (Fe). Earth's materials include the periodic table elements. However, it is rare that these elements are concentrated to the point where it is profitable to extract and process the material into usable products.
اقرأ أكثر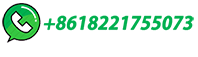
DRI production | International Iron Metallics Association
The Midrex® and Energiron gas-based processes use predominantly iron ore pellets as feedstock, but sometimes with inclusion of lump ore in the furnace charge. The Circored and Finmet / Finored gas-based processes utilize iron ore fines as feedstock.The SLRN coal-based rotary kiln process uses lump ore and, increasingly, pellets as feedstock.
اقرأ أكثر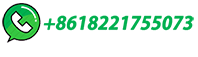
Mining the Iron Mountain
The Iron Mountain mine in southwestern Utah has served as a source of iron ore for many uses during its 160-year history. From the mid-19th century to the early years of the 21st century, its magnetite/hematite ores were first used to forge pioneer-era hinges and hardware, later for wartime steelmaking and then for producing plate, pipe …
اقرأ أكثر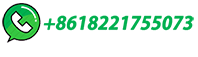
Steelmaking :: Cleveland-Cliffs Inc. (CLF)
Best-in-Class Steel Producer. Cleveland-Cliffs is the largest flat-rolled steel producer in North America. Our competitive advantage as an integrated steel company is based on our ability to operate the entire production flow from the extraction of iron ore, to steelmaking, rolling, coating, finishing, stamping and tooling steel products.
اقرأ أكثر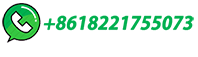
Direct Reduced Iron and its Production Processes – …
Major DRI production processes are either natural gas based or coal based. Feed material for the DR process is either sized iron ore of size ranging from 10 mm to 30 mm or iron ore pellets of size ranging from 8 mm to 20 mm produced in an iron ore pellet plant. The gas based process uses a shaft furnace for the reduction reaction.
اقرأ أكثر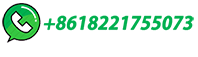
Iron Min- ing and Manufacturing in Utah: A History.
of iron mining and manufacturing in Utah. After the war, the federal government sold the Geneva Plant to U.S. Steel and the second Ironton furnace to Kaiser Steel. U.S. Steel continued its captive iron-ore operations at Iron Mountain. When available reserves were depleted there, it moved to Desert Mound where it had procured leases from
اقرأ أكثر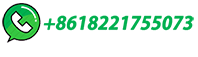
Applications of Iron Ore Pellets
This process of converting iron ore into pellets is known as Pelletization. Iron Ore Pellets are then used in the production of steel. Pellets are usually preferred instead of raw Iron Ore because it allows for maximum utilization of iron ore. This is important since iron ore reserves are depleting globally.
اقرأ أكثر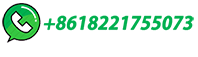
Press Release | arpa-e.energy.gov
Using domestically available iron ore feedstocks, the process has the potential to produce greenhouse gas emission-free iron at cost parity with today's carbon-intensive ironmaking methods. (Award amount: $1,000,000)Georgia Institute of Technology (Atlanta, GA) will work on a method to produce net-shaped engineered lattice structures …
اقرأ أكثر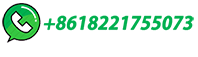
Iron ore pelletizing
We can help our customers to determine which process is the best for their ore, fuel and pellet requirements. Our iron ore pelletizing systems combine the best features of both technologies to provide the most modern plant and to produce pellets at the lowest cost and highest quality.
اقرأ أكثر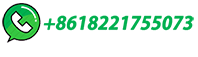
Circored Fine Ore Direct Reduction – a proven process to
Outotec's Circored technology is the only process for iron ore reduction based on hydrogen that has proven its functionality and performance in an industrial-scale demonstration plant. ... The Trinidad plant fulfilled process expectations in terms of a high and uniform degree of metallization achieved from the outset. The key ...
اقرأ أكثر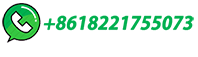
Introduction to Iron ore Pellets and Pelletizing processes
Raw material preparation – During the process for pelletization iron ore concentrate from iron ore beneficiation plant is dried and heated to around 120 deg C. The dried material is fed to the ball mill for grinding. Concentrate/ground iron ore of typical size 80 % less than 45 microns (0.045 mm) with a moisture content of around 9 % is ...
اقرأ أكثر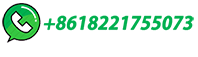
India's leading producer of Iron Ore | Vedanta Group Company
Sesa Goa Iron Ore also has two power plants of 30 MW each that produce 60 MW of clean power by using the waste heat recovery from its coke ovens and blast furnace gas. ... process optimization initiatives and most importantly through implementation of world class ESG practices. In this growth journey we remain highly dedicated towards ensuring ...
اقرأ أكثر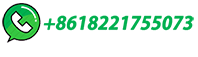
Development of Ironmaking Technology by the Direct …
processes developed at the University of Utah. One is the Flash Ironmaking Tech-nology (FIT), and the other is a moving-bed process for continuous ironmaking with gaseous reduction of iron ore concentrate (MBIT). These technologies are designed to produce iron directly from iron concentrate without requiring pelleti-zation/sintering and …
اقرأ أكثر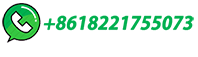
For the first time, EPA to require taconite plants to …
The U.S. Environmental Protection Agency has proposed a new rule that for the first time would require mining companies to limit mercury emissions from taconite iron ore processing plants, which ...
اقرأ أكثر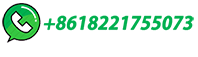
Utah Minerals | Utah Mining Association
High-grade iron ore is found in many small deposits in the Wasatch and Uinta Mountains, but large deposits are found only in southwestern Utah. For many years iron ore has …
اقرأ أكثر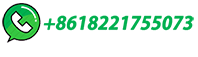
Steel magnate Henry Kaiser mined Eagle Mountain
In 1945, the site for Kaiser's acquisition to supply his multi-million dollar integrated steel plant at Fontana was the old Iron Chief Mine. The former mine was credited with early gold ...
اقرأ أكثر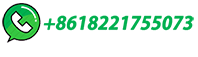
Bingham Leaching and Precipitation Plants
The early attempts used scrap iron from around the mining camps, and recovered only about 40 percent of the copper that was in the water. In 1916 Utah Copper built a leaching plant at Magna to process the low-grade ore it was having to set aside as it was mining the higher-grade ore from its Bingham open pit mine.
اقرأ أكثر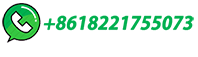
KIOCL Ltd.
KIOCL is having facilities to operate 3.5 MTPA Iron-oxide Pellet Plant, Blast Furnace Unit to manufacture 2.16 lakh tonnes per annum Pig iron at Mangaluru, Karnataka.KIOCL is an EoU and a profit making, continuous dividend paying Company with a positive net worth and Mini Ratna Category I PSU is also an ISO9001:2015, ISO14001:2015 and …
اقرأ أكثر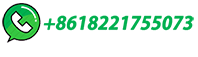
Greening Iron & Steel Production | College of Science
Existing blast furnaces use purified coal (or " coke") and limestone to turn iron ore into molten iron at extremely high temperatures. A separate facility then turns iron into high-strength steel, which goes on to become car parts, structural beams, kitchen …
اقرأ أكثر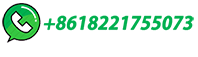