Cement Production Demystified: Step-by-Step Process and …
One type of machine used in this process is a ball mill. This machine uses rotating cylinders filled with steel balls to grind the raw materials into a fine powder. ... which can be used as a partial replacement for clinker in cement production (reduced the clinker to cement ratio). This can help to reduce the amount of energy and emissions ...
اقرأ أكثر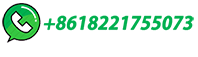
The four major costs associated with cement production
The power requirement of cement plants varies in accordance with the heat treatment process used viz., dry process or wet process. While the wet process requires almost 1,300-1,600 kcal/kg of clinker and 110-115 kwh of power to manufacture 1 tonne of cement, the dry process requires 720-990 kcal/kg of clinker and 95-110 kwh of power.
اقرأ أكثر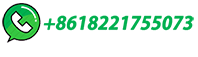
PYROPROCESS TECHNOLOGY COURSE
An emphasis on the understanding of the pyroprocess technology system: – Raw Mix Design, Burnability, and Clinker Quality – Optimization of Heat Consumption – Operation and Process Diagnostic Studies and Productivity Enhancement of the Clinker Production – Energy Conservation and Energy Audit in Pyro System – Refractory and Management …
اقرأ أكثر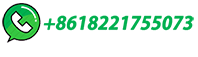
Deep decarbonisation of industry: The cement sector
kilns would be needed (11). Cement production using a mixture of hydrogen and biomass fuels is currently at an early stage of investigation (TRL 2). Biomass Carbon capture To fully decarbonise the sector, process emissions from the clinker-making process need to be addressed, regardless of the heat source. Part of the solution will
اقرأ أكثر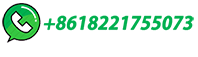
Toward smart and sustainable cement manufacturing process…
Cement plants have used new grinding equipment, dry-process instead of the wet-process kiln, modern clinker kilns, and multi-stage preheaters that can save energy [1]. The use of blends with renewable fuel and fossil fuel [ 2 ] or the use of solar calcination reactors [ 3 ] can reduce emissions and save energy in cement manufacturing.
اقرأ أكثر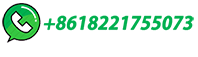
Cement Clinker Production
Valorization of sewage sludge in the fabrication of construction and building materials: A review. Zhiyang Chang, ... Cong Ma, in Resources, Conservation and Recycling, 2020. 3.1 Cement clinker production. As cement is the most widely used building material in the world, cement industry is often regarded as having excessive energy consumption and …
اقرأ أكثر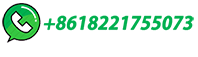
Cement Production Line
AGICO dry process cement production line comprehensively adopts the IT technology, multi-function grinding system, new-type wear-resisting and heat-resisting materials, mechanical powder conveying device, and …
اقرأ أكثر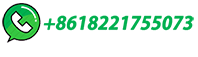
A comparative life cycle assessment for sustainable cement production
1. Introduction. Cement production is a complex process that includes the use of a high quantity of raw materials and fuels (petroleum coke, coal, natural gas, fuel oil, biomass or some wastes) and energy (electricity and heat) in addition to auxiliaries, air, and water (Valderrama et al., 2012; Galvez-Martos and berger, 2014), and as a …
اقرأ أكثر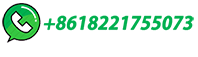
Thermodynamic modelling of cements clinkering process as …
World cement production is about 4.3 billion tons per year 1, with an average consumption of raw materials of about 1.6 tonnes for each tonne of cement manufactured 2.Valorisation of waste or by ...
اقرأ أكثر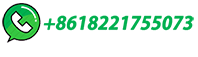
China's provincial process CO2 emissions from cement production …
According to China National Bureau of Statistics, in 2019, China produced 2.3 Gt cement 4, accounting for 56.8% of the world's total cement production, and in recent years its process-related ...
اقرأ أكثر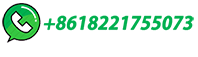
Clinker Production
Clinker production is the most energy-intensive stage in cement production, accounting for more than 90% of total industry energy use and virtually all the fuel use. The main kiln …
اقرأ أكثر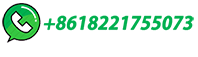
Rotary Cooler | Clinker Cooler In Cement Plant | AGICO CEMENT
Working principle of rotary cooler. Cooler is a kind of refrigeration equipment that is realized by vapor-compression or absorption cycle, the liquid can flow through the heat exchanger to reach for the purpose of the cooling air or equipment, high-temperature clinker enter into the cooler from the feeding device, cooler rotate to drive sufficient heat …
اقرأ أكثر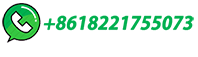
Clinker Production | Clinker Plant | Cement Plant Equipment
AGICO Cement provides cement equipment of clinker production, including rotary kiln, preheater, and precalciner, start cement plant now! Skip to content +86 . info@cement-plants. about. ... Dry Process Of Cement Production. spare parts. Ball mill pinion. Air Slide. Grinding ball. Crusher Spring. Ball mill diaphragm. Jaw Crusher ...
اقرأ أكثر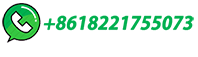
Everything you need to know about Kiln System Operations in Cement …
Each kiln subsystem (including the preheater and clinker cooler) has an important bearing on the time and temperature required for passage through the sintering zone to get clinker that will produce high quality cement. KILN TEMPERATURE PROFILE. In a rotary kiln system producing cement clinker, gas flows are counter-current to material flows.
اقرأ أكثر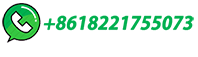
Clinker Production
A review of the effectiveness of Life Cycle Assessment for gauging environmental impacts from cement production. Oluwafemi E. Ige, ... Collins Obiora, in Journal of Cleaner Production, 2021. 2.2.3 Production of clinker. The clinker production stage is where the raw material (the raw meal) converts into clinker. The raw meal is fed into a rotary kiln …
اقرأ أكثر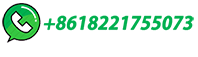
MOST IMPORTANT BOOKS IN CEMENT INDUSTRY
1. Introduction and composition of Portland cement 2. Raw materials 3. Production of cement clinker 4. Characterisation of Portland cement clinker 5. Grinding fineness of cement 6. Tests of cement quality 7. The hydration of Portland cement 8. The nature of hardened cement paste 9. Portland cements and related blended cements 10. …
اقرأ أكثر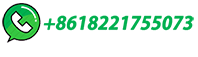
Deep decarbonisation of industry: The cement sector
The remaining 65% are due to direct process emissions, which must also be addressed. By 2050, cement production in the EU is expected to remain below pre-2010 levels. en. Deutsch Italiano ... 90% of clinker is now made via the more energy efficient dry clinker-making process (2). Older, less efficient wet kilns have almost been phased out. ...
اقرأ أكثر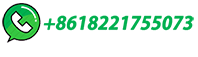
Auxiliary Equipment
Clinker production. cement equipment for clinker plant mainly include cement kiln, preheater, and other cement plant equipment, to ensure the smooth operation of equipment and technology. ... Dry Process Of Cement Production. spare parts. Ball mill pinion. Air Slide. Grinding ball. Crusher Spring. Ball mill diaphragm. Jaw Crusher Toggle …
اقرأ أكثر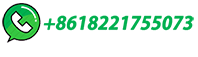
Optimisation and stabilisation of clinker production
Cement clinker production is in fact chemical. production. ... processing equipment. The forecast has the ability to. compare specified values and, according to the results,
اقرأ أكثر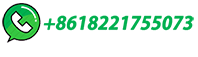
Optimization of the Clinker Production Phase in a Cement …
An MPC strategy is used to stabilize a temperature profile along the rotary kiln, guaranteeing good combustion conditions and maximizing production. In this …
اقرأ أكثر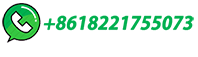
Efficiency enhancement and cost reduction in cement clinker …
Clinker production in the rotary kiln was one of the most energy-intensive processes in the cement industry. The application of exergy analysis to cement …
اقرأ أكثر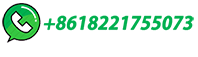
Clinker cooling
In the wet production process with a specific heat consumption of 1400 kcal/kg of clinker, the volume of the secondary air amounts from 1.3-1.5 st.m3/kg of clinker. The temperature of the secondary air leaving the …
اقرأ أكثر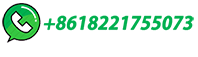
Clinker cooling
In the wet production process with a specific heat consumption of 1400 kcal/kg of clinker, the volume of the secondary air amounts from 1.3-1.5 st.m3/kg of clinker. The temperature of the secondary air leaving the satellite coolers and entering the kiln, is in the dry process kiln 840- 850 o C. and in the wet process kiln 600-650 oc.
اقرأ أكثر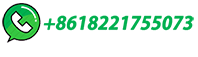
The Cement Manufacturing Process
In 2022, U.S. portland cement production increased slightly to an estimated 92 million tons, and masonry cement production increased to an estimated 2.5 million tons, according to the U.S. Geological Survey 2023 Cement Mineral Commodity Summary. The overall value of sales of cement was about $14.6 billion, with an …
اقرأ أكثر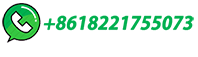
Alternative Clinker Technologies for Reducing Carbon …
In fact, the production of one ton of clinker releases about 0.83 tons of CO 2 and the production of one ton of OPC releases about 0.54 ton of CO 2 making this industry responsible for 5% to 8% of total anthropogenic greenhouse gases The two main sources of CO 2 emissions resulting from cement production are: (i) the decarbonation …
اقرأ أكثر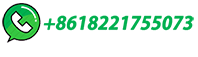
Understanding the Role of Clinker Grinding in Cement …
Clinker grinding is a vital and integral process in cement production, playing a crucial role in transforming clinker into the final cement product. Here's an exploration …
اقرأ أكثر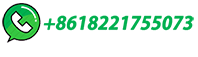
2500TPD new type dry process cement clinker production …
Description: The 2500t / d cement clinker production line adopts a new dry process, with an annual output of 775,000 tons of cement clinker and a total cement output of 1.05 million tons / year.A cement production line and auxiliary facilities from limestone crushing to cement packaging are constructed. Specialties include raw materials, production …
اقرأ أكثر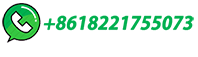
Cement Manufacturing Machine
A cement mill is just a general term for clinker grinding mill. It is a kind of grinding equipment that used to grind the calcined cement clinker then make them reach the particle fineness requirement of the finished cement product. It is the core equipment of the last step in the cement production process. The cement mill we usually used in ...
اقرأ أكثر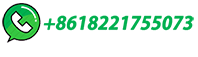
Cement Clinker Calcination in Cement Production Process | AGICO Cement
Raw Materials Crushing, Storing and Grinding. Clinker calcination is the most crucial part of the whole process of cement manufacturing. At this stage, ground raw materials will be sent into the cement kiln and be heated at a high temperature to produce chemical reactions with each other, eventually forming clinker. In addition, clinkers that just …
اقرأ أكثر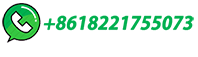
Cement Manufacturing Process
Clinker production is the most energy-intensive stage in cement production, accounting for over 90% of total industry energy use. Clinker is produced by pyro-processing in kilns. These kiln systems evaporate the free water in the meal in preheater cyclone, calcite the carbonate constituents (calcination) in calciner, and form Portland cement ...
اقرأ أكثر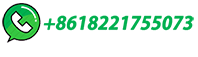