Coal Drying Improves Performance and Reduces Emissions …
Additionally, with less fuel moisture, more complete drying of coal can be achieved in the mill. This results in increased mill exit temperature (the temperature of the coal and primary air mixture at mill exit), better conveying of coal in the coal pipes and less coal pipe plugging problems. The mixture of pulverized coal and air is combusted ...
اقرأ أكثر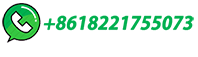
World Coal "Sticky When Wet"
the coal in the first place was to assist the pulverizers in their job. Unfortunately, the mills never saw the coal because the feeder was plugged. Increased moisture also decreases pulverizer performance by lowering the Btu value and causing additional coal recirculation to allow drying. Moisture Impact on Heatrate
اقرأ أكثر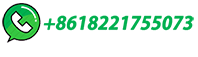
ATOX® Coal Mill
The ATOX® Coal Mill can grind and dry raw coal with up to 25 percent moisture level. By adjusting the gas flow stream with the nozzle, you can deal with more 'sticky', high-moisture feed materials. There is an oversized nozzle ring and separator that is available to make this adjustment.
اقرأ أكثر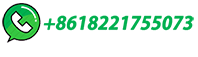
Drying of raw materials
Drying-grinding in ball mills. Fig. 4.5. shows a closed-circuit grinding plant where the drying is performed in the mill. For a better drying efficiency, a pre-drying compartment is arranged in front of the grinding compartment of the mill. The pre-drying compartment is equipped with lifters, but has not grinding media.
اقرأ أكثر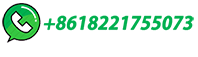
A unified thermo-mechanical model for coal mill operation
Dynamic coal mill model based on conservation laws and empirical relations. ... The physical processes associated with mills such as grinding, coal entrainment, drying, heat transfer, and classification are modeled. Internal structure of the mill is divided into four zones and coal is differentiated into ten size groups. From the validation ...
اقرأ أكثر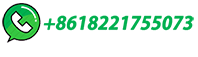
How is Ethanol Made?
Over 90 percent of the grain ethanol produced today comes from the dry milling process, with the remaining coming from wet mills. The main difference between the two is in the initial treatment of the grain. Dry Mill Ethanol Process. In dry milling, the entire grain kernel is first ground into "meal," then slurried with water to form a ...
اقرأ أكثر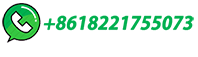
Bowl Mill Coal Pulverizer
Components of Bowl Mill Coal Pulverizer Gearbox. It is driven by an electric motor, is directly connected to the bowl hub. A planetary gear arrangement provides the proper reduction between the motor and the bowl hub to obtain the desired bowl speed. ... Air for transporting and drying the coal enters through the air inlet and is directed ...
اقرأ أكثر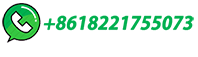
How to Process Coal into Pulverized Coal in 5 Steps?
With a vertical roller mill (VRM) VRMs consist of a rotating table or bowl and rollers. 1 To grind the coal, feed raw or initially crushed coal into the mill which is then ground between the rotating components.; 2 Finally, hot air removes moisture, carries the pulverized coal out, and a classifier segregates the particles.; Here is all you need to …
اقرأ أكثر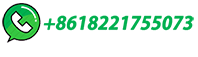
(PDF) USE OF COAL DRYING TO REDUCE WATER CONSUMED IN PULVERIZED COAL
Table 21 summarizes the avoided costs of lost power generation due to unscheduled mill outages, where it was assumed unit derates of 1/6 x 537 MW ranging from 0.5 to 1.5 days per year with replacement power costing $0.05/ kWhr, are avoided due to coal drying. Table 21 Mill Maintenance Savings – Lost Power Generation – Both CCW and CCW/FG ...
اقرأ أكثر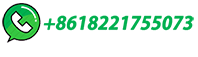
Recent developments in drying and dewatering for low …
Globally, low rank coals are responsible for about half of the world's total coal deposits. However, these low rank coals present a high moisture content, which significantly impacts their utilization processes, including lower power plant efficiency, increased transportation costs, higher CO 2 emission, and spontaneous combustion during …
اقرأ أكثر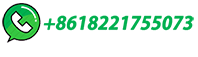
Impact Dryer Mills | Williams Patent Crusher®
The Standard Impact Dryer Mill System is utilized to grind, dry, and classify materials as fine as possible. It will produce a uniformly fine product in the following manner: ... The patented Williams Impact Dryer Mill Venturi System was developed for processing coal and other materials. This is where specifications require minimum extreme ...
اقرأ أكثر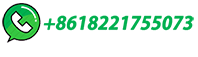
An On-Site Process for Removing Moisture from Low-Rank Coal
The total expected reduction in sulfur and mercury emissions for the fully configured commercial coal drying system at Coal Creek Station will equal the combination of the outright reduction in ...
اقرأ أكثر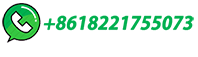
Coal drying in Europe – Part 1 | World Coal
Types of coal drying: hot gas drying A range of technologies has been developed to dry coal, including: hot gas drying, steam drying hydrothermal dewatering and mechanical thermal expression. Hot flue gas has been used in two drying processes: the rotary drum dryer and the flash mill pre-drying system.
اقرأ أكثر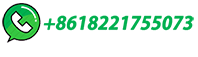
Evaporative Drying of Low-Rank Coal
Today, the most of the drying technologies are based on the evaporation of the water from the moist product. In this chapter, the most effective parameters on the …
اقرأ أكثر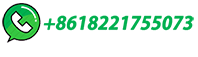
Thermokinetics of Brown Coal during a Fluidized Drying Process
This paper presents the results of research describing the thermokinetics of brown coal's (lignite) drying process in a fountain-bubble fluidized bed dryer. The drying medium was atmospheric air of a variable temperature in subsequent tests, which ranged from 27 to 70 °C. This paper presents the results of many experimental studies for two …
اقرأ أكثر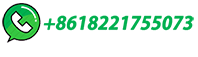
Dry milling
Dry milling IKA dry milling systems are a safe and efficient option for pulverizing and homogenizing materials. ... total surface area through smaller particle sizes and thus influencing the technology of processes is an example of IKA Dry mill capability. Specializing in process technology, IKA considers pulverization in terms of more than ...
اقرأ أكثر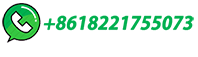
COAL PREPARATION AND FIRING
A larger separator can be used to enhance the drying capacity. Fine coal leaves the mill with the gas stream, the coal fineness is adjusted by altering the angle of the separator vanes, or the rotor speed. Coal drying is ensured by controlling the coal mill inlet temperature, to give a target mill exit temperature, usually between 70 and 900C.
اقرأ أكثر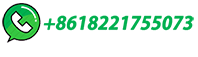
Dry Mill Rejects Handling system
Rejects discharged from coal mills are a mixture of different materials (iron pyrites, rocks, tramp metal, etc.) with pulverized coal. Magaldi engineered the MRS ® system to ensure their dry removal and mechanical …
اقرأ أكثر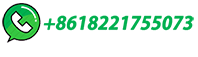
Pre-drying coal: technologies and economics
Pre-drying coal: technologies and economics Nigel Dong IEA Clean Coal Centre Webinar, 24 September 2014 . Bituminous, including anthracite 45% Sub-bituminous 32% Lignite 23% Global proved recoverable coal reserves, 2011: 891.5 Gt Low rank coal is abundant and reliable ... • Flash mill drying
اقرأ أكثر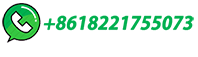
Raw Material Drying-Grinding
Inertization of coal mill circuit and fine coal bins with CO2, N2 or CO2+N2 to replace O2 which promotes spontaneous ignition of fine coal. ... Ball mills for cement raw material and coal equipped with a drying compartment adequately air swept with hot gas (2.5-3.5M/sec above the ball charge), can handle moisture about 8%. Fully air- swept ...
اقرأ أكثر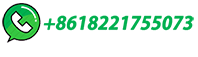
Air Swept Coal Mill
What Is Air Swept Coal Mill. The air-swept coal mill is also called a coal grinder. It is the main equipment of the cement plant, used for drying and pulverizing coal powder.It mainly consists of the feeding device, main bearing, rotary part, transmission device, discharging device, high-pressure starting device, and lubrication system.
اقرأ أكثر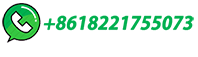
Improved Coal Fineness Improves Performance, Reduces Emissions
Heated (primary) air is supplied in the lower portion of the pulverizer to provide some coal drying and to transport the pulverized coal to the downstream combustion process.
اقرأ أكثر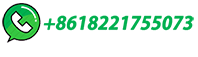
Mill Drying of Coal | J. Fluids Eng. | ASME Digital Collection
Abstract. This paper develops the fact that the drying of coal in the mill while grinding, instead of in separate driers previous to mill operations, makes possible large savings in equipment, building, and operating costs, besides making possible a net gain in boiler-plant efficiency in the order of 0.5 per cent. This gain is due to …
اقرأ أكثر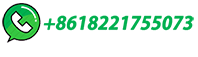
Coal Ball Mill | Grinding for Different Kinds of …
The raw material of coal powder is coal with various hardness, and it drying in the coal mill grinding process to obtain finished coal powder which can be efficiently burned. Coal ball mills are widely used in the …
اقرأ أكثر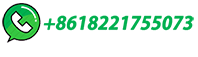
Ethanol Production and Distribution
Most ethanol in the United States is produced from starch-based crops by dry- or wet-mill processing. Nearly 90% of ethanol plants are dry mills due to lower capital costs. Dry milling is a process that grinds corn into flour and ferments it into ethanol with coproducts of distillers grains and carbon dioxide. Wet-mill plants primarily produce ...
اقرأ أكثر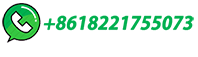
Wet and dry grinding of coal in a laboratory-scale ball mill: …
1. Introduction. Coal has an important role in electricity generation worldwide. According to data from the World Coal Association, coal-fueled power plants currently provide 37% of the global electricity [1].In 2017, China's coal-fired power generation accounted for 64.5% of the total power generation [2].Nearly 1.76 billion tons coal …
اقرأ أكثر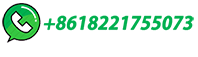
sbm model gas solid drying coal mill.md
Coal Milling And Drying Process model gas solid drying coal mill « coal russian.Coal Drying Process on Emissions station service power,lower plant efficiency,and higher mill,coal pipe and burner ….of Coal Creek Unit 1 and all gas and solid. Pressurised flash drying of Yallourn lignite ScienceDirect Pressurised flash drying of ...
اقرأ أكثر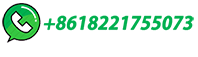
Investigation of the effects of different drying methods on coal …
Binocular microscopic images were used to determine the shape factors of coal particles. A dry ball milling process was carried out as a function of grinding time (60–960 s) and representative ...
اقرأ أكثر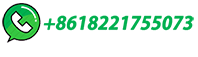
An investigation of performance characteristics …
performance of coal mill from grinding, drying, and classification viewpoint. Also, this . study illustrates association of impact of pulverizer operation parameters on the energetic .
اقرأ أكثر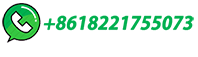
MPS mills for coal grinding
Pfeiffer SE supplies stand-alone MPS coal grinding mills as well as complete coal grind ing-drying systems. Both mill and grinding system can be operated under pressure or suction as well as under air or inert gas atmosphere. System configurations cover grinding plants with temporary storage of the pulverized coal in …
اقرأ أكثر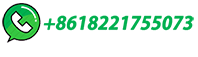