Ball-milling – Nanoscience and Nanotechnology I
The ball milling process can be summed up as: a. It consists of stainless steel chamber and several small iron, silicon carbide, hardened steel, or tungsten carbide balls to rotate …
اقرأ أكثر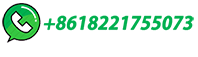
Ball milling: a green technology for the preparation and
Ball milling is a simple, fast, cost-effective green technology with enormous potential. One of the most interesting applications of this technology in the field of cellulose is the preparation and the chemical modification of cellulose nanocrystals and nanofibers. Although a number of studies have been repo Recent Review Articles Nanoscale …
اقرأ أكثر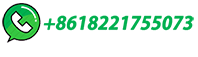
Ball Milling
Ball milling is an auxiliary process for the micro/nanomaterials production in large scale using biomass waste as the feedstock. There are no major drawbacks of this method in …
اقرأ أكثر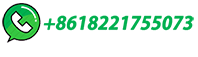
Ball Milling
Ball milling is a grinding method that grinds nanotubes into extremely fine powders. During the ball milling process, the collision between the tiny rigid balls in a concealed …
اقرأ أكثر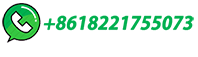
Ball milling: a green technology for the preparation and
Ball milling: a green technology for the preparation and ...
اقرأ أكثر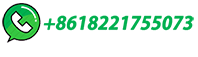
CNC Milling
A common milling operation to produce convex and concave parts. The process includes 3 steps – roughing, semi-finishing and finishing. Roughing uses round inserts to do the initial work for removing most of the material. Ball-nose end mills are the perfect fit for semi-finishing and finishing.
اقرأ أكثر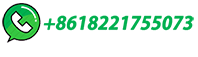
Ball milling as a mechanochemical technology for …
Mechanochemical technique aims to strike a balance between defect formation via ball milling and size adjustment of a solid grain to nanoscale (<1000 nm) (Ullah et al., 2014).During the process, a high-energy mill is employed and a specific powder charge is placed along with a milling medium (Lin et al., 2017).The kinetic …
اقرأ أكثر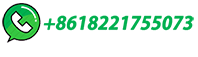
Exploring Ball Mill Diagram: A Comprehensive Guide
The grinding action in a ball mill is achieved through two primary fragmentation mechanisms: attrition and the impact. Impaction happens when the …
اقرأ أكثر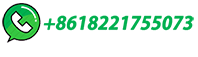
What Is a Ball Mill and How Does It Work?
The ball mill rotates around a horizontal axis, allowing the grinding process to take place as the balls reduce the material to a fine powder. A mill consists of …
اقرأ أكثر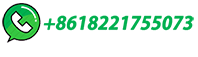
Milling Process – Definition, Milling Manufacturing Processes
Milling is a process performed with a machine in which the cutters rotate to remove the material from the work piece present in the direction of the angle with the tool axis. ... The geometric form created by milling fall into three major groups: Plane surfaces: the surface is linear in all three dimensions. The simplest and most convenient ...
اقرأ أكثر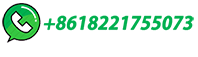
Ball Milling
Reactive ball milling. Reactive ball milling method is to mill starting materials under various gas atmospheres. In hydrogen storage research field, this method is used to synthesize hydrides of metals and alloys at low temperature by milling under certain hydrogen pressure, to form metal hydrides whose alloy phase is not stable (e.g., Mg 2 …
اقرأ أكثر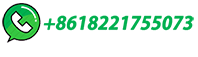
Nanomaterials | Free Full-Text | High-Energy Ball Milling for …
The current production method of nanobiochar (NBC), an emerging, environmentally friendly nanocarbon material, is tedious and lengthy. Therefore, in this study we aimed to improve the productivity of NBC via high-energy ball milling by manipulating the grinding media and processing time. The particle size distribution of the …
اقرأ أكثر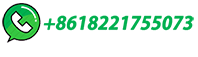
Milling Process, Defects, Equipment
Milling is the most common form of machining, a material removal process, which can create a variety of features on a part by cutting away the unwanted material. The milling process requires a milling machine, workpiece, fixture, and cutter. The workpiece is a piece of pre-shaped material that is secured to the fixture, which itself is attached ...
اقرأ أكثر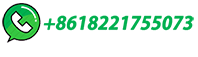
Hydrolysis reaction of ball-milled Mg-metal chlorides …
There's a replacement reaction occurred during the ball-milling process between Mg and chlorides, and the product can form a typical micro-galvanic cell with Mg in the chlorides solution. The Mg-10 wt% FeCl 3 composite ball-milled for 30 min has the best hydrolysis properties especially for its 1479.1 ml*g −1 min −1 initial hydrogen ...
اقرأ أكثر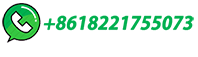
Two-stage ball milling of recycled machining chips to create …
The granules were subsequently ball milled to form powders. ... The interrupted two-stage milling means the ball milling process was stopped at 12-h intervals to collect powder samples to investigate the morphology evolution. All powders were sieved for 15 min using a Ro-tap RX-29 sieve shaker (W.S. Tyler, Mentor, Ohio) and four …
اقرأ أكثر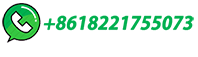
Face Milling 101: Process, Differences, And Practical Tips
Face milling is a machining process used for preparing large, flat surfaces on a workpiece. This can be preparatory, in perfecting the squaring of a material billet that is to be the subject of extensive machining, or it can be a finishing operation to render a mating or seal surface perfectly flat and perpendicular, ready for assembly/fitting.. The process …
اقرأ أكثر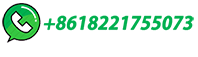
Glass Milling in the Production of Specialty Glass Powders
Image Credit: Mo-Sci Corp. The most common forms of glass provided by Mo-Sci are microspheres, ingots, and glass powder. Powdered glass, in particular, is central to a range of applications throughout industry and research; for example, glass nanofillers offer distinct benefits to the development of composite materials used in dental and …
اقرأ أكثر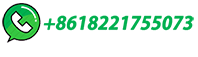
Grinding in Ball Mills: Modeling and Process Control
The feed material is typically composed of the BFRs and the catalyst, both in powder form. As the cylinder starts to rotate, the grinding balls inside the cylinder crush and grind the feed ...
اقرأ أكثر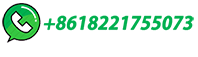
Ball Form Millling Process
This process of ball milling is done approximately 100 to 150 hrs to get uniform fine powder. 4. Ball milling is a mechanical process and thus all the structural and chemical changes are produced by mechanical energy. I have seen an interesting image at for ball milling method at wikipedia. You can see the image here. Advantages of ball milling ...
اقرأ أكثر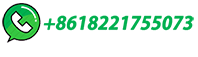
What is a ball mill and What are Its Advantages and …
Ball mills are cylindrical and often the grinder of choice when mashing paints, ores, ceramic materials, and certain hard chemicals. A ball mill can effectively convert a …
اقرأ أكثر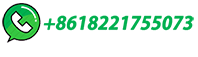
Ball Mill
The ball milling process is carried out for approximately 100–150 ... Ball mills are commonly used for crushing and grinding the materials into an extremely fine form. The ball mill contains a hollow cylindrical shell that rotates about its axis. This cylinder is filled with balls that are made of stainless steel or rubber to the material ...
اقرأ أكثر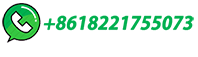
All About Milling in Machining | Xometry
Milling is a versatile machining process that can be applied to a wide range of materials, including: metals, plastics, and composites. The suitability of a material for milling depends on factors such as its machinability, hardness, and the specific form of milling operation. Listed below are the materials suitable for milling:
اقرأ أكثر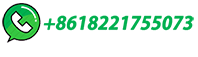
ball milling process: Topics by Science.gov
Process engineering with planetary ball mills.. PubMed. Burmeister, Christine Friederike; Kwade, Arno. . Planetary ball mills are well known and used for particle size reduction on laboratory and pilot scales for decades while during the last few years the application of planetary ball mills has extended to mechanochemical …
اقرأ أكثر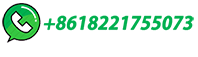
A Simple and Effective Physical Ball‐Milling Strategy to …
The covalent cross-linking within PMP hydrogel (Figure 1a) determines its physical properties.In the aqueous solution, borax forms boronic acid B(OH) 3 and tetrahedral boronate ions [B(OH) 4 −]. [] The [B(OH) 4 −] ions with four -OH groups at each corner reacts with PVA chains and/or MXene@PPy mixture to initiate strong interactions …
اقرأ أكثر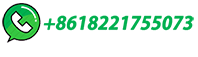
Producing Metal Powder from Machining Chips …
In the pursuit of achieving zero emissions, exploring the concept of recycling metal waste from industries and workshops (i.e., waste-free) is essential. This is because metal recycling not only helps …
اقرأ أكثر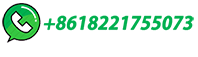
Ball Milling Method for Synthesis of Nanomaterials
Schematic view of motion of the ball and powder mixture. During the high-energy ball milling process, the powder particles are subjected to high energetic impact. Microstructurally, the mechanical alloying process can be divided into four stages: (a) initial stage, (b) intermediate stage, (c) final stage, and (d) completion stage.
اقرأ أكثر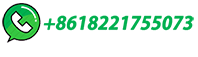
Amorphization of different furosemide polymorphic …
recrystallization caused by sample heating during the milling process (Jensen et al., 2015). Form Ⅰ ball milled for 5 min and 120 min are referred to as form I-5 min and form I-120 min, respectively. The same description is applied for forms Ⅱ and Ⅲ and other milling times. All independent milling experiments were performed in triplicates
اقرأ أكثر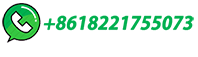
Exploring ball milling theory: A comprehensive guide
Ball milling is a fundamental and widely utilized technique in material processing. Understanding the principles behind ball milling theory is crucial for achieving optimal milling outcomes and maximizing the benefits of this versatile technique.
اقرأ أكثر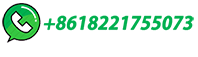
Exploring the relationship between solvent-assisted ball …
Garnet-type solid electrolytes, such as Li 6.4 La 3 Zr 1.4 Ta 0.6 O 12 (LLZTO), are promising materials for solid-state batteries, but processing remains a challenge, in part due to the high sintering temperature required for densification. This temperature can be lowered by decreasing the initial particle size via solvent-assisted …
اقرأ أكثر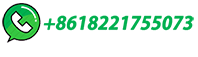
Ball Mill (Ball Mills Explained)
Ball Mill Introduction . There are three main stages to mineral processing in the mining industry.These are: Comminution (crushing and grinding).; Beneficiation (separation and concentration).; Smelting and refining.; Ball mills are employed in the comminution stage as grinding machines (size reduction).The purpose of grinders in the mining industry is to …
اقرأ أكثر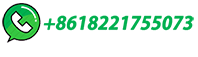