Hammer crusher
Spindle support rotor hammer crusher main parts, bear the weight, impact force from the rotor, hammer, thus requiring the spindle material has high strength and toughness, the design uses a 35 silico-manganese molybdenum vanadium steel forging.Circular end surface of the spindle, the maximum diameter of 130 mm, the bearing is 80 mm. …
اقرأ أكثر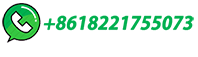
Modelling the cement process and cement clinker quality
limits applications to specific plants and limited process variations in terms of process parameters. A process model that included plant-specific parameters of a cement plant using thermochemical data from Fact, where no mixed solution phases were included, was developed by Modigell et al. (2002). The linking of coupled
اقرأ أكثر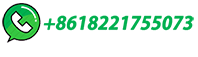
Plants | JK Cement
The quality management system at JK Cement Works is certified by the Prestigeous Lloyds Register for quality assurance since the year 1995. Our plants are also ISO 9001:2008 & ISO 14001:2004 certified and are in the process of getting our laboratory accredited with the NABL-National Accreditation Board for Testing and Calibration Laboratories.
اقرأ أكثر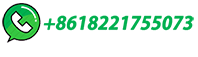
A practical guide to improving cement manufacturing …
The cement production process 1. The Quarry: The cement production process begins with the extraction of limestone and clay from the quarry. 2. Crusher and Pre-Blending: …
اقرأ أكثر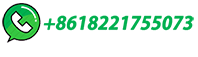
Cement Industrial Process: Modeling and Optimization …
The crusher specific electrical energy represents the energy consumed by the different elements of the crusher to produce a ton of cement. The major equipment that …
اقرأ أكثر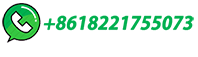
Hammer Crusher Working Principle
We take a Φ900 x 900mm single rotor, irreversible multi-row hinged hammer crusher as an example to introduce its structure and parts. This type of hammer crusher is commonly seen in cement plants and is suitable for crushing limestone, coal, and other medium hardness ores. It is mainly composed of a transmission device, rotor, lining …
اقرأ أكثر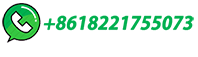
Cement grinding optimisation
Pre-crushing of cement clinker using a Barmac crusher offers realistic benefits to a cement plant in terms of process efficiency. • The introduction of the Barmac crusher can increase the cement circuit throughput in order of 10–20%, providing that there is no capacity limitation in other parts of the circuit.
اقرأ أكثر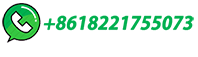
Cement Manufacturing Process
Generally cement plants are fixed where the quarry of limestone is near bye. This saves the extra fuel cost and makes cement somehow economical. Raw materials are extracted from the quarry and by means of conveyor belt material is transported to the cement plant. There are also various other raw materials used for …
اقرأ أكثر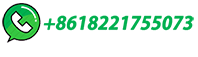
Cement Manufacturing and Process Control | SpringerLink
The major raw materials used as a source of CaO for cement manufacturing are limestone, chalk, marl, etc. These raw materials by virtue of their natural occurrence contains other mineral impurities e.g, MgO, SiO 2, Al 2 O 3, Fe 2 O 3, alkali compounds, and sulfides.These impurities play an important role to influence the cement …
اقرأ أكثر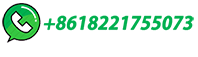
Cement Manufacturing Process
Extraction of raw material and crushing of material. Generally cement plants are fixed where the quarry of limestone is near bye. This saves the extra fuel cost and makes cement somehow …
اقرأ أكثر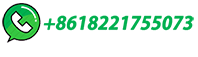
Cement Manufacturing Process
The rock pile loaded to the loading machine is either fed to a primary crusher in the quarry, the product of which is further transferred to the cement works, or …
اقرأ أكثر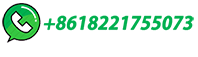
Cement Clinker Manufacturing Process with Reactions
Extraction and Preparation of Raw Materials. The main raw materials (limestone, clay chalk or basalt) are quarried from natural rocks. They are crushed and transferred to pre-blending storage where other substances (such as sand, iron ore, bauxite, shale, slag, fly ash) are added to get the desired chemical composition.
اقرأ أكثر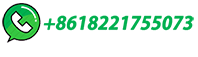
Cement Crusher and Cement Lump Breaker Solutions
Franklin Miller's Cement Crusher and Cement Lump Breaker solutions are designed to optimize your cement production process, enhancing efficiency, and reducing downtime. Our robust and reliable equipment ensures consistent material sizing and flow, allowing you to focus on producing high-quality cement products for your customers.
اقرأ أكثر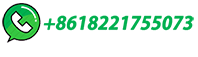
Everything you need to know about Crushers in Cement …
SUMMARY. The compression type crushers like jaw and gyratory crushers are used for hard and abrasive raw materials. Because of their limited reduction ratio of 3 : 1 to 7 : 1 …
اقرأ أكثر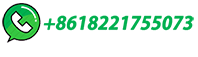
Types of Cement Crushers | Choosing the Right Machine
Types of Cement Crusher Machines. While there may be different types of cement crushers available, the basic working principle is the same. The cement crusher machines are designed to crush large-sized raw materials into smaller pieces, making them suitable for further processing. Here are some common types of cement crusher machines.
اقرأ أكثر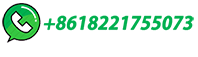
Cement Clinker Calcination in Cement Production Process | AGICO Cement
Raw Materials Crushing, Storing and Grinding. Clinker calcination is the most crucial part of the whole process of cement manufacturing. At this stage, ground raw materials will be sent into the cement kiln and be heated at a high temperature to produce chemical reactions with each other, eventually forming clinker. In addition, clinkers that just …
اقرأ أكثر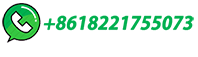
The Cement Plant Operations Handbook
Providing a comprehensive guide to the entire cement production process from raw material extraction to the finished product, the industry's favourite technical reference book is now fully updated with new material and an extended chapter on alternative fuels.
اقرأ أكثر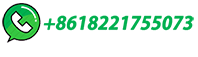
What Is The Crushing Process
Although there is no limit set, the downsizing process over 3 mm is considered as "crushing" and the ones below 3 mm are considered "grinding". Even though the ore is reduced below 3 mm with conical and some impact crushers, this process is called crushing. The process of size reduction is defined by below conversion formula:
اقرأ أكثر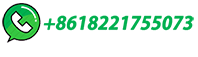
Impact crushers | FL Cement
Many cement plants process oversize limestone boulders that often contain a lot of clay and sand, necessitating a crusher that can handle feed with both large-size blocks and some sticky materials. Our EV impact hammer crusher uses a horizonal feed system to process abrasive and moderately sticky raw materials in just one stage – providing ...
اقرأ أكثر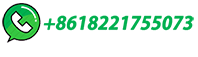
EC Cement Plant
Egyptian Cement greenfield plant is located at Suhag Governorate, about 400 KM south Cairo. It is the newest Cement Plant in Egypt and the region established on area around one million m2 and equipped with the latest technology. the production line using the dry process method with capacity 6000 TPD clinker, however the plant designed to reach a …
اقرأ أكثر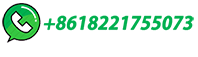
Clinkerization
Brick Lining of Cyclones: All preheater components need to be lined from inside with appropriate refractory to save shell/components from heat and to hold heat inside for process use. Refractory castable, Bricks, Insulation Bricks are used in preheater. Calciner. Calciner serves the purpose of decomposition of carbonates into reactive oxide calcium …
اقرأ أكثر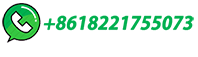
Impact Crusher
In the working process of the machine, the rotor rotates at a high speed driven by the motor. When materials enter the crushing chamber, they will be impacted and crushed by the blow bar on the rapidly turning rotor, …
اقرأ أكثر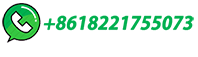
The Complete Guide to Primary Crushing, Secondary Crushing…
Learn everything you need to know about primary crushing, secondary crushing, and tertiary crushing in this comprehensive guide. Discover the types of crushers used in each stage, their working principles, and the advantages and disadvantages of each process. Get answers to frequently asked questions and …
اقرأ أكثر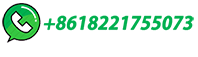
Chapter 4 Cement Manufacturing and Process Control
Cement Manufacturing and Process Control 4.1 Cement Manufacturing: Basic Process and Operation To design the Refractory for the lining of different equipments in a cement plant, it is necessary to understand the total operational process of a cement plant in depth. It is necessary to know the conditions prevailing in different equipments and the
اقرأ أكثر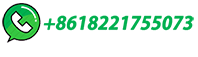
Jaw Crusher
Mini Cement Plant Hot Sale; Cement Plant 700 ~ 2000tpd; Cement Plant 2500~7000tpd; Cement Types Menu Toggle. OPC Manufacturing Plant; ... It usually requires two crushing stages to make raw materials into cement raw mix for further process, the first stage is a coarse crushing stage, and the second is fine crushing. Jaw crushers are well suited ...
اقرأ أكثر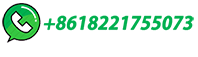
cement plant process crusher equations
Laboratory Crushers Pulverizers Grinders. We have the right crusher pulveriser grinder or mill for the laboratory to pilot plant sample processing We serve all major industries such as mining and metallurgy chemistry pharmaceutical cement material engineering environment agri food biotech commercial laboratories and research centres.
اقرأ أكثر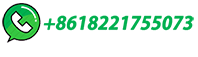
Cement Roller Press, Roller Press In Cement Plant | HPGR Crusher
The cement roller press, also known as roller press in cement plant, high pressure grinding roll (HPGR), is a kind of cement equipment for brittle materials, apply for grinding cement clinker, cement raw material, gypsum, coal, quartz sand, iron ore, blast furnace slag, and other materials.. The cement roller press is generally applied to the cement …
اقرأ أكثر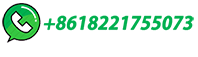
Complete Lecture about Crushers in Cement Industry
Previous Post Next Post Contents1 Coarse size reduction of raw materials in Cement Industry1.1 Size reduction machinery and methods1.1.1 A Machinery for size reduction in the coarse range (crushers) by application of compression:1.1.2 B Crushers for size reduction by impact:1.1.3 C For comminution in the fines range (grinding mills) by …
اقرأ أكثر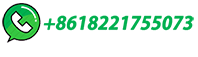
Hammer Crusher Working Principle
The structure design of a hammer crusher. We take a Φ900 x 900mm single rotor, irreversible multi-row hinged hammer crusher as an example to introduce its structure and parts. This type of hammer crusher is commonly seen in cement plants and is suitable for crushing limestone, coal, and other medium hardness ores. It is mainly composed of a …
اقرأ أكثر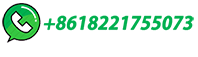
Cement Plant: The Manufacturing Process 4 5
Cement Plant: The Manufacturing Process worldcementassociation 1 Limestone (CaCO3) is taken from a quarry 2 4 3 The limestone is fed into a crusher and then stored until needed The clinker is mixed with additives, such as gypsum, and then ground in a cement mill, which creates cement The cement is then packed and distributed to …
اقرأ أكثر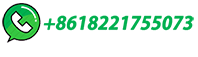