Resistance to Grinding and Cement Paste Performance of
Grinding of finished cement is performed in a single stage, intergrinding materials with very different grindabilities. This intergrinding process has many different …
اقرأ أكثر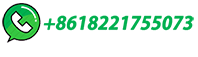
Cement Grinding
Classification of Separating Principles •„critical particle": balance between mass and flow forces on the particle F Z = centrifugal force F S = flow force F R = resulting force F tangential F radial. 8 Cement Production Technology –Cement Grinding –Mechanical Design and Function of Separator Contents Topic 1 Separators –General ...
اقرأ أكثر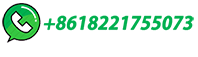
in cement industry
in cement industry VENKATESH.N1, THULASIMANI.G 2, BALAKRISHNAN.R 3, KARTHIKRAJA.P 4, ANANTHAKUMAR.S 5, GOKUL.R 6 . ... clinker to grinding plants in areas where cement-making raw materials are not available. ... Operating principle of Hydraulic Roller Press . The feed material (cement clinker, slag or other ...
اقرأ أكثر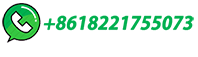
(PDF) Performance Evaluation of Vertical Roller Mill in Cement Grinding
The cement industry is the main supplier of raw materials for the production of concrete and reinforced concrete. For grinding cement, two types of mills are used - ball and roller.
اقرأ أكثر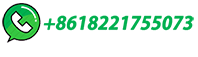
Application of Vertical Roller Mill in Cement Production
Learn how vertical roller mill technology is transforming the cement industry. Explore its benefits, efficiency, and eco-friendly features. Discover why it is the go-to solution for sustainable cement production. ... The vertical roller mill operates on the principle of grinding materials between a rotating grinding table and a set of grinding ...
اقرأ أكثر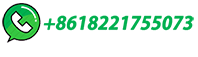
The Cement Plant Operations Handbook
Cement milling 110 111 The Cement Plant Operations Handbook – Seventh Edition 6. Cement milling Finish milling is the grinding together of clinker with some 3-5 per cent gypsum, natural or synthetic, for set control, and quite often other components: blastfurnace slag, pozzolan, silica fume, limestone or pulverised fuel ash ('pfa'
اقرأ أكثر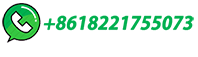
The Cement Plant Operations Handbook
raw materials, burning, grinding and quality control are supported by a range of chapters addressing critial topics such as maintenance and plant reporting, alongside a detailed …
اقرأ أكثر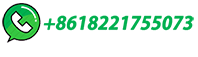
Cement Grinding
Cement grinding using Grate Discharge principles developed in the ore milling industry applied to the cement industry. This experience plus the years of manufacturing know how unquestionably …
اقرأ أكثر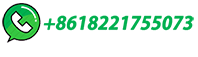
Vertical Roller Mill VS Roller Press in Cement Industry
Tube mill has been used as the main grinding equipment in the cement industry for a long time, and it is still widely used because of its simple structure, easy operation, and low price. However, the energy utilization rate of tube mills is only 2% ~ 20%, which is very low. ... Grinding Principle. Both the vertical roller mill and roller press ...
اقرأ أكثر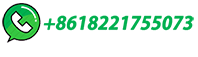
Latin American Cement Industry Invests To Reduce CO2 …
Latin American Cement Industry Invests To Reduce CO2 Emissions; ... in the drying stage of the inputs, before they enter the grinding process, instead of charcoal, the kilns use vegetable fuels such as waste bamboo chips and eucalyptus. ... The HPS kiln is a compact single-shaft kiln that operates on the counterflow principle and into which …
اقرأ أكثر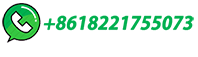
Milestone Trends in Indian Cement Industry
KHD charts its green footprints on the road to low carbon emissions. India is the second largest cement producer in the world and accounted for over 8 per cent of the global installed capacity. Of the total capacity, 98 per cent lies with the private sector and the rest with the public sector. The top […]
اقرأ أكثر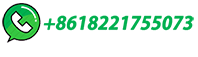
Sustainable transition towards biomass-based cement industry…
The distribution of electricity consumption across critical unit operations is as follows: cement grinding (31–44 ... (reconfiguring existing cement systems) and landscape pressures. The cement industry, being a ... biomass feedstocks in cement manufacturing or the generation of biofuels and implement robust biomass ash …
اقرأ أكثر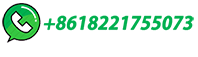
Cement Raw Meal & Homogenization Process in The Cement Industry
Cement Grinding Menu Toggle. Hydraulic Roller Press; High Pressure Grinding Roll; Cement Ball Mill; ... they all follow the same basic principle: ... the raw meal homogenization silo used in the cement industry is generally multi-material flow silo, because this homogenization silo can not only ensure a good homogenization effect but …
اقرأ أكثر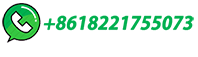
Cement Milll Separator | Cyclone Air Separator in Cement …
Cement mill separator, or cement separator, is a type of equipment that was widely used in the cement grinding system and raw mill system of cement plants.The function of the separator is to separate the fine-sized particles from the coarse-sized particles, so as to avoid material condensation and over grinding in the mill, and improve the milling …
اقرأ أكثر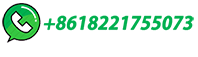
Separators in the cement industry
in order to achieve a certain percentage of residue on 30µm (From Duda Cement Data Book). - For example, to get 20% residue on 30µm, a turbo separator needs to produce a cement at 3200-3900 Blaine and a : …
اقرأ أكثر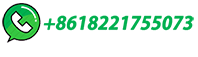
Predictive Control of a Closed Grinding Circuit System in Cement Industry
Cement industry is considered as a strategic industry all over the world (Shen et al., 2017). The operational cost of implementing manufacturing processes in this industry is so high that a few ...
اقرأ أكثر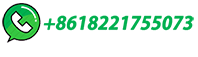
Performance Evaluation of Vertical Roller Mill in Cement …
grinding and separation mechanisms individually. Schematic view of a typical vertical roller mill with the streams is illustrated in Figure 1 and Table 1 gives the
اقرأ أكثر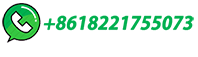
Predictive Control of a Closed Grinding Circuit System in Cement Industry
This paper presents the development of a nonlinear model predictive controller (NMPC) applied to a closed grinding circuit system in the cement industry. A Markov chain model is used to characterize the cement grinding circuit by modeling the ball mill and the centrifugal dust separator. The probability matrices of the Markovian …
اقرأ أكثر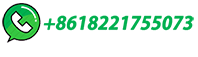
Operational parameters affecting the vertical roller mill …
Sustainable operations and proven benefits of the technology in cement grinding applications attracted interests of the mineral industry. Within the scope of the study, ore grinding performance of the VRM was investigated via a mobile grinding plant and relationships between operational parameters were identified.
اقرأ أكثر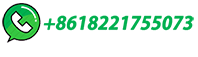
Everything you need to know about Crushers in Cement industry
Generally speaking, crushing denotes the size suitable as feed for the next main stage, i.e, grinding. In present – day cement manufacture, with due regard to the possibilities of the reduction machinery employed, crushing is taken to mean reducing the particle size between about 80 and 20 mm. ... In the cement industry, which uses chiefly ...
اقرأ أكثر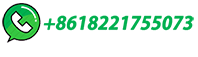
A Comprehensive Guide to the Cement Manufacturing Process
Cement manufacturing is an industry that involves several steps, including the gathering of raw materials. ... Raw material grinding. After crushing, the raw …
اقرأ أكثر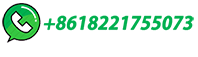
Cement Grinding Unit & Process | High Quality …
Explore Amrit Cement's state-of-the-art cement grinding unit. Learn about our cement grinding process and plant stages for high quality cement.
اقرأ أكثر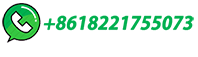
Vertical Roller Mill Operation in Cement Plant
The vertical roller mill (VRM) is a type of grinding machine for raw material processing and cement grinding in the cement manufacturing process.In recent years, the VRM cement mill has been equipped in more and more cement plants around the world because of its features like high energy efficiency, low pollutant generation, small floor area, etc.. The …
اقرأ أكثر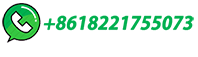
Grinding Machine: Definition, Parts, Working Principle, Operation
A grinding machine is a production machine tool used in the manufacturing industry in which the grinding wheel is attached in the tool post and the workpiece is fixed to the work table and when the operation starts it removes the unwanted material to get the desired surface finish, correct size, and accurate shape of the workpiece.
اقرأ أكثر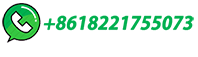
Cement Ball Mill Maintenance
BALL MILL INSPECTION PROCEDURE. source : Introduction. This document is intended to help the staff of the cement plants. On a process point of view, a mill inspection is only representative if the grinding mill circuit is in a steady working condition with a representative cement product.
اقرأ أكثر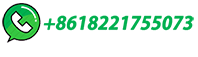
Energy-Efficient Technologies in Cement Grinding
In this chapter an introduction of widely applied energy-efficient grinding technologies in cement grinding and description of the operating principles of the related equip‐ ments and comparisons over each other in terms of grinding efficiency, specific energy consumption, production capacity and cement quality are given. A case study per‐ …
اقرأ أكثر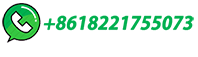
OPTIMIZATION OF CEMENT GRINDING OPERATION IN …
Condition in one of the grinding chambers of the mill . Results of Optimization . The graphical analysis presented in Figure 2 represents progress of grinding along the length of the mill after optimizing the grinding process. rogress of grinding is clearly visible in Desired p the graphs. Figure -2: Analysis of longitudinal samples.
اقرأ أكثر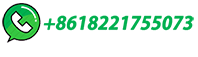
Cement Grinding
Feed material is provided by air slide. Material falls onto centre of dispersion disc, is accelerated radially and distributed evenly in separating area. Fan blow separating air (recirculation or fresh air) into spiral housing and through the curved guide vanes where …
اقرأ أكثر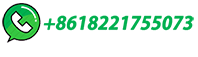
Ball Mill Grinding Machines: Working Principle, Types, Parts
Explore the working principle, types, parts, applications, advantages, and recent developments of ball mill grinding machines. ... Cement Industry: Ball mills are extensively used in the cement industry for grinding raw materials, clinker, and additives to produce cement. The ability to finely grind materials and control the grinding process ...
اقرأ أكثر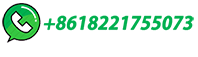
Research of iron ore grinding in a vertical-roller-mill
VRM's are well-established grinding equipment for various tasks in the coal and cement industry today. In terms of numbers of new installed units in the cement industry VRM's have overtaken ball mills for a few years, which makes VRM's the leading mill technology (Harder, 2010). 2. Experimental2.1. Pilot scale mill LM4.5
اقرأ أكثر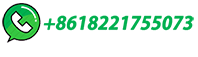