How it Works: Crushers, Grinding Mills and Pulverizers
Ball mills typically use water or other liquid and additives to help reduce friction and provide cooling during the grinding process. The feed enters one end of the ball mill, and discharges out the other end. Ball mills vary greatly in size, from large industrial ball mills measuring more than 25 ft. in diameter to small mills used for …
اقرأ أكثر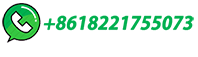
Ball Mill Grinding Machines: Working Principle, Types, Parts
Explore the working principle, types, parts, applications, advantages, and recent developments of ball mill grinding machines. Discover how these versatile tools …
اقرأ أكثر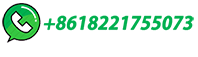
Ball Mill Success: A Step-by-Step Guide to Choosing the Right Grinding …
Grinding media, pivotal for the efficacy of the ball milling process, come in various materials, each offering unique characteristics and advantages tailored to specific applications. Ceramic Balls: Composed of materials like silicon nitride, alumina, and zirconia, ceramic balls are favored for their exceptional hardness and resistance to ...
اقرأ أكثر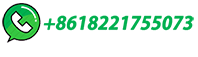
Ball Mills
Ball Mills. Ball mills have been the primary piece of machinery in traditional hard rock grinding circuits for 100+ years. They are proven workhorses, with discharge mesh sizes from ~40M to <200M. ... We primarily process 6-8lb motor stators, smaller transformers and radiator ends to separate out the clean copper. ...
اقرأ أكثر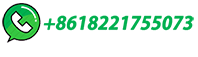
Ball Milling
Ball milling technique, using mechanical alloying and mechanical milling approaches were proposed to the word wide in the 8th decade of the last century for preparing a wide spectrum of powder materials and their alloys. In fact, ball milling process is not new and dates back to more than 150 years. It has been used in size comminutions of ore, …
اقرأ أكثر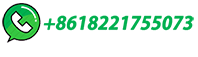
Ball mill: Principles, construction, working, uses, merits, and
A ball mill is a type of grinder or mill used to mill the materials into fine powder in pharmaceutical, chemical, or metallurgical industries. Ball milling relies on the …
اقرأ أكثر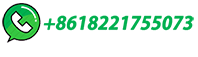
Disturbance observer based multi-variable control of ball mill grinding
The grinding process is a size reduction operation used in the mineral industry to liberate the valuable minerals from the coarse ore. The typical plant flowsheet of a ball mill grinding circuit is shown in Fig. 1, which consists of a ball mill, a pump sump, hydro-cyclones and solids feeding conveyors. Download : Download full-size image; Fig. 1.
اقرأ أكثر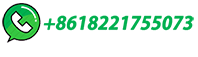
Grinding in Ball Mills: Modeling and Process Control
Keywords: Ball mills, grinding circuit, process control. I. Introduction Grinding in ball mills is an important technological process applied to reduce the size of particles which may have different nature and a wide diversity of physical, mechanical and chemical characteristics. Typical examples are the various ores,
اقرأ أكثر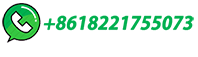
BALL MILLS Ball mill optimisation
grinding process. Clinker grain sizes depend on pre-crusher settings but are in some cases still up to 50mm when fed to the ball mill and therefore, it is necessary to adjust …
اقرأ أكثر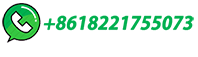
SAG Mill Grinding Circuit Design
These mills typically grind ROM ore in a single stage. A large example of such a mill was converted from a single-stage milling application to a semi autogenous ball-mill-crushing circuit, and the application is well described. This refers to high-aspect AG/SAG mills. Ball Charge Motion inside a SAG Mill. With a higher density mill charge.
اقرأ أكثر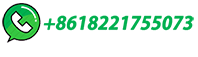
Fine grinding: How mill type affects particle shape characteristics …
A generic description provided by King (2001) ... in both cases grinding in a ball mill is being compared to grinding in the high shear environment of a stirred mill. ... A method using 2-D images obtained from SEM-based image analysis system to model mineral liberation in regrind stirred mills. In: MEI Process Mineralogy'14, Cape Town ...
اقرأ أكثر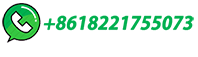
Optimization of Cement Grinding Operation in Ball Mills
Cement ball mills typically have two grinding chambers. The first chamber is filled with larger diameter grinding media and lined with lifting liners. ... The graphical analysis in Figure 2 represents the progress of the grinding process along the length of the mill. In a correct operation the residue will be high initially, falling gradually ...
اقرأ أكثر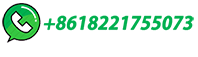
Energy-Efficient Technologies in Cement …
In this chapter an introduction of widely applied energy-efficient grinding technologies in cement grinding and description of the operating principles of the related equipments and comparisons over …
اقرأ أكثر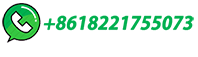
Grinding in Ball Mills: Modeling and Process …
The paper presents an overview of the current methodology and practice in modeling and control of the grinding process in …
اقرأ أكثر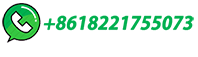
Simulation and optimization of a two-stage ball mill grinding …
The grinding circuit investigated in the current study is a two-stage grinding circuit (Fig. 2) in which two overflow type mills are arranged in series and operated under wet condition.The run-of-mine ore was crushed to 10 mm, and it was then fed to the first ball mill, which was closed by a rake classifier.The second mill operated in a combined …
اقرأ أكثر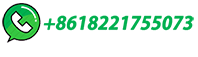
Ball Mills, Pebble Mills, Material Processing Mills
Ball Mills, Pebble Mills, Material Processing Mills: For more than a century, Patterson has been the industry leading manufacturer of wet and dry grinding mills for size reduction or dispersal. Patterson's ball, pebble and rod mills are built to last. We are still filling parts requests for mills sold over 60 years ago. Patterson mills are available in a wide variety …
اقرأ أكثر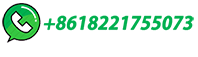
Demystifying the Ball Milling Process: Expert Insights
The ball milling process is carried out by using balls, which can be steel balls or ceramic balls, to apply force on the feed materials to reduce its size through impact and attrition as the balls fall from near the top of the shell. ... Grinding Method Description Pros and Cons; Ball Mill: A cylindrical device used for grinding materials like ...
اقرأ أكثر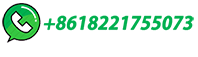
Demystifying the Ball Milling Process: Expert Insights
A ball mill is a type of grinder used to reduce the size of materials through grinding and particle size reduction process. Its primary application is to disintegrate …
اقرأ أكثر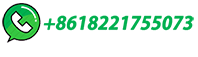
Walking Through the Ball Milling Process | Economy Ball Mill
Grinding Media Size and Weight: The size and weight of the grinding media can dramatically influence the milling action. Balls made of more dense media can produce a coarse grind, while lighter balls lead to a finer grind. The choice of media depends on the material being milled and the desired particle size.
اقرأ أكثر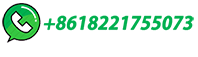
CANADIAN ALLIS CHALMERS 9' x 7' (2.7m x 2m) Ball Mill, …
GRINDING EQUIPMENT; BALL MILLS; CANADIAN ALLIS CHALMERS 9' x 7' (2.7m x 2m) Ball Mill, 400 HP ... Brief Description . CANADIAN ALLIS CHALMERS 9' x 7' (2.7m x 2m) Ball Mill, 400 HP (295 kW) Canadian AC Mill ; Herringbone Gear ; WANT TO SELL SIMILAR EQUIPMENT?
اقرأ أكثر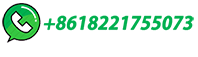
Ball Grinding Process
Ball grinding process is a grinding method of crushing ore with ball-shaped grinding medium in the grinding mill. In the ball grinding process, because the …
اقرأ أكثر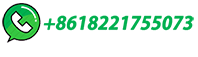
Constrained model predictive control in ball mill grinding process
Grinding process. The grinding process studied in this paper operates in a closed loop as shown in Fig. 2, including a ball mill and a spiral classifier. The feed, iron ore (from primary crusher, size ≤ 14 mm) is fed into the ball mill by swaying feeders.The tumbling action of the balls within the revolving mill crushes the feed to finer sizes.
اقرأ أكثر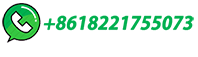
Ball Milling
Ball milling is a grinding technique that grinds and blends bulk material into extremely fine powders. From: International Journal of Hydrogen Energy ... Meanwhile, the milling balls will also break the deformed aluminum particles. Therefore, the ball milling process will cause many defects, dislocations and cracks in the aluminum particles, ...
اقرأ أكثر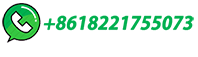
Large Batch Laboratory Ball Mill 150L to 300L
This is our largest batch ball mill. Best at dry grinding, it has a grinding chamber of either 150L or 300L (40 or 80 gallons). The 911MPELMBM-150/300 is a process and laboratory machine, which is suitable for …
اقرأ أكثر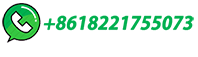
Grinding Mill Design & Ball Mill Manufacturer
All Grinding Mill & Ball Mill Manufacturers understand the object of the grinding process is a mechanical reduction in size of crushable material. Grinding can be undertaken in many ways. The most common way for high capacity industrial purposes is to use a tumbling charge of grinding media in a rotating cylinder or drum.
اقرأ أكثر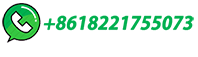
Grinding Mills
In many industries the final product, or the raw material at some stage of the manufacturing process, is in powdered form and in consequence the rapid and cheap preparation of powdered materials is a matter of considerable economic importance. In some cases the powdered material may be prepared directly; for example by …
اقرأ أكثر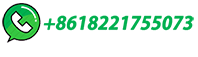
Calculate and Select Ball Mill Ball Size for Optimum Grinding
In Grinding, selecting (calculate) the correct or optimum ball size that allows for the best and optimum/ideal or target grind size to be achieved by your ball mill is an important thing for a Mineral Processing Engineer AKA Metallurgist to do. Often, the ball used in ball mills is oversize "just in case". Well, this safety factor can cost you much in …
اقرأ أكثر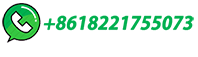
Constrained model predictive control in ball mill grinding process
Ball mill grinding is a fundamental operation process, and in many respects the most important unit operation in a mineral processing plant. Grinding process represents almost half of the total operating costs associated with the mining operation, and the product particle size greatly influences the recovery rate of the valuable minerals and ...
اقرأ أكثر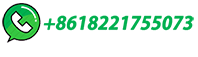
Intelligent optimal control system for ball mill grinding …
Grinding particle size (%, 74 μm) of hydrocyclone overflow and circulation load to ball mill are the two key indexes for grinding process. Grinding particle size rep-resents the …
اقرأ أكثر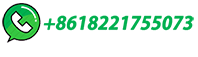
Ball Mill Design/Power Calculation
The basic parameters used in ball mill design (power calculations), rod mill or any tumbling mill sizing are; material to be ground, characteristics, Bond Work Index, bulk density, specific density, desired mill tonnage capacity DTPH, operating % solids or pulp density, feed size as F80 and maximum 'chunk size', product size as P80 and …
اقرأ أكثر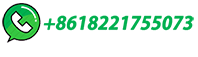