EVERY COMPONENT OF BALL MILL DETAILED & EXPLAINED
Fine Grinding and Mill Cooling. PROBLEM. Insufficient mill cooling lead to material agglomeration on balls and liners. The grinding is not any more done by balls against material but by material against material. SOLUTION. Adapted mill cooling, playing with:-Clinker temperature-Mill ventilation-Water injection
اقرأ أكثر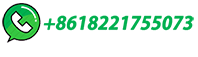
Ball mills | FL Cement
Ball mill for cement grinding. An inefficient ball mill is a major expense and could even cost you product quality. The best ball mills enable you to achieve the desired fineness quickly and efficiently, with minimum energy expenditure and low maintenance. With more than 4000 references worldwide, the FL ball mill is proven to do just that.
اقرأ أكثر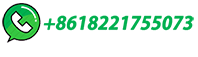
Cement ball mill
Cement ball mill. Process introduction Compared to other traditional ball mill, the cement ball mill of CHAENG can improve output by 15%20%, and the specific surface area of …
اقرأ أكثر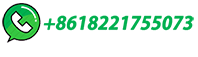
The effect of ball size on breakage rate parameter in a pilot …
To produce 1 ton of cement 110 kW h electrical energy is consumed in the conventional cement making process and about 40% of this energy is consumed to clinker grinding process by ball mills in a typical cement plant (Fujimoto, 1993). The last annual world and Turkey cement production are approximately 2.6 billion tons and 48 million …
اقرأ أكثر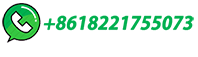
Grinding in Ball Mills: Modeling and Process …
The paper presents an overview of the current methodology and practice in modeling and control of the grinding process in industrial …
اقرأ أكثر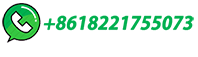
Cement Separator & Ball Mill Optimization
-Find: required maximum ball size – F80 – Maximum ball size (mm.) Mill performance test. Steps 1. Recording of related operational data 2. Air flow measurement 3. Crash stop and visual inspection in mill 4. Sampling in mill 5. Evaluation of test . 1. Recording of related operational data-Tube Mill. Feed rate, Return, Grinding aids, Water ...
اقرأ أكثر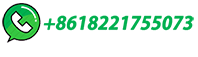
Ball Mills
In all ore dressing and milling Operations, including flotation, cyanidation, gravity concentration, and amalgamation, the Working Principle is to crush and grind, often with rod mill or ball mill, the ore in order to liberate the minerals. In the chemical and process industries, grinding is an important step in preparing raw materials for …
اقرأ أكثر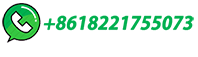
OPTIMIZATION OF CEMENT GRINDING OPERATION IN …
Operation and Elements of a Closed-Circuit Ball Mill System . Cement ball mills typically have two grinding chambers. The first chamber is filled with larger diameter grinding media andlined with lifting liners . The first chamber coarse-grinds the feed material and prepares it for the second chamber. The second chamber is the fine grinding ...
اقرأ أكثر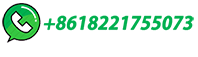
The cement mill
Cement manufacturing - brief description of a cement mill. Cement clinker is usually ground using a ball mill. This is essentially a large rotating drum containing grinding media - normally steel balls. As the drum rotates, …
اقرأ أكثر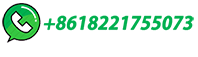
Process Training Ball Mill
Ball Charge. Ball mills for cement grinding usually operate with a filling degree between 25 and 35 %. The filling degree is defined as the volume of the grinding media (balls) as a percentage of the total mill volume. Since mill speed, liner shape and mill diameter are usually unchangeable parameters, the only adjustment in a mill can be made ...
اقرأ أكثر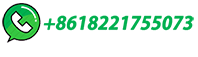
BALL MILLS Ball mill optimisation
OPTIMIZATION OF CEMENT GRINDING OPERATION IN …
WEBoptimization of cement grinding operation in ball mills Several energy efficient options for cement grinding are available today such as vertical roller mills, roller presses (typically …
اقرأ أكثر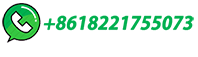
The effect of ball size on breakage rate parameter in a pilot …
The mill was crashed-stopped during various periods. Samples were representatively taken from inside the mill in distances of 20–30. cm along the center and edge lengths for selected periods which are 2, 5, 10, 15, 20, 30, 45 and 60 min.. For modelling of grinding process in pilot scale ball mill, determination of the particle size …
اقرأ أكثر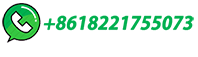
Small Ball Mill | Mini Ball Mill for Small Scale Mineral Grinding
The small ball mill is a small-capacity grinding equipment, which is defined relative to large ball mill.It is generally suitable for small-scale production in the trial production stage. Due to its small size and easy movement, small ball mill is sometimes referred to as mobile ball mill. The mobile ball mill can be easily moved to the location of the material for on-site …
اقرأ أكثر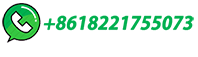
Downhole Milling Tools
enabling these mills to exit the casing with minimal wear. Round-Nose Window Mills These less aggressive window mills are used for cleaning up ledges to give an exit a smooth, even transition. Tubing Mills When sand, cement and scale plug tubing, tubing mills clean them out with a combination of jetting and milling action. They
اقرأ أكثر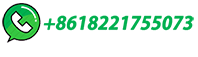
Grinding in Ball Mills: : Modeling and Process Control
15. Deniz, V. A Study on the Specific Rate of Breakage of Cement Materials in a Laboratory Ball Mill. - Cement and Concrete Research, Vol. 33, 2003, 439-445. Crossref. ... The Effect of Ball Size on Breakage Rate Parameter in a Pilot Scale Ball Mill. - Minerals Engineering, Vol. 22, 2009, 660-664. Crossref. Google Scholar [19] 19. …
اقرأ أكثر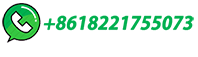
Let's talk: polysius® booster mill – the next level in cement …
Wilczek: The mill accepts a maximum particle size of about 0.5 mm for hard and up to 4mm for softer materials. One typical characteristic of the mill is the high energy density, 10-20 times higher compared to a ball mill, resulting in a very compact design. The high energy density in the small grinding chamber requires a fast material transport.
اقرأ أكثر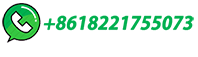
Open and closed circuit dry grinding of cement mill rejects in a pilot
The separator reject sample from a nearby cement factory (Oyak Bolu Cement Industry) was collected for the experimental part of this study. The sampling point for the clinker grinding circuit was depicted in Fig. 2.The capacity of the cement mill during the sampling time was 130 t/h and the specific energy consumption was 32 kW h/t.
اقرأ أكثر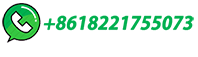
Cement Mill for Sale | Buy Cement Ball Mill & Vertical Roller Mill …
Cement mills are the milling machines used in cement plants to grind hard clinker into fine cement powders. Cement ball mill and vertical roller mill are two most widely used cement mills in today's cement grinding plants and are also the main types of cement mill we produce.. As a professional cement equipment manufacturer, AGICO has rich …
اقرأ أكثر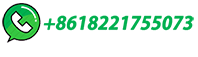
Cement grinding optimisation
Due to limitation of the mill's rotational speed, the smallest ball size is usually restricted to about 15 mm. Cement grinding using stirred mills (Pilevneli and Azizli, 1999) indicates that using smaller media (5–8 mm range) improves grinding energy efficiency up to 50% using stirred mills. For specialized types of cement, which are finer ...
اقرأ أكثر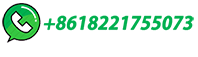
Cement Mill Optimization: Practical Strategies for Enhanced …
Adjusting mill parameters: Fine-tuning mill parameters such as mill speed, ball charge, filling ratio, and grinding media size can have a substantial impact on the grinding efficiency of the mill. For example, a 10% increase in mill speed can result in up to 10% higher production rate, while optimizing the ball charge can lead to a 5-10% ...
اقرأ أكثر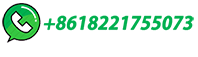
A Review of the Grinding Media in Ball Mills for Mineral …
The ball mill is a rotating cylindrical vessel with grinding media inside, which is responsible for breaking the ore particles. Grinding media play an important role in the …
اقرأ أكثر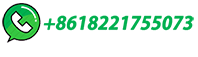
Ball mills for various applications | Gebr. Pfeiffer
Working principle. Fed into the mill through one or both bearing trunnions, the material is ground by impact and friction from the balls. The ground product is discharged from the mill through discharge slots provided in the mill tube, through a …
اقرأ أكثر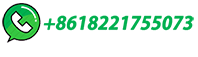
The Potential of Additives in Cement Production
For this reason, Master Builders Solutions has invested in a pilot mill. This is a 1:10 scale version of a genuine cement ball mill and it offers realistic conditions without the tremendous cost of tests at a real cement factory. Our pilot mill is located at our development center in Treviso, Italy, and is used mainly for basic research and for ...
اقرأ أكثر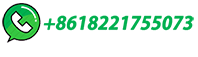
Rotary kilns for calcining and roasting
PERI™ AutoCharge Mill Grinding Ball Charging System ... FL can help with an excellent Research and Development Group and with well-equipped pilot plant facilities, including a 0.5m x 5m test kiln and a 1m x 10m test kiln. ... FL is a full flowsheet technology and service supplier to the global mining and cement industries. …
اقرأ أكثر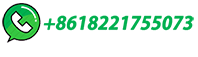
Using modelling and simulation for the design of full scale …
Production capacity of a fully air-swept industrial scale two-compartment KHD Humboldt Wedag® cement ball mill was optimized with the aid of simulation. It was …
اقرأ أكثر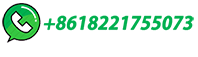
Grinding ball data
When dry grinding cement raw material, a protective coating of ground material covers the mill liners and grinding balls. It is known that cement raw material is much less abrasive than cement clinker. The wear of raw mill liners does not present an urgent financial problem, because extension of their lifetime is of insignificant influence on ...
اقرأ أكثر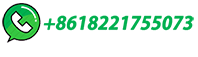
Laboratory Ball Mill, 5 Kg Capacity, 10 Kg Capacity, 20 Kg …
Apart from the cement industry, it is also used in the paint, plastic, granite and tile industries. The equipment is provided with a revolution counter for recording the revolutions. Models available: Laboratory Ball Mill 5 Kg capacity (AIM 441) Laboratory Ball Mill 10 Kg capacity (AIM 441-10) Laboratory Ball Mill 20 Kg capacity (AIM 441 -20)
اقرأ أكثر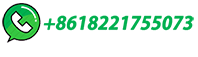
Grinding Media Wear Rate Calculation in Ball Mill
In the previous discussion the fact was established that the work done by a ball when it strikes at the end of its parabolic path is proportional to its weight and velocity; then, since the velocity may be considered as constant for all the balls in the mill, the work done by a ball is proportional to its weight. Since the amount of ore crushed varies as …
اقرأ أكثر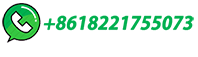
The Monarch Process
The final step is finish grinding. The Monarch finish milling system consists of five ball mills—large rotating cylinders containing steel balls. As the feed enters the mill, the balls continuously crush and grind the clinker and gypsum into a fine powder, a process known as comminution.
اقرأ أكثر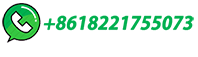