Iron processing | Definition, History, Steps, Uses, & Facts
Iron ore processing is a complex and vital process that transforms raw iron ore into usable steel. From exploration and extraction to grinding, beneficiation, and …
اقرأ أكثر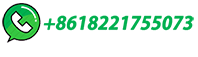
23.3: Metallurgy of Iron and Steel
For a long time, charcoal was the form of carbon used in the reduction process. The production and use of iron became much more widespread about 1620, when coke was introduced as the reducing agent. ... The furnace is charged with alternating layers of iron ore (largely Fe 2 O 3) and a mixture of coke (C) and limestone (CaCO 3). …
اقرأ أكثر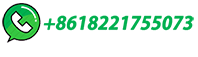
Iron Ore Flotation Process: The Journey from Ore to …
Iron ore flotation process. 1. Grinding: Crushing and grinding the raw ore to a certain particle size is a necessary preparation before iron ore flotation.The purpose of grinding is to fully ...
اقرأ أكثر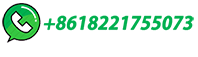
Iron Ore Processing, General
Iron ore handling, which may account for 20–50% of the total delivered cost of raw materials, covers the processes of transportation, storage, feeding, and washing of the ore en route to or during its various stages of treatment in the mill.. Since the physical state of iron ores in situ may range from friable, or even sandy materials, to monolithic …
اقرأ أكثر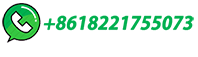
How to Manufacture Pig Iron: How Pig Iron is made?
Guide for manufacturing and making Pig Iron. Following three distinct operations are involved in the manufacturing process of pig-iron: (1) Dressing (2) Calcination and roasting (3) Smelting. (1) Dressing: The iron ores as obtained from mines are crushed into pieces of size of 25 mm diameter. This is achieved in the rock crushers of ordinary type. The …
اقرأ أكثر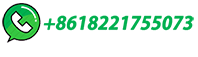
Extraction of Iron | Metallurgy | Blast Furnace and Reactions …
This kind of iron is called Cast Iron and has a slightly lower carbon content 2 – 3 %. This is even harder than pig iron. Wrought Iron/ Malleable Iron. Wrought iron is the purest form of iron available commercially available and is prepared from cast iron by heating cast iron in a furnace lined with Haematite (Fe 2 O 3). The Haematite reacts ...
اقرأ أكثر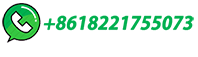
Iron processing
Iron ore sintering consists of heating a layer of fines until partial melting occurs and individual ore particles fuse together. For this purpose, a traveling-grate machine is …
اقرأ أكثر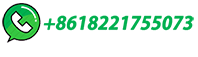
Iron Production
Iron ore is usually a mixture of iron and vast quantities of impurities such as sand and clay referred to as gangue. The iron found in iron ores are found in the form of iron oxides. ... As the process continue the molten iron flow down through the furnace and collects at the bottom, where it is removed through an opening in the side. When it ...
اقرأ أكثر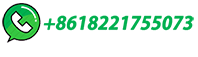
Evolution of Ironmaking Techniques | From Ancient to …
These processes involve the direct reduction of iron ore using natural gas or hydrogen, producing high-purity iron that can be used in various applications, including steelmaking. Furthermore, advancements in smelting technologies, such as the use of plasma and novel reactor designs, aim to enhance energy efficiency and reduce environmental impact.
اقرأ أكثر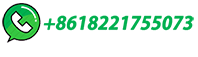
Iron Ore Processing, General
Making iron and steel from iron ore requires a long process of mining, crushing, separating, concentrating, mixing, agglomeration (sintering and pelletizing), and …
اقرأ أكثر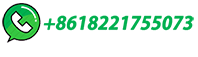
What Are Iron Ore Pellets and How to Make Them?
The iron ore beneficiation process includes three parts: 1. Reduce the mineral particle size: Use crushing, screening, and grinding processes to produce very fine iron powder. 2. Improve the iron ore grade: Use the methods of magnetic separation and flotation separation to obtain a high-quality iron ore concentrate. 3.
اقرأ أكثر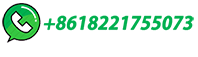
Research Progress of Intelligent Ore Blending Model
The iron and steel industry has made an important contribution to China's economic development, and sinter accounts for 70–80% of the blast furnace feed charge. However, the average grade …
اقرأ أكثر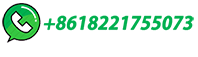
From Ore to Iron with Smelting and Direct Iron Reduction
Figure 1: Steelmaking byproducts for blast furnace (BF), basic oxygen furnace (BOF) and electric arc furnace (EAF) processes. Source: World Steel Association (worldsteel) The first step in the production of steel or cast iron alloys is the reduction of iron ore—which contains iron oxide and gangue or mineral impurities—to unrefined, …
اقرأ أكثر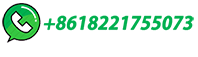
Electric Arc Furnace Process
These gasses drive off the oxygen contained in iron ore, producing metallic iron. Unlike pig iron (the product of a BF), the result of the DRI process, sponge iron, which still retains silica that must be removed in the EAF [26]. A combination of recycled scrap, sponge iron, and hot-briquetted iron (compacted form of DRI) is first loaded into ...
اقرأ أكثر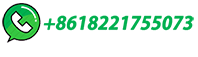
Pig Iron Manufacturing Process
In the latest report of the engineers at Trollhattan, it is stated that the power consumption per ton of pig iron varies in proportion to the iron content of the ore. A poor ore and pig iron high in silicon and …
اقرأ أكثر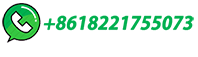
Iron Ore Smelting Process
The ore is loaded into a blast furnace along with measured quantities of coke and limestone. Hot combustion air is supplied to the furnace and some form of fuel used to raise the temperature. The iron is reduced from the …
اقرأ أكثر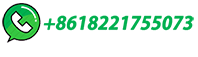
Iron Ore: The Steel Raw Materials Journey | MachineMFG
Theoretically, the highest iron content in iron ore is around 72%, and iron ore with an iron content above 60% is called rich iron ore. Iron ore is first reduced to iron (pig iron) in a furnace, then sent to a steel-making furnace for decarburization and refined into steel. Scrap steel can also be melted and regenerated in a steel-making furnace.
اقرأ أكثر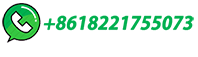
The Fundamentals Of How Cement Is Made
The crushed rock is combined with other ingredients such as iron ore or fly ash and ground, mixed, and fed to a cement kiln. ... The heated air from the coolers is returned to the kilns, a process that saves fuel and increases burning efficiency. After the clinker is cooled, cement plants grind it and mix it with small amounts of gypsum and ...
اقرأ أكثر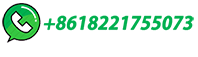
Iron processing
Iron processing - Smelting, Refining, Alloying: The primary objective of iron making is to release iron from chemical combination with oxygen, and, since the blast furnace is much the most efficient process, it receives the most attention here. Alternative methods known as direct reduction are used in over a score of countries, but less than 5 percent of iron …
اقرأ أكثر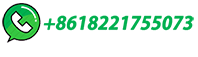
The six main steps of iron ore processing
Learn about the steps involved in iron ore processing, from crushing and grinding to separation. Contact Multotec experts for guidance on iron processing.
اقرأ أكثر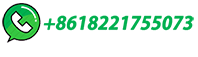
Introduction to Iron ore Pellets and Pelletizing processes
The various advantages of iron ore pellets are given below. Iron ore pellet is a kind of agglomerated fines which has better tumbling index when compared with the iron ore and it can be used as a substitute for the iron ore lumps both in the BF and for DRI production. Pellets have good reducibility since they have high porosity (25 % to 30 …
اقرأ أكثر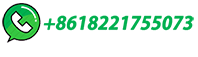
Iron processing
Several processes are based on the use of a slightly inclined rotating kiln to which ore, coal, and recycled material are charged at the upper end, with heat supplied by an oil or …
اقرأ أكثر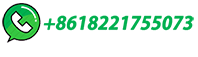
Intelligent Recommendation Framework for Iron Ore …
Optimization of sinter ore allocation is a key step in the steel production process, which has become the most important measure for steel enterprises to effectively reduce cost, improve quality, save energy and reduce emissions. In this paper, the first intelligent recommendation model for the sintering dosing scheme considering cost, …
اقرأ أكثر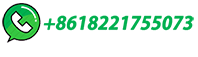
From Ore to Alloy: Navigating Ironmaking in Modern Steel …
From ore processing to alloy design, the journey of iron through blast furnaces, direct reduction plants, electric arc furnaces, and continuous casting molds shapes the steel …
اقرأ أكثر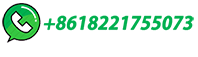
Iron ore sintering. Part 1. Theory and practice of the sintering process
Sintering is a process by which a mixture of iron ores, fl uxes and coke is agglomerated in a sinter plant to manufacture a sinter product of a suitable composition, quality and granulometry to be ...
اقرأ أكثر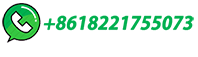
Journal of Process Control
Different kinds of iron ore have different grades of iron, S contents, and prices. The iron ore mix, coke, limestone, dolomite, and returned sinter that is combined in the second proportioning phase have different contents of Fe, SiO 2, CaO, MgO, Al 2 O 3, S, and P that directly affect the chemical components of the raw mix, as well as the …
اقرأ أكثر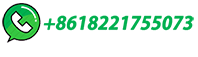
How Electric Car Batteries Are Made: From Mining To …
The process of mining the rare metals ... (like we have cheese or sauce between the main ingredients of a sandwich!). ... From mining and processing of the iron ore for the 1.5 inch thick high grade steel towers to the mining and transport and MELTING of thousands of tons of sand into the glass fibers for the gigantic blades and the tons of ...
اقرأ أكثر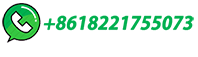
Evolution of Ironmaking Techniques | From Ancient to …
These processes involve the direct reduction of iron ore using natural gas or hydrogen, producing high-purity iron that can be used in various applications, including …
اقرأ أكثر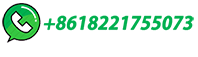
Iron Making
An ancient alchemy sustained Hopewell Furnace: transforming mineral into metal. Since 4,000 years ago, when humans learned how to free iron from ore, the basic process has not changed. Iron oxide is heated in an intense flame fed by carbon fuel. Oxygen in the ore combines with carbon monoxide released from the fuel and is …
اقرأ أكثر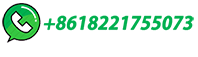
Steel
Steel - Smelting, Alloying, Refining: In principle, steelmaking is a melting, purifying, and alloying process carried out at approximately 1,600° C (2,900° F) in molten conditions. Various chemical reactions are initiated, either in sequence or simultaneously, in order to arrive at specified chemical compositions and temperatures. Indeed, many of the …
اقرأ أكثر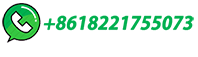