Everything You Need to Know About Wet Media …
Read on to learn more about the steps involved in wet grinding, and how the process can vary from one project to another. How does a wet grinder work? Wet milling machines can include horizontal media mills, attritor …
اقرأ أكثر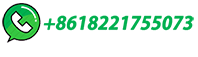
Ball Mills
Available cylinder sizes range from laboratory mills to 12′ in diameter.. Discharge Features. For discharge of the product on wet grinding processes we offer our standard media retention grate along with an …
اقرأ أكثر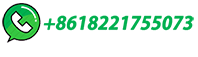
Small Ball Mill Capacity & Sizing Table
Do you need a quick estimation of a ball mill's capacity or a simple method to estimate how much can a ball mill of a given size (diameter/lenght) grind for tonnage a product P80 size? Use these 2 tables to get you close.
اقرأ أكثر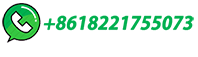
Exploring Ball Mill Diagram: A Comprehensive Guide
Explore the anatomy of a ball mill with a detailed ball mill diagram. Learn more on our blog for valuable insights into this essential industrial equipment.
اقرأ أكثر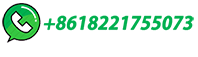
Wet Ball Milling Method and Technology
Wet milling, a core aspect of the wet grinding process, involves breaking down materials in a liquid medium. The wet ball milling process, a popular choice in many sectors, employs a ball mill to achieve a fine grind. This method is particularly effective for materials that are too hard for standard milling. Steps in Wet Ball Milling Process
اقرأ أكثر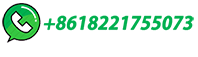
Overflow VS Grate Discharge Ball or Mill
Allow me to compare: Ball mills can be of the overflow or of the grate discharge type. Overflow discharge mills are used when a product with high specific surface is wanted, without any respect to the particle size distribution curve. Overflow discharge mills give a final product in an open circuit. Grate discharge mills are used …
اقرأ أكثر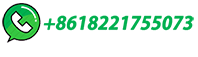
Ball Mill
The characteristic tumbling motion of these mills has given them the name 'tumbling mills', which include the ball mill, tube mill and rod mill. Ball mills are horizontal rotating cylindrical or conical steel chambers, approximately one third to half full of steel, alloy steel or iron balls, like that shown in Fig. 4.10 A–C, or flint stones.
اقرأ أكثر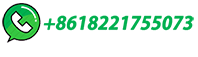
Ball Mills
Laboratory Ball Mills are used for rapid batchwise comminution of medium-hard, soft, brittle, fibrous, temperature-sensitive and moist samples down to the finest particle sizes.
اقرأ أكثر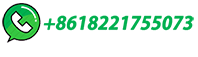
Ball Mill Design/Power Calculation
A wet grinding ball mill in closed circuit is to be fed 100 TPH of a material with a work index of 15 and a size distribution of 80% passing ¼ inch (6350 microns). …
اقرأ أكثر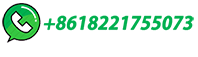
Wet Grinding Mills Mexico | Custom Milling & Consulting LLC
Greater yield with little product loss. Maximum color strength and gloss durability. As much as 300% reduction in process time. 5% reduction in raw material costs. Minimal …
اقرأ أكثر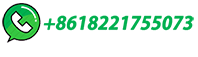
What Are the Differences between Dry and Wet Type Ball Mill?
The wet ball mill has a simple transportation device with less auxiliary equipment, so the investment is about 5%-10% lower than that of a dry ball mill. The grinding particle size is fine and uniform. The wet ball milling can not only grind agglomerate into fine particles, but also mix the lean material and the plastic material …
اقرأ أكثر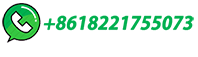
Rod Mill Design & Power Draw
For rod, ball, or pebble mills the peak is usually near Vp = .50, while actual observations as low as V= .42 have bean made in some ball mills (Rowland, 1973). See Figure 2. Power draw is not significantly affected by the presence of the slurry in the mill.
اقرأ أكثر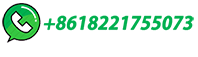
Grinding in Ball Mills: Modeling and Process Control
Besides particle size reduction, ball mills are also widely used for mixing, blending and dispersing, amorphisation of materials and mechanical alloying [1, 49, 51].
اقرأ أكثر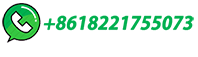
Ball Mill Parameter Selection – Power, Rotate Speed, Steel Ball
V — Effective volume of ball mill, m3; G2 — Material less than 0.074mm in product accounts for the percentage of total material, %; G1 — Material less than 0.074mm in ore feeding accounts for 0.074mm in the percentage of the total material, %; q'm — Unit productivity calculated according to the new generation grade (0.074mm), t/(m3.h). The …
اقرأ أكثر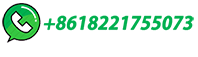
How to Size & Design a Regrind Ball Mill
Therefore, use one 3.05 meter (10.0 foot) diameter inside shell 2.89 meter (9.5 foot) diameter inside new liners by 5.79 meter …
اقرأ أكثر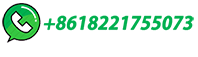
Planetary Ball Mills | Ultra Fine Grinding
Planetary Ball Mills are among the most variable and effective tools when it comes to size reduction of hard, brittle or fibrous materials. From benchtop size to pilot production size, from full-direction grinding to cryogenic grinding, our extensive portfolio virtually guarantees there is an appropriate standard solution that will meet your requirements.
اقرأ أكثر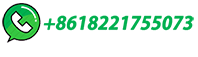
SAG milling & grinding pilot plants
Ball mills: Ball mills are the stalwart unit of the majority of pilot grinding circuits. ALS has a range of rubber lined overflow ball mills including: 2.3kW, 4.4 kW high aspect (900 mm Dia x 400 mm EGL), 3 x units of 5.5 kW and 7.5 kW (900 mm Dia x 790 mm), 1 x 15 kW 900 mm Dia x 1800 mm EGL, 1 x 30 kW 1240 mm Dia x 1440 mm EGL).
اقرأ أكثر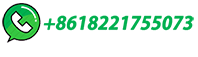
Unlocking Precision: A Guide to Choosing the Right Standard End Mill
Leveraging the end mill size chart for tool inventory management. In a machining setting, efficient tool inventory management is important to reduce downtime and increase productivity. One way of doing this is by using an end mill size chart, which helps operators to know the different available sizes of tools and their uses.
اقرأ أكثر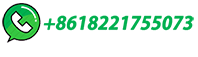
Comprehensive Guide to End Mill Sizes for CNC Machines
6G Tools: Provides a chart of standard end mill sizes, which includes ball end mill sizes. Eternal Tools: This guide discusses the use of end mills in CNC routers and mini-milling machines, which are now widely available in table-top sizes. Recommended Reading: Exploring the World of Carbide End Mills
اقرأ أكثر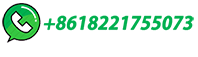
End Mill Sizes
End Mill Sizes Size Decimal Category Size Decimal Category Size Decimal Category Size Decimal Category 0.0050 0.0050 Micro 0.0520 0.0520 Micro 0.0980 0.0980 Micro 7/16" 0.4375 Inch 0.0060 0.0060 Micro 0.0530 0.0530 Micro 2.5mm 0.0984 Metric 29/64" 0.4531 Inch 0.0070 0.0070 Micro 0.0540 0.0540 Micro 0.0990 0.0990 Micro 15/32" 0.4688 Inch
اقرأ أكثر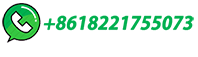
Ball Mill Application and Design
Ball mills cab be used equally well for wet or dry grinding. In the case of wet grinding the particles are also dispersed in the liquid medium. ... Ball mills scale up well and in fact improve in performed with increasing size. Ball mills are available in sizes from laboratory scale (also called milling jars) of 0.1 usg to large 5,000 gallon mills.
اقرأ أكثر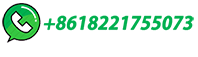
Why use Different Size Balls in a Mill
Having selected the best ball size, it will be seen by referring to tables 27 and 28 that the preferable ball size usually gave the best capacity and efficiency. Also, the preferable ball size coincides closely with the best selective grinding, the main exception being the "plus 10-mesh" series in table 28.
اقرأ أكثر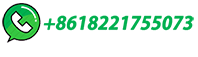
Dry Grinding Vs. Wet Ball Mill Grinding | Economy Ball Mill
At Economy Ball Mill, we're a leading manufacturer of custom-made ball mills for various industries. We have many years of experience in designing and producing high-quality ball mills that can meet your specific requirements. We can provide both dry ball mills and wet ball mills, and can complete attritor mill barrel rebuilds.
اقرأ أكثر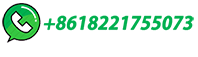
Wet Continuous Production Mills
How Continuous Attritors Work The continuous Attritor is a compact vertical design suitable for continuous production of large quantities of materials. Advantages of using a continuous Attritor include continuous large …
اقرأ أكثر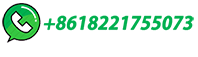
MODULE #5: FUNCTIONAL PERFOMANCE OF BALL …
particle size as the target grind size for the ball mill circuit; for ex-ample, it is convenient to select the desired 80% passing size as the target grind size. You can then use this target grind size to define and distinguish between "coarse" and "fine" particles in any of the
اقرأ أكثر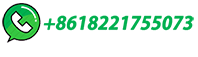
Grinding Mills | Mineral Processing Equipment | CITIC HIC
3. The maximum ball loading capacity of AG mill is calculated at 3% of effective mill volume, while the SAG mill with ball loading capacity at 15% of mill volume. 4. The operating speed is usually 75% of critical speed of mill, the variable frequency speed regulation is ideally somewhere between 5% to 10% of rated speed.
اقرأ أكثر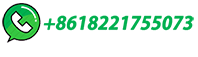
Ball Mills
Center peripheral discharge Rod Mill for minimal slimes in final product. CERAMIC LINED BALL MILL. Ball Mills can be supplied with either ceramic or rubber linings for wet or dry grinding, for continuous or batch …
اقرأ أكثر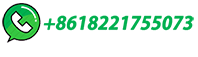
Ball size distribution for the maximum production of a …
In this research, ball wear model was combined with the grinding model to optimise the milling stage of an industrial ball mill. Fig. 2 presents the flow sheet of the milling circuit but an open circuit determined by the region between point A and B, which represents the industrial ball mill, was considered for this research. The industrial mill is …
اقرأ أكثر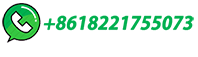
Solved The feed size to a single stage wet ball mill was 9.5
The ball mill grindability test at 65 mesh showed 12 kWh / t. The internal diameter of the ball mill was 5.03 m and the length to diameter ratio 0.77 . The steel balls occupied 18% of the mill. The total load occupied 45% of the mill volume. If the mill operated at 72% of the critical speed, determine the mill capacity (t/h).
اقرأ أكثر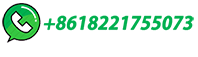
Technical specifications and selection guide for ball mills
Ball mills are available in various sizes and capacities, and their technical specifications can vary depending on the manufacturer and model. Some of the key technical specifications include: - Diameter and Length: Ball mills are typically available in …
اقرأ أكثر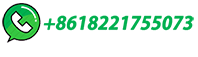