Everything you need to know about clinker/cement Grinding
EVERYTHING YOU NEED TO KNOW ABOUT …
WEBClinker Grinding Mill. The clinker, gypsum, and additive will next be fed into the grinding mill, to produce the desired type of …
اقرأ أكثر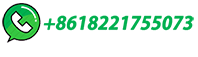
Modular Grinding Plant | AGICO Cement Machinery
Clinker and other additives for grinding are fed by fork-lift truck to respective feeding bins. The feeding bins are installed in standardized containers. ... Grinding Mill Module. ... The function of the packaging module is to pack bulk cement into bags for …
اقرأ أكثر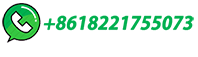
CEMENT CLINKER GRINDING: EVALUATION OF MILL SPIN …
The surface area increased mainly as a function of increases in mill spin speed, while residence time and grinding media load had lesser impacts. Keywords : clinker; cement; grinding; ball mill; grinding media.
اقرأ أكثر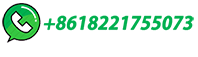
(PDF) A study of different grinding aids for low-energy cement clinker
In this study we compare the effects of three different grinding aids on clinker grinding using a ball mill. A commercial grinding additive, triethanolamine (TEA), and two industrial grinding aids ...
اقرأ أكثر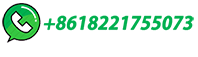
CLINKER GRINDING UNIT PROCESS
Clinker and gypsum, being mixed together in predetermined proportions, are fed to the grinding mills. Chemical gypsum, if used instead of natural gypsum, needs to be dried either by natural sun drying or by mechanical drying, before it is used with cooled and dried clinker for inter - grinding in mills.
اقرأ أكثر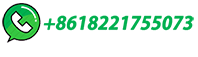
Better and cheaper cement: Optimising the right clinker …
Dusty clinker can also have poor grindability and a higher kWh/t demand and can cause severe vibration and quality problems when vertical roller mills are used to grind clinker. Keeping clinker dust levels as low as possible (Figure 3) has many benefits to cooler, kiln and downstream plant performance.
اقرأ أكثر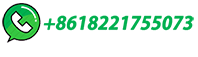
The Evolution of Clinker Vertical Roller Mills: From Inception …
During the 1980s, the technology of vertical roller mills for clinker grinding saw several improvements. Manufacturers like Loesche, FL, and Polysius began to refine the design and operation ...
اقرأ أكثر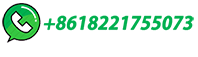
id/17/clinker grinding and packing mill.md at main
Host and manage packages Security. Find and fix vulnerabilities
اقرأ أكثر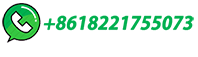
CONVENTIONAL CLINKER GRINDING
of the clinker fine-grinding in ball mills. This model enables the prediction of the ... Conveying, packing, loading, 5.1% Clinker burning and cooling, 24.6% Raw meal homogenisation, 1.6% Strip ...
اقرأ أكثر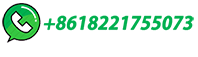
What is Clinker? The Relationship Between Clinker Phases and Grinding …
Clinker is the primary material of cement, and it is called as semi-finished product. Clinker is a granulated material made of raw meal powder obtained by grinding limestone and clay together by sintering the raw meal in a rotary furnace at 1400°C-1500°C degrees. Produced clinker's mineralogical structure effects clinker's grinding energy.
اقرأ أكثر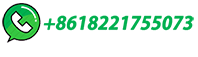
China Cement Grinding Station-Price Preference and …
Machines needed in cement grinding plant are cement mill, cement classifier, cement packing machine, dust collector, bucket elevator, etc. Cement mill The ball mills are still the most widely used cement mills. Clinker and 3–5% gypsum together with other additives, if necessary, are ground to extreme fineness in the it.
اقرأ أكثر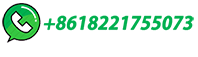
Roll Equipment and Roller Press for Cement Clinker Grinding and Packing
Roll Equipment and Roller Press for Cement Clinker Grinding and Packing Unit Plant, Find Details and Price about Cement Roller Mill Roller Mill from Roll Equipment and Roller Press for Cement Clinker Grinding and Packing Unit Plant - …
اقرأ أكثر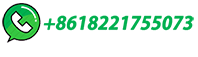
Clinker size and cement grinding | GCP Applied Technologies
Clinker size and cement grinding. Clinker size is important for the optimization of cement grinding, and is also an indicator of cement quality. ... Coarse clinker is more of an issue for ball mills. Some cement groups use a formula, such as Bond's, to calculate the maximum ball size required in a ball mill, based on the average …
اقرأ أكثر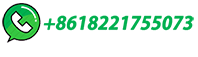
Clinker Grinding Unit
The whole system of cement grinding station mainly includes cement grinding, cement homogenization and batching, cement packaging and bulk loading. And the system is composed of cement mill, OSEPA high …
اقرأ أكثر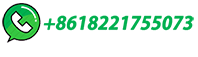
Cracking the Code: The Mystery Behind Why Clinker is Hard to Grind
Moreover, utilizing specialized grinding techniques, such as pre-grinding or inter-grinding additives, can further enhance the grindability of clinker. Pre-grinding involves crushing the clinker before it enters the mill, while inter-grinding additives are blended with the clinker during the grinding process to reduce particle agglomeration …
اقرأ أكثر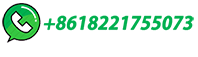
Modular Grinding Plant | AGICO Cement Machinery
Clinker and other additives for grinding are fed by fork-lift truck to respective feeding bins. The feeding bins are installed in standardized containers. ... Grinding Mill Module. ... The function of the packaging …
اقرأ أكثر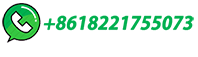
Cement clinker grinding: Evaluation of mill spin speed, …
In this study, the milling of clinker was evaluated by varying the mill speed (24 and 72 RPM), residence time (3 and 5 hours) and grinding media load (30 and 40 %) in a ball mill.
اقرأ أكثر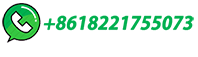
Cement Clinker Grinding Mill
Cement Clinker Grinding Mill. The cement clinker uses limestone, clay, and iron as the main raw materials, and is prepared into a raw material at an appropriate ratio, and is partially or completely melted and cooled to …
اقرأ أكثر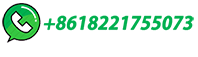
cement grinding Unit
High grinding efficiency. For the structure, of the cement mill, we adopt the advanced obstructing equipment for internal powder, add the activated device to the fine grinding chamber, and there is the special grate plate at the end of the cement mill, which can reduce the size of the grinding medium, greatly improve the grinding efficiency, and …
اقرأ أكثر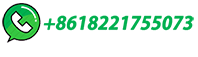
All Stages of Cement Manufacturing from The Cement …
Clinker, after being cooled, is moving to these circulating drums & ground into such a powder that each pound has 150 billion grains. This powder is known as the final item of this process cement. Packing and Shipping; Cement is transferred from grinding mills to silos (big storage tanks), which pack 20 to 40 kg bags.
اقرأ أكثر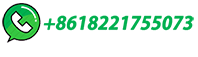
CEMENT MANUFACTURING PROCESS
Clinker grinding and cement manufacturing The clinker is mixed with gypsum and other additions within a cement mill. Cement storage The cement is stored in silos, separated according to its classes. Packaging or bulk shipment. The cement is bagged or unloaded in a tanker truck for transport by road or rail. ProTIR | Burning zone
اقرأ أكثر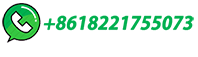
Cement Production Process | Cement Manufacturing Process …
Clinker storage capacity can be based on the market, and a cement plant usually stores 5-25% of the annual clinker production. Cement grinding: The clinker is taken from the clinker silo and sent to the feed bin where it is mixed with gypsum and additives before entering the cement grinding plant. In the cement grinding process, …
اقرأ أكثر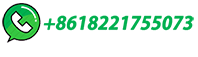
Clinker Grinding Techniques in Cement Manufacturing
Clinker grinding is a vital and integral process in cement production, playing a crucial role in transforming clinker into the final cement product. Here's an exploration …
اقرأ أكثر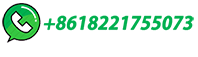
Cement
The clinker and the required amount of gypsum are ground to a fine powder in horizontal mills similar to those used for grinding the raw materials. The material may pass straight through the mill (open-circuit grinding), or coarser material may be separated from the ground product and returned to the mill for further grinding (closed-circuit ...
اقرأ أكثر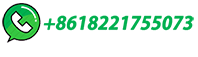
White Cement Manufacturing
White Cement Plant. The production process of white Portland cement is quite different from ordinary Portland cement. It is unique in both process flow and cement equipment selection. In white cement plants, the main manufacturing process includes six steps: raw material crushing, raw material grinding, clinker calcination, clinker cooling, cement …
اقرأ أكثر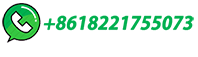
The effects of grinding media shapes on the grinding kinetics …
The effects of balls and cylinders on the clinker's specific rate of breakage were investigated. The results showed that the specific rate of breakage provided by cylinders is higher than that of balls. − 2.00 + 1.70 mm is an optimum feed size for 20 mm diameter balls and 20 × 20 mm diameter cylinders.At that feed size, the value of Si is …
اقرأ أكثر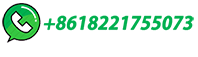
Overview of cement clinker grinding
The object of the roller press installation was to add sufficient grinding capacity to the Nazareth I finish mill system to warrant the building of an on-site packing facility, which would then ...
اقرأ أكثر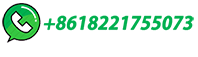
Review on vertical roller mill in cement industry & its …
A two-compartment ball mill with a highly efficient separator is still procured for new cement grinding units installation, although the vertical roller mill has now …
اقرأ أكثر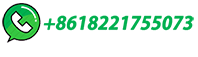
(PDF) Clinker grinding process and cement …
Grinding Aids reduce particle re-agglomeration during and after the milling process so improving the yield. Strength enhancers push clinker reactivity increasing the use of SCM in blended...
اقرأ أكثر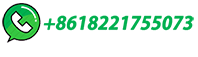
Experimental study of clinker grinding in a ball mill and …
which is the most used unit operation in clinker grinding, the majority component of the cement. Amongst the variables that aect the dynamics of the solids in the mills and, consequently, the nal granulometric distribution of the material to be milled, are the rotation speed, the grinding media and clinker lling degree.
اقرأ أكثر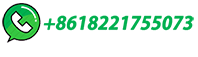