Hammer Mill Parts | Wear Parts For Industry | Qiming Casting
It is primarily used to crush materials with a maximum particle size of 600-1800 mm down to 25 mm or less. Hammer mills are suitable for medium-hard and fine crushing of materials such as limestone, slag, coke, coal, and other industrial sectors, including cement, chemical industry, electric power, and metallurgy. Hammer Mill Parts.
اقرأ أكثر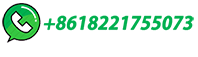
Cement grinding optimisation
The current world consumption of cement is about 1.5 billion tonnes per annum and it is increasing at about 1% per annum. The electrical energy consumed in cement production is approximately 110. kWh/tonne, and around 40% of this energy is consumed for clinker grinding.. There is potential to optimise conventional cement …
اقرأ أكثر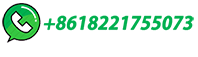
OPTIMIZATION OF CEMENT GRINDING OPERATION IN …
Optimization of the Cement Ball Mill Operation . Optimization addresses the grinding process, maintenance and product quality. The objective is to achieve a more efficient operation and increase the production rate as well as improve the run factor. Consistent quality and maximum output with lower specific power consumption
اقرأ أكثر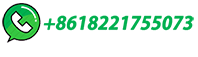
Volume 3, Issue 5, November 2013 Study of Processing …
A raw mill is the equipment used to grind raw materials into "raw mix" during the manufacture of cement. Dry raw mills are the normal technology installed today, allowing minimization of energy consumption and CO2 emissions. Process of raw mill in grinding of raw material and silo storage 1. Transporting crushed raw material to raw mill
اقرأ أكثر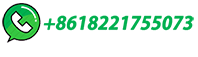
Optimizing hammer mill performance through screen …
This paper discusses mechanical preprocessing studies undertaken with the objectives to demonstrate improved efficiency and capacity in size reduction via optimization of …
اقرأ أكثر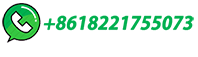
History & Growth of Cement industry in India
Cement industry is very vast and higher revenue is being paid by this sector to government of Rajasthan.1 Last decade cement industry has a compound growth of 8% with increase in housing sector. In recent years the growth is not so good as compared to earlier decade, because of slow economical growth. ...
اقرأ أكثر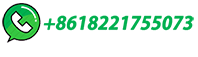
Hammer mill (system solutions) | Bruks Siwertell
Our hammer mills can be arranged as individual units, but for large-scale wood-processing requirements they can be delivered as a system solution; configured in groups to deliver outstanding performance. Multiple mills …
اقرأ أكثر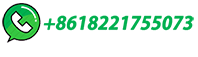
Solutions for Wear Protection in the Cement Industry
in the Cement Industry Raw material Raw meal separator Dust removal filter Preheater Fuel preparation Tertiary air duct Rotary kiln Raw meal silos Clinker cooler Clinker silos ... Cement mill Vertical mill, ball mill KALMETALL, KALCAST Cement separator Separators, cyclones ABRESIST, KALCRET,
اقرأ أكثر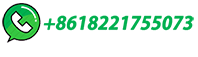
Industrial Hammer Mill Grinders
The ideal grinder necessary is determined by feed size, feed rate, operating conditions and desired product output for processing. Stedman offers two types of industrial hammer mill grinders, aka Animal Feed Hammer …
اقرأ أكثر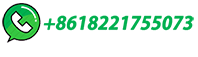
Implementation of Lean Manufacturing in a Cement Industry …
The cement production process passes through numerous workstations, including crushing raw materials, grinding raw materials, burning the materials in a rotary kiln, grinding cement in the mills ...
اقرأ أكثر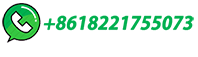
Bangladesh Cement Industry Review
USD 3 billion cement industry managed to post a mere 6% YoY growth in demand compared to an imposing 15.49% growth in 2018. Cement ... •Meghna Cement Mills Ltd is expected to have doubled its production capacity of Mongla plant to 2 MMT per annum in the mid-2019. The company signed a contract
اقرأ أكثر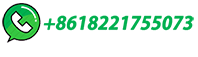
Clinker Grinding Techniques in Cement Manufacturing
Tube Mills: Tube mills are similar to ball mills but have a longer horizontal cylinder for grinding clinker. They are used less frequently than other grinding equipment in the cement industry. Air-Swept Mills: Air-swept mills use air to transport the clinker and grind it within a closed circuit. These mills are energy-efficient and can produce ...
اقرأ أكثر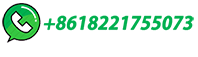
Hammermill Crushers
Hammermill Crushers are known to generate material finer than 3/16" (4mm), which in some applications may be undesirable. However, if there is a market for finer material, or if it is acceptable within the desired product size, Hammermills can achieve reduction ratios that may otherwise require multiple crushers.
اقرأ أكثر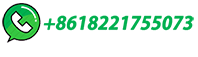
Modeling of energy consumption factors for an …
ity in the cement industry. e population balance model for simulation of a VRM in a cement clinker grinding circuit was investigated by Fatahi and Barani 11 . ˚ey reported that the clinker ...
اقرأ أكثر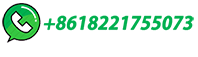
Improvement on the Design,Construction and Testing of …
Hammer mill (cereal miller) is a device consisting of a rotating head with a free swinging hammer or beater which reduce grains or similar hard dry objects to a predetermine …
اقرأ أكثر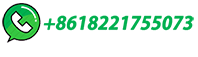
Crushers / Lumpbreakers for Cement & Concrete
Schutte Hammermill excels in providing tailored solutions for cement processing, offering specialized equipment designed to optimize efficiency and productivity in the cement industry. Our hammer mills are integral in the size reduction process, playing a key role in pulverizing raw materials to achieve the desired particle sizes for cement ...
اقرأ أكثر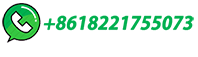
(PDF) Cleaner production assessment in cement plant …
Finally, the clinker is taken out of kiln bottom. Cement Mill and Finishing Thus the clinker formed in Vertical Shaft Kiln will be fed into the cement mill hopper by means bucket elevator where 2% Gypsum will be added and fed to the ball mill for grinding operation. Gypsum helps in initial setting of cement.
اقرأ أكثر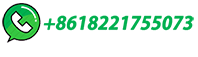
BALL MILLS Ball mill optimisation
Ball mill optimisation As grinding accounts for a sizeable share in a cement plant's power consumption, optimisation of grinding equipment such as ball mills can provide significant cost and CO 2 emission benefits to the cement producer. n by Thomas Holzinger, Holzinger Consulting, Switzerland BALL MILLS 1 FEBRUARY 2021 INTERNATIONAL …
اقرأ أكثر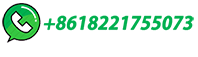
Vertical Roller Mill Operation in Cement Plant
The vertical roller mill (VRM) is a type of grinding machine for raw material processing and cement grinding in the cement manufacturing process.In recent years, the VRM cement mill has been equipped in more and more cement plants around the world because of its features like high energy efficiency, low pollutant generation, small floor area, etc.. The …
اقرأ أكثر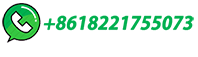
Hammermills
The first product Prater (formerly Prater Pulverizer) developed was a hammer mill, also known as hammer forges or hammer works. Since that time, our company has sold thousands of hammer mills to customers in various industries. For over 90 years, we have relied on advanced technology to properly engineer our mills for new applications.
اقرأ أكثر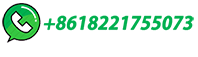
Hammer Crushers
HAZEMAG offers a double rotor Hammer Crusher and is used as primary crusher in cement industry for soft to medium-hard rock. They offer a very high crushing ration of 10:1 up to 80:1. ... The product is ideal as feed material to downstream ball mills or vertical roller mills. Double rotor Hammer Crushers are able to process materials with a ...
اقرأ أكثر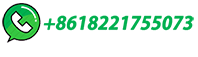
Cement
Cement is produced by a high-temperature (about 1500 °C) reaction in a rotary kiln of carefully proportioned and blended ratios of lime (CaO), silica (SiO 2), alumina (Al 2 O 3), and iron oxide (Fe 2 O 3).The production of cement is a chemical process requiring an accurate blend of the previously cited four key organic oxides and the …
اقرأ أكثر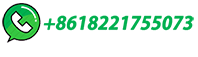
(PDF) Possibilities of implementing bimetallic hammer castings in
Liquid-liquid configuration bi-metal casting is a process that uses two separate gating systems to fill the mold cavity in two stages. The patented method (Zic et al., [94]) allows for risk-free ...
اقرأ أكثر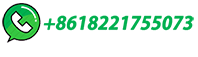
PFEIFFER MILLS FOR THE CEMENT INDUSTRY
Basing on our decade-long experience and best consulting competence, we can plan the ideal grinding plant for every customer in the cement industry, ensuring economical …
اقرأ أكثر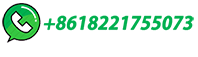
Indian Cement Sector
Cement Mill - Vertical Roller Mill: 27.07: Cement Mill - Ball Mill Closed Circuit: 23.20: Cement Mill - Ball Mill with HPRG: 0.65: Packing Plant: 0.67: Compressor upto clinkerisation: 0.89: Compressor Cement Griding and Packing
اقرأ أكثر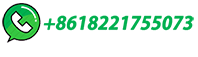
PROCESS CONTROL FOR CEMENT GRINDING IN …
the capacity of grinding and drying of mill. The grindability affects the capacity of grinding, type of mill and roller pressure. The capacity of the mill is calculated Using G K * D 2.51 Where, G is capacity of the mill, K1 is roller mill coefficient and D is table diameter. 2. PROCESS CONTROL OF VRM The conventional control system of VRM
اقرأ أكثر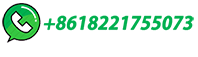
Back to Basics Hammer Milling and Jet Milling …
A hammer mill is typically good for grinding softer materials with Mohs hard-ness ranging from 1 to 5, while a jet mill can grind materials with Mohs hardness as high as 10. High hardness materi-als become very abrasive; therefore, they are not suitable for high-speed hammer mills. In a typical jet mill, grinding
اقرأ أكثر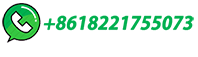
Grinding
Milling and crushing operations pose a number of headaches to cement plant operations. They consume large amounts of electrical energy. They are subject to severe abrasion. And their performance effects things well beyond the grinding plant, impacting the efficiency of the entire process, not to mention final product quality. A poorly designed or functioning …
اقرأ أكثر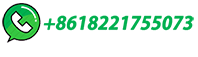
Back to Basics Hammer Milling and Jet Milling …
This article gives a detailed description of hammer mill and jet mill operation, and describes how to characterize the feed material and control product particle size.
اقرأ أكثر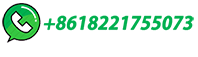
Construction, Working and Maintenance of
In a non-reversible hammer mill with screen bars, shown in above figure, material is broken first by impact between hammers and breaker plates and then by a scrubbing action (shear and attrition) of material against screen bars. Attrition crushing is most useful in the following two circumstances. When material is friable or not too abrasive.
اقرأ أكثر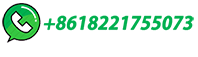