Ball Mills in the Mineral Processing Industry
The General Function of Ball Mills. A ball mill is a grinder used for grinding and blending materials for mineral dressing processes, paints, pyrotechnics, ceramics, and selective laser sintering. Appearance. Ball mills have various designs and functions, ranging from laboratory-scale versions to large industrial models.
اقرأ أكثر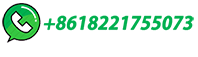
How to Improve Ball Mill Performance
The energy specific grinding rate of the coarse material in the ball mill can then be defined as follows: The mill specific grinding rate reflects both the efficiency of the mill environment in breaking the …
اقرأ أكثر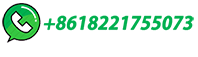
Planetary Ball Mills | Ultra Fine Grinding
Planetary Ball Mills are among the most variable and effective tools when it comes to size reduction of hard, brittle or fibrous materials. From benchtop size to pilot production size, from full-direction grinding to cryogenic grinding, our extensive portfolio virtually guarantees there is an appropriate standard solution that will meet your requirements.
اقرأ أكثر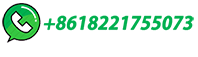
Calculate and Select Ball Mill Ball Size for Optimum Grinding
In Grinding, selecting (calculate) the correct or optimum ball size that allows for the best and optimum/ideal or target grind size to be achieved by your ball mill is an …
اقرأ أكثر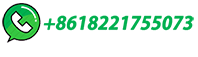
Ball Mills
The capacity, or throughput, of a ball mill is directly linked to particle size of the ball mill discharge. For example, it takes approximately 3 times as long to achieve 200 mesh grind as it does to achieve 65 mesh grind. Establishing a commercial liberation size is critical when designing and engineering your grinding circuit.
اقرأ أكثر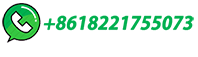
Milling tests with the FRITSCH Planetary Ball Mills
Is it possible or not to grind the fertilizer samples and reach nano size particles less than (<) 100 nm? Yes, it's possible, but this is challenging due the following: Several steps of millingprocesses are needed with various size of grinding balls (20 mm to 0.1 mm), it
اقرأ أكثر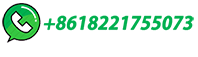
Ball-milling – Nanoscience and Nanotechnology I
Ball milling is an economic and facile technique to produce nanosized materials. It is a top-down approach of nanoparticle synthesis which includes mechanical breakdown of large …
اقرأ أكثر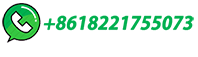
Ball Mills vs Rod Mills
The voids (or interstitial space) within a rod load are approximately half those in a ball mill grinding load. Rods in place weigh approximately 400 pounds per cu. ft. and balls in place approximately 300 pounds per cu. ft.. Thus, quantitatively, less material can progress through the voids in the rod mill grinding media than in the ball mill ...
اقرأ أكثر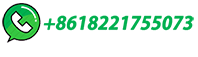
Temperature Reduction for Ball Mill Optimization | Lechler US
While often simple in design, ball mills remain one of the most common and most useful methods of finely grinding and/or blending materials. Used for paint pigments, pyrotechnics, ceramics, mineral dressing processes, and more, ball mills help us create many of the products we rely on every single day.
اقرأ أكثر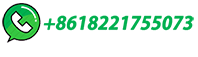
Ball milling: a green technology for the preparation and
The ball mill Ball milling is a mechanical technique widely used to grind powders into fine particles and blend materials. 18 Being an environmentally-friendly, cost-effective technique, it has found wide application in industry all over the world. Since this mini-review mainly focuses on the conditions applied for the preparation and ...
اقرأ أكثر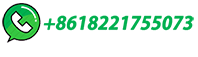
Used Ball Mills (mineral processing) for sale in USA
allis chalmers svedala ball mill, year 1979 rebuilt 1998. used. manufacturer: allis-chalmers; reference number: tt-1812 allis chalmers svedala ball mill, year 1979 rebuilt 1998 allis chalmers svedala ball mill 13' diameter x 21' long rubber-lined mill with siemens-allis 2,000 hp 4000 volt 200 rpm s...
اقرأ أكثر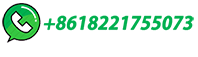
Small Ball Mill Capacity & Sizing Table
Do you need a quick estimation of a ball mill's capacity or a simple method to estimate how much can a ball mill of a given size (diameter/lenght) grind for tonnage a product P80 size? ... Calculate …
اقرأ أكثر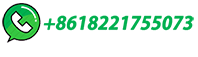
Principles of Grinding in Ball Mills
Find out more about the principles of grinding in ball mills from Orbis Machinery, LLC. Call us today for more information 262-522-1939.
اقرأ أكثر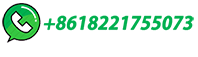
Factors Affect The Output and Quality of Ball Mills And How …
The safety factor is low, the service life is short, etc., and these will inevitably affect the continuous production of the ball mill. Therefore, the overall performance of the ball mill is better. 3. The ball mill is of good quality. The better the quality of the ball mill, the more stable the performance of the ball mill will be during ...
اقرأ أكثر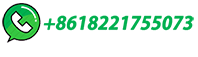
Grinding in Ball Mills: Modeling and Process Control
Ball mills can grind a wide range of materials, including metals, ceramics, and polymers, and can operate on a variety of scales, from laboratory to industrial (Monov et al. 2013). The produced ...
اقرأ أكثر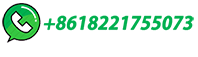
Ball mills and ceramic grinding balls // Umicore Ceramics
However, grinding balls are perfectly suited to the attrition of materials and powders. This is called a ball mill or grinding machine: the balls and the product to be ground are placed in a container, which is set in motion, in rotation. The attrition is then achieved by a mechanical grinding mechanism due to the friction of the balls on the ...
اقرأ أكثر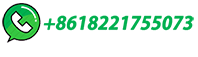
Ball-milling – Nanoscience and Nanotechnology I
The powder is reduced to nanosize using ball mill. A magnet is positioned outside the chamber to apply pulling force on the material. ... glass ceramic, ore dressing of ferrous as well as non-ferrous metals, etc. Ball mill can be used to grind ores and other materials which can be both wet and dry. On the basis of removal of end products, ball ...
اقرأ أكثر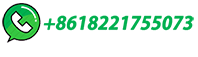
Technical specifications and selection guide for ball mills
- Motor Power: The motor power of a ball mill is an important factor in determining its grinding capacity. Ball mills can be equipped with motors ranging from 10 kW to 500 kW or more, depending on the size and desired output of the mill. - Speed: Ball mills are usually operated at speeds between 60% and 70% of the critical speed.
اقرأ أكثر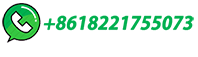
Calculate Ball Mill Grinding Capacity
Calculate Ball Mill Grinding Capacity. The sizing of ball mills and ball milling circuits from laboratory grinding tests is largely a question of applying empirical …
اقرأ أكثر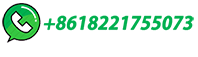
Exploring Ball Mill Diagram: A Comprehensive Guide
The grinding action in a ball mill is achieved through two primary fragmentation mechanisms: attrition and the impact. Impaction happens when the grinding media (balls or hard pebbles) bump into each other and with the material being ground. ... Ball mills can be as small as lab-scale mills or as large as industrial mills with a …
اقرأ أكثر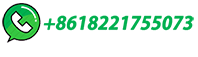
Mini Planetary Ball Mill XQM-0.4A
Is a necessary device of high-tech materials mixing, fine grinding, sample making, new product development and small batch production. Tencan planetary ball mill owns small volume, high efficiency, low noise and functional features which is a ideal equipment for R&D institution, university, enterprises laboratory to get samples (you can get four …
اقرأ أكثر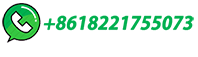
Planetary Ball Mills
This means that during one rotation of the sun wheel, the grinding jar rotates twice in the opposite direction. This speed ratio is very common for Planetary Ball Mills in general. Planetary ball mills with higher energy input and a speed ratio of 1:-2.5 or even 1:-3 are mainly used for mechanochemical applications.
اقرأ أكثر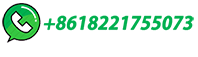
Difference Between Sag Mill vs Ball Mill
Sharing is Caring :)- Today we will learn about difference between sag mill vs ball mill. A mill is a machine by which solid or hard materials are broken into smaller pieces by means of grinding, crushing or cutting. This commutation is an essential part of many processes. Various kinds of mills are there with … Difference Between Sag Mill vs Ball Mill Read …
اقرأ أكثر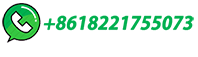
BALL MILLS FROM NANO GRINDING TO …
BALL MILLS FROM NANO GRINDING TO MECHANOCHEMICAL SYNTHESIS. December 2019. Authors: Tanja Hanke. Retsch . Figures (5) …
اقرأ أكثر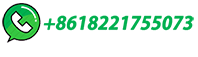
Ultrafine Grinding with Laboratory Ball Mills
With the planetary ball mills and the new high energy ball mill Emax, RETSCH offers two types of ball mills which provide the required energy input for colloidal grinding down …
اقرأ أكثر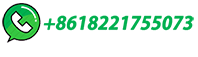
Industrial Ball Mill Grinders
Ball mill drums offer an efficient and inexpensive way to grind materials down to a more usable size, often as fine as 25-75 microns. Both continuous and batch style ball mills use centrifugal force, gravity and hard media to break up industrial materials into fine pieces or powder. Ball milling systems grind dry material and wet slurry alike.
اقرأ أكثر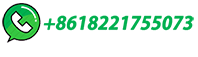
Grinding to nano-sizes: Effect of media size and slurry viscosity
Ball wet/dry media and jet mills are often used to reduce large particles to nanosize range 1-100 nm (Cho et al. 2009). Wet or dry milling methods would be used to make nanoparticles, and each ...
اقرأ أكثر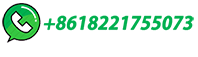
Understanding the mechanism: How does a ball mill work?
Components of a Ball Mill. 1. Drum: The drum is the main component of the ball mill, which houses the grinding media and the material to be milled. It is typically made of steel and is rotated at a specific speed to achieve the desired milling outcome. 2. Grinding Media: Grinding media are small metal balls that serve as the primary milling agents.
اقرأ أكثر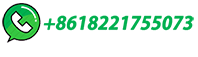
Solved Problems 12 to 14 are based on the following
Question: Problems 12 to 14 are based on the following information: A ball mill is to grind 250 tons/day of calcite having a specific surface of 90.34 sq. cm/g. No recrushing of material is to be done. Overall energy effectiveness of the ball mill is 7.5%. Ritterger's number of calcite is 1053 ft-lbg m2 Mesh 10/14 14/20 20/28 28/35 35/48 48/65 ...
اقرأ أكثر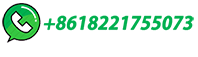